Dissimilar Metal Corrosion with Zinc
The hot-dip galvanized coating is primarily comprised of zinc and zinc alloys, but is sometimes placed in contact with different metals including stainless steel, aluminum, copper and weathering steel. When two different metals are in contact and exposed to a common electrolyte, one of the metals experiences accelerated corrosion while the other is protected. This type of accelerated corrosion between dissimilar metals is referred to as galvanic corrosion. Because galvanic corrosion can occur at a high rate under certain circumstances, it is important to evaluate the combination of galvanized steel with other metals to determine if galvanic corrosion is of concern.
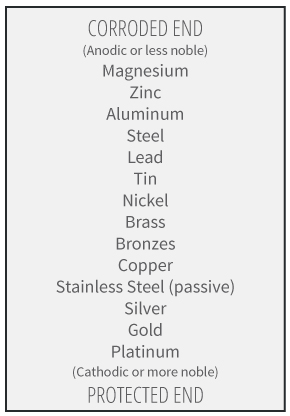
All metals have different electrical potentials that can be quantified in the presence of a conductive medium such as moisture or saltwater. A Galvanic Series of Metals lists metals and alloys in decreasing order of electrical activity in a particular medium.
Metals and alloys nearer the top of the series have a greater negative electrical potential than the more noble or stable metals below. When two metals of different electrical potentials are combined under the right conditions, a galvanic cell is formed.
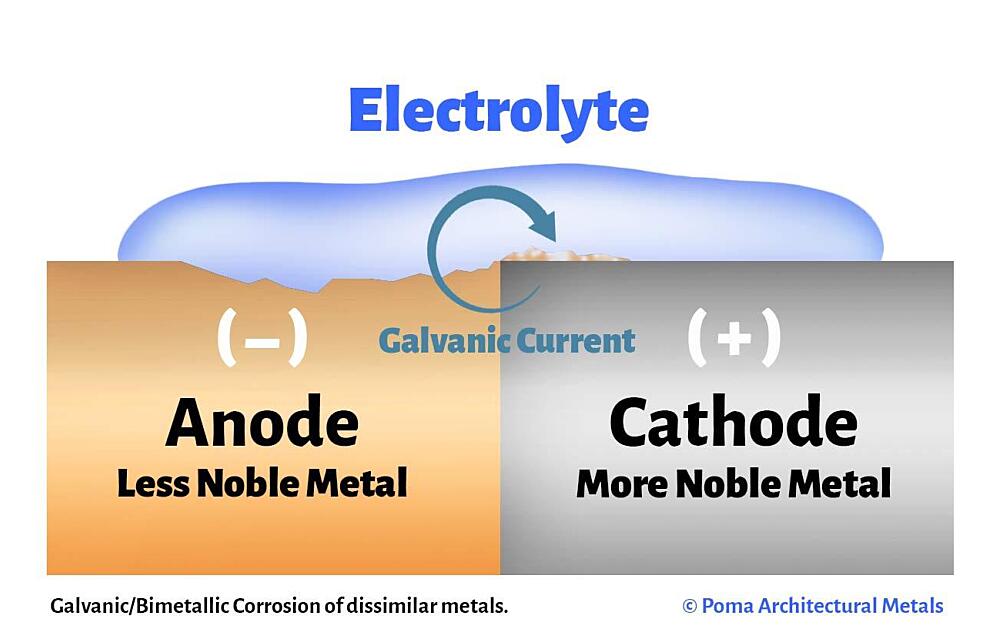
The galvanic cell is similar to a battery, consisting of two dissimilar metals immersed in an electrolyte solution. An electrochemical reaction occurs involving a transfer of electrons from one metal to the other (electric current) when the two metals are connected by an external, conductive path. This results in accelerated corrosion of the metal losing electrons while the metal receiving electrons is preserved.
However, just because dissimilar metals are in contact does not mean galvanic corrosion will occur. The formation of a galvanic cell requires all the following components to be present1:
- Anode – metal of greater negative electrical potential, where electrons are generated by the reaction. Accelerated corrosion occurs here.
- Cathode – metal of less negative electrical potential, where electrons are received. The cathode is protected from corrosion.
- Return Current Pathway – electrical connection (e.g. direct contact) between the anode and cathode.
- Electrolyte – conductive medium that allows electrons to be transferred from anode to cathode. A common example is ordinary moisture such as water, rain, dew, snow, high humidity, or sea spray.
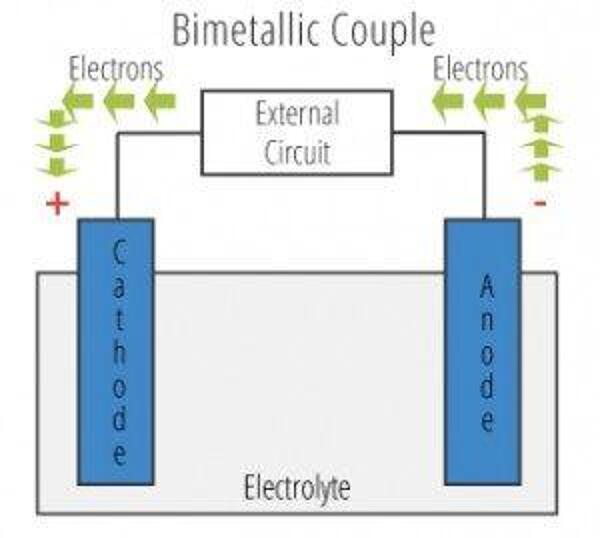
Preventing Galvanic Corrosion
To prevent galvanic corrosion from occurring, one element of the corrosion cell must be interrupted:
- Replace the Anode or Cathode – where the combination of dissimilar metals cannot be avoided, specify combinations which minimize the difference in electrical potential.
- Removal of Return Current Path (Electrical Isolation) – utilize electrically inert spacer materials with a very low ability to absorb moisture. Common materials include neoprene, rubber, plastic, Mylar, nylon, Teflon, glass reinforced epoxy (GRE) gaskets, and more. Corrosion-inhibiting pastes, dried adhesives, and sealants are also utilized where practical.
- Removal of Electrolyte Exposure – installation in sheltered conditions such as the interior of climate-controlled buildings does not typically result in galvanic corrosion. In atmospheric exposure or immersion conditions, application of a durable paint system can minimize exposure of the connection to the electrolytes in the environment. This method is specified when electrical isolation is not feasible (slip critical connections, welded connection, etc.). Painting both metals is preferred to avoid accelerated corrosion concentrated in the areas of coating imperfections on the anodic metal. Maintenance of the paint is required to minimize exposure of the anode.
Primary Factors Affecting Rate of Galvanic Corrosion
Difference in electrical potential – Refer to the figure below for a Galvanic Series containing values for electrical potential of various metals in a saltwater application8. Generally, severity of corrosion increases when combining galvanized steel with metals far away from zinc in the galvanic series. Actual electrical potential values will vary depending on the specific electrolyte present if not saltwater4.
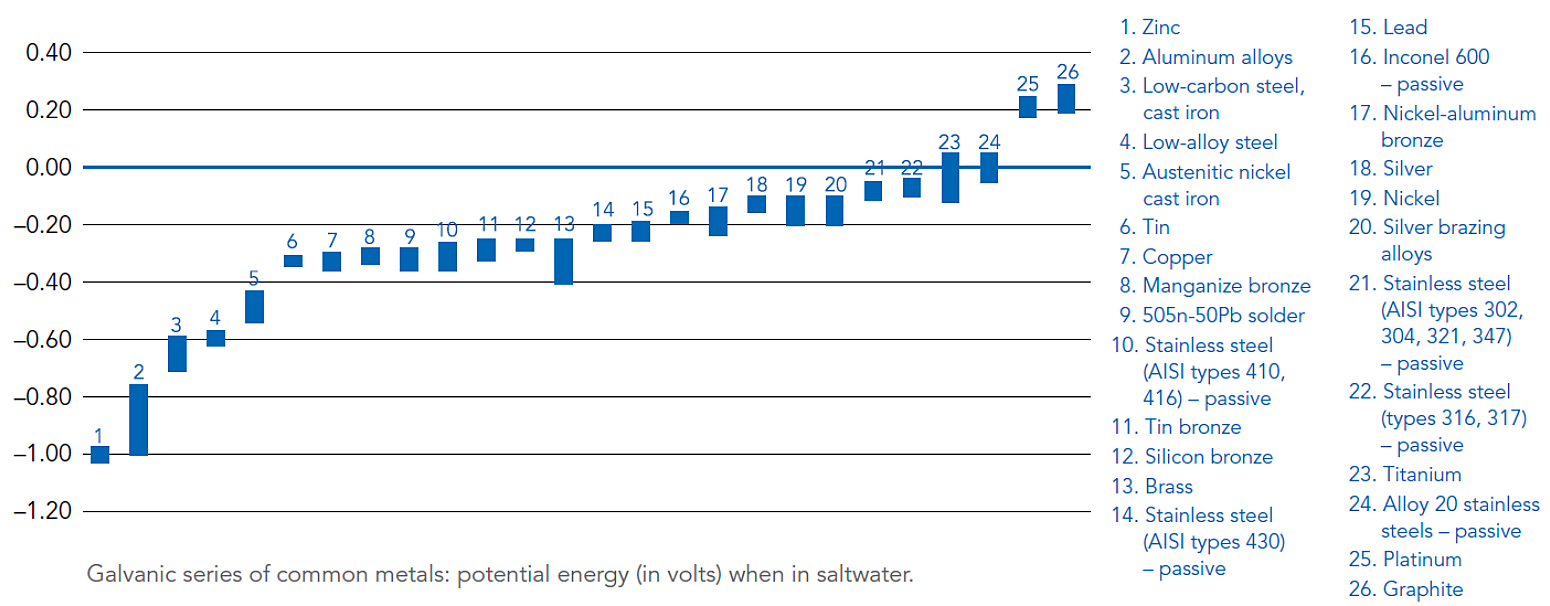
Zinc-to-Metal Surface Area Ratio – Avoid combining a small area of galvanized steel with a large area of cathodic metal. For example, avoid the use of galvanized fasteners to combine cathodic metals such as carbon steel, copper, or stainless steel. Generally, an anode-to-cathode surface ratio of at least 10:1 is recommended to minimize galvanic corrosion8.
Aggressiveness of the electrolyte or installation environment – in many atmospheric applications, rainwater and dew are the primary electrolytic materials, but they do not contain many salts and ions which would make them highly conductive. On the other hand, industrial and marine environments may result in the presence of strong electrolyte materials containing a heavy amount of salts and ions. Galvanic cells are more easily formed in immersion situations.
Other factors – metal oxide layer formation, corrosion inhibitors, chemical reactions, physical and chemical homogeneity of the metal surface, and environmental effects (temperature, oxygen content, effect of electrode potential, etc.)1,2.
Bi-metallic effect on galvanized steel
The following table was developed by interpreting available corrosion data and indicates the impact of electrical potential, environment, and surface area ratios to predict the impact of galvanic corrosion on the long-term performance of galvanized coatings3,5,6. In some cases where moderate impact is predicted, galvanic corrosion may be tolerable on a project by project basis. As galvanic corrosion is a very complex corrosion issue with many variables, it is difficult to predict corrosion rates and the information below is provided for guidance only based on a limited set of variables.
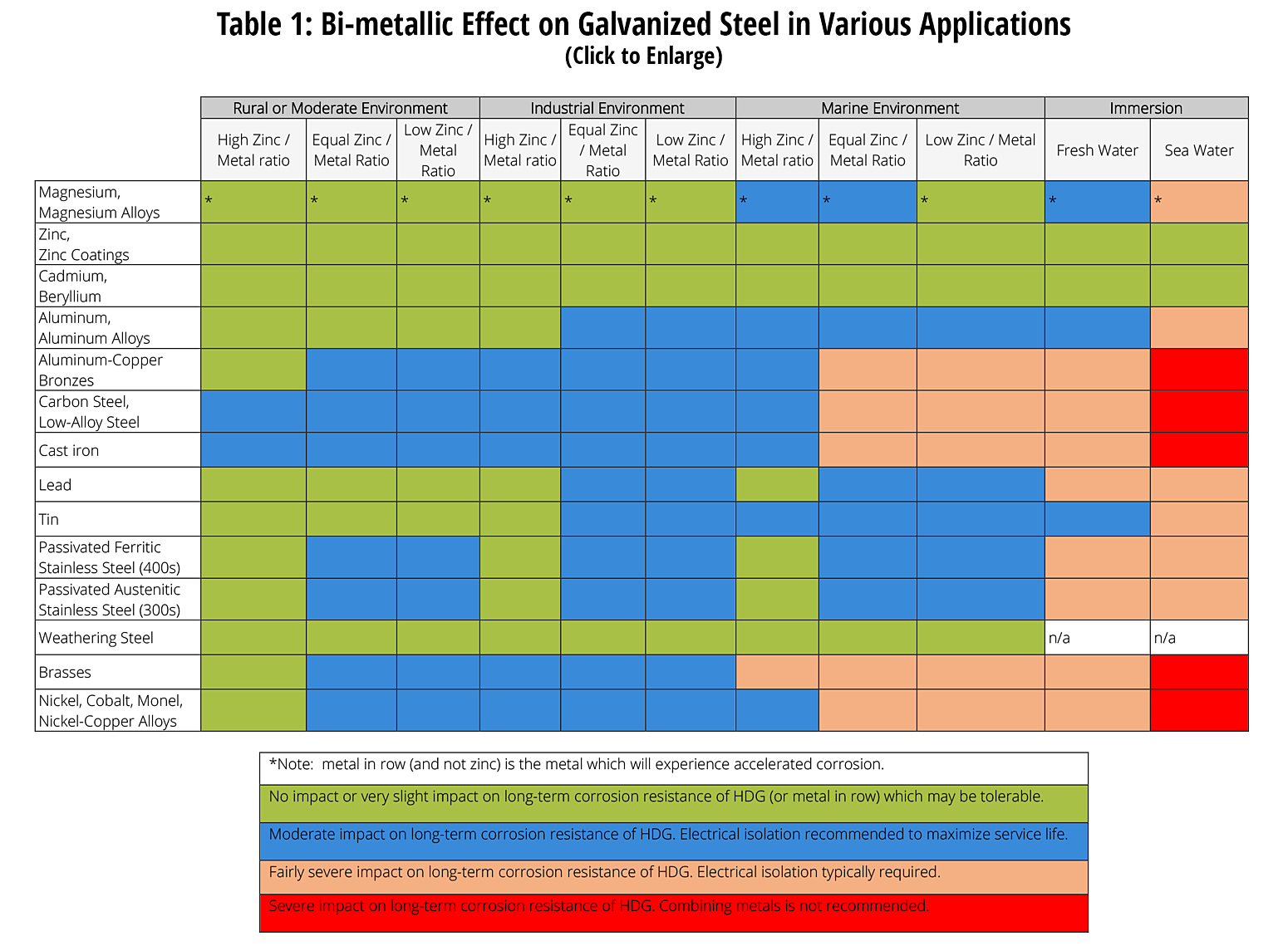
Specific Bi-metallic Applications Involving Batch Hot-dip Galvanized Steel
Other Zinc Coatings – There is no fear of galvanic corrosion when galvanized steel is in contact with other zinc coatings. Common examples include the use of mechanically galvanized bolts to connect high-strength HDG structural steel, and connections between metallized bridge girders and galvanized cross-braces. As zinc coating thickness is directly related to coating longevity, the component with the thinnest zinc coating will be the first to experience corrosion.
Painted Steel – In theory HDG steel may be successfully combined with painted steel, but this assumes a durable paint coating system which is diligently maintained. It is preferable to paint both metals to minimize exposure of the galvanizing should the painted components experience damage or weathering.
Weathering Steel - When HDG bolts are used to connect weathering steel, zinc will initially sacrifice itself until a protective layer of rust develops on the weathering steel, preventing further sacrificial action. Batch HDG parts have enough zinc thickness to last until the weathering steel patina develops (typically 1-5 years) with only minimal loss in coating life. As a result, weathering steel may be fastened with HDG bolts despite a low anode surface area ratio9.
HDG Vent/Drain Hole Plugs – Tapered plugs made from zinc or aluminum are used to fill vent/drain holes on galvanized hollow fabrications such as handrail. Aluminum plugs are more economical and per Table 1 any moderate impact on service life in marine environments may be acceptable in service. For galvanized products placed in coastal or high humidity/chloride environments where maximum longevity is also a primary design consideration, the use of zinc plugs are considered.
Bolted Structural Connections – Dielectric washers and bolt sleeves can be specified to achieve full isolation of the bolt, but all dielectric materials should be evaluated for compatibility with the loading condition8. For high strength connections, shims and washers are not allowed under existing standards, meaning the impact on connection design and installation must be evaluated and quantified prior to use7.
HDG and Black Rebar in Concrete – if galvanized steel and black steel are specified to be connected in concrete between different mesh layers of an exposed panel or the upper section only of reinforcement in a pile foundation in the ground, accelerated corrosion of zinc occurs after depassivation of the galvanized rebar in concrete10. Though depassivation does not often occur for decades, galvanic corrosion should be especially considered for high chloride environments (i.e. heavy road salting or marine environments). Common mitigations include galvanizing all rebar, supports, spacers, and tying wire; applying dielectric tapes for electrical isolation; and increasing concrete cover over the connection point.
References
- Baboian, Robert, Galvanic Corrosion, Metals Handbook, 9th Ed., Vol. 13, Corrosion, ASM International.
- Zhang, X.G., Galvanic Corrosion of Zinc and It’s Alloys, Electrochemical Society, Vol. 143, No. 4, April 1996.
- British Standard Institute; Additional Corrosion of Zinc and Zinc Based Alloys Resulting From Contact With Other Metals or Carbon; pp 6484: 1979.
- ASTM G82-98(2014), Standard Guide for Development and Use of a Galvanic Series for Predicting Galvanic Corrosion Performance, ASTM International, West Conshohocken, PA, 2014, www.astm.org
- MIL-STD-889C, Department of Defense Standard Practice: Dissimilar Metals (22-AUG-2016).
- American Iron and Steel Institute. Committee of Stainless Steel Producers, April 1977.
- RCSC Research Council on Structural Connections, Specification for Structural Joints Using High-Strength Bolts. RCSC, August 1, 2014 (includes April 2015 Errata).
- Hewitt, Christopher; Humphries, Alan; Twomey, Eric, “Opposites Attract: A Primer On Galvanic Corrosion of Dissimilar Metals,” Modern Steel Construction, January 2019.
- H.E. Townsend, et al., “Atmospheric Corrosion Performance of Hot-Dip Galvanized Bolts for Fastening Weathering Steel Guardrail,” CORROSION/98, paper no. 344 (Houston, TX, NACE, 1998).
- Yeomans, SR, Galvanized Steel Reinforcement in Concrete, Elsevier, 2004