Welding Before HDG
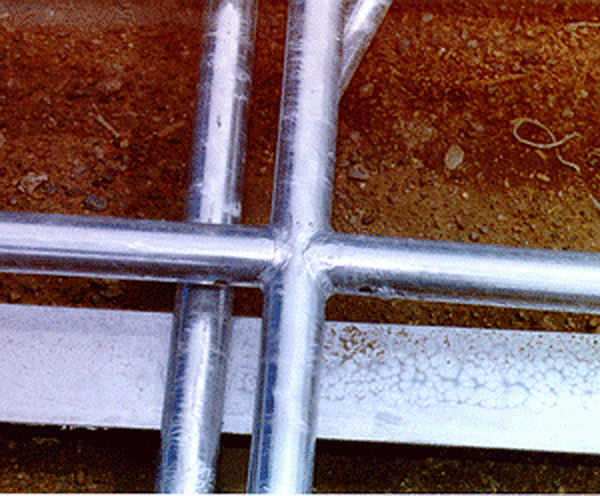
A diversity of steel fabrication sizes and configurations are well suited for galvanizing. Throughout North America, variously sized hot-dip galvanizing kettles are available, allowing this broad scope of structural fabrications to be galvanized.
Unless the welded structure will be too large for the galvanizing kettle, it is common practice to weld steel before galvanizing. Welding steel prior to galvanizing ensures that the entire structure is coated with corrosion-inhibiting zinc.
As with any fabrication to be galvanized, it is important for the steels surfaces to be entirely free of residues commonly found on steel, including weld flux. To make this objective easier to meet, when welding prior to galvanizing an uncoated electrode should be used to prevent flux deposits. If using a flux-coated electrode is unavoidable, mechanical cleaning methods will be needed to prepare the steel for galvanizing.
It is additionally advisable to avoid anti-spatter sprays when welding prior to galvanizing, as they often are not removed by chemical cleaning and must be mechanically removed.
In order to minimize costs and turnaround times, removal of any surface contaminants that chemical cleaning processes will not eliminate, including weld flux, should be performed at the fabrication facility.
Welding Process | Welding Electrode | Silicon Content |
---|---|---|
SMAW | Jetweld 2 (E6027) Fleetwood 35 LS (E6011) Fleetwood 7 (E6012) | 0.25% 0.10% 0.30% |
SA | L60-860 (F6A2-EL12) L61-860 (F7A2-EM12K | 0.22% 0.35% |
FCAW-S | NR-203 NiC+ (E71T8-K2) NR 311(E70T-7) | 0.07% 0.10% |
Appearance of the Weld
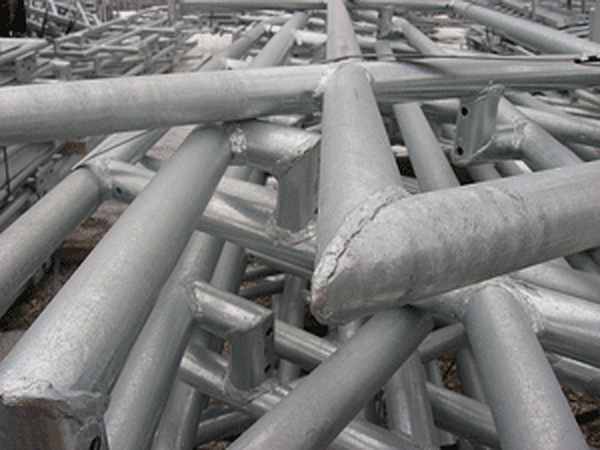
When welded items are galvanized, both the cleanliness of the weld area and the metallic composition of the weld itself affect the galvanized coatings quality and appearance. It is recommended that the welds on the steel be of consistent thickness and symmetrical. The specifics of welding techniques can best be obtained from the American Welding Society (800-443-9353) or your welding equipment supplier. Several welding processes and techniques have been found to be successful for items to be galvanized.
Preferred Welding Processes
Welding processes such as gas metal arc welding (GMAW) or gas tungsten arc welding (GTAW) are recommended since they essentially produce no slag.
Welding Electrode Selection
When selecting a welding electrode, make sure that it provides a deposited weld composition as close as possible to the parent metals chemical composition. The composition compatibility will yield a more uniform zinc surface appearance. As with galvanizing high silicon steel, welding rods high in silicon may cause excessively thick and/or darkened galvanized coatings to form over the weld.
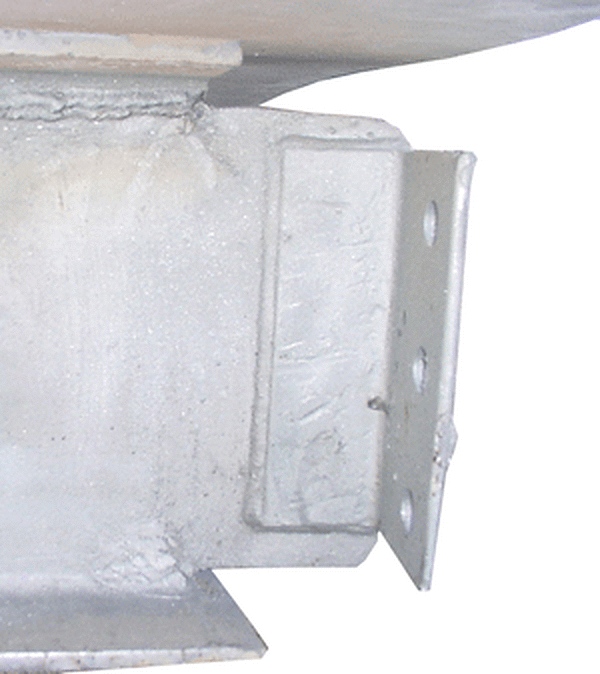
Seal-welding
If the gap between two surfaces to be welded is less than 3/32 (2.5mm), all edges must be completely seal-welded
Stitch-welding vs. Continuous Welding
It is often beneficial to use stitch-welding techniques as opposed to continuous welding. If air is trapped in a seal-welded space it will expand rapidly upon immersion into the zinc bath. This may cause a sudden fracture of the steel structure. A stitch weld in conjunction with a gap of 3/32 (2.5mm) or more between pieces is suggested to avoid this.
Welding Residue Stud Insulators or ferrels may also cause problems when galvanizing. Residue or impurities may remain around the base, leaving imperfections somewhat like welding slag. These residues must be mechanically cleaned prior to galvanizing.
Induced Stresses, Differences in Steel Thickness
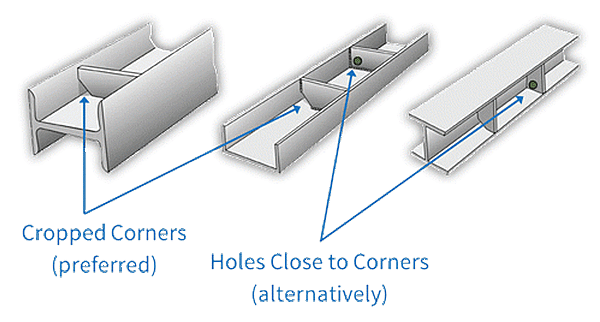
Welding two parts together induces areas of increased stress around the weld joint. Warping and distortion may occur upon immersion into the molten zinc. Additionally, if the parts of the assembly are unequal in thickness, temporary bracing may be necessary to limit warping and distortion.