Venting & Drainage
Tubular assemblies (handrails, pipe columns, pipe girders, street light poles, transmission poles, pipe trusses, sign bridges) are commonly galvanized because corrosion protection is afforded to the interior and exterior of the product. To provide an optimal galvanized coating, hollow products require proper cleaning, venting, and draining.
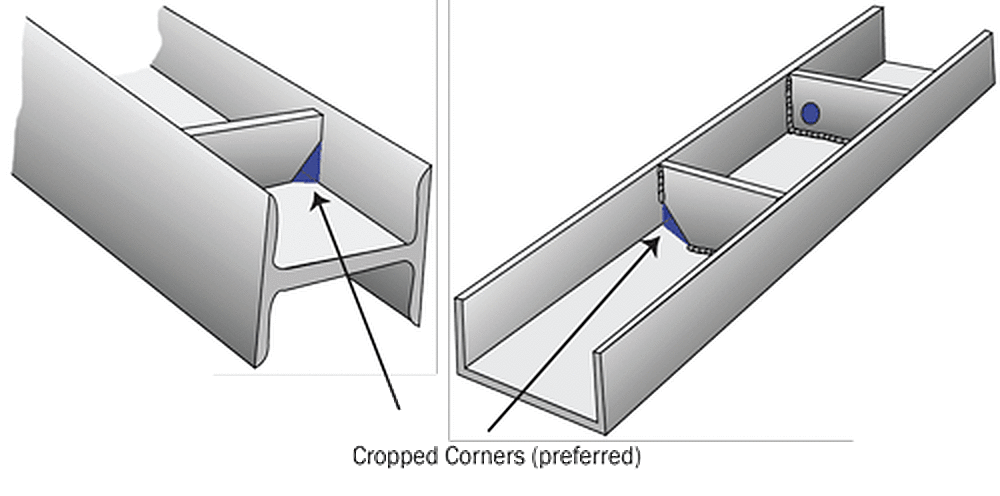
Cleaning
As with all steel, pipe and other hollow materials must be thoroughly cleaned before the molten zinc will metallurgically bond with the steel. Pipe can present two special cleaning challenges. First, the mill coating (varnish, lacquer, and similar materials) applied by pipe manufacturers requires extra time and effort to remove at the galvanizing plant. Some galvanizers do not have the capability to remove this coating. Some organic mill coating formulations, both foreign and domestic, are extremely difficult to remove with common cleaning solutions, so blasting may be required. Ordering uncoated pipe avoids costly attempts to remove these mill coatings. In some cases, it may be more cost effective to substitute tube for pipe.
Second, welding around mill coatings burns and carbonizes the varnish in the surrounding areas and cannot be removed by the normal cleaning process at a galvanizer. This soot must be removed by blasting or other mechanical cleaning methods prior to delivering steel to the galvanizing facility.
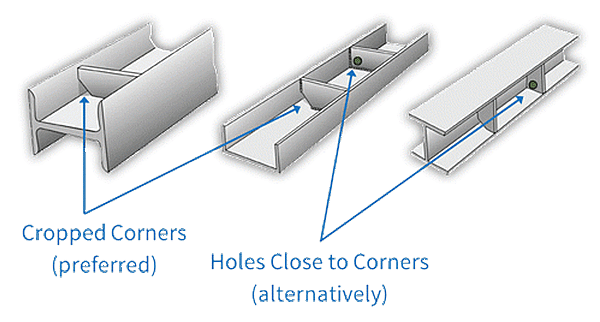
Venting
The primary reason for vent and drain holes is to allow air to be evacuated, permitting the object to be completely immersed into cleaning solutions and molten zinc. Proper hole sizing and location make it safer to galvanize and provide the optimal finish. The secondary reason is to prevent damage to the parts. Any pickling solutions or rinse waters that might be trapped in a blind or closed joining connection will be converted to superheated steam or gas and can develop a pressure of up to 3,600 psi (25 MPa) when immersed in molten zinc. Not only is there risk of damage to the fabrication being galvanized, but there also is risk of serious hazard to galvanizing personnel and equipment.
When the fabrication is lowered into the cleaning solutions and zinc, air and frothy fluxes must be allowed to flow upward and completely out. Cleaning solutions and molten zinc must be allowed to flow in and completely wet the surfaces. Then, when the structure is raised from the bath, no solutions should be trapped inside. Consequently, ample passageways allowing unimpeded flow into and out of the part must be designed into assemblies. Proper galvanizing results when the inside and outside of a product are completely cleaned and zinc-coated.
Items are immersed and withdrawn from the galvanizing kettle at an angle; thus, the vent holes should be located at the highest point and drain holes at the lowest. All sections of fabricated pipe-work should be interconnected with full open-tee or miter joints. Each enclosed section must be provided with a vent hole at each end.
Vent holes are frequently left open but can be closed with drive caps or plugs after galvanizing. Various methods of venting are acceptable, but the subsequent plugging of these holes should be kept in mind, where necessary or desired.
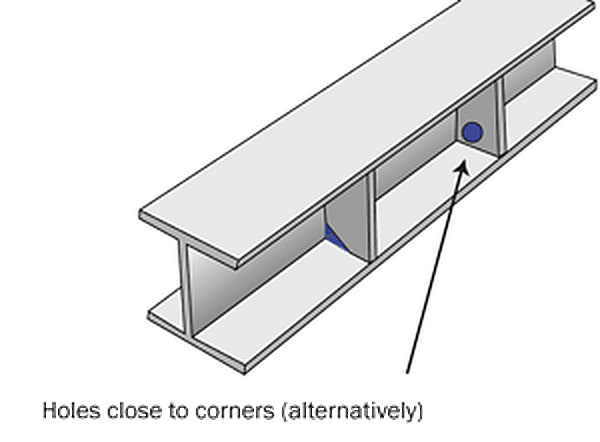
Drainage
When hot-dip galvanizing, cleaning solutions and molten zinc must be able to flow into, over, through, and out of the part. Improper drainage design which impedes free flow can cause complications for the galvanizer and the customer including: poor appearance, bare spots, and excessive build-up of zinc. These unnecessary and costly mistakes are a key example of the importance of communication early in the design phase of the project.
Following best design practices will ensure the highest quality coatings. A few areas where drainage is especially important are gusset plates, stiffeners, end-plates, and bracing. Use these guidelines:
- Gusset plates should have generously cropped corners to provide for free drainage. If copping the gusset plates is not possible, place at least 1/2 (13 mm) holes as close to the corners as possible.
- All stiffeners, gussets, and bracing should be cropped a minimum of 3/4 (19 mm) to ensure unimpeded flow of solutions.
- To allow molten zinc access during immersion in the galvanizing bath and drainage upon withdrawal, provide holes at least 1/2 (13 mm) in diameter in end-plates on rolled steel shapes.
- Alternatively, place at least 1/2 (13 mm) holes in the web within 1/4 (6 mm) of the end-plate. End-plates should have holes placed as close to interior corners as possible to facilitate drainage.
For more information on venting and drainage of specific products, see the corresponding pages int he navigation.