Distortion & Warping
When the decision is made to hot-dip galvanize, the design engineer should ensure that the pieces can be suitably fabricated for highest-quality galvanizing. Best practice suggests steel to be galvanized should be symmetrical and of similar thickness.
With proper consideration and understanding of how the hot-dip galvanizing process affects steel, asymmetrical designs or structures containing sections of unequal thickness can be successfully galvanized, as can fabrications where cold-working techniques (bending, hole-punching, rolling, shearing) are employed.
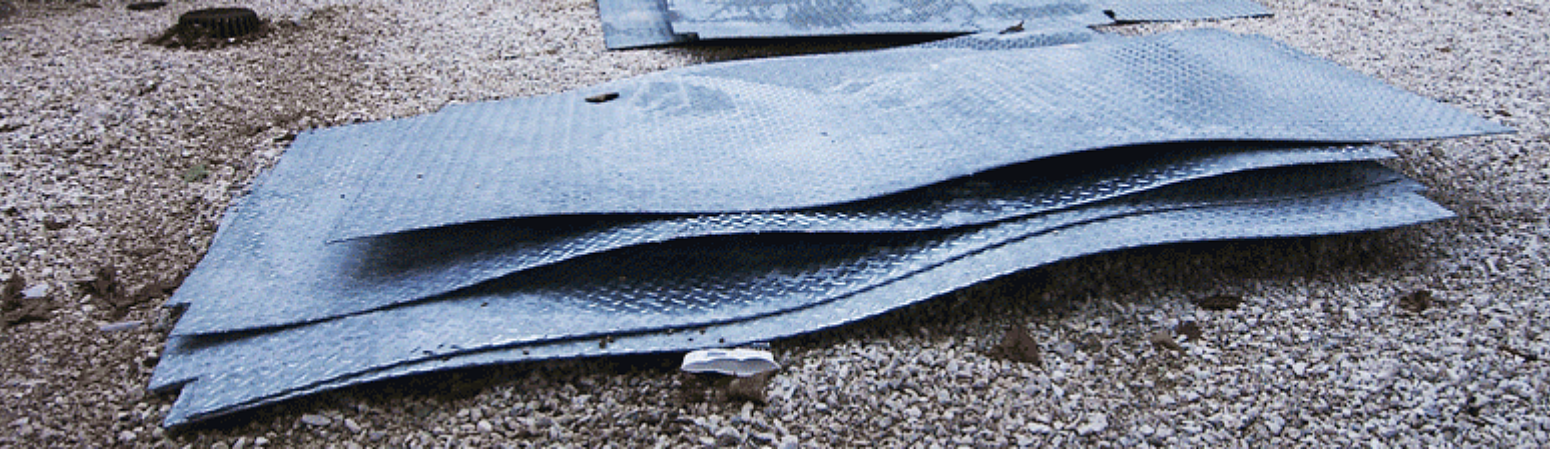
Steel being galvanized progresses through a temperature cycle upon immersion into and withdrawal from the galvanizing bath. Because parts are immersed at an angle, uneven heating occurs, creating a temperature profile along the part being galvanized. This temperature profile allows the steel's internal stresses to be relieved at different times in the immersion cycle. These stresses may cause changes in shape and/or alignment (distortion and warping).
The following steps can be taken to minimize this risk:
- Where possible, use symmetrically rolled sections in preference to angle or channel frames. I-beams are preferred to angles or channels.
- Use parts in an assembly of equal or near equal thickness, especially at joints.
- Use temporary bracing or reinforcing on thin-walled and asymmetrical designs.
- Bend members to the largest acceptable radii to minimize local stress concentration.
- Accurately pre-form members of an assembly so it is not necessary to force, spring, or bend them into position during joining. Continuously weld joints using balanced welding techniques to reduce uneven thermal stresses. Pinholes from welding are very dangerous in items to be galvanized and must be avoided. Staggered welding techniques to produce a structural weld are acceptable. For staggered welding of 1/8-inch (4 mm) or lighter material, weld centers should be closer than 4 inches (10 cm).
- Avoid designs that require progressive-dip galvanizing. It is preferable to build assemblies and subassemblies in suitable modules so they can be immersed quickly and galvanized in a single dip. In this way, the entire fabrication can expand and contract uniformly. Where progressive dipping is required, consult your galvanizer.
Consult your galvanizer regarding the use of temporary bracing or reinforcing.
The guidelines for safeguarding against warping and distortion during hot-dip galvanizing of steel assemblies are outlined in ASTM A384.