Holes
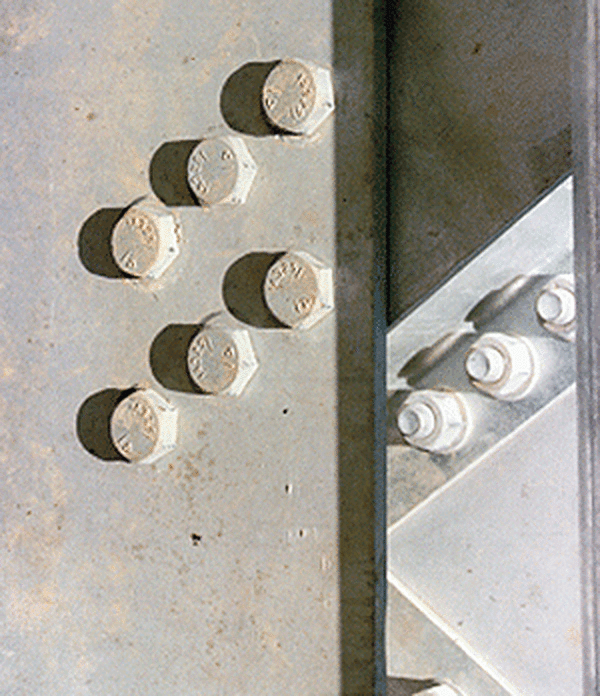
Hot-dip galvanizing is a zinc coating applied to bare steel, and typical coatings range from 3-8 mils (75-200 microns). Therefore, when steel is dipped in molten zinc, the steel becomes slightly thicker. When designing and detailing tapped holes, even the smallest change in thickness is important. When the decision is made to hot-dip galvanize, hole sizes in certain products must be oversized to account for the added thickness of the zinc coating to the edges.
As it can be difficult to predict the exact thickness of the zinc coating, if the hole is not large enough after galvanizing, it can be retapped. Even though retapping will leave exposed bare steel, regalvanizing is not required as the zinc coating on the mating fastener will protect chased or retapped nuts cathodically.
For holes threaded after galvanizing, the hole should be drilled undersize before galvanizing so the threads can be cut after galvanizing.
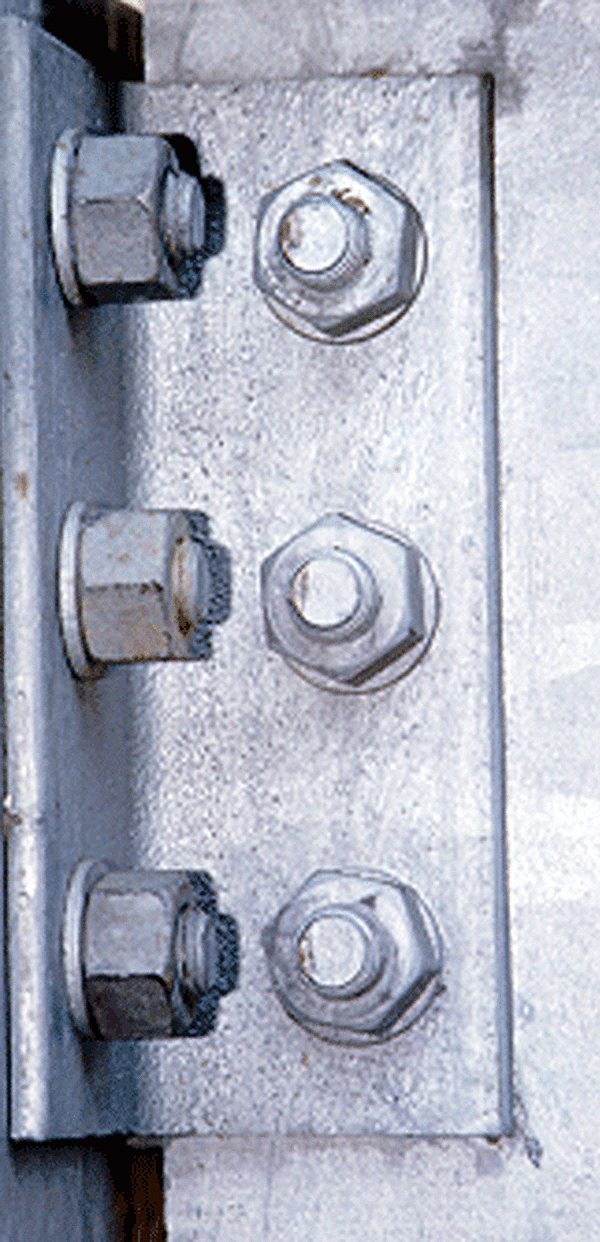
Clearance holes must be designed to account for zinc pickup. Oversizing holes according to ASTM guidelines is usually sufficient to account for the thickness of the zinc coating, or the holes can be reamed to fit after galvanizing.
Threaded assemblies must adequately accommodate galvanized fasteners. It is important to make sure the hole is undersized enough so when cutting the threads, all zinc is removed and the hole is still accurately sized. If all of the zinc is not removed from the threaded hole, its relatively soft structure may become damaged when fitting the hole with a fastener. It is best to mate a galvanized fastener with threads solely composed of steel to ensure a quality bolted connection. Cut threads will expose bare steel, but the zinc coating on the threads of the mating hot-dip galvanized fastener will protect the bare steel for the bolted connection.
Utilizing galvanized fasteners is always recommended when connecting galvanized structural pieces, and uncoated fasteners should never be placed in galvanized threaded holes. Zincs cathodic protection characteristics cause it to sacrifice itself to protect the uncoated fastener, accelerating the rate in which zinc is consumed.
The use of very small holes should be minimized as well, as they may become completely obscured and/or filled by zinc. If small holes are unavoidable, the area may be heated after galvanizing in order to remove any excess zinc and open the hole.