Dissimilar Steel Chemistries
Most ferrous materials are suitable for hot-dip galvanizing. Cast iron, malleable iron, cast steels, hot-rolled steel, and cold-rolled steels all can be protected from corrosion with zinc applied in the hot-dip galvanizing process. Weathering steel and certain stainless steels (300 series) also can be galvanized.
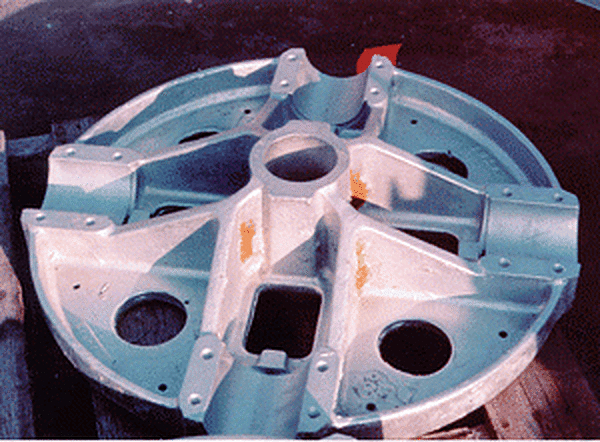
It is important to understand that the chemical composition of the material being galvanized can affect coating characteristics. However, corrosion protection typically is not affected by these coating characteristic differences.
Fabrications with varying steel chemistries can form the galvanized coating's iron-zinc intermetallic layers at different rates, resulting in a non-uniform coating appearance. Again, corrosion protection is not affected by non-uniform appearances.
Variations in color and texture do not affect the corrosion protection provided by the galvanized coating. It is important to understand that upon normal weathering in the environment, the entire coating commonly evolves to a uniform appearance.
While the overwhelming determinant of coating thickness is steel chemistry, varying surface conditions and/or different fabrication methods also can affect coating appearance. This is because different parameters for pickling (immersion time, solution concentrations, temperatures) and galvanizing (bath temperature, immersion time) are required for:
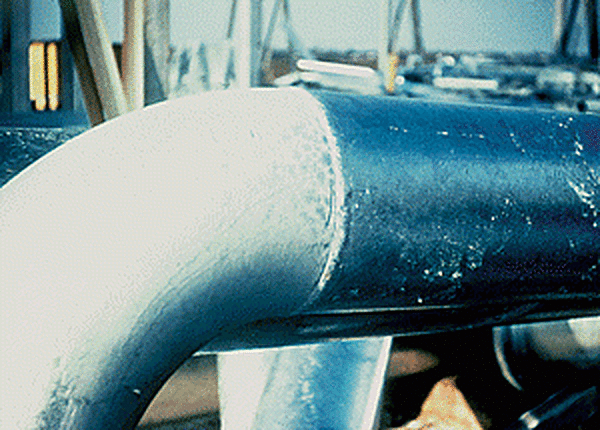
- Excessively rusted surfaces
- Machined surfaces
- Malleable iron
- Hot-rolled steel
- Cold-rolled steel
- Castings, especially with sand inclusions
- Pitted surfaces
- Steel with relatively high levels of carbon, phosphorus, manganese, and/or silicon
Many coatings such as paint and lacquer cannot be removed from the steel with the chemical cleaning process used in the galvanizing facility. As perfectly cleaned steel is required for the metallurgical reaction to occur in the galvanizing kettle, these contaminants need to be removed mechanically from the surface prior to sending the fabrication to the galvanizer.
To allow for optimum coating development when combining dissimilar steels in a single fabrication, consider these guidelines:
- Galvanize dissimilar steels separately and assemble after galvanizing
- Avoid the use of old steel with new steel, or combining castings with rolled steel in the same assembly
- Avoid using excessively rusted, pitted, or forged steels in combination with new or machined surfaces; if this is unavoidable, a thorough abrasive blast-cleaning of the assembly (normally before any machining is done) will allow for a more uniform galvanized coating.
Stainless steels in the 300 series can be galvanized because they contain nickel, which is necessary to initiate reaction between the steel and the zinc. Stainless steels in the 400 series do not contain nickel and cannot be galvanized.
Weathering steel also can be galvanized, although it typically contains relatively high amounts of silicon and will develop thicker coatings that are usually matte gray in finish. The corrosion protection provided by galvanizing is unaffected by coating appearance.