Steel Residues
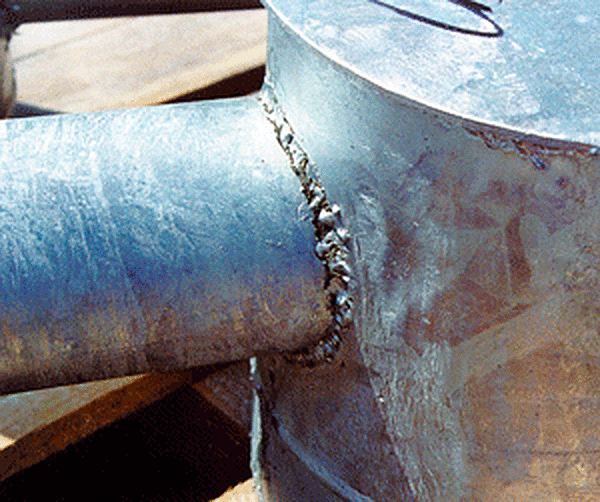
One of the many benefits of hot-dip galvanizing is that coating integrity is readily apparent: zinc metallurgically bonds only with clean steel. Coating uniformity is immediately apparent as the work is withdrawn from the molten zinc bath.
Steel surface preparation prior to galvanizing is of paramount importance in delivering complete, optimum-quality zinc coatings.
Some surface residues, such as mill lacquer, welding slag, varnish, water-insoluble paints, adhesives, and sand used in the making of castings, are not removed by the standard chemical cleaning methods involved in the galvanizing process.
Residues that cannot be chemically cleaned from the steel surface can be removed by mechanical cleaning, prior to delivering the steel to the galvanizer. Typically, pipe and tube are coated with organic lacquers that are very difficult to remove by chemical cleaning. When pipe comes from the steel supply house, the coating may be tough to identify. Mill lacquers and varnish require extra effort and time to remove. Abrasive blast-cleaning may be necessary to remove some organic mill coating formulations.
There are numerous mechanical cleaning methods that can be used to remove these common residues, including:
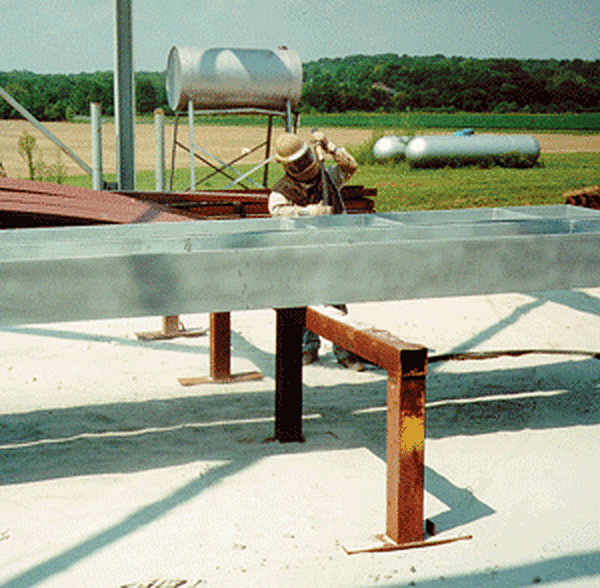
- Abrasive blasting / wheel-abrading
- Barrel and vibratory finishing
- Brush- and hand-finishing
- Grinding and polishing
Contact your galvanizer when planning to use steel coated with lacquer or other products to determine whether the coating can be removed at the galvanizing plant.
In order to lower costs and minimize turnaround times, abrasive blast-cleaning should be performed at the fabrication facility.