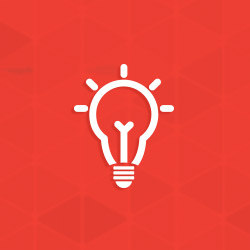
Using Paint as an Electrical Insulator Between Dissimilar Metals
I know I shouldn't have dissimilar metals in contact in my design, but its my only option and I can't put a barrier between the two. Can I paint the surfaces to act as an electrical insulator?
When using hot-dip galvanized steel in a design, it is preferable to have the entire project hot-dip galvanized in order to avoid a galvanic corrosion cell created by dissimilar metals in contact. If the entire fabrication is hot-dip galvanized, the sustained corrosion protection of the zinc coating will be uncompromised and provide many years of maintenance-free protection. However, reality dictates the perfect solution cannot be obtained 100% of the time and dissimilar metals must sometimes be used together within a design. What do we do then? Is there any way to slow down or stop the accelerated corrosion caused by dissimilar metals in contact?
Galvanic Corrosion
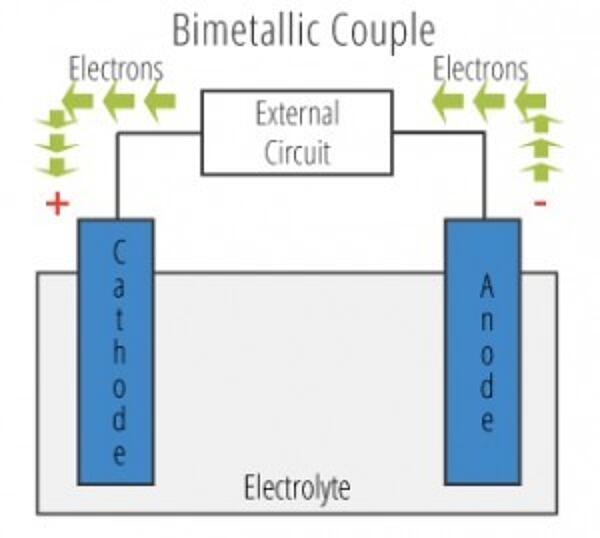
To understand the answer to this question, one needs to understand the pieces of a galvanic cell. A galvanic cell contains four elements: an anode, a cathode, an electrolyte solution, and an electrical connection between anode and cathode. When working with hot-dip galvanized steel, the zinc coating is almost always the anode and a more noble metal (usually stainless steel, carbon steel, or aluminum) used in the design acts as the cathode. The electrical connection is created when anode and cathode are put into direct contact with one another. An electrolyte solution can be found easily in nature; varying from a seawater to a humid atmosphere. A galvanic cell must contain all four of these elements in order to function and cause accelerated corrosion. Eliminating one of these elements will eliminate the galvanic cell, therefore eliminating the accelerated corrosion process.
Can Paint be a Solution?
What part can paint play in eliminating a corrosion cell? It certainly cannot eliminate the existence of the cathode or the anode. Those two elements were introduced during the design phase by using a dissimilar metal in contact with zinc. Changing the projects design to incorporate only one metal will eliminate this element of the galvanic cell. Painting a materials surface may seem like a reasonable way to eliminate the electrical connection between the anode and cathode, but in reality, this is not a reliable solution. During installation, the chipping paint around edges and bolts exposes bare metal which will allow a return current. Some paints, such as zinc-rich primers, may even be conductive themselves, and do nothing to electrically insulate metals from one another when in contact. The final option then is to eliminate the metals exposure to an electrolyte solution. Paint has the potential to perform this function under some conditions. Paint provides barrier protection to materials that will also serve to decrease exposure to an electrolyte and slow down the accelerated corrosion process of a galvanic cell.
So is an application of paint over the surface of dissimilar metals enough to eliminate a galvanic cell and stop the accelerated corrosion? Not entirely, but it can help. Paint may do well to initially eliminate a material's contact with an electrolyte solution, but holidays, wear, and chipping of the coating are all inevitable problems with a paint coating that will once again expose both bare metals to the electrolyte solution and the accelerated corrosion of a galvanic cell. While this corrosion rate may be substantially lower than if the materials were not painted at all, its possible these corrosion rates will be higher than on a design using only hot-dip galvanized steel.
As with any design using dissimilar metals in contact, the surface areas of both the anode and the cathode will be a large factor in the severity of the galvanic corrosion observed. If there is a small anode (zinc) protecting a larger cathode (bare carbon steel), the corrosion seen on the zinc will be quite severe. However, if this setup is reversed, and the cathode is much smaller than the anode, the corrosion on the anode will be much less severe and may even be difficult to detect at all.
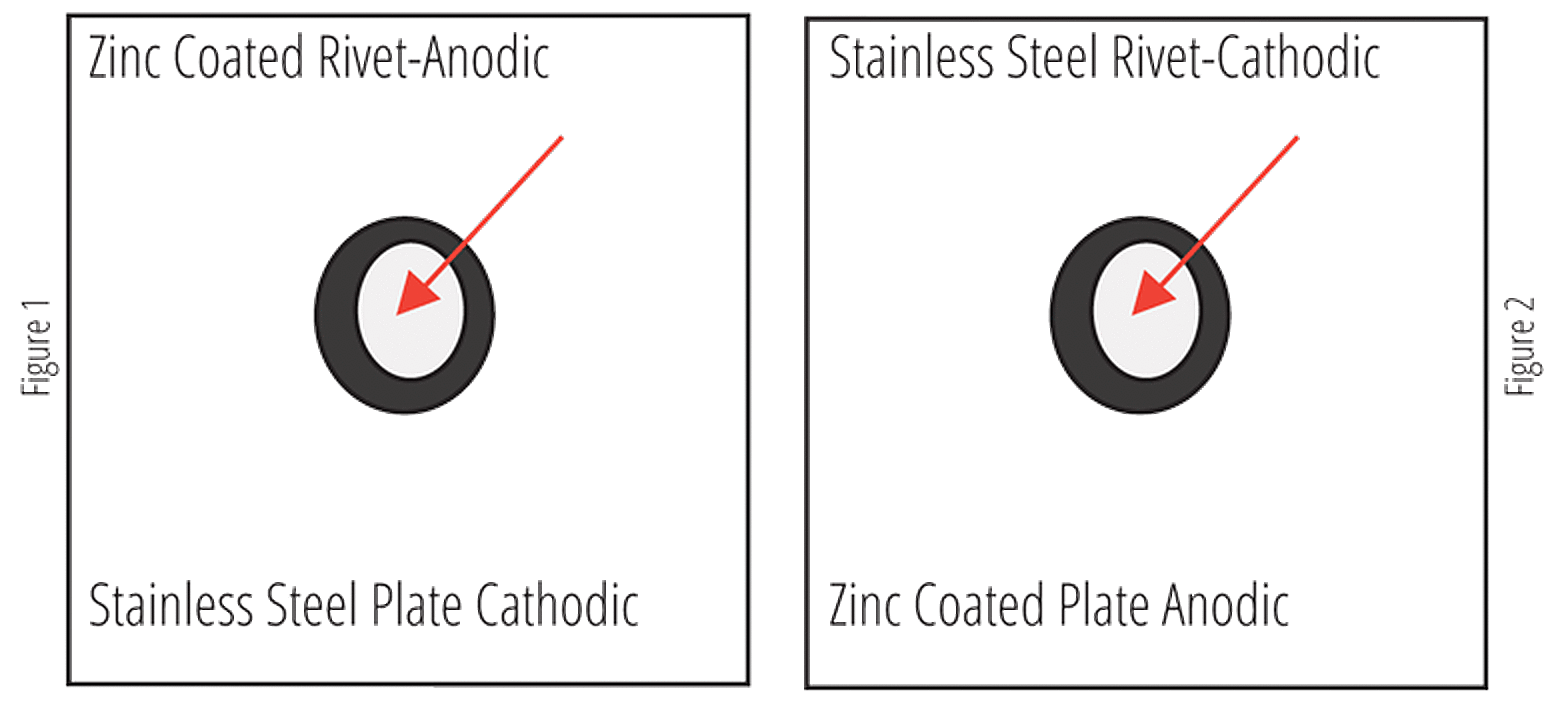
With this principle in mind, it is clear painting only the more anodic metal (hot-dip galvanized steel), will lead to severe localized corrosion of the zinc coating. Holidays and chips in the coating will leave a very small surface area of the anode exposed to the electrolyte solution. This coupled with a large surface area of the cathode will cause severe corrosion in localized spots of the galvanized coating. Conversely, if only the more noble metal is painted, the small holidays and chips in the paint will create a small surface area on the cathode which can be protected by the rather large surface area of the anodic material.
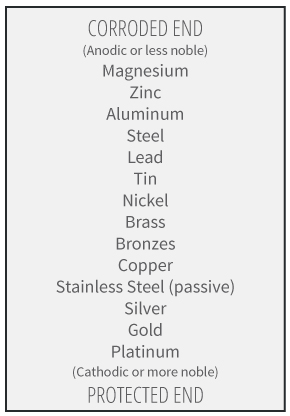
Conclusion
Best practice is to use only one metal (hot-dip galvanized steel) in a design. However, if this is not possible, it is possible to slow the accelerated corrosion effects of the galvanic cell created by the materials. Paint is not a reliable method of deterring the return current path of the galvanic cell; rubber or some other insulating material would be best for that. However, paint may be an effective method of weakening one element of the galvanic cell by reducing the materials exposure to an electrolytic solution. This will only be an effective method if both the anodic material (hot-dip galvanized steel) and the cathodic material (see galvanic series) are painted, or if only the cathodic material is painted. However, the anodic material should never be painted while the cathodic material is left bare.
For more info on hot-dip galvanized steel in contact with dissimilar metals, refer to AGA guide on dissimilar metals.
© 2025 American Galvanizers Association. The material provided herein has been developed to provide accurate and authoritative information about after-fabrication hot-dip galvanized steel. This material provides general information only and is not intended as a substitute for competent professional examination and verification as to suitability and applicability. The information provided herein is not intended as a representation or warranty on the part of the AGA. Anyone making use of this information assumes all liability arising from such use.