Steel Selection
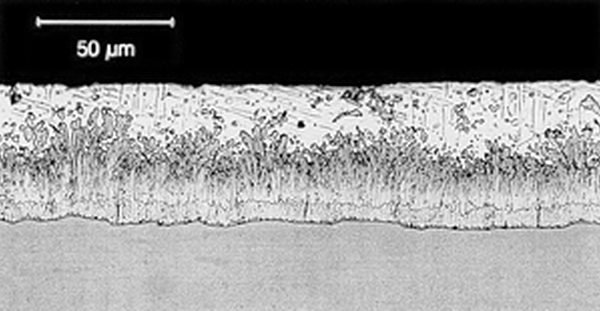
Galvanized coatings are formed by a chemical process during which steel and zinc metallurgically bond, forming a series of corrosion-inhibiting, highly abrasion-resistant zinc/iron alloy layers covered by a layer of pure zinc. For most hot-rolled steels, the zinc-iron alloy portion of the coating will represent 50-70% of the total coating thickness, with the free zinc outer layer accounting for the balance.
The chemistry of the steel influences the galvanized coatings appearance. Steel compositions vary depending on strength and service requirements. Trace elements in the steel (silicon, phosphorus) affect the galvanizing process as well as the structure and appearance of the galvanized coating. Steels with these elements outside of the recommended ranges are known in the galvanizing industry as highly reactive steel, and may produce a coating composed entirely, or almost entirely, of zinc-iron alloy layers.
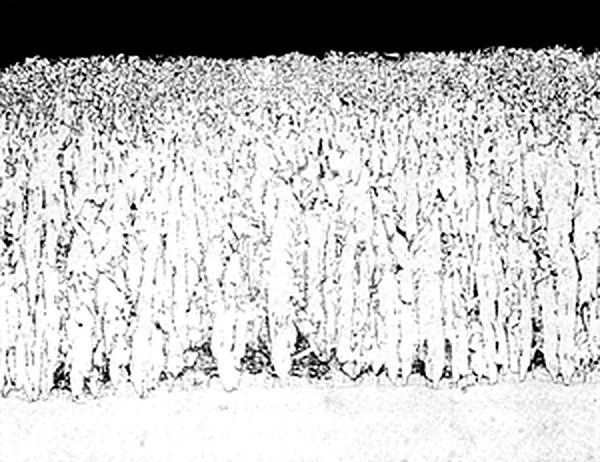
A typical coatings produced from reactive steels exhibit different coating characteristics than a typical galvanized coating such as:
- Appearance: The atypical galvanized coating may have a matte gray appearance and/or rougher surface due to the absence of the free zinc layer. The free zinc layer present on typical coatings imparts a shinier finish to a galvanized coating.
- Adherence: The zinc-iron alloy coating tends to be thicker than a typical galvanized coating. In the rare situation where the coating is excessively thick, there is the possibility of diminished adhesion under external stress (rough handling, sharp impact).
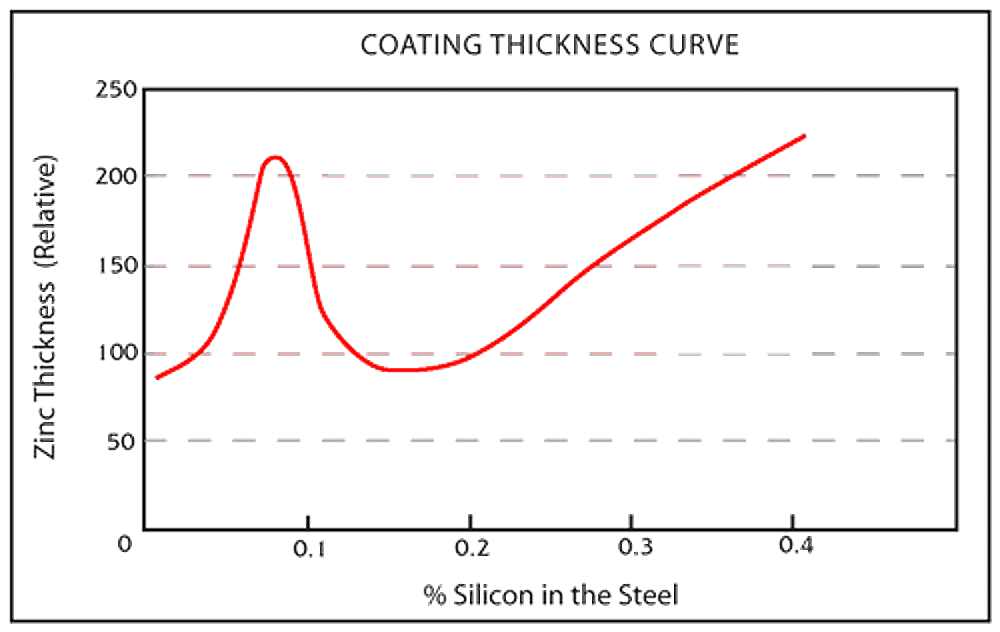
Reactive steels are still galvanized on a regular basis, and it is important to note differences in appearance have no effect on the corrosion protection afforded by the galvanized coating. The performance of the coating is based on the thickness of the zinc; therefore, often the duller (and thicker) coatings produced by reactive steels last longer. Furthermore, all galvanized coatings as they weather over time will develop a uniform matte gray appearance.
It is difficult to provide precise guidance in the area of steel selection without qualifying all steel grades commercially available. However, these guidelines discussed will assist you in selecting steels that provide good galvanized coatings.
- Levels of carbon less than 0.25%
- Phosphorus less than 0.04%
- Manganese less than 1.3%
- Silicon levels less than 0.04% or between 0.15% - 0.22%
Silicon may be present in many steels commonly galvanized even though it is not a part of the steels controlled composition, because silicon is used in the steel deoxidation process and is found in continuously cast steel. Both silicon and phosphorous act as catalysts during the galvanizing process, resulting in rapid growth of zinc-iron alloy layers.
Even when both elements are individually held to desirable limits, the combined effect between them can still produce an atypical coating of all or mostly zinc-iron alloy layers. When possible, your galvanizer should be advised of the grade of steel selected in order to determine whether specialized galvanizing techniques are suggested.
Hydrogen embrittlement is of concern for steels of ultimate tensile strength of 150 ksi (1100 MPa). During the chemical reaction between steel, rust and the chemicals used in the pickling stages of the galvanizing process, hydrogen is produced and absorbed by the steel. The very small grain structure of high-strength steel prevents the hydrogen from being expelled during immersion in the molten zinc. When put under stress in use, the steel may become brittle and fracture.