Fasteners, Bolts & Nails
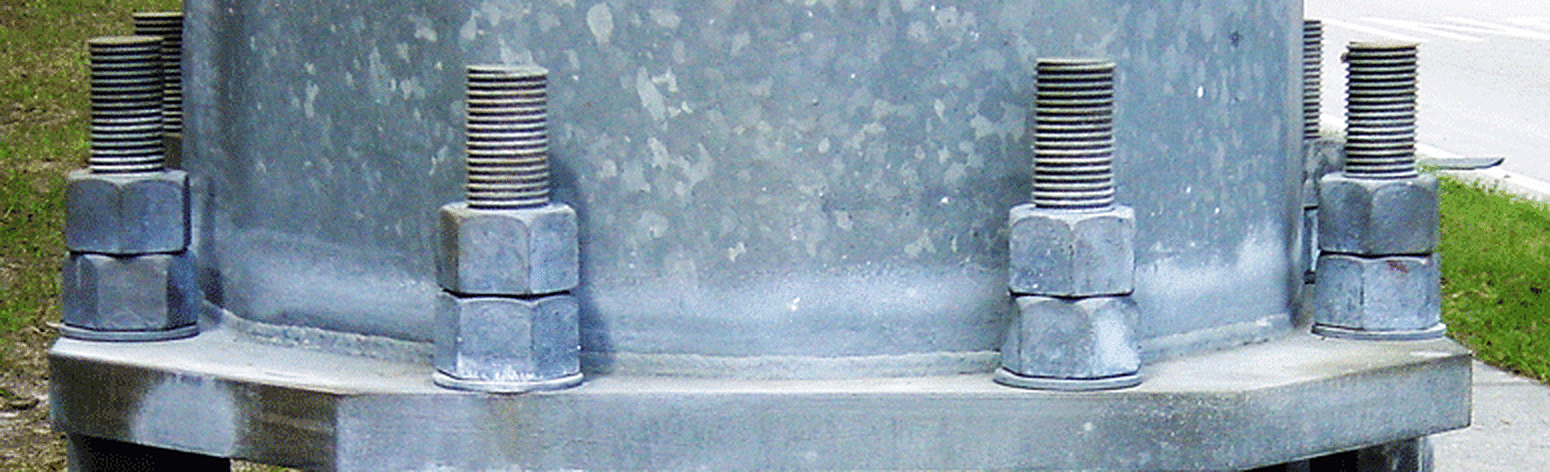
Left unprotected, steel will corrode and suffer loss of mechanical properties and integrity. When it comes to fasteners, corrosion and loss of integrity are particularly dangerous. Therefore, one of the most critical choices in the design of connections is how to protect the fasteners. Hot-dip galvanizing, coating steel with zinc, delivers long-term, maintenance-free corrosion protection in a variety of exposure conditions.
The hot-dip galvanized coating, unlike other zinc-coated fasteners, is metallurgically bonded to the underlying steel forming an impervious barrier between the steel substrate and the corrosive environment. This metallurgic bond means the zinc becomes an inherent part of the steel, rather than just a surface coating, and thus is difficult to damage even when torquing and tightening fasteners. The hot-dip galvanized coating will preferentially corrode to protect the fasteners underlying steel as well as any small areas exposed due to mechanical damage. Therefore, hot-dip galvanizing is an effective method for delivering both long-term barrier and cathodic protection whether fastening connections in atmospheric, concrete, soil, or fresh- or salt-water applications.
The hot-dip galvanized process delivers an excellent fastener for a variety of reasons:
- Complete & consistent coverage the complete immersion in molten zinc ensures excellent corrosion protection for 100% of the exposed surfaces, with a consistent zinc thickness.
- Coating thickness hot-dip fasteners, depending upon diameter, will have from 1.7 to 3.4 (43 to 86 microns) mils of the impervious zinc coating. Zinc-plated fasteners have a thin zinc coating, up to only 1 mil (25 microns).
- Cathodic protection unlike other barrier coatings, such as paint, zinc is a sacrificial metal and preferentially corrodes to protect the underlying steel.
- Bond strength hot-dip fasteners have a coating bond strength in the range of 3600 psi (24.82 MPa). The coating is extremely difficult to damage. Painted and zinc plated coatings have a typical bond strength of only a few hundred PSI and are easily scratched and removed.
- Hardness Hot-dip galvanized fasteners have zinc-iron alloy layers, formed during the galvanizing process, that are harder than the base steel itself. These abrasion resistant layers make the galvanized coating difficult to damage during tightening.
- Temperature range Galvanized fasteners perform well across a broad temperature range, from continuous exposure in the arctic climates to the extremes of 392°F (200°C) in processing plants.
- Paintable Prepared according to ASTM D 6386 (Practice for Preparation of Zinc [Hot-Dip] Galvanized Coated Iron and Steel Product and Hardware Surfaces for Painting), hot-dip coatings are successfully painted, providing long-lasting under film corrosion protection.
- Applicability Hot-dip galvanizing is a factory-controlled process, independent of weather conditions, and touch-up in the field is rarely necessary. However, should field touch-up or repair of the galvanized coating be needed, zinc coatings can be repaired following the guidelines of ASTM A 780 (Practice for Repair of Damaged and Uncoated Areas of Hot-Dip Galvanized Coatings).
- Suitability - The thicker zinc coating on hot-dip fasteners translates into excellent performance in extreme weather and atmospheric conditions. Larger connections are most commonly hot-dip galvanized. Additionally, hot-dip galvanized fasteners are suitable for use in contact with treated wood.