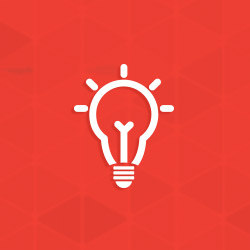
Aluminum Vent/Drain Hole Plugs & Galvanic Corrosion
Zinc or Aluminum Vent/Drain Hole Plugs Which is Better?
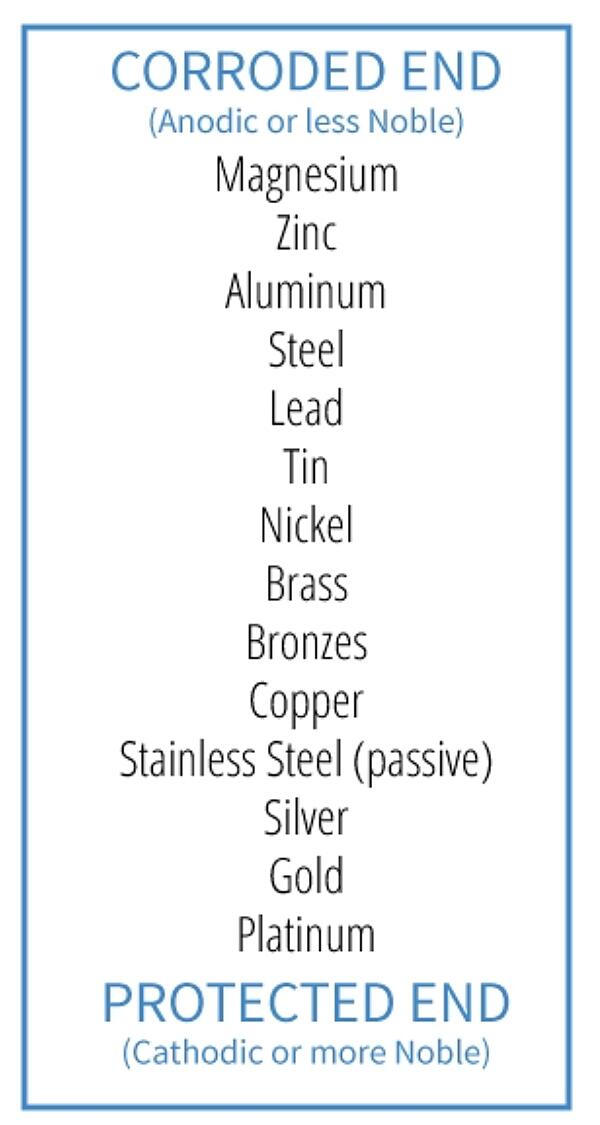
Every now and then you may encounter a customer who does not prefer the presence of venting and drainage holes, despite the benefits the holes provide in terms of safety to galvanizing plant personnel and overall coating quality. The good news is vent/drain holes can be easily sealed after hot-dip galvanizing using zinc or aluminum plugs which are pushed into the holes and filed flush with the surrounding coating. Plugs are most commonly installed on hot-dip galvanized handrails to prevent children from sticking their fingers in those holes and injuring themselves while preventing flying insects from making nests inside. Otherwise, the plugging of vent/drain holes in other types of fabrications is not commonly performed unless for aesthetic reasons, like providing a uniform appearance for Architecturally Exposed Structural Steel (AESS). Plugging of vent/drain holes can be thought of as a best practice, but it is not mentioned nor required within ASTM specifications.
It is often preferred to have vent/drain hole plugs placed by the fabricator, but the plugs can also be placed by the galvanizer. Be sure to address the topic of plugs in the purchase order to prevent any confusion regarding responsibility for purchasing and plugging holes. Regardless of who provides the plugs, it is advantageous to ask the customer about the intended use of the product, the design life, and whether the product will be exposed to a high humidity or high chloride environment. This information is helpful to determine whether the more economical aluminum plugs can be utilized with minimal worry over galvanic corrosion, or whether zinc plugs should be utilized instead. Although discussing this topic with your customer is not necessarily your responsibility, it can go a long way to keeping your customer happy by ensuring their hot-dip galvanized products will perform as intended.
The reason for this is when two different metals such as zinc and aluminum are in contact in a corrosive environment, one of the metals experiences accelerated galvanic corrosion while the other metal remains galvanically protected. To determine whether this is a problem regarding vent/drain hole plugs, refer to the galvanic series of metals (Figure 1) for a listing of different types of metals and their corresponding electrical potentials in a salt water solution. Metals with a lower (more negative) electrical potential will sacrifice themselves for metals with a higher (more positive) electrical potential. When dissimilar metals are in contact, the metal with a lower electrical potential is called the anode, and the metal with a higher electrical potential is called the cathode. The anode provides protection to the cathode, and in the process of providing this protection, the anode material is sacrificed.
In addition, the relative surface areas of the contacting dissimilar metals are relevant in determining the corrosion rate of the anode material. For example, when dissimilar metals are in contact, it is more desirable to have a large anode surface in contact with a small cathode surface to give the anode a very slow corrosion rate.
So the next time your customer asks Which is better? Do I need to worry about galvanic corrosion with vent/drain hole plugs? you can provide the following explanation:
Aluminum is next to zinc on the galvanic scale, meaning the combination of these materials results in only a minor effect on each other. In addition, the use of aluminum plugs results in a favorable anode-to-cathode ratio where the large anode surface (zinc) is in contact with a small cathode surface (aluminum plugs). Therefore, in most applications involving environments without high humidity and/or chlorides, it is more likely the galvanized coating will suffer (at the most) only very slightly additional corrosion due to galvanic corrosion, which is usually tolerable in service. On the other hand, there is no concern regarding galvanic corrosion when using zinc plugs as both the plugs and hot-dip galvanized coating are comprised of the same metal. Therefore, zinc plugs are more suitable for projects requiring maximum design life in corrosive environments, including high humidity/chloride environments.
To purchase aluminum and zinc plugs, contact either The Steel Supply Company at (631) 385-7273 or www.thesteelsupplyco.com, or Bruce Reichelt at (503) 879-9085. Both aluminum and zinc vent plugs are available in sizes ranging from ¼" to 2" in 1/16" or 1/4" increments. Larger or custom sizes may be available upon request.
For more info on hot-dip galvanized steel in contact with dissimilar metals, refer to AGA guide on dissimilar metals.
© 2025 American Galvanizers Association. The material provided herein has been developed to provide accurate and authoritative information about after-fabrication hot-dip galvanized steel. This material provides general information only and is not intended as a substitute for competent professional examination and verification as to suitability and applicability. The information provided herein is not intended as a representation or warranty on the part of the AGA. Anyone making use of this information assumes all liability arising from such use.