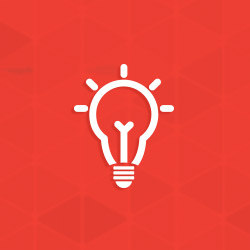
Considerations for Progressive Dipping
My design cannot be optimized to fit into the kettle can I hot-dip galvanize by progressive dipping?
Hot-dip galvanizing is a complete immersion process, which means the parts must fit in the zinc bath to be coated. In North America, the average kettle length is 40 feet, but there are many 50-60 foot long kettles with depths ranging from 6-12 feet, and widths ranging from 5-8 feet. As a result, many oversized structures are designed in modules or sub-units which are able to fit in the kettle for later assembly after hot-dip galvanizing. Although it is preferable to galvanize large assemblies in suitable modules, progressive dipping can provide an alternative option when hot-dip galvanizing articles larger than the dimensions of the kettle.
In the progressive dipping process, half of the article is lowered into the kettle first, removed, and then the other half is dipped to complete the hot-dip galvanized coating. There are some unique challenges when it comes to progressive dipping, and it is crucial to have direct communication with the galvanizer early in the design phase to address the following concerns:
Maximum Article Size for Progressive Dipping Because progressive dipping is simply the process of coating the steel part in two passes, only half of the article length or height must fit into the kettle to coat the entire article by this process. In other words, if at least half of the piece can fit in the bath, the part can be galvanized on one side, re-hung, and then dipped on the remaining surface. In essence, this would nearly double the article size that can be coated, depending on the kettle and article dimensions. However, it is important to consider that when increasing the length and height of the article beyond the kettle size for progressive dipping, the kettle width becomes the primary dimensional constraint. The width of the article must still be kept within the kettle width dimension in order to place the article partially within the bath. Kettle dimensions for all member galvanizers can be confirmed on the AGA website.
Lifting Orientation and Handling The maximum article size which can be progressively dipped may be further limited by the layout and lifting capabilities of the hot-dip galvanizing plant. Discuss lifting orientation and lift points directly with the galvanizer to avoid clashing of the article with nearby walls or equipment at the plant for both passes to produce the coating. Additionally, confirm the article weight is within the safe working load limit of the available lifting equipment.
Warpage & Distortion Progressive dipping results in uneven heating and cooling of the material to apply the full coating, increasing the risk of distortion. When progressive dipping is required, the risk of distortion can be significantly reduced by consulting with the galvanizer to take into account length variations of the assembly and by planning for thermal expansion conditions.
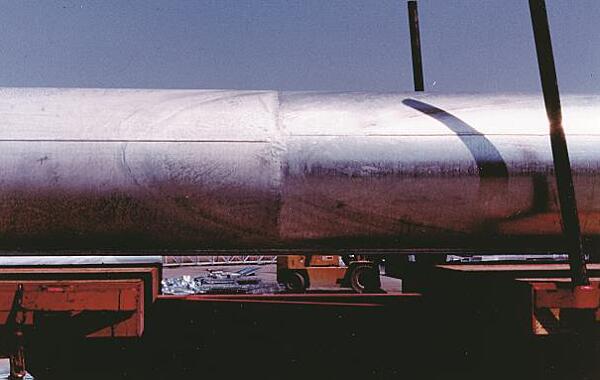
Overlap Line Progressively dipped pieces often have an overlap area that is visible on the piece. The line or darker area is purely cosmetic and will fade over time as the coating weathers naturally. As the overlap area will most likely develop a thicker coating, it is important to consider if the excess zinc will impact a connection point with other pieces. If required, the excess coating thickness can be buffed or ground down to match the surrounding coating.
Temperature Variations Uneven heating and cooling of the article are inevitable when progressive dipping since one end of the construction will always be in the molten zinc bath, while the other end is exposed to cooler air. Therefore, progressive dipping results in different expansion rates for the upper and lower part of the component, leading to thermally induced tensions in the component which may lead to distortion. The risk of distortion can be reduced by consulting with the customer to take into account length variations of the assembly and planning for thermal expansion conditions. Additionally, ensuring vent and drain holes are adequately sized will enable rapid immersion and withdrawal of the object from the bath. Bracing (permanent or temporary) can also be incorporated to provide stability during the thermal expansion and contraction cycle. Especially for welded assemblies, confirm with the engineer/owner that the welds and the physically constrained/framed portions of the assembly are capable of handling the increased stresses from thermal expansion at the zinc bath temperature. Analyzing the conditions of the first dip is most critical as the temperature gradient will be greatest. The temperature differential is less severe for the second dip due to heat retained in the steel from the first immersion.
© 2025 American Galvanizers Association. The material provided herein has been developed to provide accurate and authoritative information about after-fabrication hot-dip galvanized steel. This material provides general information only and is not intended as a substitute for competent professional examination and verification as to suitability and applicability. The information provided herein is not intended as a representation or warranty on the part of the AGA. Anyone making use of this information assumes all liability arising from such use.