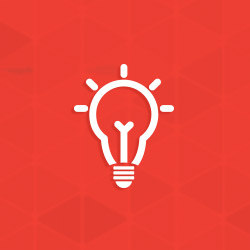
Weld Slag Clean Up Requirements prior to Galvanizing
Ive been asked to perform blast cleaning prior to galvanizing on all steel products that are welded. Why is this required and is this applicable for the MIG or TIG process when welding with bare or uncoated wire?
When welded structures are hot-dip galvanized, the weld area cleanliness significantly affects the quality and appearance of the galvanized coating around the weld. If a coated electrode (i.e. a flux-coated welding wire/rod/stick) is used during welding, all welding flux and slag must be cleaned by the fabricator prior to galvanizing or the zinc coating will not adhere to the weld area (causing bare spots in the coating).
Chemical cleaning solutions used in the galvanizing process cannot remove weld flux and slag. Therefore, weld slag must be removed by grinding, abrasive blast cleaning, wire brush, flame-cleaning, or chipping.
In order for weld slag to develop, flux must melt from the flux-coated welding wire/stick, then deposit onto the weld area. Therefore, only welds performed with flux-coated wire or a flux blanket are susceptible to the formation of weld slag. Welds performed with bare wire are not susceptible to weld slag formation and will therefore not require abrasive cleaning for this specific purpose.
See Table 1 for a list of common weld processes and whether weld slag formation is of concern for each process.
Welding Process | Acronym(s) | Potential for Slag Formation? |
---|---|---|
Shielded Metal Arc Welding (Manual / Stick Welding) |
SMAW / MMA | Yes Flux Coated Electrode |
Flux Cored Arc Welding | FCAW / FCA | Yes Flux Coated Electrode |
Submerged Arc Welding | SAW | Yes Granular Flux Blanket |
Gas Metal Arc Welding / Metal Inert Gas Welding |
GMAW / MIG | No |
Gas Tungsten-Arc Welding / Tungsten Inert Gas Welding |
GTAW / TIG | No |
Plasma Arc Welding | PAW | No |
© 2025 American Galvanizers Association. The material provided herein has been developed to provide accurate and authoritative information about after-fabrication hot-dip galvanized steel. This material provides general information only and is not intended as a substitute for competent professional examination and verification as to suitability and applicability. The information provided herein is not intended as a representation or warranty on the part of the AGA. Anyone making use of this information assumes all liability arising from such use.