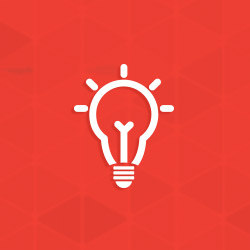
Cracking of HDG in the Area of the Weld
I recently galvanized a large overhead sign structure and was quite surprised that it cracked significantly around the weld areas after galvanizing. I wasn't aware that welded material that is going to be galvanized has the potential to crack. What is the cause of this cracking? Is there anything I can do to prevent this from occurring in the future?
The cracks found in your galvanized steel can be attributed to stresses introduced during the welding of two different thicknesses of steel. The stresses from the welding are from the weld metal itself, as it is typically harder and stronger than the base metal, and from the heat applied during welding. The welding process can increase the hardness and reduce the ductility of steel in the heat-affected zone, making it more susceptible to brittle fracture. Another factor that could potentially play a role in the cracking is hydrogen embrittlement. Harder, stronger steel is more susceptible to hydrogen embrittlement.
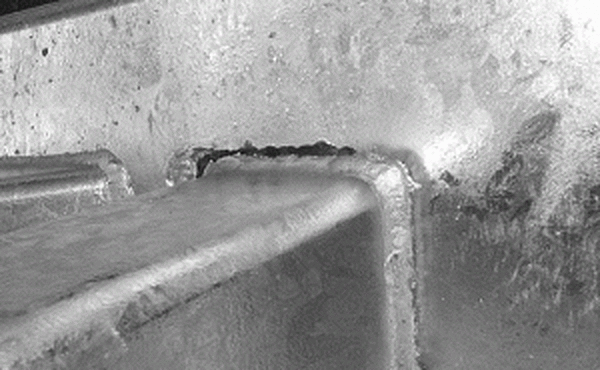
The weld metal and heat affected zones can obtain hardness values much higher than other areas of the steel. The hardness of steel is directly proportional to the tensile strength of the steel. If weld areas or heat affected zones obtain hardness values above 35 Rockwell C (steel with a Rockwell C hardness of 35 correlates to a tensile strength of 160 ksi [160,000 psi]), they are susceptible to hydrogen embrittlement. One studys results suggest that steels with hardness values above this are highly susceptible to cracking, especially when put under load. The fact that welding stresses are partially relieved in the galvanizing kettle, and the combination of different section thicknesses thermally expanding and contracting at different rates, combined to cause the cracking in your sign. As you can see from your pictures, all of the cracking originated in the weld area, particularly in the heat-affected zones where the hardness values could potentially be high. Also in these areas is the combination of two different thickness steels, which will expand and contract at different rates, adding even more stress to an already highly-stressed area.
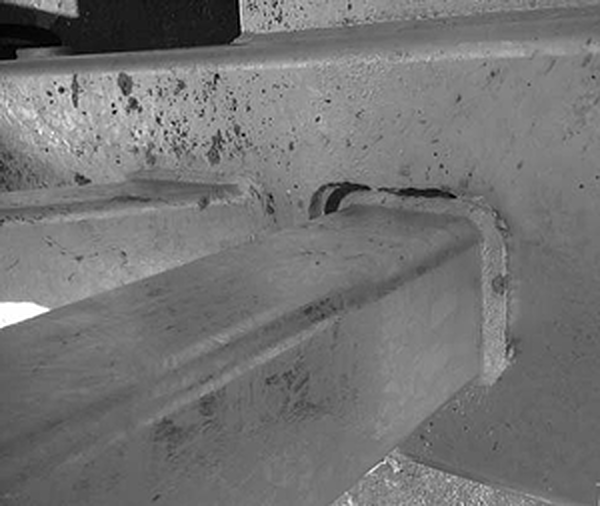
The answer to avoiding this problem (and most others) is to relieve stress. One such stress-relieving procedure can be found in ASTM A143, Standard Practice for Safeguarding Against Embrittlement of Hot-Dip Galvanized Structural Steel Products and Procedure for Detecting Embrittlement. Although welding is not specifically mentioned, a method for stress relief is explained. Included in Section 5.3 is a statement that details the procedure for stress relieving cold-formed steel and can be applied to relieving stresses from welding. It states that stress relieving should be conducted at a maximum of 1100°F (595°C) for approximately one hour per inch (25.4 mm) of section thickness.
The heat treatment of steel prior to galvanizing will relieve stresses in the steel and reduce the potential for cracking. It will reduce hardness values in the weld material and, more importantly, the heat-affected zone. There are many factors that can play a role in the cracking of structural steel. Designing fabrications to eliminate zones of high potential stress, or relieving these stresses prior to galvanizing, should eliminate future cracking in these structures.
© 2025 American Galvanizers Association. The material provided herein has been developed to provide accurate and authoritative information about after-fabrication hot-dip galvanized steel. This material provides general information only and is not intended as a substitute for competent professional examination and verification as to suitability and applicability. The information provided herein is not intended as a representation or warranty on the part of the AGA. Anyone making use of this information assumes all liability arising from such use.