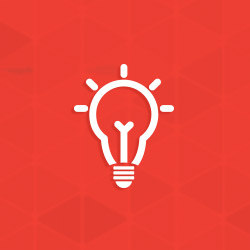
Design Considerations for Fabricating Steel to be Hot-Dip Galvanized
What considerations should I keep in mind when designing steel fabrications to be galvanized?
As the name implies, steel is dipped into a bath of molten zinc during the hot-dip galvanizing process. While the process is inherently simple, hot-dip galvanizing is different than painting or other corrosion protection coating systems, and therefore presents unique requirements during the design stage in order to ensure a high-quality zinc coating. ASTM A385, Standard Practice for Providing High-Quality Zinc Coatings (Hot-Dip), specifies design recommendations that should be followed when fabricating steel to be galvanized. There are too many recommendations to be discussed in this issue, so they will be broken up and presented as a series continuing into later issues. In this, the fourth part of the series, we will be discussing how to select a proper steel to be hot-dip galvanized.
Hot-dip galvanizing is a versatile process which can provide quality coatings to most iron-containing materials. This includes plain carbon steel, hot-rolled steel, cold-rolled steel, cast steel, ductile iron, cast iron, and even stainless and weathering steels. However, there are some attributes of the steel that can affect the characteristics of the galvanized coating.
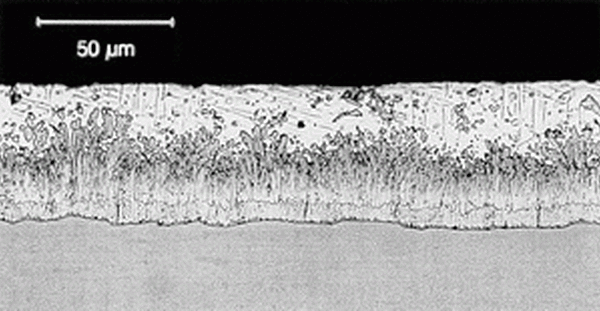
The galvanizing process relies on a diffusion reaction between iron and zinc that create zinc-iron alloy layers of coating. A free zinc layer adheres to these layers as the steel is drawn from the molten zinc bath to create the typical galvanized coating. However, there are some steel chemistries that may lead to an atypical galvanized coating consisting of only the zinc-iron alloys and a matte finish. In rare occasions, coatings such as these may become excessively thick and brittle. In order to provide a typical galvanized coating with an outer free zinc layer, some care must be taken when selecting the steel to be galvanized with attention to the steel chemistry. The guidelines below will assist in the steel selection process. Steel with chemistries outside these boundaries are considered reactive steels and may form the atypical coating discussed above. When deciding if the steel chemistry falls within these suggested limits, keep in mind the mill test report you are given may not be 100% accurate.
- Carbon levels should be below 0.25%
- Manganese levels should be below 1.3%
- Phosphorous levels should be below 0.04%
- Silicon levels should be below 0.04% or between 0.15% and 0.22% (See Sandelin Curve)
- The Silicon Equivalent should be below 0.04% or between 0.15% and 0.22%
Silicon Equivalent = Silicon content + [2.5xPhosphorous content]
An accelerated growth of the galvanized coating may lead to a matte gray finish, but this is primarily seen as a cosmetic issue. Other than the rare case of the coating becoming excessively thick, the corrosion protection performance of the steel is not affected by its appearance.
While it is important to keep steel chemistry in mind when selecting a steel for your galvanizing project, it is much more important to communicate with your galvanizer throughout the design process. As is the case with most design considerations, your galvanizer will have experience with the subject and may be able to propose solutions not mentioned here. If the galvanizer is made aware of the issue in advance, galvanizing reactive steel can be done with successful results.
© 2025 American Galvanizers Association. The material provided herein has been developed to provide accurate and authoritative information about after-fabrication hot-dip galvanized steel. This material provides general information only and is not intended as a substitute for competent professional examination and verification as to suitability and applicability. The information provided herein is not intended as a representation or warranty on the part of the AGA. Anyone making use of this information assumes all liability arising from such use.