Welding Galvanized Steel
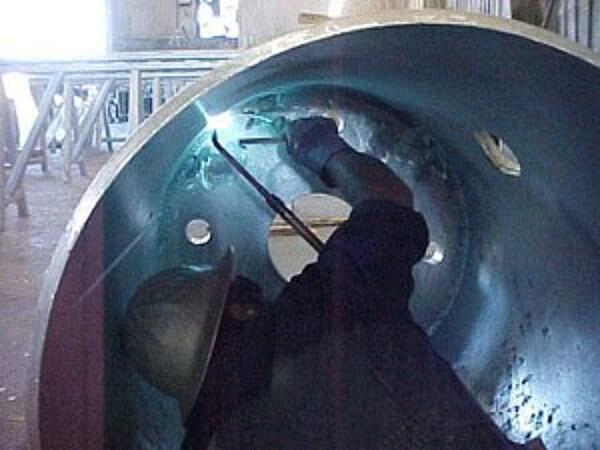
Welding fabrications before and after galvanizing is common. Requirements to allow for this are relatively simple to implement. Both welding before and after galvanizing are compatible with the objective of providing superior corrosion protection.
Many commonly practiced welding and cutting techniques can be used on galvanized steel (see American Welding Societys (AWS) specification D-19.0, Welding Zinc Coated Steel). Welding on galvanized steel can be necessary if the final structure is too large to be dipped in a galvanizing bath or for structures that must be welded in the field.
AWS D-19.0 calls for welds of galvanized steel on areas free of zinc. Thus, for galvanized structural fabrications, the zinc coating should be removed at least 1-4 (2.5-10 cm) from either side of the intended weld zone and on both sides of the piece. The most common and preferred removal method is grinding back the zinc coating, but burning the zinc away or pushing it back from the weld area are also effective.
Welding galvanized steel should always be done in well-ventilated locations to minimize fume inhalation. The AWS publication, AWS/ANSI Z49:1, Safety and Cutting in Welding, covers all aspects of welding safety and health. However, galvanized steel can be welded without removing the zinc coating if special procedures are followed.
Listed below are abbreviated procedures for welding galvanized steel using the most common welding techniques.
- Gas Metal Arc Welding
- Shielded Metal Arc Welding
- Oxyacetylene Welding
- Stud Welding
- Welding Rebar
- Friction Welding
- Resistance Welding of Zinc-coated Steel
Gas Metal Arc Welding (GMAW)
Gas metal arc welding, also known as Metal-Inert Gas (MIG) welding, is a versatile semi-automatic welding technique particularly suited for the welding of thinner materials (<1/2 [13 mm] thick).
Welding speeds for GMAW are typically slower for galvanized surfaces. These reduced speeds allow longer time for the zinc to burn off at the front of the weld pool. Increasing the current supplied to the welding electrode may provide sufficient means to burn off zinc coatings of greater thickness.
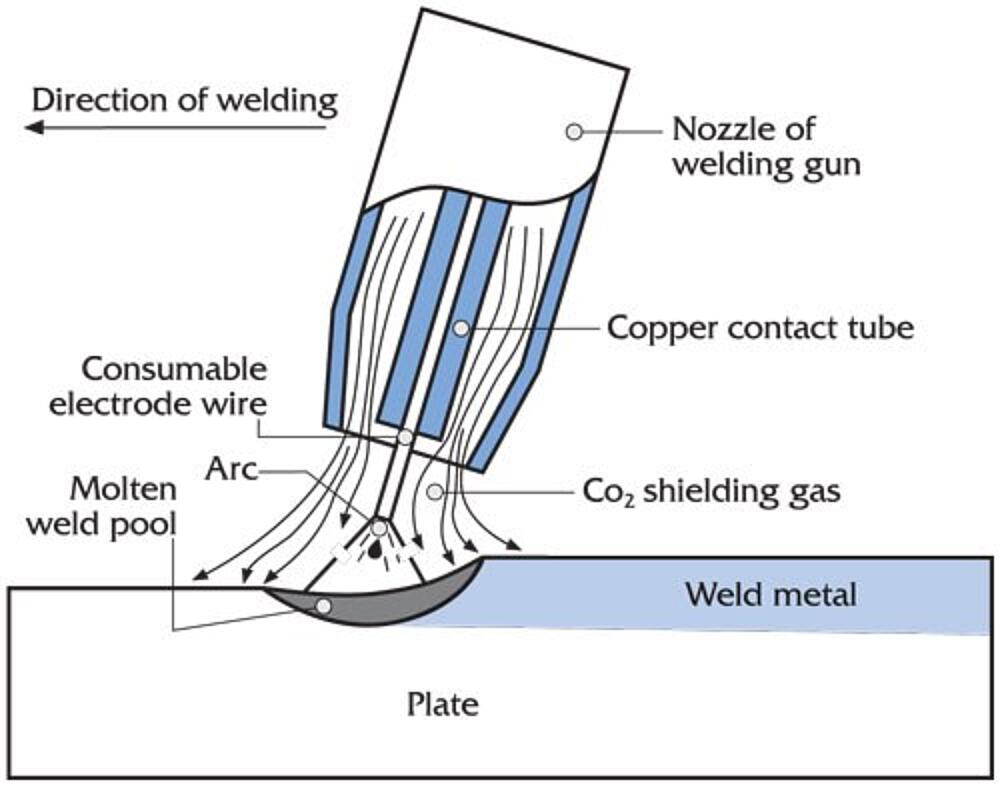
Weld penetration depth is decreased when welding galvanized steel. When performing butt-welds, larger gaps must be provided. Consistent penetration is achieved by employing a side-to-side motion of the welding torch when butt-welding in the flat position. Spatter increases when welding galvanized steel using CO2 shielding gas. The formation of spatter particles is directly proportional to the thickness of the zinc coating. Therefore, spatter formation is greater for hot-dip galvanized steel than continuously galvanized (sheet) steel.
Spatter particles can adhere to the steel surface causing an unsightly appearance. Applying a silicon-, petroleum- or graphite-based spatter release compound before welding can reduce spatter adherence. These compounds allow spatter particles to be easily brushed off after welding.
Increasing the heat, reducing welding speed, and using an argon-CO2 shielding gas when GMA welding can give a more stable arc and produce smoother weld deposits with minimum spatter and zinc loss.
Shielded Metal Arc Welding (SMAW)
The most common arc welding process is shielded metal arc (SMAW) welding. SMAW welding is a process in which flux-covered electrodes ranging from 9 to 18 inches (23 to 46 cm) in length, and 1/16 to 5/16 inches (1.6mm to 8.0 mm) in diameter, are used.
Weld depth penetration is decreased in the SMAW welding of galvanized steel, as is the case for GMAW welding, the root opening for butt-welds must be increased from that of uncoated steel surfaces. However, it is possible to obtain full weld depth penetration by altering the normal weld techniques for uncoated steel. If the angle of the electrode is reduced from the normal 70º to 30º , and the weld speed is reduced significantly, normal weld depths can be achieved by moving the electrode back and forth in line with the joint.
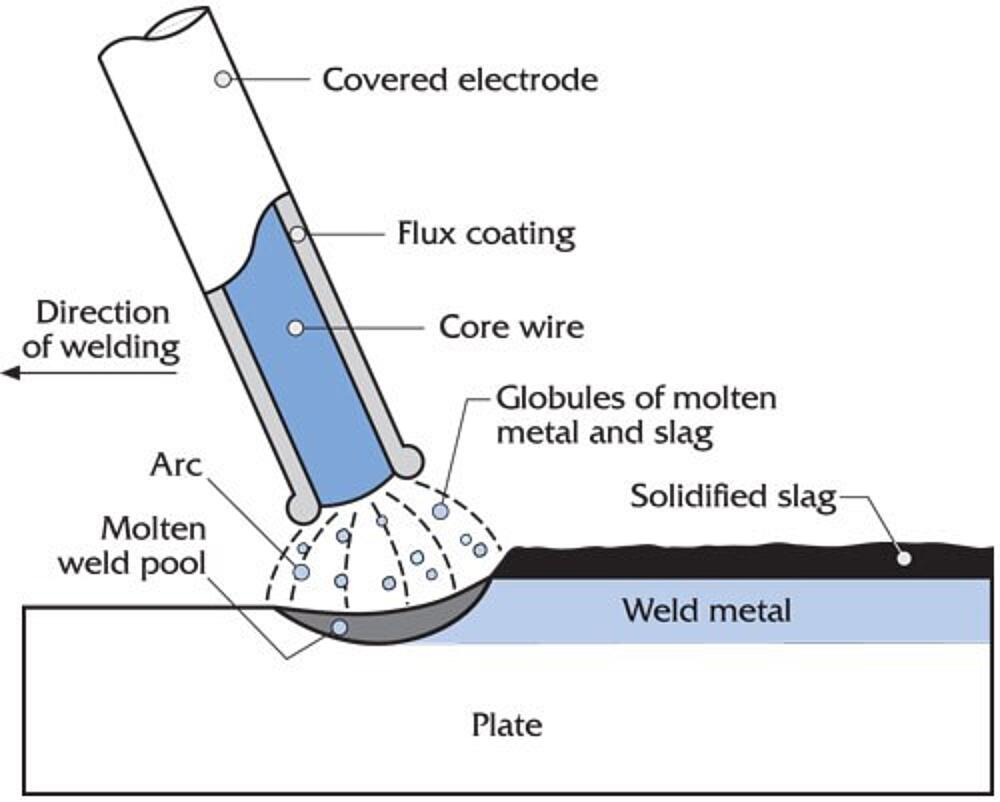
Spatter formation also increases using SMAW welding. Generally, spatter formation does not increase to an extent where anti-spatter compounds are required. Slower welding speeds allow for more of the zinc coating to burn off and reduce the amount of spatter formation. As for GMAW welding, it is not usually necessary to increase the current to the electrode to increase the amount of zinc burned off.
Reducing the angle of the electrode and reducing the weld travel speed will significantly increase the quality of SMAW weld on the zinc-coated surface. Steels with thicknesses greater than 1/2 (13 mm) are recommended to be welded with SMAW. The following considerations should be noted when applying SMAW on galvanized steel:
The welding electrode should be applied slower than normal, with a whipping action that moves the electrode slightly forward of the weld pool and then backward into the weld pool. This ensures that all of the zinc is burned off before the weld bead progresses. After volatilization, the welding is the same for uncoated steel.
Weaving and multiple weld beads should be avoided. Heat input into the joint should be kept to a minimum to avoid undue damage to the adjacent coating, while not sacrificing the heat required to burn off the zinc prior to bead progression. A short arc length is recommended for welding in all positions to give better control of the weld pool and to prevent either intermittent excessive penetration or undercutting. Weld penetration depth is decreased when welding galvanized steel. When performing butt-welds, larger gaps must be provided. Consistent penetration is achieved by employing a side-to-side motion of the welding torch when butt-welding in the flat position. Deviations from SMAW techniques for uncoated surfaces and zinc-coated surfaces occur due to the extra heat required for removal of the zinc coating. Inducing a whipping motion during welding allows for as much as possible of the zinc coating to be removed prior to weld formation. A more disturbed weld pool results, increasing the fluidity of the slag and spatter formation.
Oxyacetylene Welding
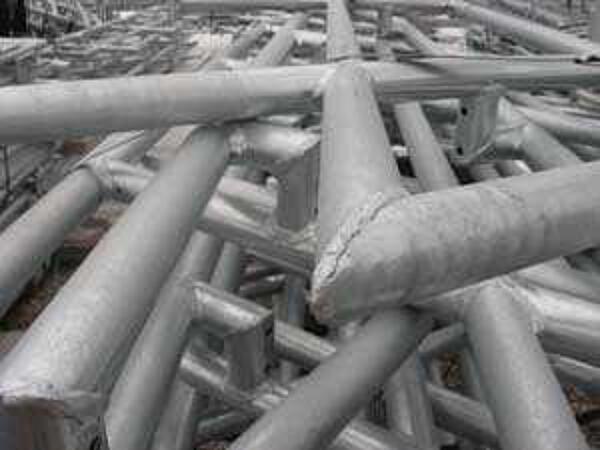
All grades of hot-dip zinc coated steels can be welded by oxyacetylene fusion welding. Preparation for welding is similar to that for welding uncoated steel. Because low travel speed is necessary for this process, which is necessary to bring the joint edges to the fusion temperature, the extra heat causes the zinc coating to be affected over a much greater area than when using faster welding processes. Best results are obtained when the filler rod is moved back and forth, producing a ripple weld. Nozzle sizes similar to those used for welding uncoated steel of similar thickness should be used. Welds should not be remelted by a flame to improve their appearance; this will result in additional loss of the zinc coating.
Stud Welding
If galvanized studs are to be welded onto galvanized surfaces, it is essential to remove the zinc coating from the end of the stud and the surface onto which the stud is to be welded. If the end face is still zinc coated, the weld metal may be violently expelled from the joint because of volatilization of the zinc from the faying surface.
Welding Rebar
The welding of reinforcing bars can be achieved utilizing SMAW or GMAW without removing the zinc coating. However, removing the zinc coating within 2 (50 mm) of the weld joint is preferred. Refer to the American Welding Societys Manual D 1.4 for additional information on welding rebar.
The bar ends may be prepared to the required profile by sawing, grinding, or oxygen cutting. Cold-shearing is not recommended and bars prepared in this way should be carefully inspected to ensure that the shearing process has not damaged the ends. If damage is found, the ends must be cut back to sound metal. Fusion faces should be free from irregularities, which would interfere with the deposition of the specified size of weld, or cause defects. If the ends of the reinforcing bars are prepared at the site, the prepared edges will be free from zinc and welding procedures are the same as for uncoated bars. The presence of zinc on the end of the bars to be welded has no significant effect on the welding procedure or the time required to make the joints. The only difference occurs in the formation of fumes when the prepared edges were coated with zinc.
Friction Welding
Flat-ended studs, whether uncoated or galvanized, cannot be welded to galvanized plate because the alloy layers in the zinc coating appear to act as a low friction-bearing surface and insufficient heat is developed for welding. Using pointed studs solves the problem with friction welding studs to galvanized surfaces. The best results are obtained on studs with a point having a 120º angle. The presence of zinc coating on the stud increases the time required for welding.
Resistance Welding of Zinc-Coated Steel
Resistance welding is generally used to join galvanized steel less than 1/4 inch thick and with a zinc coating lighter than 1 oz/ft2 (305 g/m 2 ). Coatings up to 1.5 oz/ft 2 (460 g/m 2 ) have been successfully welded, but electrode life is much shorter than with lighter coatings. On heavier coatings, it is necessary to replace or redress worn electrodes more frequently. Sheet materials can be resistance welded without removal and with little damage to the zinc coating. Most after-fabrication galvanized coatings are thicker than recommended for resistance welding and become impractical to do so.