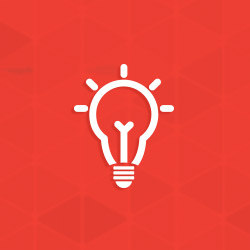
Advantages of HDG Fasteners
My customer is comparing hot-dip galvanizing with several different competing protective coatings to protect his bolts and other fasteners. Besides a longer service life, what other advantages does hot-dip galvanizing provide over competing protective coatings?
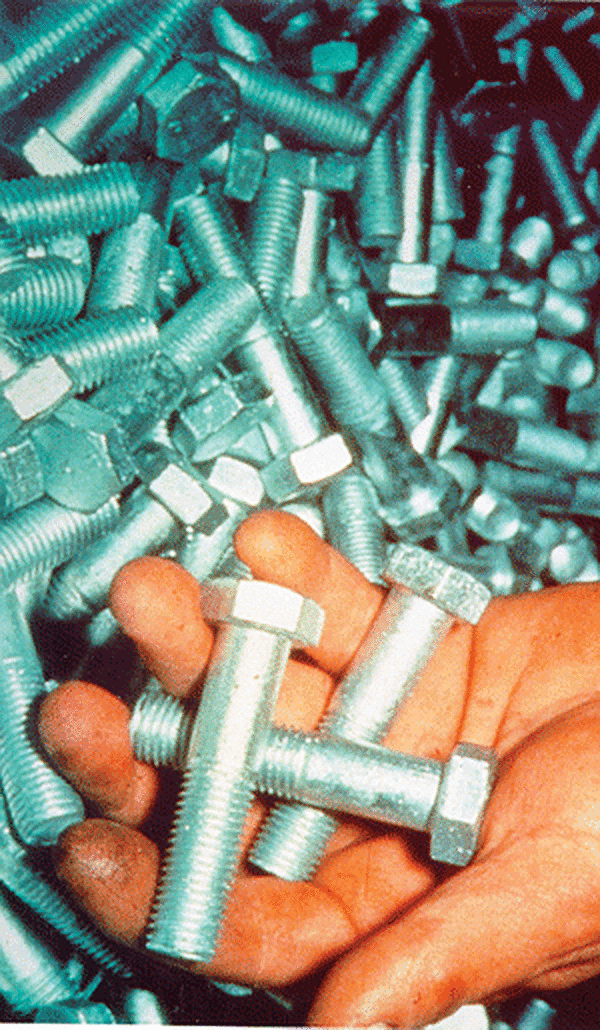
You are correct hot-dip galvanizing does provide a longer service life than competing protective coatings. In addition to a longer service life, hot-dip galvanizing is superior to competing protective coatings in several other ways. In this article, I will discuss how hot-dip galvanizing compares to zinc plating, mechanical galvanizing, painting, and epoxy coating. Bolts and other fasteners are unique because they often have many curved surfaces, edges, or corners. Hot-dip galvanizing provides uniform coatings on these surfaces because the process develops the zinc coating by way of a metallurgical reaction. During this reaction the coating grows perpendicularly to the base steel, meaning corners and edges develop coatings at least as thick as those on flat surfaces. In contrast, the zinc-plating and painting processes produce very thin coatings on edges and corners. The mechanical galvanizing method uses a deposition process and does not produce coating thicknesses as uniform as hot-dip galvanizing. In the mechanical galvanizing process, glass beads must peen the zinc onto the base steel to deposit the coating on the steel surface.
By their nature, threads are curved with many edges and corners, as are bolt heads. If they are not adequately coated, corrosion can begin first in these areas. Corrosion on threads can create safety issues due to reduced fastening strength, while corrosion on bolt heads can create rounded heads that can be easily stripped. Coating uniformity is very important to ensure a consistent coating across the length of the bolt or other fasteners. Hot-dip galvanizing has a built-in quality control measure by way of its metallurgical reaction. If the steel surface is not clean, the galvanized coating will not form. As long as the surface is clean, uniform coatings form, because the base steel is subject to the exact same process variables at the same time. Mechanically galvanized bolts can have coatings that are not properly compacted, creating the possibility for bare spots, and epoxy coated bolts can develop voids or holidays during the curing process. This means it is possible for epoxy coated bolts to begin corroding before the bolts even leave the processing facility.
For zinc coatings, corrosion protection is related to the amount of zinc on the base steel. Thicker coatings provide more corrosion protection. Zinc plating tends to produce very thin coatings suitable for indoor applications only. Higher coating densities provide more zinc per surface area and thereby provide more corrosion protection. The hot-dip galvanizing process creates coatings that have a higher density than mechanical galvanizing or zinc plating processes. Mechanical galvanizing produces a coating with a density of approximately 0.45 oz/ft2/mil compared to a coating density of 0.6 oz/ft2/mil produced by the hot-dip galvanizing method. This means hot-dip galvanized coatings provide at least 30% more zinc per unit area than mechanically galvanized coatings.
Another important consideration for protective coatings is the durability of the coating. Bolts and other fasteners are often repeatedly handled during processing, creating the possibility for abrasion of the coating. If the coating is scraped from the base steel prior to fastening, the corrosion process can be accelerated. The iron-zinc alloy layers of hot-dip galvanized coatings are harder than the base steel itself, providing outstanding abrasion resistance of the hot-dip galvanized coating. Other zinc coatings are only half as hard as the base steel, at best. In addition to the strong barrier protection of galvanized steel, all zinc coatings provide cathodic protection to the base steel when the coating is scratched. Paint and epoxy coatings provide only barrier protection and can be easily scraped from the base steel.
Along with abrasion resistance, adherence of the coating to the base steel is very important. If the coating does not adhere tightly to the base steel, it can easily be removed and thereby create bare spots. Hot-dip galvanizing has a bond strength of approximately 3600 PSI, whereas zinc plating and paint have a bond strength of only a couple hundred PSI. In conclusion, in addition to providing a longer service life than competing protective coatings, hot-dip galvanizing provides the superior coating of edges, corners, and threads, higher coating densities, increased abrasion resistance, and greater bond strength.
© 2025 American Galvanizers Association. The material provided herein has been developed to provide accurate and authoritative information about after-fabrication hot-dip galvanized steel. This material provides general information only and is not intended as a substitute for competent professional examination and verification as to suitability and applicability. The information provided herein is not intended as a representation or warranty on the part of the AGA. Anyone making use of this information assumes all liability arising from such use.