Hot-Dip Galvanized Coating
The coating that develops during the galvanizing process is metallurgically bonded to the steel - virtually becoming a part of the steel itself. During the reaction in the kettle, the zinc interacts with the iron in the steel to form a series of zinc-iron alloy layers. The photomicrograph below is a cross-section of the galvanized steel coating, showing a typical microstructure comprised of three alloy layers and a layer of pure metallic zinc.
- The thin Gamma layer composed of an alloy that is 75% zinc and 25% iron
- The Delta layer composed of an alloy that is 90% zinc and 10% iron
- The Zeta layer composed of an alloy that is 94% zinc and 6% iron
- The outer Eta layer that is composed of pure zinc
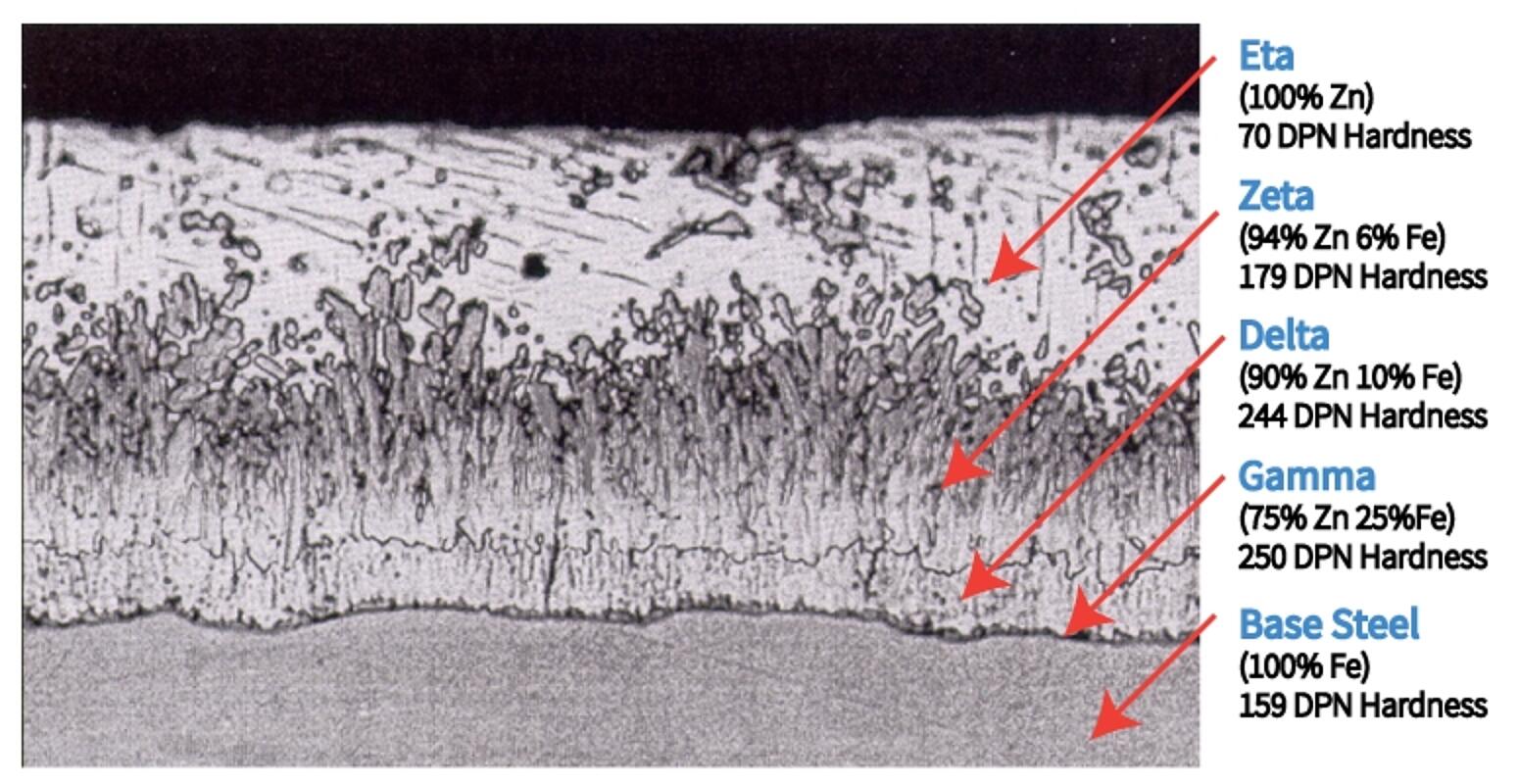
In addition to the chemistry of each layer, the figure identifies the hardness of each layer expressed as a Diamond Pyramid Number (DPN). The DPN is a progressive measure of hardness; the higher the number, the greater the hardness. Typically, the Gamma, Delta and Zeta layers are harder than the underlying steel. The hardness of these inner layers provides exceptional protection against coating damage by abrasion. The Eta layer is quite ductile, providing the coating with some impact resistance. The galvanized coating is adherent to the underlying steel on the order of several thousand pounds per square inch (psi). Other coatings typically offer adhesion rated at several hundred psi at best. Hardness, ductility, and adherence combine to provide the galvanized coating with unmatched protection against damage caused by rough handling during transportation to and/or at the job site, as well as in service. The toughness of the galvanized coating is extremely important since barrier protection is dependent upon the integrity of the coating.
Galvanized Coating Thickness
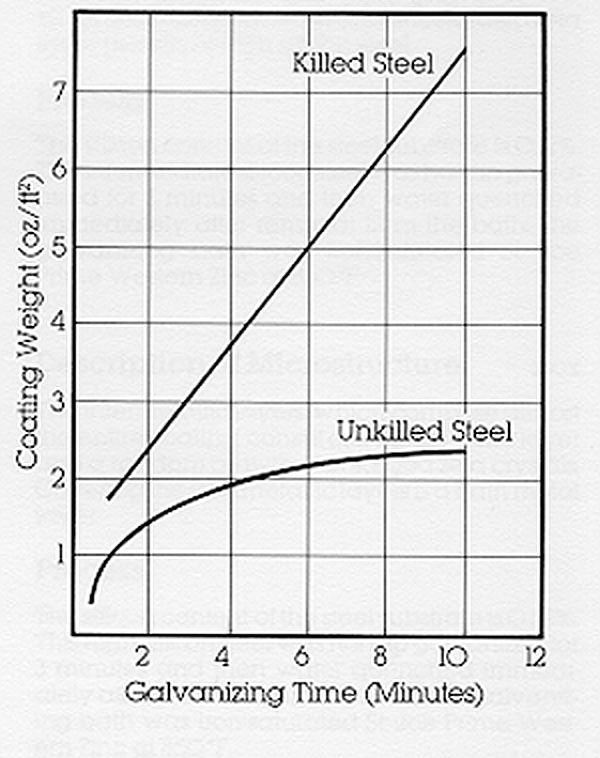
The American Society of Testing and Materials International (ASTM), the Canadian Specification Association (CSA) and the American Association of State Highway and Transportation Officials (AASHTO) specifications establish minimum standards for the thickness of galvanized coatings on various categories of items. These minimum standards are routinely exceeded by galvanizers due to the nature of the galvanizing process.
Factors influencing the thickness and appearance of the galvanized coating include chemical composition of the steel, steel surface condition, cold-working of steel prior to galvanizing, bath temperature, bath immersion time, bath withdrawal rate, and steel cooling rate.
The chemical composition of the steel being galvanized is very important. The amount of silicon and phosphorus in the steel strongly influences the thickness and appearance of the galvanized coating. Silicon, phosphorous or combinations of the two elements can cause thick, brittle galvanized coatings. The coating thickness curve shown in the figure below relates the effect of silicon in the base steel to the thickness of the zinc coating. The carbon, sulfur and manganese content of the steel also may have a minor effect on the galvanized coating thickness.
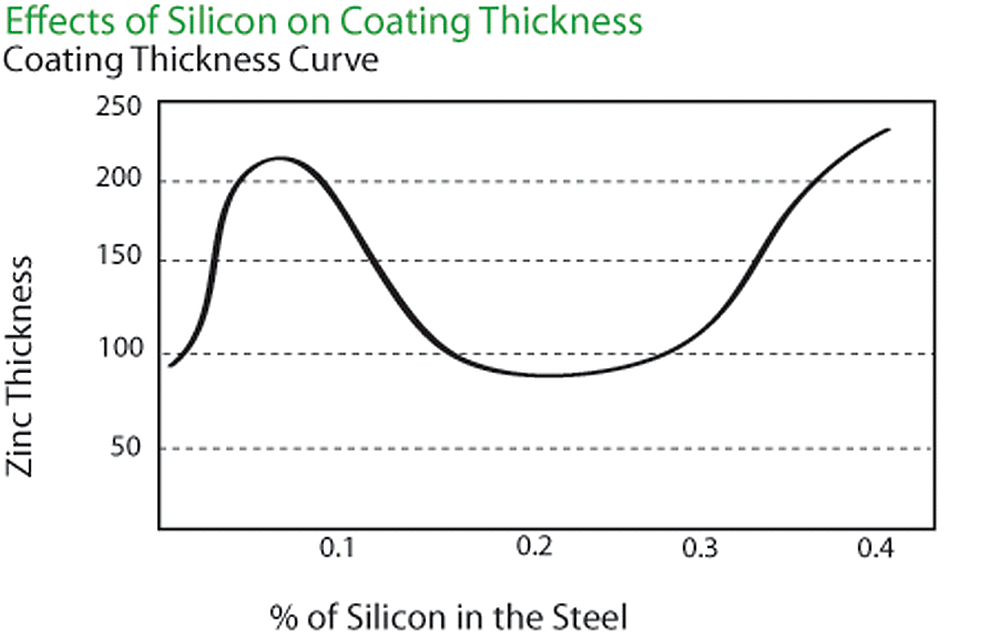
The combination of elements mentioned above, known as reactive steel in the galvanizing industry, tends to accelerate the growth of zinc-iron alloy layers. This may result in a finished galvanized coating consisting entirely of zinc-iron alloy. Instead of a shiny appearance, the galvanized coating will have a dark gray, matte finish. This dark gray, matte coating will provide as much corrosion protection as a galvanized coating having a bright appearance.
It is difficult to provide precise guidance in the area of steel selection without qualifying all of the grades of steel commercially available. The guidelines discussed below usually result in the selection of steels that provide good galvanized coatings.
- Levels of carbon less than 0.25%, phosphorus less than 0.04%, or manganese less than 1.35% are beneficial
- Silicon levels less than 0.04 % or between 0.15% and 0.25% are desirable
Even though it is not a part of the controlled composition of the steel, silicon may be present in many steels commonly galvanized. This occurs primarily because silicon is used in the deoxidization process in steel making and is found in continuously cast steel. The phosphorus content should never be greater than 0.04% for steel that is intended for galvanizing. Phosphorus acts as a catalyst during galvanizing, resulting in rapid growth of the zinc-iron alloy layers. This growth is virtually uncontrollable during the galvanizing process.
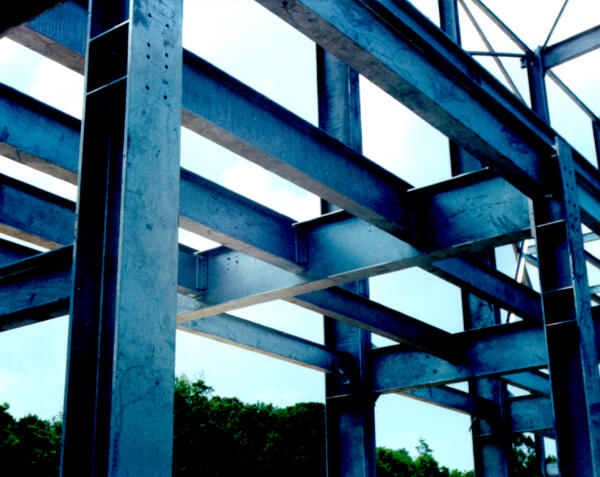
As the galvanizing reaction is a diffusion process, higher zinc bath temperatures and longer immersion times generally will produce somewhat heavier alloy layers. Like all diffusion processes, the reaction proceeds rapidly at first and then slows as layers grow and become thicker. However, continued immersion beyond a certain time will have little effect on further coating growth. When galvanizing reactive steels, the diffusion process proceeds at a faster rate, producing thicker coatings.
The thickness of the outer pure zinc layer is largely dependent upon the rate of withdrawal from the zinc bath. A rapid rate of withdrawal causes an article to carry out more zinc and generally results in a thicker coating.
ASTM, CSA and AASHTO specifications and inspection standards for galvanizing recognize that variations occur in both coating thickness and compositions. Thickness specifications are stated in average terms. Further, coating thickness measurements must be taken at several points on each inspected article to comply with ASTM A123/A123M for structural steel, A153/A153M for hardware, or A767 for reinforcing steel bar (rebar).
Appearance
Galvanized coatings are generally bright and shiny but within a year will weather to a uniform dull gray appearance. The basic finish requirements of the galvanized coating are that it be relatively smooth, continuous, and free from gross surface imperfections. Smoothness is an ambiguous term; the product's end use must be the determining factor in setting tolerances for smoothness. The galvanized coating is continuous and provides optimum corrosion protection.
Handling techniques for galvanizing may require the use of chain slings, wire or other holding devices to lower material into the galvanizing kettle if suitable lifting features are not available on the item. Chains, wires, and special jigs used to handle the items may leave a mark on the galvanized item. These marks are not detrimental to the coating, nor are they cause for rejection. If considered necessary, or expose bare steel, these areas can be easily touched up using the procedures described in ASTM A780.
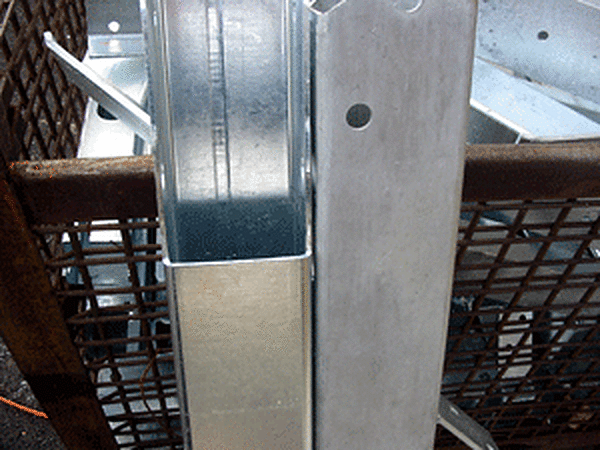
Differences in the luster and color of galvanized coatings do not significantly affect corrosion resistance. The presence or absence of spangle has no effect on coating performance. The well-known spangled appearance found on galvanized products is a crystallization process dependent upon the zinc bath chemistry, the rate of cooling, the method of pickling, the steel chemistry, and the thickness of the coating. Dull gray or patchy matte gray galvanized coatings give a service life equal to bright or spangled coatings since the service life depends on the zinc coating thickness. Variations in coating appearance or finish are important only if they will affect the intended use of the article. The primary function of the galvanized coating is corrosion protection.
Regardless of the initial appearance (whether bright and shiny, matte gray, or a combination of these), all galvanized steel parts take on a uniform matte gray over time. As the coating naturally weathers and develops its protective zinc patina, the result is a soft gray appearance - evening out any differences in appearance that may have existed originally.
Surface Reflectivity
The bright shiny appearance of a newly galvanized coating is sometimes not desired depending on the application. Some government agencies require that the surface of coated steel products not exceed certain reflectivity values. In the early 1970s there were four separate power companies/agencies that demanded galvanized products be dulled, that is, their reflectivity needed to be reduced to a range of 12% to 18% before field installation.
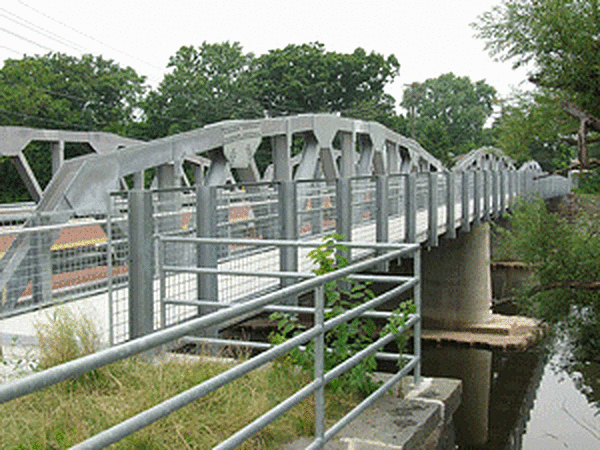
A newly-galvanized part with the normal pure zinc layer on the outside has a natural reflectivity of over 70% in the visible range. If the outer surface of the part has an intermetallic layer, rather than the normal pure zinc layer, the reflectivity is greatly reduced. This reflectivity change will also happen over time as the galvanized part weathers and the zinc oxides and carbonate films form on the surface of the part. However, if the surface must be dulled immediately, there have been some treatments used in the past that have proven successful. If surface reflectivity is an issue, contact your local galvanizer to discuss possible options to produce the desired coating appearance.