In Contact with Other Metals
Where zinc comes into contact with another metal, the potential for corrosion through a bimetallic couple exists. The extent of the corrosion depends upon the position of the other metal relative to zinc in the galvanic series, and to a lesser degree on the relative size of the surface area of the two metals in contact.
Any time a bimetallic assembly contains metal systems that are subject to galvanic corrosion, the ratio of the cathodic area to that of the anode must be carefully considered. The corrosion current that flows between the cathode and anode is independent of area, but the rate of penetration at the anode is dependent on the current per unit area, that is, current density. Therefore, it is undesirable to have a large cathode surface in contact with a small anode surface. The rate of penetration from corrosion increases as the ratio of the cathode to anode surface area increases.
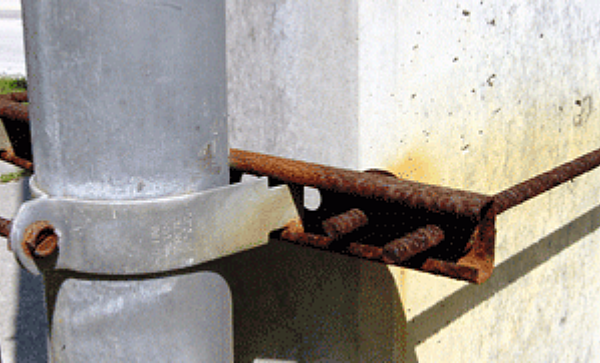
For example, when using a bare steel plate with a zinc rivet, the ratio of the cathode surface area to the anode surface area is large, and the rivet will fail rapidly because of accelerated corrosion. When combining a zinc plate with a stainless steel rivet, the area ratio between the cathode and anode is reversed, and although more surface area is affected, the depth of penetration is small; the fastener should not fail because of corrosion.
The behavior of galvanized coatings in contact with various metals is summarized in the table below. The information given is provided as a guide to avoid situations where corrosion may occur when galvanized surfaces are in contact with another metal.
The following information provides more detail on other common metals used in construction that may come in contact with hot-dip galvanized steel. For more detailed information about galvanic corrosion and hot-dip galvanizing in contact with dissimilar metals, see our primary page on Dissimilar Metals in Contact.
Copper and Brass
If an installation requires contact between galvanized materials and copper or brass in a moist or humid environment, rapid corrosion of the zinc may occur. Even runoff water from copper or brass surfaces can contain enough dissolved copper to cause rapid corrosion. If the use of copper or brass in contact with galvanized items is unavoidable, precautions should be taken to prevent electrical contact between the two metals. Joint faces should be insulated with non-conducting gaskets; connections should be made with insulating, grommet-type fasteners. The design should ensure water is not recirculated and water flows from the galvanized surface towards the copper or brass surface and not the reverse.
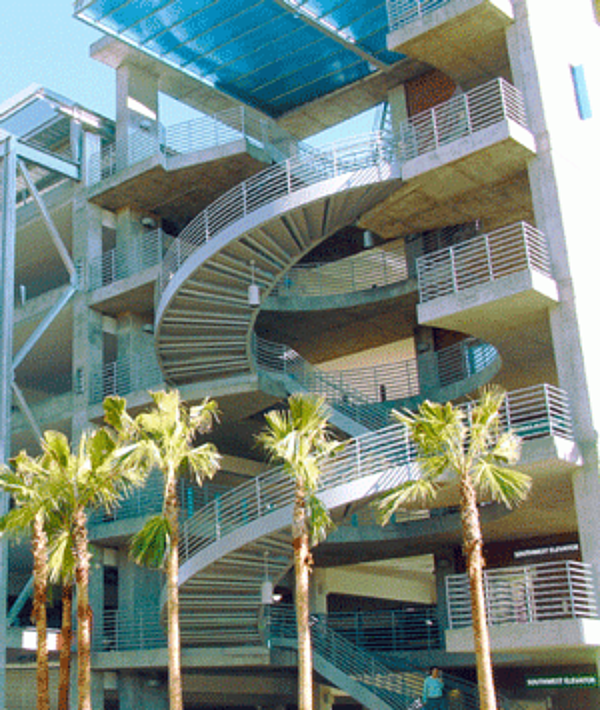
Other Zinc Coatings
There is no fear of galvanic corrosion when galvanized steel is in contact with other zinc coatings. Common examples include the use of mechanically galvanized bolts to connect high-strength HDG structural steel, and connections between metallized bridge girders and galvanized cross-braces. As zinc coating thickness is directly related to coating longevity, the component with the thinnest zinc coating will be the first to experience corrosion.
Painted Steel
In theory HDG steel may be successfully combined with painted steel, but this assumes a durable paint coating system which is diligently maintained. It is preferable to paint both metals to minimize exposure of the galvanizing should the painted components experience damage or weathering.
Aluminum
When used in mild-to-moderately corrosive environments and/or mild-to-moderate humidity, contact between a galvanized surface and aluminum is unlikely to cause substantial incremental corrosion. However, under very humid conditions or corrosive environments (including atmospheres close to bodies of salt water), these materials may require electrical isolation from each other for the structure to perform as intended.
Stainless Steel
When used in mild-to-moderately corrosive environments and/or mild-to-moderate humidity, contact between a galvanized surface and stainless steel is unlikely to cause substantial incremental corrosion. However, under very humid conditions or corrosive environments (including atmospheres close to bodies of salt water), these materials may require electrical isolation from each other for the structure to perform as intended.
Weathering Steel
When galvanized bolts are used on weathering steel, the zinc will initially sacrifice itself until a protective layer of rust develops on the weathering steel. Once this rust layer develops, it forms an insulating layer that prevents further sacrificial action from the zinc. The zinc coating has to be thick enough to last until the rust layer forms, usually several years. Most hot-dip galvanized bolts have enough zinc coating to last until the protective rust layer develops on the weathering steel, with only a minimal loss in coating life.
HDG and Black Rebar in Concrete
Iif galvanized steel and black steel are specified to be connected in concrete between different mesh layers of an exposed panel or the upper section only of reinforcement in a pile foundation in the ground, accelerated corrosion of zinc occurs after depassivation of the galvanized rebar in concrete10. Though depassivation does not often occur for decades, galvanic corrosion should be especially considered for high chloride environments (i.e. heavy road salting or marine environments). Common mitigations include galvanizing all rebar, supports, spacers, and tying wire; applying dielectric tapes for electrical isolation; and increasing concrete cover over the connection point.
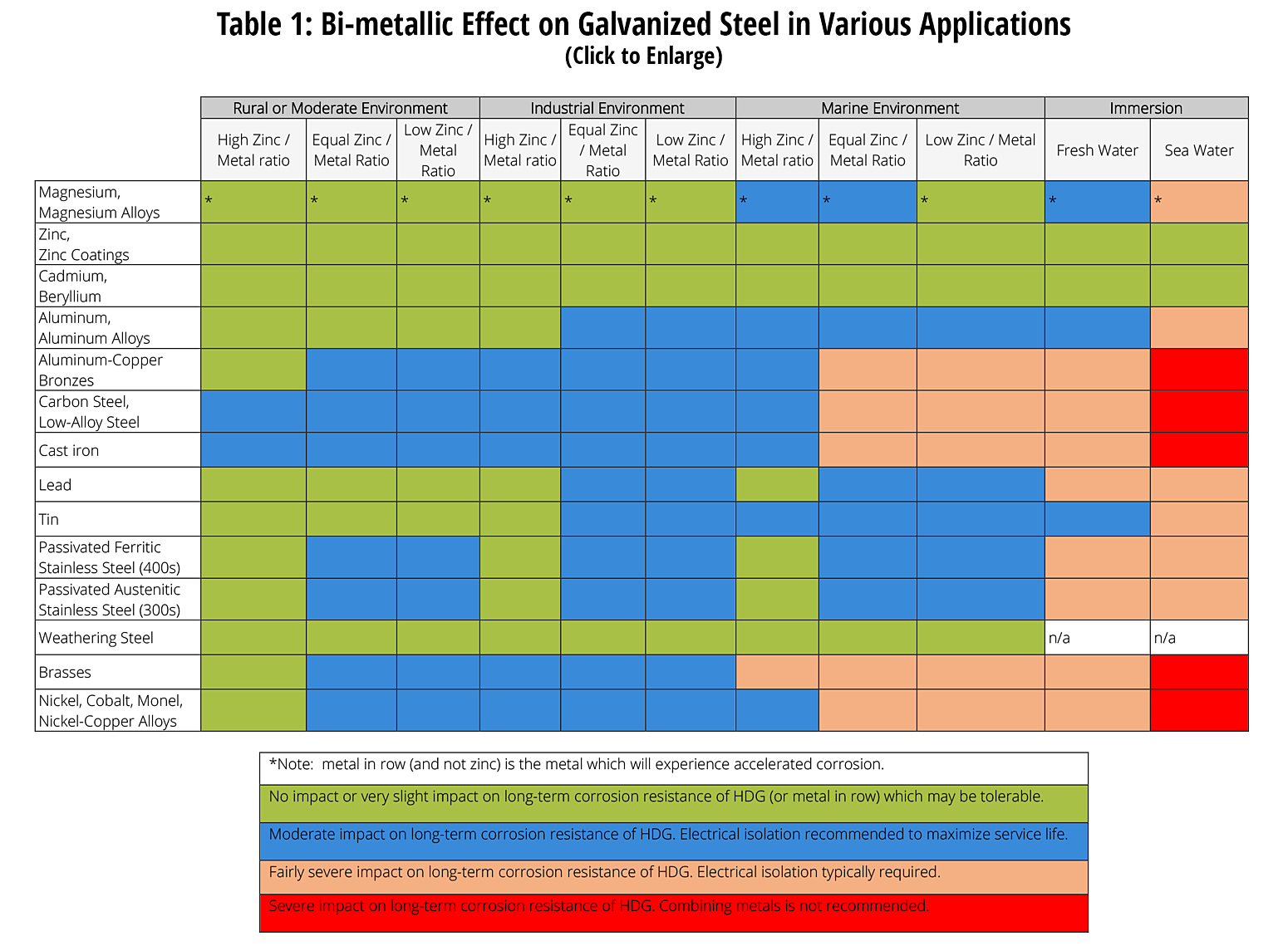