Corrosion Protection for Steel
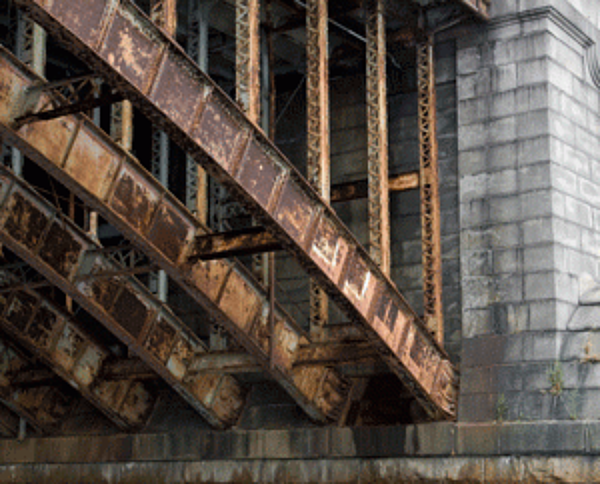
Steel is an abundant, efficient building material that provides specifiers design freedom. However, for projects exposed to the atmosphere and other harsh environments, it is critical to coat the steel for corrosion protection. Often large construction projects target a 50-100 year design life, highlighting the need for durable, long lasting corrosion protection. There are countless examples demonstrating the proven protection of hot-dip galvanizing in some of the harshest environments.
The reason for the extensive use of hot-dip galvanizing (HDG) is the three-fold protective nature of the coating. As a barrier coating, it provides a tough, metallurgically-bonded zinc coating that completely covers the steel surface and seals the steel from the corrosive action of the environment. Additionally, zinc's sacrificial behavior protects the steel, even where damage or a minor discontinuity in the coating occurs. Finally, the natural weathering of the coating results in the development of an additional layer of protection on the surface.
Barrier Protection
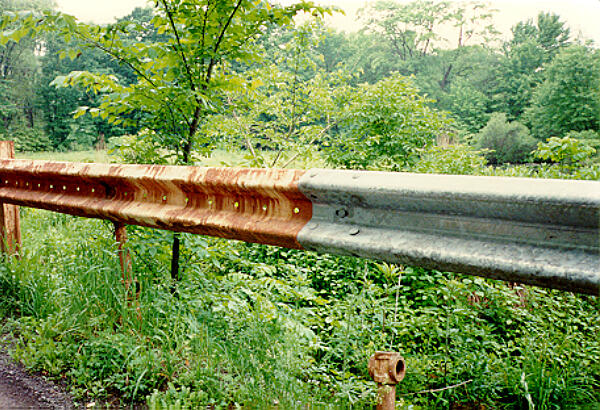
Barrier protection is perhaps the oldest and most widely used method of corrosion protection. It acts by isolating the base metal from the environment. Like paints, the hot-dip galvanized coating provides barrier protection to steel. As long as the barrier is intact, the steel is protected and corrosion will not occur. However, if the barrier is breached, corrosion will begin.
Because a barrier must remain intact to provide corrosion resistance, two important properties of barrier protection are adhesion to the base metal and abrasion resistance. The tightly-bonded, impervious nature of zinc makes galvanizing a very good barrier coating.Furthermore, zinc corrodes approximately 1/10 to 1/40 the rate of steel depending on the environment, making the corrosion rate of a thin zinc coating equivalent to a much thicker steel piece. Coatings such as paint that have pin holes are susceptible to penetration by elements causing underfilm corrosion to spread rapidly.
Cathodic Protection
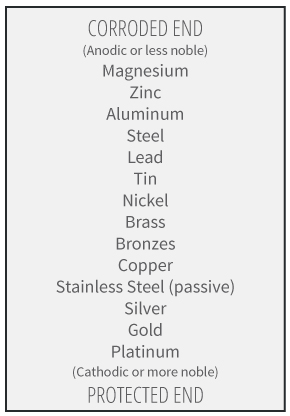
Cathodic protection is a more effective method of resisting corrosion. It requires changing an element of the corrosion circuit by introducing a new corrosion element, thus ensuring the base metal becomes the cathodic element of the circuit.
Hot-dip galvanizing protects steel cathodically similarly to the sacrificial anode method. Basically, a metal (zinc) anodic to the base metal (steel) is placed in the circuit to corrode in place of the base metal. The Galvanic Series of Metals is a list of metals arranged in order of electrochemical activity in seawater (the electrolyte). This arrangement of metals determines what metal will be the anode and cathode when the two are put in an electrolytic cell. Metals higher on the list are anodic to the metals below meaning they provide cathodic or sacrificial protection when the two are connected.
From the list, it is apparent in the case of hot-dip galvanizing, zinc will protect preferentially corrode to protect the underlying base steel. In fact, the cathodic protection of HDG ensures even if the coating is damaged to the point bare steel is exposed (up to ¼ inch in diameter), no corrosion will begin until all the surrounding zinc is consumed.
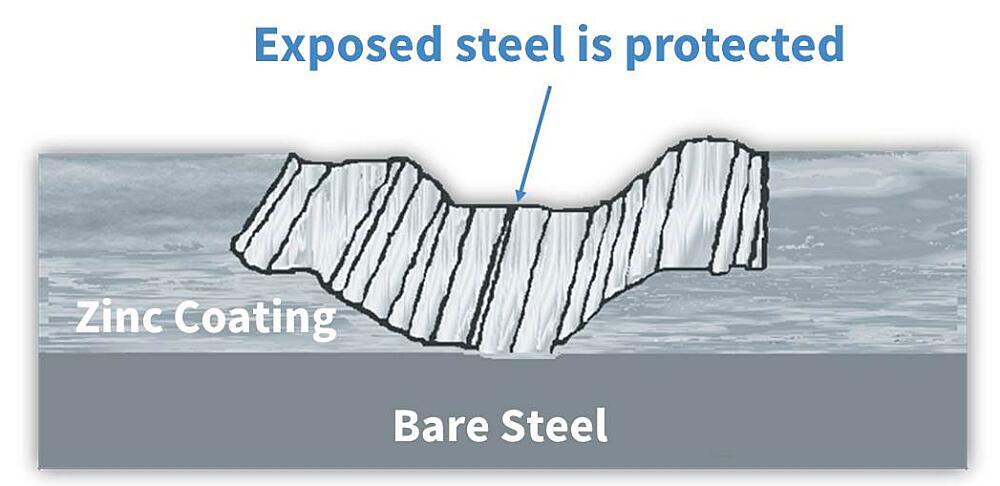
Zinc Patina
Different than barrier and cathodic protection which resist corrosion of the steel itself, the zinc patina protects the zinc coating. Zinc, like all metals, begins to corrode when exposed to the atmosphere. Thus, freshly galvanized steel progresses through a natural weathering process when exposed to wet and dry cycles in the environment.
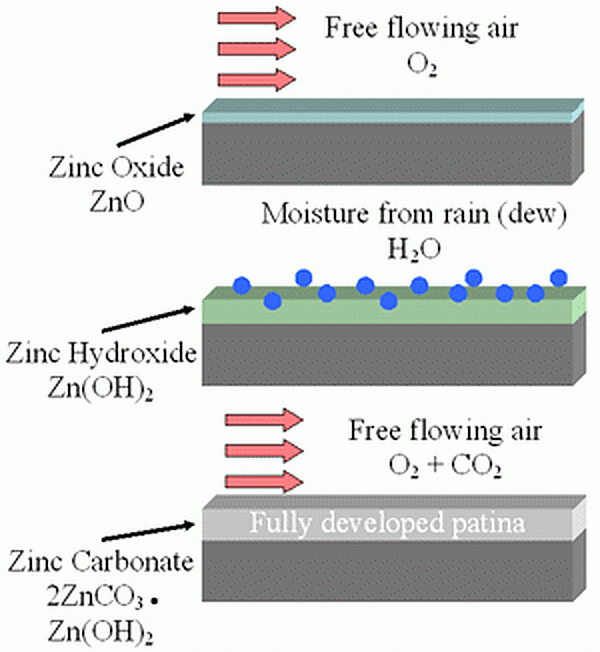
As galvanized coatings are exposed to free flowing air, the formation of the zinc patina begins with a thin layer of zinc oxides. Then as the piece is exposed to moisture (rainfall, dew, humidity) the zinc oxide particles react with the water to form a porous, gelatinous zinc hydroxide. Then during dry cycles, carbon dioxide reacts with the zinc hydroxide and converts to a thin, compact, and tightly adherent layer of zinc carbonate. The rate of the patina formation varies according to the environmental conditions, but it typically takes approximately 6-12 months to fully develop.
The fully developed patina is a passive, stable film that adheres to the zinc surface and is not water soluble so it does not wash off in the rain or snow. Because of this, the zinc patina corrodes very slowly and protects the galvanized coating underneath retarding the corrosion rate to about 1/30th the rate of steel in the same environment. As the zinc patina develops, the galvanized coating will turn a matte gray color.
The zinc patina formation is critical in the long-lasting corrosion resistance of hot-dip galvanizing. Because the patina development relies on natural wet and dry cycles found in the environment, the results of salt spray tests, which rely on constant wet exposure, are not accurate in predicting the life of galvanized coatings in the real world.