Durability
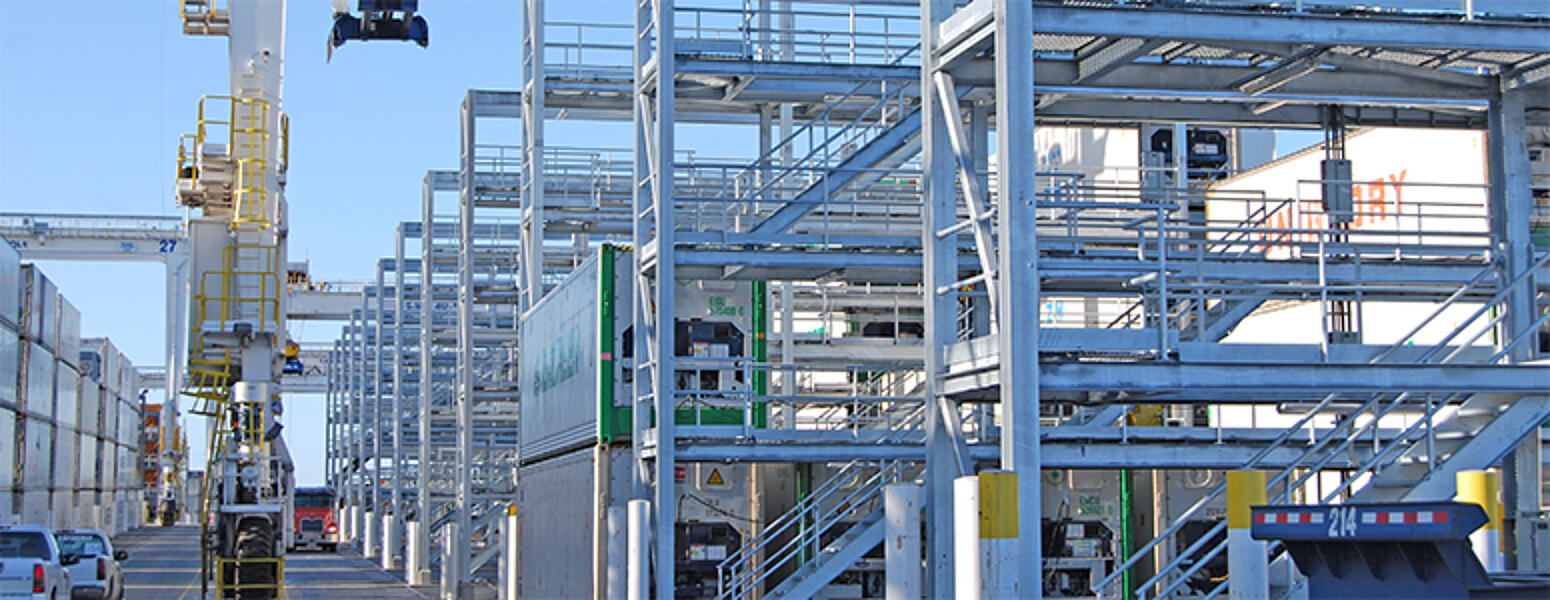
Hot-dip galvanized (HDG) steel has been specified extensively in petrochemical, industrial, power/utility, and bridge/highway projects because of its unmatched durability in these harsh environments. The heart of HDGs durability is the metallurgical bond of the coating. The reaction in the kettle between the zinc and the iron in the steel is unique and results in the coating becoming part of the steel rather than a surface element.
In addition to the bond strength which is approximately 3,600 psi, the way the coating develops is key to its long-term durability. The galvanized coating grows evenly throughout the part and covers all surfaces, ensuring its abrasion resistance is all-encompassing. This is important not only while in service but also during shipment and erection.
The three biggest factors in hot-dip galvanizings durability are abrasion resistance, uniform protection, and complete coverage.
Abrasion Resistance
A unique characteristic of the hot-dip galvanized (HDG) coating is the development of tightly-bonded (~3,600 psi), abrasion resistant intermetallic layers. The cross-section of a galvanized steel coating shows the three intermetallic layers (Gamma, Delta, and Zeta) and top layer of pure zinc (Eta). During the galvanizing process, these layers develop naturally during a metallurgical reaction between the iron in the steel and zinc in the kettle.
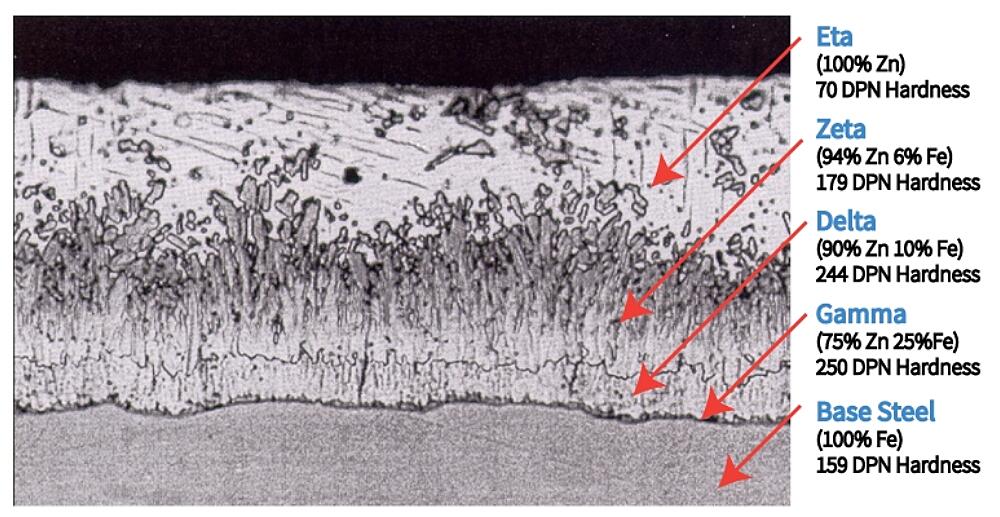
The photomicrograph also shows the hardness of each of the layers as a Diamond Pyramid Number (DPN). The DPN is a progressive measure of hardness; the higher the number, the greater the hardness. Typically, the Gamma, Delta, and Zeta layers are harder than the underlying steel. The hardness of these inner layers provides exceptional abrasion resistance. The outside, Eta layer is quite ductile which provides some impact resistance, which coupled with the inner layers makes damaging the HDG coating very difficult.
Hot-dip galvanizings abrasion resistance provides unmatched protection against damage caused by rough handling during transport and erection, as well as in service. Other coatings typically have bond strengths around 300-600 pounds per square inch (psi) in comparison to galvanizing which is around 3,600 psi. Therefore, other coatings can be easily damaged during shipment and construction, weakening their effectiveness, as barrier protection is dependent upon the integrity of the coating.
Uniform Protection
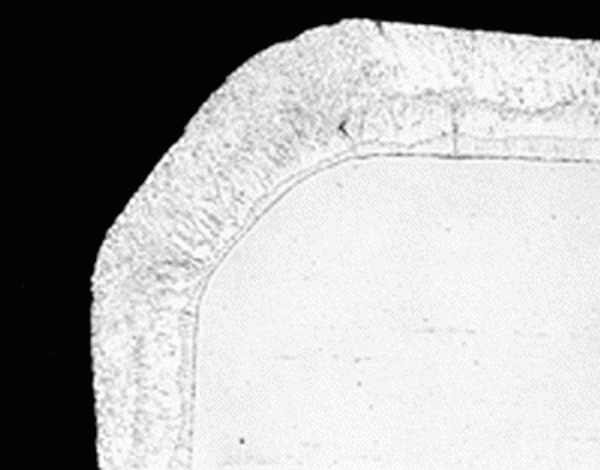
While steel is in the galvanizing kettle, the molten zinc reacts with the iron in the steel to form the galvanized coating. The interaction is a diffusion reaction, meaning the galvanized coating grows perpendicular to all surfaces. Therefore, the coating is naturally as thick on corners and edges as flat surfaces providing uniform protection. Since coating damage is most likely to occur at edges, added protection is needed most at these junctures.
The photomicrograph shows a cross-section of a corner galvanized steel demonstrating the uniform thickness around the bend. Brush- or spray-applied coatings have a natural tendency to thin at corners and edges leaving the part prone to attack. Conversely, the uniform protection of hot-dip galvanized steel leaves no weak points for accelerated corrosion.
Complete Coverage
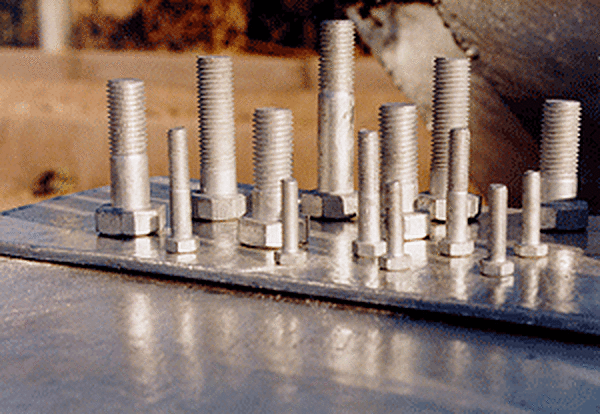
Hot-dip galvanizing is a total immersion process, meaning the steel is fully submerged into cleaning solutions and the molten zinc coating all interior and exterior surfaces. This complete coverage ensures even the insides of hollow and tubular structures and the threads of fasteners are coated.
As corrosion tends to occur at an increased rate on the inside of hollow structures where humidity and condensation occur, interior coverage is very beneficial. Hollow structures that are painted have no corrosion protection on the inside. Fully coating fasteners is equally important as they are utilized at connection points which are critical to structural integrity.