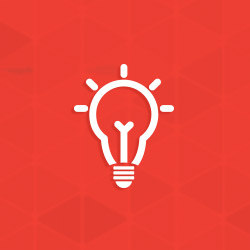
Most Common Appearance Concerns on HDG Steel
What are the most common appearance concerns with hot-dip galvanized steel?
Hot-dip galvanized coatings provide outstanding corrosion protection to the base steel, but since hot-dip galvanizing is an industrial process, its finish is not always smooth or uniform like paint or powder coating can be. And although galvanized steel is specified for its appearance in some cases, such as in nature settings where the weathered galvanized steel blends in with the environment, ASTM A385, Section 3.6, specifically states, In general, galvanized coatings are specified because of their corrosion resistance, not because of their appearance. The relative corrosion resistance of the normal and abnormal coatings is, for all practical purposes, equal. Some appearance issues on galvanized coatings occur more frequently, such as mottling, dull and shiny parts on the same fabrication, bare spots, inclusions (various types), and flaking or delamination of the galvanized coating.
Mottling
After galvanizing, the steel cools from a temperature of approximately 840 F to ambient temperature. If the steel is quenched, cooling takes place rapidly, but not all galvanizers have quench baths and quenching is not recommended on some designs due to the potential for warpage/distortion of the steel. When the newly galvanized steel is allowed to cool naturally (without quenching), it can take several hours for the steel to come down to ambient temperature. Thinner steel cools faster while thicker steel takes longer to cool. Sometimes an individual piece of steel will have different cooling rates.
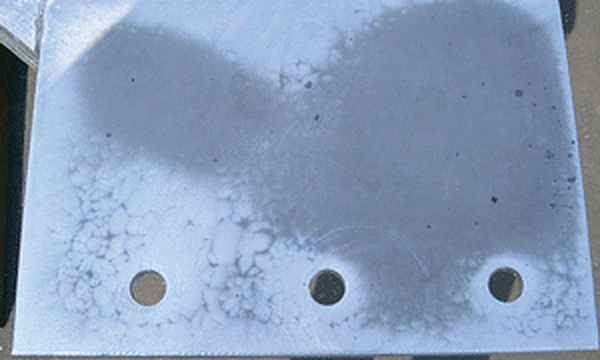
For example, the outer portion of a square plate can cool quicker than an interior portion. Because the interior portion remains hotter longer, it is possible for the galvanizing reaction to continue as long as that area is above 550 F and the continued reaction consumes the outer free zinc (eta) layer in the process. Because the galvanizing reaction continues on the interior portion and consumes the free zinc layer, but not the exterior portion of the steel (meaning the free zinc layer remains in those areas), this causes a nonuniform appearance of the galvanized coating; however, this difference in appearance does not affect the corrosion protection of the galvanized coating and is acceptable per ASTM specifications.
Dull and Shiny on the Same Piece
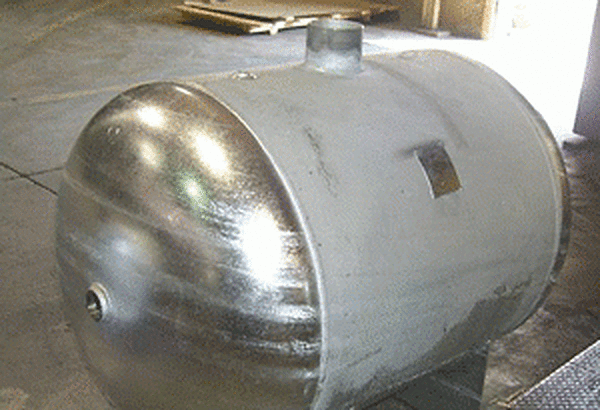
The most common reason for galvanized steel to have different appearances is the chemistry of the steel pieces. There are two elements of steel chemistry which most strongly influence the final appearance; silicon and phosphorous. Both elements are catalysts to coating growth, and the thicker coating is responsible for the differing appearance.
In addition to producing thicker coatings, highly reactive steels tend to have a matte gray or mottled appearance instead of a typical bright coating. This difference in appearance is a result of the rapid zinc-iron intermetallic growth. This growth of the intermetallic layer is out of the galvanizers control; however, if he is aware of the steels composition beforehand, he can utilize some process controls to minimize the effect. Sometimes connected (welded) galvanized pieces or even the same piece of steel will have different appearances (varying light and dark areas) due to steel chemistry. This is often observed when connecting different types or thicknesses of steel, but can also occur on similar pieces. Another common place this is found is in welded areas, as the silicon content of the weld rod can influence appearance. Regardless of the appearance, all of these products have an equal amount of corrosion protection and meet the specification requirements.
Bare Spots
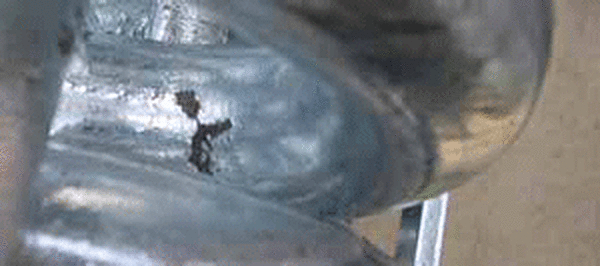
Bare spots, uncoated areas on the steel surface, are a surface defect that can occur because of inadequate surface preparation. Bare spots may be caused by welding slag, sand embedded in castings, excess aluminum in the galvanizing kettle, or lifting devices that prevent the coating from forming in a small area. In order to avoid bare spots, the galvanizer must ensure the surfaces are clean and without rust after pretreatment. Small bare spots can be repaired in the galvanizing shop. If the size of the bare spot or a total number of spots causes rejection, the parts may be stripped, re-galvanized, and then re-inspected for compliance to the specifications.
Dross Inclusions
Dross inclusions are a distinct particle of the zinc-iron intermetallic alloy that can become entrapped in the zinc coating. Dross inclusions may be avoided by changing the lifting orientation or redesigning the product to allow for more effective drainage. If the dross particles are small and completely covered by zinc metal, they will not affect the corrosion protection, and thus, are acceptable. If there are gross dross particles (large inclusions) that prevent the full galvanized coating from forming on the steel, then the particles must be removed and the area repaired.
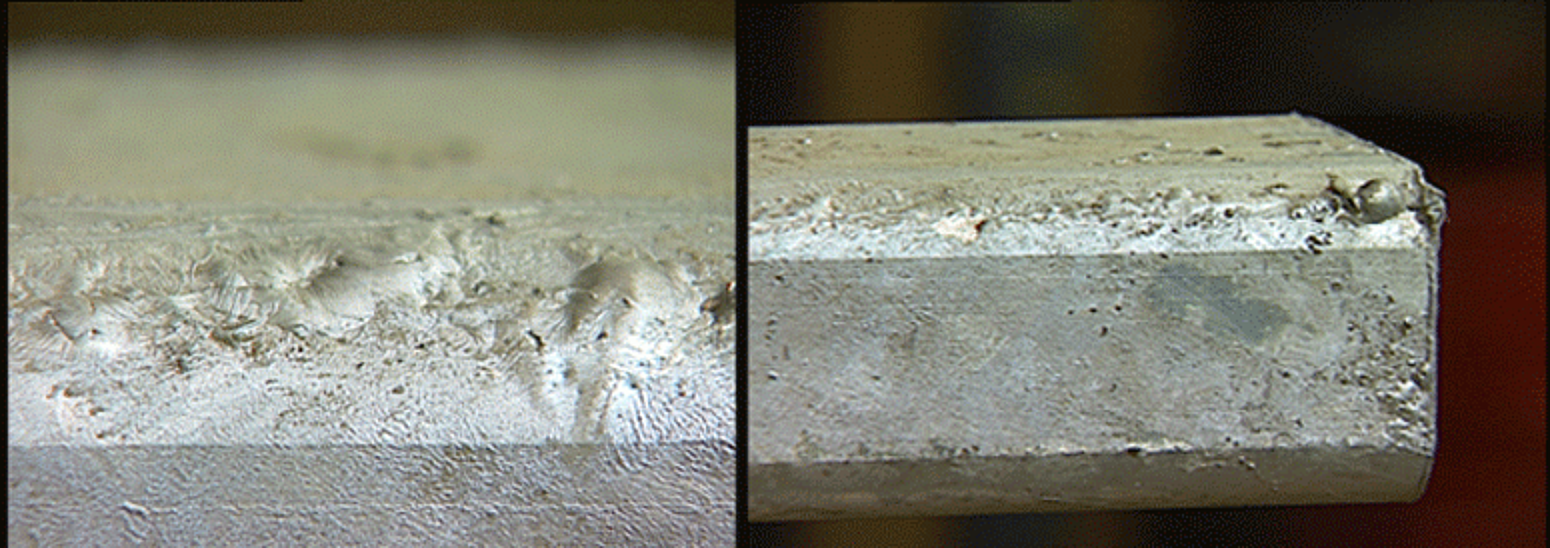
Flux Inclusions
Flux inclusions are created by the failure of the flux to release during the hot-dip galvanizing process, preventing the coating from forming. Because no coating grows under the inclusion, the area must be repaired prior to acceptance. If the area is small enough, it can be cleaned and repaired with touch-up, but if the flux inclusion covers a large area, the part must be rejected. Flux deposits on the interior of a hollow part, such as a pipe or tube, cannot be repaired and thus must be rejected. Parts rejected for flux deposits may be stripped of their zinc coating and then re-galvanized to provide an acceptable coating.
Skimmings Inclusions
Zinc skimming deposits are usually caused when there is no access to remove the zinc skimmings during the withdrawal of the steel from the galvanizing kettle. Zinc skimmings on the molten zinc surface are then trapped on the zinc coating. Zinc skimming deposits are not grounds for rejection as long as the zinc coating underneath is not harmed during their removal and it meets the necessary specifications.
Peeling/Delamination of the Galvanized Coating
Delamination or peeling creates a rough coating on the steel where the zinc has come off. There are a number of causes for zinc peeling. Many large galvanized parts take a long time to cool in the air and continue to form zinc-iron layers after they have been removed from the galvanizing kettle. This continued coating formation leaves behind a void between the top two layers of the galvanized coating. If there are many voids formed, the top layer of zinc can separate from the rest of the coating and peel off the part. If the remaining coating still meets the minimum specification requirements, then the part is acceptable. If the coating that remains on the steel does not meet the minimum specification requirements, then the part must be rejected and re-galvanized. If delamination occurs as a result of fabrication after galvanizing, such as blasting before painting, then the galvanizer is not responsible for the defect.
Flaking of the Galvanized Coating
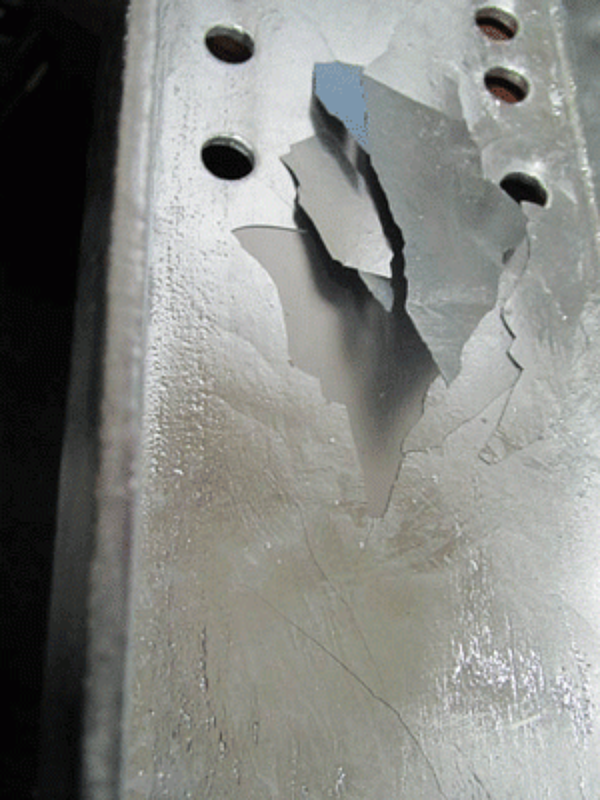
When heavy coatings (8-10mils or more) develop during the galvanizing process, flaking can result. Excessively thick coatings generate high stresses at the interface of the steel and galvanized coating which causes the zinc to become flaky and separate from the steel surface. Flaking can be avoided by minimizing the immersion time in the galvanizing kettle and cooling of the galvanized steel parts as quickly as possible, and/or if possible using a different steel grade. If the area of flaking is small, it can be repaired and then accepted; however, if the flaking area is larger than allowed by the specifications, the part must be rejected and re-galvanized.
Summary
This article has discussed some of the most common appearance concerns with hot-dip galvanized coatings. Like any other protective coating, there are other potential concerns to be aware. The AGA publication Inspection of Hot-Dip Galvanized Steel Products discusses other potential concerns and the free online AGA Inspection Course is available at www.galvanizeit.org/inspection-course.
© 2025 American Galvanizers Association. The material provided herein has been developed to provide accurate and authoritative information about after-fabrication hot-dip galvanized steel. This material provides general information only and is not intended as a substitute for competent professional examination and verification as to suitability and applicability. The information provided herein is not intended as a representation or warranty on the part of the AGA. Anyone making use of this information assumes all liability arising from such use.