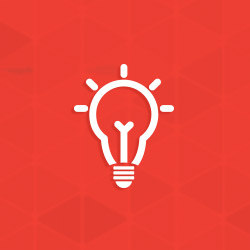
Coating Characteristics of Batch Hot-Dip Galvanizing
The batch hot-dip galvanized coating consists of a series of zinc-iron alloy layers with a surface layer of pure zinc. The unique coating is metallurgically bonded to the steel substrate, with the coating integral to the steel. The strength of the bond, measured in the range of several thousand psi, results in a very tightly adherent coating.
Batch hot-dip galvanizing produces a coating typically thicker than other zinc coating processes. Minimum coating thicknesses for various steel products and steel thickness are established by the ASTM standards A123, A153, and A767, as well as the CSA specification G 164. The image below shows the relationship between estimated service life and coating thickness. The shaded area represents the minimum thickness requirements found in the most common batch hot-dip galvanizing specification, ASTM A123.
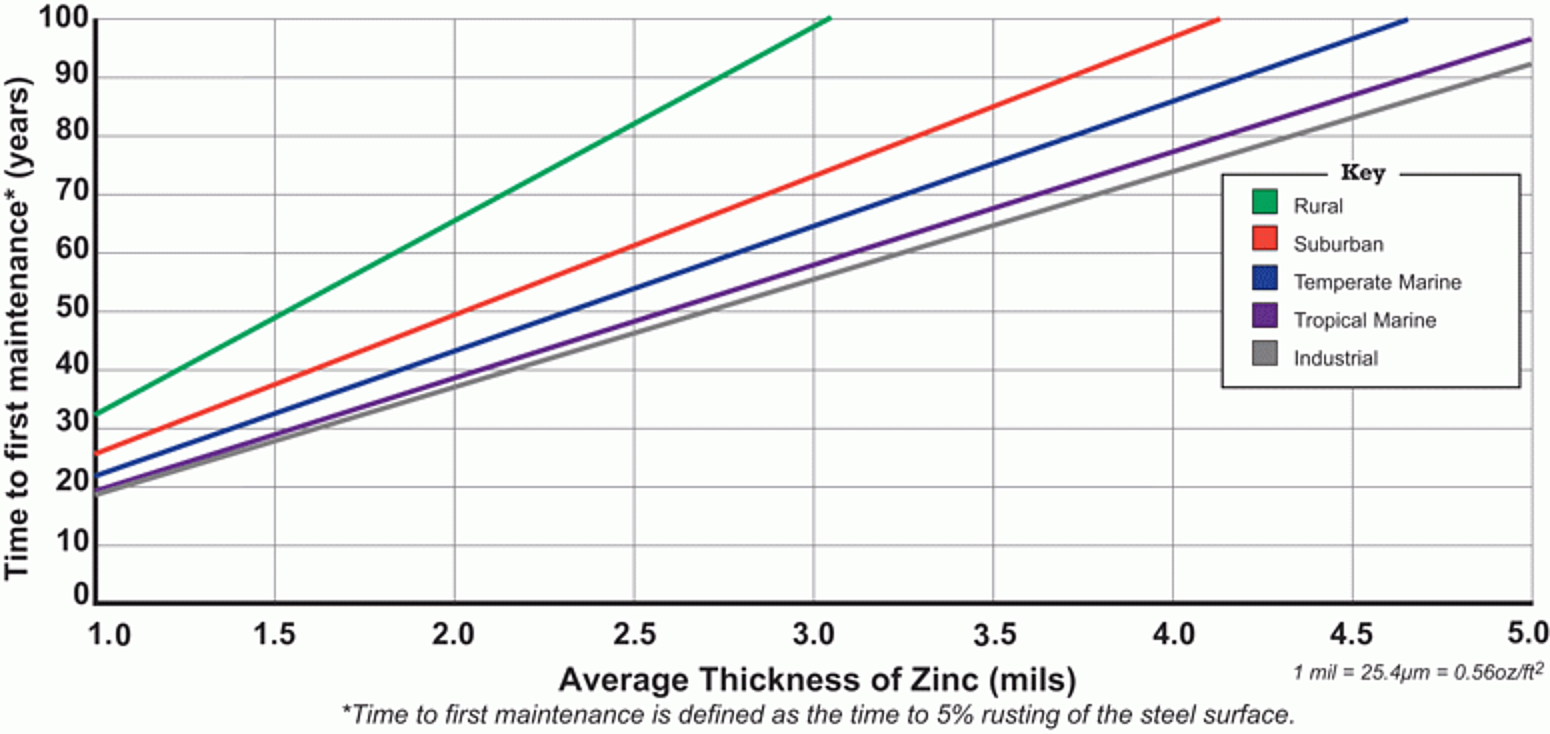
The zinc-iron alloy of the coating has hardness values that approach or exceed those of the most commonly galvanized structural steels, offering excellent abrasion resistance for applications such as stairs and walkways. The zinc-iron alloy layers are actually harder than the base steel.
The hot-dip galvanized coating is generally uniform on all surfaces. Edges, corners, and threads have coatings at least as thick, or thicker than flat surfaces, providing excellent protection at these critical points.
The pure zinc layer and the zinc-iron alloy layers are anodic to steel, providing sacrificial protection in the event the coating is scratched. This ensures steel exposed as a result of damage to the hot-dip coating will not rust as long as there is sufficient coating on the surface of the steel.
© 2025 American Galvanizers Association. The material provided herein has been developed to provide accurate and authoritative information about after-fabrication hot-dip galvanized steel. This material provides general information only and is not intended as a substitute for competent professional examination and verification as to suitability and applicability. The information provided herein is not intended as a representation or warranty on the part of the AGA. Anyone making use of this information assumes all liability arising from such use.