HDG Environmental Advantages
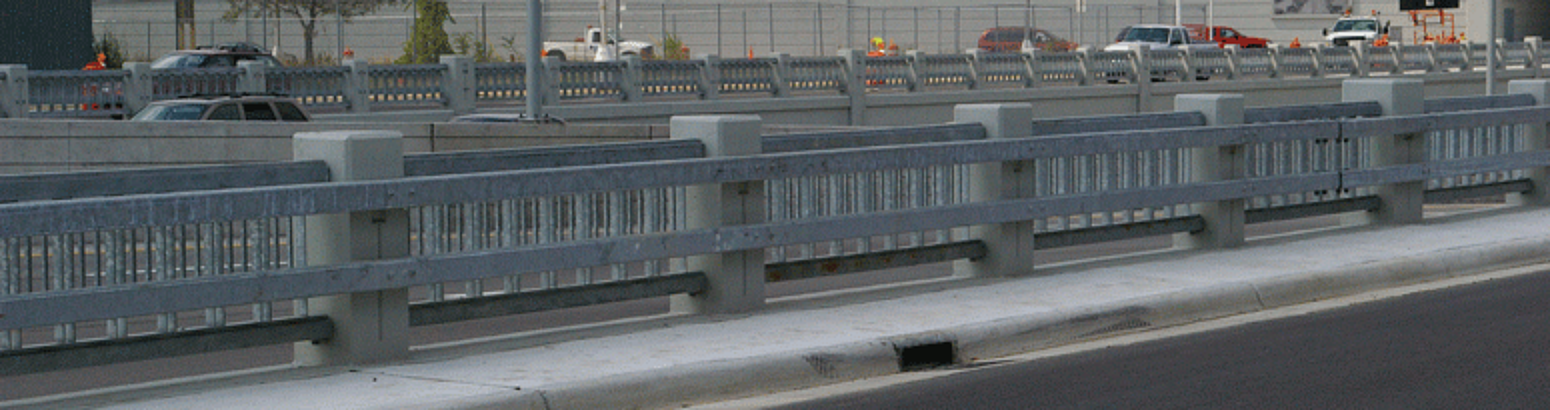
The production of any building material requires material and energy inputs and emission and waste outputs. The key to sustainable development is to ultimately lower the environmental impact of producing a product, through optimization of manufacturing. Specifiers who are committed to sustainable development have pushed for more transparency and objective measures of building materials' environmental impact in order to select those with less burden to current and future generations.
Hot-dip galvanized (HDG) steel has a number of environmental advantages that minimize the impact to the environment over the life of the project.
Natural, Abundant Materials
Hot-dip galvanized steel is made from two naturally occurring, abundant elements - zinc and iron ore. Iron ore (steel), the base metal, is the 4th most abundant element in the Earth's crust. Zinc, which comprises 98% of the hot-dip galvanized coating, is a natural, healthy metal. Zinc exists naturally in the air, water, and soil and is the 24th most abundant element in the Earth's crust. More than 5.8 million tons of zinc is naturally cycled through the environment by plant and animal life, rainfall, and other natural phenomena.
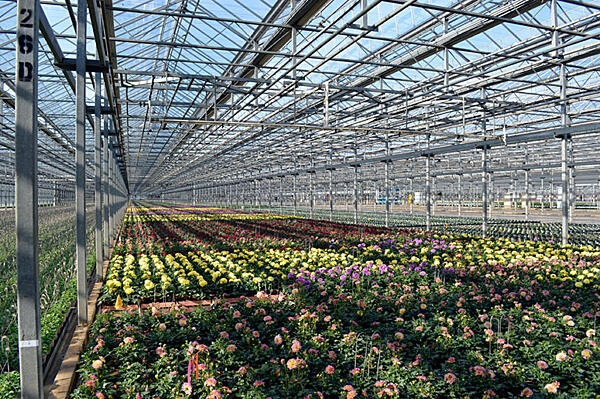
In addition to being natural and abundant, zinc is essential to life. All living things, from the smallest microorganisms to humans require zinc to live. Zinc is critical to growth as it plays a role in cell division, growth, and wound healing. It also plays an important part in daily functions such as breathing, digestion, reproduction, and cognition. And of all micronutrients, zinc has the strongest effect on our immune system which can help prevent disease and fight infection. Zinc is often used in fertilizers to fortify crops and promote growth.
As zinc is already naturally found in and cycled throughout the environment, the use of hot-dip galvanized steel is not introducing disruptive or harmful elements to the eco-system.
Infinitely Renewable Resources
In addition to being natural and abundant, both zinc and steel are infinitely recyclable without the loss of any physical or chemical properties. This means rather than being down-cycled into other products or uses, zinc and steel can be used as zinc and steel again and again, without compromising their integrity. Therefore, when considering the life-cycle assessment (LCA) of hot-dip galvanized steel, it is a cradle-to-cradle product, as there is essentially no "grave" to the zinc or steel.
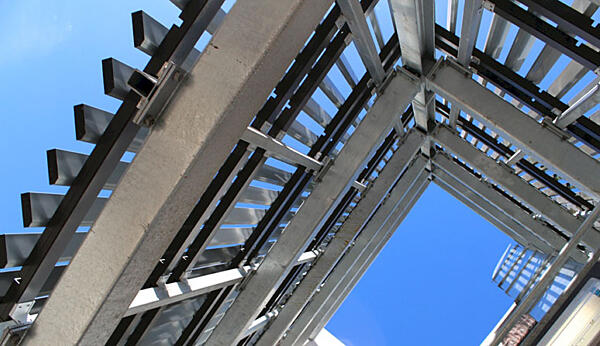
The 100% recyclability of hot-dip galvanized steel is a great benefit to minimizing environmental impact, but it is only half of the story. The fact the primary components of hot-dip galvanizing, zinc and steel, can be recycled is important, but there are two measures of recyclability that ultimately define the positive contribution to the environment: recycling rate and reclamation rate.
Recycling content is the amount of a product produced from recycled sources. Reclamation rate measures how often a product is actually recycled at the end of its useful life. Steel is the most recycled material in the world, and zinc also has a very high reclamation rate. This leads to a high recycling rate, as the reclaimed zinc and steel is often put right back into use.
The table below shows the Recycling and Reclamation Rates for both zinc and steel:
Zinc1 | Steel2 | |
---|---|---|
Reclamation Rate | 80% | 100% |
Recycling Rate | 30% | 70% |
1 International Zinc Association (IZA) Zinc Recycling, 2004 2 Steel Recycling Institute Steel Lakes LEED with Recycles Content, March 2009 |
The steel recycling rate in the table encompasses all steel types. When it comes to hot-dip galvanized steel, the story is even better, as the recycling rate of structural steel is more than 90%. The recycling rate of zinc is lower primarily because there is not enough zinc available to reclaim to create recycled product - its durability and longevity allows it to stay in use for decades.
Life-Cycle Assessment (LCA)
A life-cycle assessment (LCA) is an objective measurement of a product's environmental impact. Often called a "cradle-to-grave" study, LCA quantifies the environmental impact of a process or product from raw material acquisition, energy inputs and emission outputs during production and use, and end-of-life management recycling/disposal). LCAs have begun to gain favor in the specification community as a means of gauging a product's sustainability.
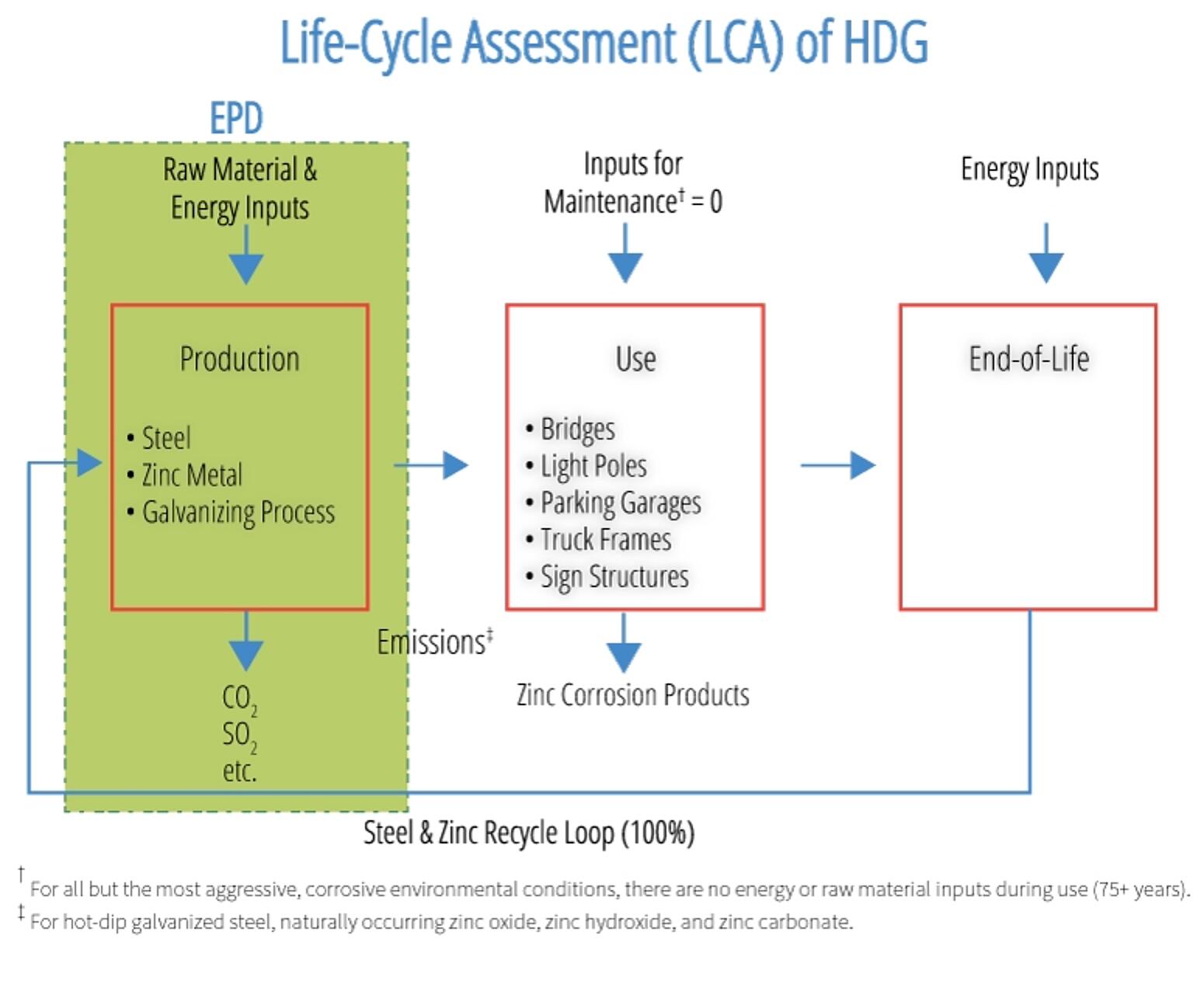
In 2008, the International Zinc Association (IZA) hired internationally renowned LCA experts Five Winds International and PE International to conduct a life-cycle inventory (LCI) and life-cycle assessment (LCA) for hot-dip galvanized steel. Utilizing data from worldwide sources regarding energy consumption and air/fluid/solid emissions measured during zinc production and during the actual galvanizing process, combined with analogous survey data collected from the steel industry, an LCA for hot-dip galvanized steel was compiled. This study provided a baseline understanding of the industry's impact today, one the AGA is committed to improving in the future.
In 2014, the American Galvanizers Association (AGA) began working with thinkstep, Inc. (formerly PE International) to update the LCA and generate an Environmental Product Declaration (EPD) for hot-dip galvanized steel. The EPD, which is a cradle-to-gate analysis, was then verified and published by UL Environment in 2016, following the principles, requirements, and guidelines in ISO 14040/14044 standards.
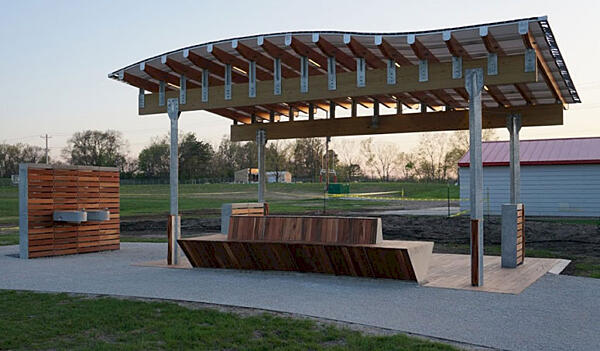
Hot-dip galvanizing is unique in that all material and energy inputs and emission outputs are isolated to the production phase. HDG requires no maintenance during the practical service life of most structures, i.e. 75 years or more. This means no transportation of labor to the repair site, no energy, no emissions such as sand from blasting or paint dust during removal, and no materials are needed after the initial production and installation of the HDG steel.
Additionally, hot-dip galvanized steel is the most recycled material in the world with approximately 90% of steel and 80% of all available zinc reclaimed for recycling. The energy required to produce the recycled product is 30% less than required to produce virgin HDG steel.
In addition to the LCA study conducted through IZA, two previously published cases studies were performed in Europe displaying the environmental impact differences between hot-dip galvanized steel to painted steel. These case studies show that although steel is the primary component in both LCAs, the coating does make a difference in the overall environmental impact.