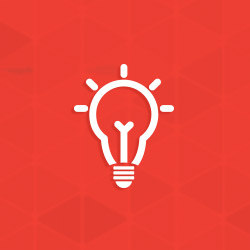
Galvanizing Old or Recycled Steel
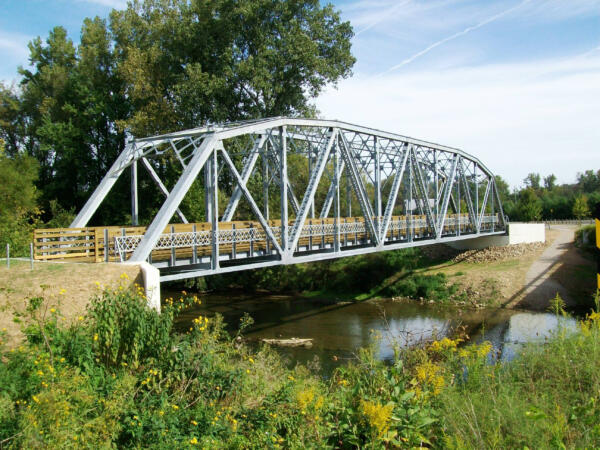
What is important for the galvanizer to consider when hot-dip galvanizing old or recycled steel?
When hot-dip galvanizing older steel which has been recycled from another project, the steel can sometimes be in poor condition or badly corroded. However, as long as the steel sections are structurally sound and fit for purpose, it is possible to refurbish and hot-dip galvanize. The Knox County Bridge in Ohio (2010) is an example of a successful recycling project where painted steel was disassembled, rehabilitated, and prepared successfully for galvanizing. Although there can be substantial cost and maintenance benefits to the user when choosing to recycle and then hot-dip galvanize old steel, the galvanizer should be aware of the potential for additional surface preparation and the effect on final coating appearance.
Preparing old/recycled steel for hot-dip galvanizing
Previously hot-dip galvanized steel is easier to re-galvanize, as long as some thickness of the original coating remains. The old coating can be stripped in the pretreatment process (acid pickling), exposing what is virtually new steel for galvanizing.
Any other coating system will require removal using abrasive or chemical methods. After stripping of the previous coating system, standard degreasing and acid pickling of the steel should be enough to attack the accumulated dirt, grease, and rust. If the steel is excessively rusted or pitted, an extended picking time may be required.
When recycling steel from corrosive environments, such as bridge steel exposed to heavy de-icing salt applications and therefore containing residual chlorides, abrasive blast cleaning can help to open up microscopic pits in the steel which can entrap corrosive material at high concentrations. Afterwards, an extended pickling time should be enough to attack residual chlorides. As salts come into contact with the acid, they should dissolve into the pickling solution. Chemical chloride-removal washes should not be used to remove residual chlorides in the steel because such washes are meant for concrete and not for steel applications.
Effects on the final product appearance
When hot-dip galvanizing recycled steel, initial surface condition and steel chemistry can provide varying final coating appearance. With recycled steel that has been abrasive blast cleaned, the roughened surface of the steel is likely to result in a rough coating. However, a rough coating may develop regardless of abrasive blast cleaning due to initial surface conditions such as surface pitting.
When recycled steel with a high silicon content (reactive steel) is prepared using abrasive blast cleaning, the roughened surface of the steel interferes with the growth of the zeta inter-metallic layer and thus limits the coating thickness. A coating thickness may be developed which is less than typical. Alternatively, roughening the surface of low silicon (less reactive) steel increases the steel surface area and causes the steel to react more vigorously with the zinc to result in a thicker coating than normal (and therefore a longer coating life).
Mixing Old and New Steel
Fabrications with varying initial surface conditions such as old steel, new steel, pitted steel, and/or newly machined surfaces can form the galvanized coatings iron-zinc intermetallic layers at different rates, resulting in a non-uniform coating appearance. Where fabricated assemblies containing varying surface conditions are unavoidable, the entire assembly should be thoroughly abrasive blasted prior to pickling to give the best chance for producing a consistent galvanized coating appearance. Although the assembly may vary in initial surface appearance, these variations do not affect the corrosion protection provided by the galvanized coating and the entire coating will take on a uniform appearance upon normal weathering in the environment.
© 2025 American Galvanizers Association. The material provided herein has been developed to provide accurate and authoritative information about after-fabrication hot-dip galvanized steel. This material provides general information only and is not intended as a substitute for competent professional examination and verification as to suitability and applicability. The information provided herein is not intended as a representation or warranty on the part of the AGA. Anyone making use of this information assumes all liability arising from such use.