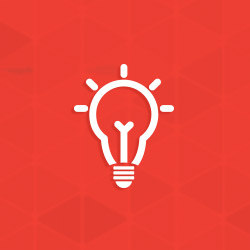
Zinc Recycling
At present, approximately 70% of the zinc produced worldwide originates from mined ores and 30% from recycled or secondary zinc. The level of recycling is increasing each year, in step with progress in the technology of zinc production and zinc recycling. Today, over 80% of the zinc available for recycling is indeed recycled.
Zinc is recycled at all stages of production and use for example, from scrap that arises during the production of galvanized steel sheet, from scrap generated during manufacturing and installation processes, and from end-of-life products.
The Zinc Recycling Circuit
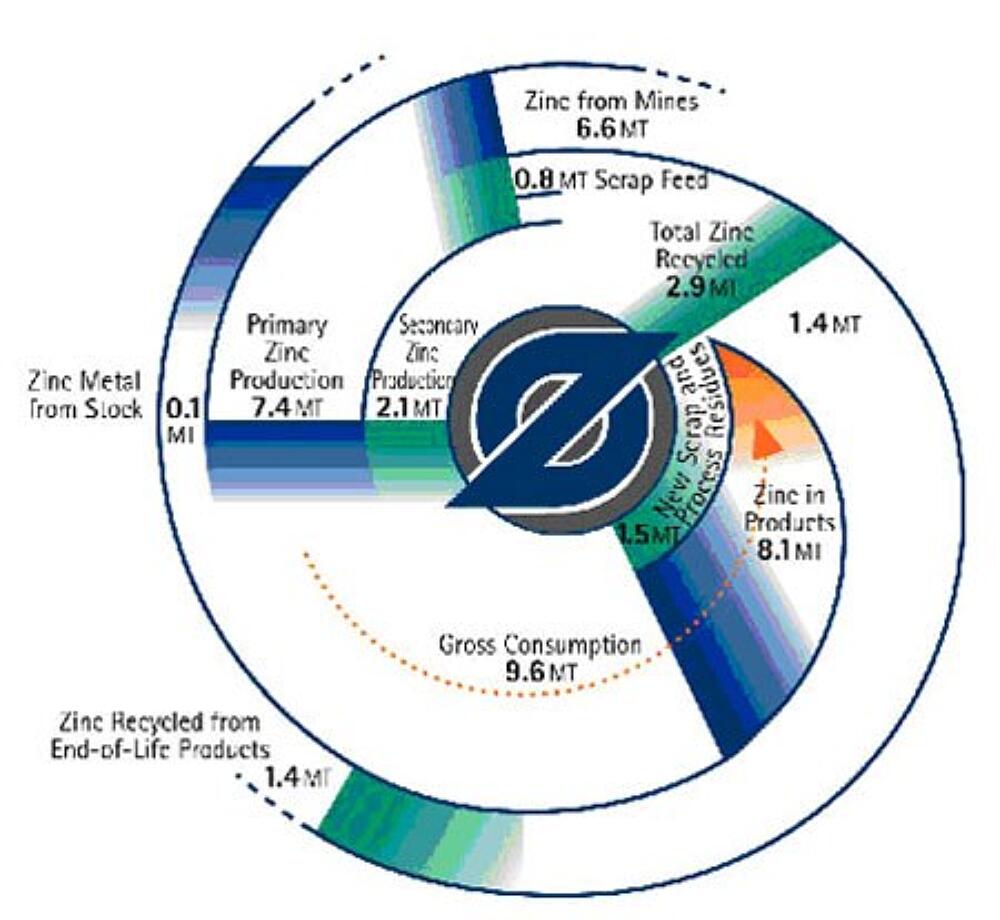
Zinc-coated steel and other zinc containing products are slow to enter the recycling circuit due to the very nature of their durability. The life of zinc-containing products is variable and can range from 10-15 years for cars or household appliances, to over 100 years for zinc sheet used for roofing. Street lighting columns made of zinc-coated steel can remain in service for 40 years or much longer, and transmission towers for over 70 years. All these products tend to be replaced due to obsolescence, not because the zinc has ceased to protect the underlying steel. For example, zinc coated steel poles placed in the Australian outback a hundred years ago are still in excellent condition1.
The presence of zinc coating on steel does not restrict steels recyclability and all types of zinc-coated products are recyclable2. Zinc coated steel is recycled along with other steel scrap during the steel production process the zinc volatilises and is then recovered.
Zinc coated steels are easily collected and treated in existing process streams. The Electric Arc Furnace (EAF) is the most widely used process for recycling zinc-coated steel. The high temperatures cause zinc which is volatile at high temperatures to leave the furnace along with other gases. The gas stream is treated and the zinc collected in the dust, of which zinc (18-35%) and iron are the main constituents. These dusts undergo an enrichment process in a rotary kiln, known as a Waelz kiln3. This leads to the production of zinc oxide, which in turn becomes a raw material for the production of zinc metal. Several new technologies are in use or under development for processing EAF dusts and the valuable metals they contain.
The Electric Arc Furnace Process
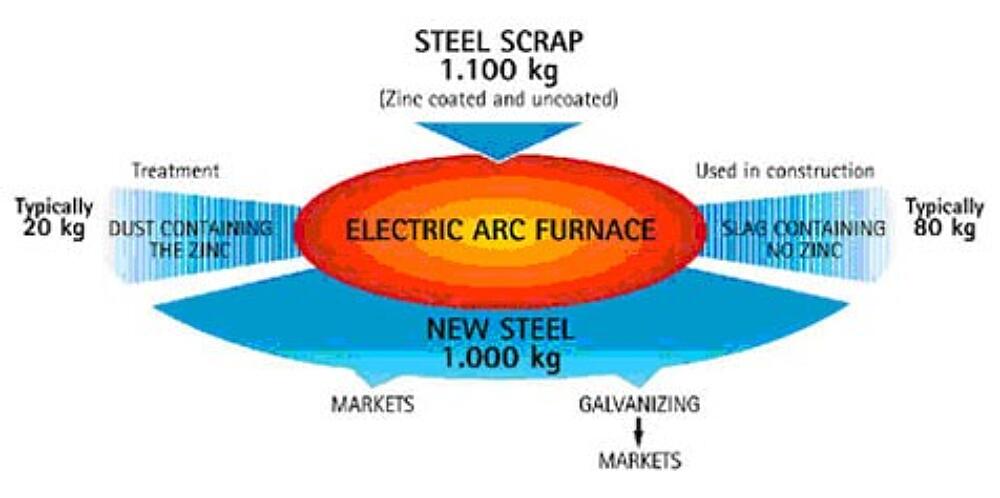
(1) G Thompson. A Tribute to Zinc Australias first international telegraph line. IZA. 1997.
(2) M Martin & R Wildt. Closing the Loop An Introduction to Recycling Zinc Coated Steel. IZA 2001.
(3) The Waelz process is the leading technology for treating EAF flue dust and is continuously being optimized for energy input, product and offgas quality. In 1997, the Waelz process was used to treat over 1 million tonnes of EAF dust, representing 77% of world flue dust reprocessing capacity. K Mager et al. Recovery of Zinc Oxide from Secondary Raw Materials New Developments of the Waelz Process. Published in Fourth International Symposium on Recycling of Metals and Engineered Materials. Edited by DL Stewart, RL Stephens and JC Daley, TMS 2000. ISBN 0-87339-494, p.329-344.
© 2025 American Galvanizers Association. The material provided herein has been developed to provide accurate and authoritative information about after-fabrication hot-dip galvanized steel. This material provides general information only and is not intended as a substitute for competent professional examination and verification as to suitability and applicability. The information provided herein is not intended as a representation or warranty on the part of the AGA. Anyone making use of this information assumes all liability arising from such use.