Metallizing
Zinc spraying, or metallizing, is accomplished by feeding zinc wire or powder into a heated gun, where it is melted and sprayed onto the part using combustion gases and/or auxiliary compressed air to provide the necessary velocity. Prior to metallizing, the steel must be abrasively cleaned.
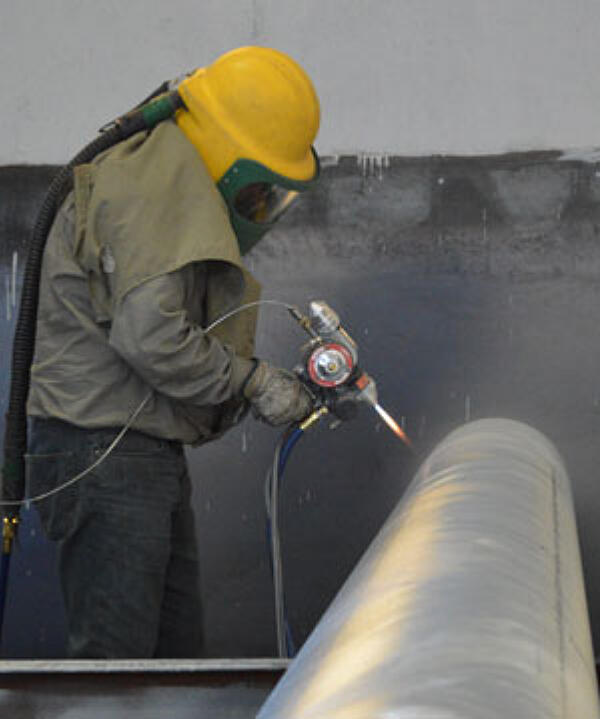
The 100% zinc coating can be applied in the shop or field, but is more commonly done in the shop where heat for melting is more readily available. Metallizing may be used on any size steel, though the complexity of the structure is important, as applying a consistent coating and reaching recesses, hollows and cavities is difficult. Zinc spray is often used as an alternative to hot-dip galvanizing when the part is too large for immersion in the kettle and is also a great option for extending the life of already erected galvanized structures. The biggest limitations to metallizing applications are the availability of skilled operators and equipment and a significant cost premium.
Coating Characteristics
The metallized zinc coating is rough and slightly porous, with a density of about 80% of hot-dip galvanizing. As the metallized coating is exposed to the atmosphere, zinc corrosion products tend to fill the pores providing consistent cathodic protection. The mechanically-bonded, pure zinc coating covers welds, seams, ends, and rivets well and can be applied in excess of 10 mils (254 µm). Coating consistency is dependent on operator experience and coating variation is always a possibility. Coatings tend to be thinner on corners and edges and no coating is applied to interior surfaces or difficult-to-access recesses and cavities.