Uncoated Weathering Steel (UWS)
Uncoated weathering steel (UWS), or COR-TEN steel1, was originally developed as a high-strength steel, but later the steel industry realized alloying elements such as manganese, silicon, chromium, nickel, copper, and phosphorus provided corrosion resistance. When exposed to atmospheric conditions, weathering steel initially corrodes and then develops a 'rust' patina that limits further oxidation. The stable and protective patina development and regeneration increase the corrosion resistance of the steel significantly over mild carbon steel.
History
The history of weathering steel began in the 1910s in the U.S. when copper-alloyed steels were tested for corrosion resistance, with further improvements made by adding phosphorus in 1926. In 1933, the United States Steel Corporation patented a highly durable steel, later branded as Cor-Ten, primarily for use in heavy-duty applications like railroad hopper cars. Over time, the steel's corrosion resistant properties became recognized, and it was widely adopted for transportation and construction. The first highway application occurred in 1964 in New Jersey for the Moorestown Interchange was built over New Jersey Turnpike, and its use in bridges expanded internationally, starting with the University of York Footbridge in 1967.
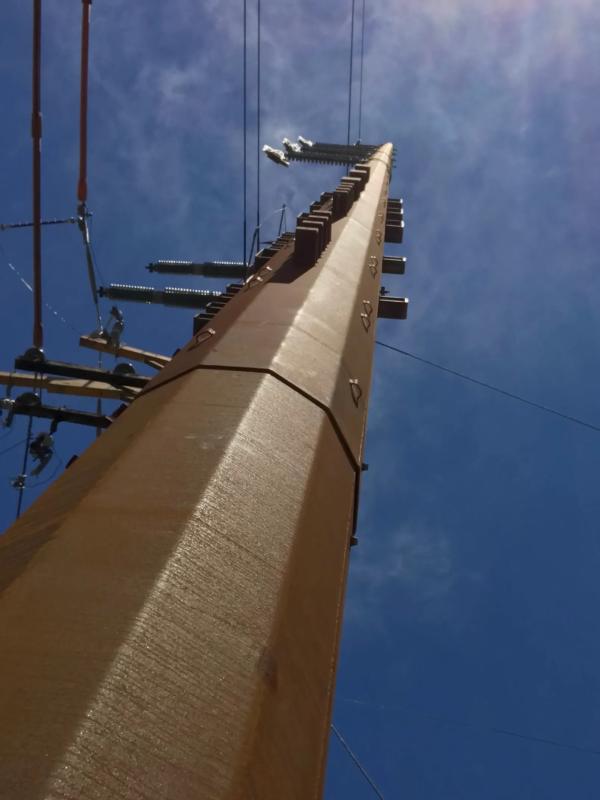
Uses
UWS is commonly used in outdoor sculptures and architectural structures for its distressed, antique look, seen in works like the Chicago Picasso sculpture and Robert Indiana's Love sculpture. It is also used in large structural applications like bridges, such as the New River Gorge Bridge, and in buildings like the Barclays Center and the John Deere World Headquarters. Though popular for its initial aesthetic appeal, its use in railcars encountered issues with rust, especially when painted, as the protective patina couldn't form properly. Similarly, UWS is sometimes a popular choice to achieve a natural aesthetic for highway structures, although a 2010 memorandum from FHWA states weathering steel guardrail should be limited unless the owner agency adopts a frequent periodic inspection and replacement schedule, citing performance concerns.
Disadvantages
Weathering steel has gained popularity for the aesthetic appeal of its natural weathering and low maintenance durability. However, there are some notable disadvantages to its use:
- Unintended Corrosion - Weathering steel is marketed as a corrosion resistant, low maintenance solution. However, there have been a number of weathering steel failures over the past decade due to the rust patina not forming or regenerating effectively. Some of these failures have led to serious safety concerns.
- This is of particular concern when weathering steel is used in areas with consistently humid or wet conditions. This includes marine and coastal areas, areas where dew or vegetation touch the steel, areas of poor drainage or that are otherwise in contact with water and not allowed to dry out (such as the interior of hollow structures where condensation builds). In these conditions, the rate of corrosion can exceed the formation of the patina layer leading to accelerated corrosion.
- The weathering steel patina is also adversely affected by high levels of pollutants such as sulfur dioxide or chlorides. As chlorides are used in all de-icing agents, there should be elevated concern and inspection of weathering steel bridges that are exposed to these treatments. This is particularly important in areas where there could be poor drainage.
- Finally, verifying the difference between weathering steel's rust patina and localized corrosion can be tricky, especially to an unseasoned inspector. For example, section losses in fracture critical areas were noted but not raised as highly critical in the Fern Hollow Bridge collapse in Pennsylvania.
- Maintenance Requirements - Though weathering steel used in ideal environments reduces maintenance compared to traditional steel, there is still need to regularly inspect, and at times, maintain the steel. A few important requirements are to remove any vegetation in contact with the steel and trim back any that may grow to contact the steel. More detail on inspection and maintenance can be found in Sections 4.0 and 5.0 of the National Steel Bridge Alliance (NSBA) Uncoated Weathering Steel Reference Guide.
- When used in bridges, it's important to monitor for and remove debris from drains and to inspect and maintain joints.
- Both dry (air blasting) and wet (pressure washing) cleaning are recommended on a regular basis for weathering steel bridges depending on the environment and use of de-icing materials, but generally every 2-4 years.
- Rust Bleeding/Staining - Although some designers like the rust appearance of weathering steel, the staining to surrounding materials is considered a major drawback. This rust bleeding is an eyesore and has been lambasted in some very high profile projects over time, such as the Barclays Center in Brooklyn, NY. In fact, NSBA's UWS Reference Guide contains a whole section 3.5 on Stain Prevention.
- Fabrication/Usability Considerations - Weathering steel's unique properties can make it more challenging to fabricate than mild carbon steels. Furthermore, because of the initial corrosion, some applications may require thicker steels, which can add material and labor costs and reduce overall efficiency.
Comparison to Hot-Dip Galvanized Steel (HDG)
Where versatility is needed, or where project-bundling spans multiple environments, or for products meant for stockability where installation location is unknown at the time of fabrication, hot-dip galvanizing (HDG) can provide many of the same benefits as UWS and in a broader set of environments with only a minor increase in initial cost. Where it is needed to emulate the appearance of weathering steel, Colorants for Galvanized Steel can be used to alter the initial appearance of hot-dip galvanized steel. This information can be helpful on projects where woodland aesthetics are raised as an important concern.
In fact, in a study conducted by Jennifer McConnel at the University of Delaware on behalf of the National Steel Bridge Alliance (NSBA), on the Durability of Steel Bridge Corrosion Protection Systems which analyzed historical performance of 3-part paint systems, Zinc-Rich Paint, weathering steel, hot-dip galvanizing, and metallizing, McConnell concluded "Based on these visual observations and the longevity estimates given in Table 4-2, galvanizing was judged to provide the best performance of all corrosion protection systems evaluated in this work." Further, the report states, "Galvanizing has the potential to provide more than 100 years of service life for all the service life benchmarks considered."
You can learn more about the comparison of uncoated weathering steel to hot-dip galvanized steel in our side-by-side comparison publication.