Corrosion Rate
Approximately 85% of all steel produced is carbon steel and therefore susceptible to natural oxidation and galvanic corrosion. The rate of corrosion is well understood in typical atmospheric conditions, but for the design engineer, the precise localized or micro-environment conditions must be well understood for him/her to have confidence in the ultimate durability of the design. Other micro-environments include exposure to fresh and salt water (in or very near) or in soil.
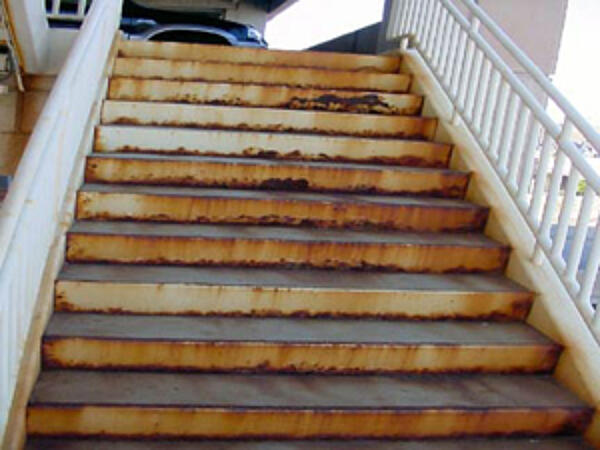
Corrosion of carbon steel and even alloy steels in micro-environments can be very complex. For example, the pH, moisture content, and chloride level are just three of the variables determining the corrosion rate of galvanized steel in soil.
Corrosion charts are difficult to develop because of the many variables present in any given micro-environment. For example, corrosion in water must consider factors such as oxygen content, the extent of agitation, wave action, temperature, chloride levels and more. This makes developing a chart predictive of corrosion rates for any specific location extensive and sometimes costly, and why many corrosion rate charts exist, but only for unique locations and conditions.
Here is a little more detail about steel corrosion rates in various environments.
Atmospheric
The most common exposure environment for metallic corrosion is atmospheric. As steel, copper, magnesium, aluminum, et al are exposed to the atmosphere, they react with free flowing air and moisture to develop oxides. The performance of atmospherically exposed metals depends on five main factors: temperature, humidity, rainfall, sulfur dioxide (pollution) concentration in the air, and air salinity. None of these factors can be singled out as the main contributor to corrosion. Extensive studies have been conducted on these metals and a predictable corrosion rate for each is available.
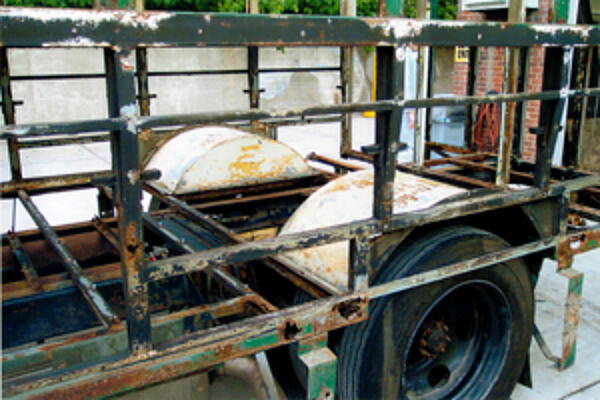
Corrosion of carbon steel occurs when the relative humidity of the air is 70% to 80% and the air temperature is above 32 F. Corrosion rates may be accelerated by air impurities that dissolve in condensed water or rain water and by dust and dirt settling on the metal surface.
General corrosion rates of carbon steel in different atmospheres and it should be noted corrosion rates in micro-environments can greatly exceed those corrosion rates.
In Soil
Steel in soil is subjected to a range of corrosive forces quite unlike those experienced in atmospheric exposure conditions, and the performance of steel in-ground is not as well understood as is the durability in above-ground applications. With more than 200 different types of soil identified in North America, corrosion rate in soils is varied and hard to predict. Steel requires oxygen, moisture and the presence of dissolved salts to corrode. If any one of these is absent, the corrosion reaction will cease or proceed very slowly. Steel corrodes quickly in acidic environments and slowly or not at all as alkalinity is increased. The corrosion rate of steel in soil can range from less than 0.2 microns per year in favorable conditions to 20 microns per year or more in very aggressive soils.
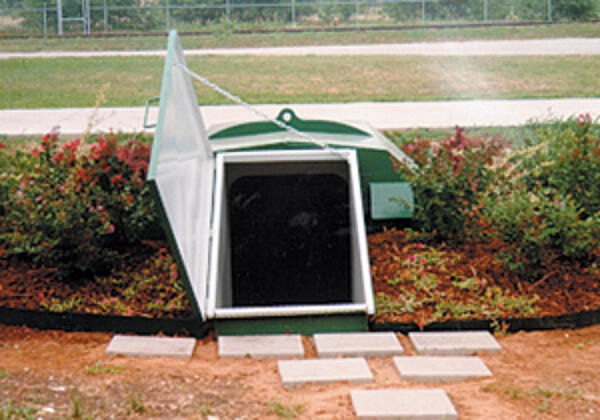
Corrosion of metals in soil is extremely variable and while the soil environment is complex, it is possible to make some generalizations about soil types and corrosion. The main factors that dictate the corrosivity of the soil are moisture content, pH level, and chlorides. These soil conditions are affected by additional characteristics such as aeration, temperature, resistivity, and texture or particle size. Any given soil is a very heterogeneous material consisting of three phases: solid, gaseous, and aqueous.
The solid phase consists of soil particles that vary in size, in chemical composition, and the level of entrained organic material. The solid phase of soils are classified according to their average particle size and chemistry. Traditionally, particles between 0.07 mm to 2 mm are considered sand, particles from 0.0005 mm to 0.07 mm are silts, and 0.005 mm and smaller are clays. Because of the smaller particle size and their ability to absorb water readily, clay soils present a higher corrosion rate than sandy soils.
The gaseous phase consists of air entrained in the soils pores. Access of gas (air) into the soil depends on its permeability. Drier soils or coarser grained soils will allow more oxygen access to the sub-surface and increase the rate of steel corrosion relative to the areas with less oxygen.
The aqueous phase, or the soil moisture is the vehicle that allows corrosion to proceed. The relative acidity of the aqueous solution is the most important factor in the corrosion rate. At low pH the evolution of hydrogen tends to eliminate the possibility of protective film formation, so steel corrosion continues, but in alkaline solutions, protective films are created and reduce the corrosion rate. The greater alkalinity, the slower the rate of attack becomes. In neutral solutions, other factors such as aeration become more important, so generalizations are more difficult to develop.
Marine (Water)
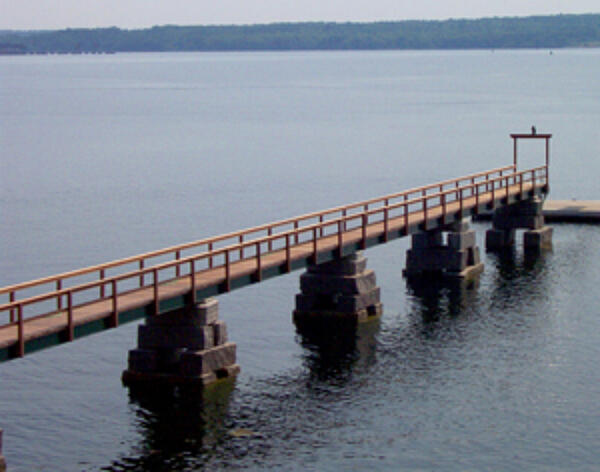
A less common environment for metal is submerged in or exposed to water. Moisture is highly corrosive to most metals including steel, aluminum, and zinc. There are many different types of water (pure water, natural fresh water, potable water (treated drinking water), and seawater) and each has different mechanisms that determine the corrosion rate. The parameters that affect corrosion of metals in water include pH level, oxygen content, water temperature, agitation, the presence of inhibitors, and tide conditions.
Onshore areas of marine corrosion include docks, harbors, naval yards, where sacrificial anodes providing cathodic protection may be employed, as well as protective coatings such as marine paints and galvanizing. Offshore oil and gas platforms are exposed to particularly aggressive corrosion from sea salt spray and immersion.
Pipeline
Depending on the nature of the product being carried, exposure conditions, operating conditions (24/7 v. sporadic), and commitment to maintenance, pipeline corrosion may mean a useful life of one year or more than 50. In North America the cost of pipeline corrosion is approximately $9 billion annually with 10% apportioned to cost of failure, 38% to capital requirements, and 52% to operations and maintenance.
Although technology and monitoring equipment investment has increased significantly in the past few years, including risk assessment and pipeline integrity management programs, several high profile failures brings into question the effectiveness of such commitment to safety.
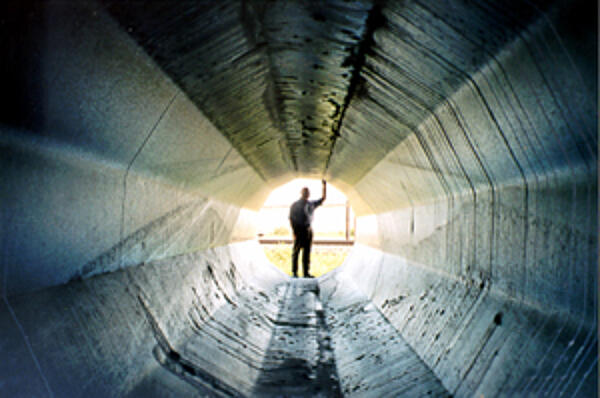
One of the challenges to pipeline corrosion is ot typically starts on the inside of the pipe, making detection difficult. Pervasive within the pipeline industry is the mentality to wait until a failure occurs to fix it. This is because the cost to implement effective inspection such as smart pigs is very high. This myopic strategy may save money in the near term, but surely has a higher cost to the environment and future capital requirements.