Corrosion Testing
There are three general methods of corrosion testing: service history, field performance, and accelerated corrosion tests. Service history over a long period of time is the most reliable and available, but the data may not reflect the exact conditions the material is exposed to currently.
Field performance corrosion testing is similar to service history, but typically entails examining performance variable over a shorter period such as one to five years. Once the data is collected, one can extrapolate it to provide a somewhat scientific prediction of performance to 10, 20, or even 50 years. Extrapolating the variable performance to 10, 20 or even 50 years then provides a somewhat scientific prediction of long-term performance.
Combining service history with field performance can also be very effective. For example if the environment around a project changed in the last 5 years of its life, examining the total service history as well as the field performance differences after the change in environment may yield a prediction for a new project in that environment.
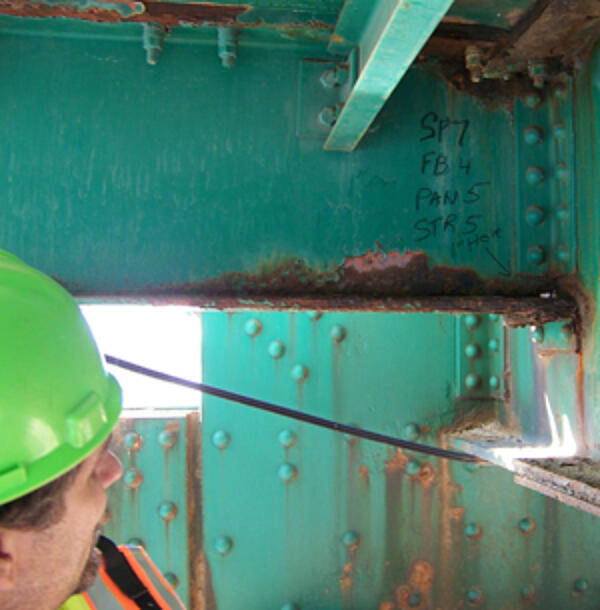
Accelerated corrosion testing is commonly used because of the quicker results; however, it is difficult to design the test to account for all corrosion mechanisms involved, and therefore the results can be compromised. For example, 1,000 hour salt fog spray tests on zinc coated products such as galvanized steel do not allow the wet/dry cycles of normal atmospheric exposure. Those wet/dry cycles are necessary for the development of the zinc patina of zinc oxide, zinc hydroxide, and zinc carbonate which gives galvanized products durability for decades.
There are two common testing methods used to study the corrosion on a piece of steel:
- Ultrasonic testing is a non-destructive test with very high sensitivity detection of internal flaws in steel and changes in thickness. Very short ultrasonic pulse-waves are sent into the steel to determine if any corrosion has changed the sound signature of the piece, indicating corrosion has occurred.
- A scanning electron microscope (SEM) focuses a beam of electrons on a surface that when reflected back yield discernable information about the surface condition and topography of the sample being tested. Typical applications are detecting micro-cracking and molecular composition of the material or coating applied over the material.