Zinc Coatings
Zinc, a natural, healthy, and abundant element was first used in construction in 79 AD. Zinc metal has a number of characteristics that make it a well-suited corrosion protective coating for iron and steel products. Zincs excellent corrosion resistance in most environments accounts for its successful use as a protective coating on a variety of products and in many exposure conditions.
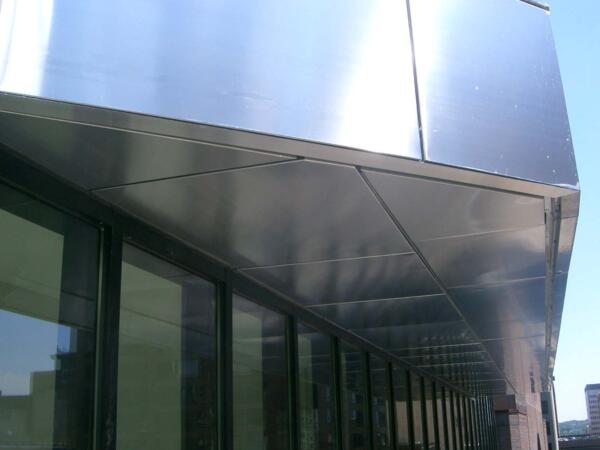
This proven corrosion resistance is a result of zincs ability to form dense, adherent corrosion byproducts, which leads to a rate of corrosion considerably lower than ferrous materials 10 to 100 times slower, depending on the environment. While a fresh zinc surface is quite reactive when exposed to the atmosphere, zinc corrosion products develop rapidly on the surface as the coating is exposed to natural wet and dry cycles in the atmosphere. These corrosion products, collectively known as the zinc patina, act as an additional barrier between the steel and the environment.
A number of different methods of applying zinc coatings to steel are commercially available, each of which has unique characteristics. Often all of these coatings are incorrectly labeled galvanizing, but it is important to understand the differences. The products produced by each of these processes have different uses depending on their applicability, relative economics and expected service life.
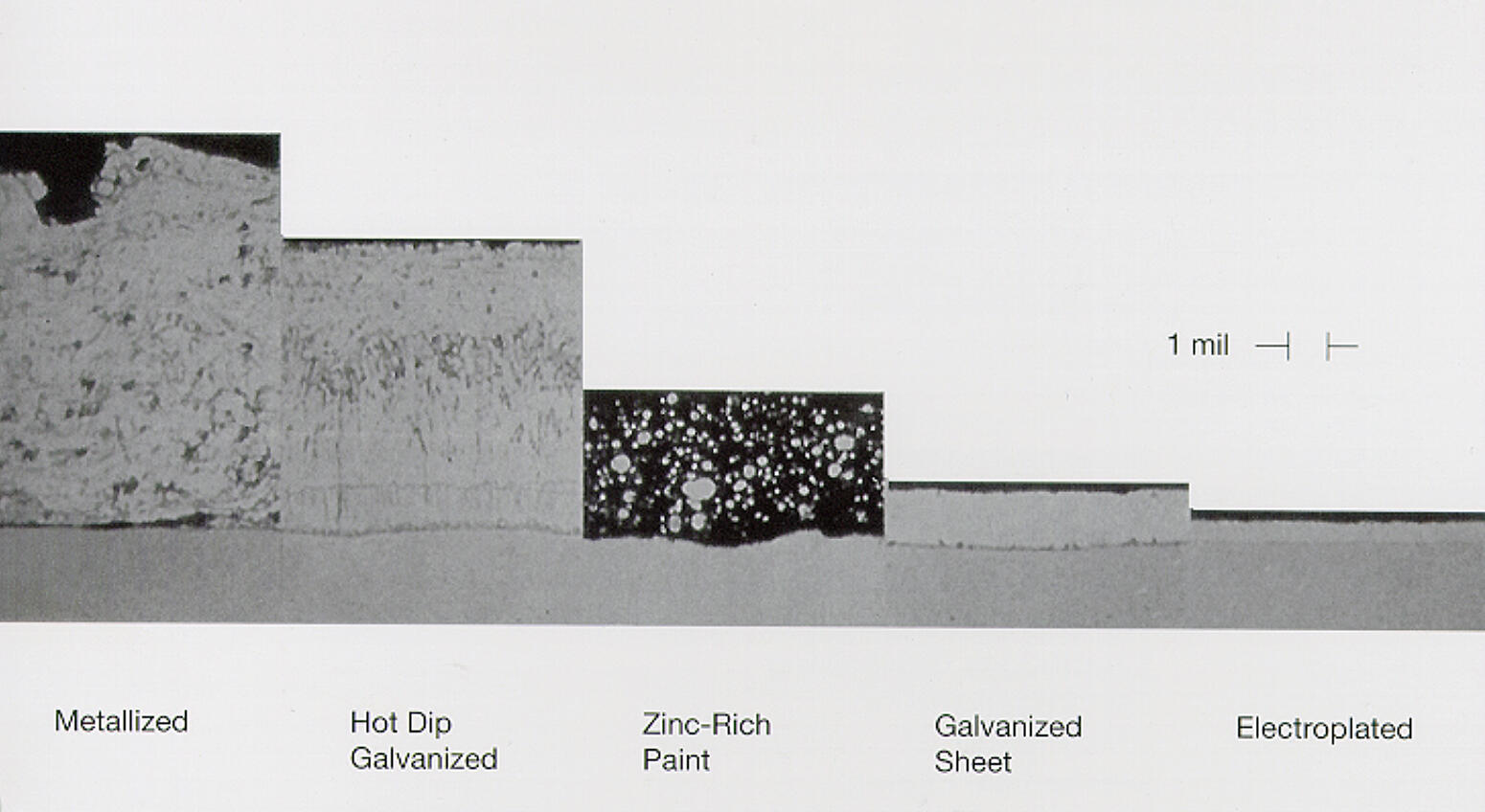
Selection of Zinc Coatings
Once the decision is made to use a zinc coating for corrosion protection, a few additional factors must be considered to ensure the proper coating is selected for the application and service environment. Each zinc coating covered in this section provides varying degrees of corrosion protection and it is important to identify the corrosiveness of the exposure environment to determine if the coating selected will provide adequate service life.
Some zinc coatings will be eliminated by the nature alone, (zinc coating processes limited to small parts or sheet steels cannot be considered for the protective coating of structural steel members); others may be ruled out based on cost, appearance, availability, etc.
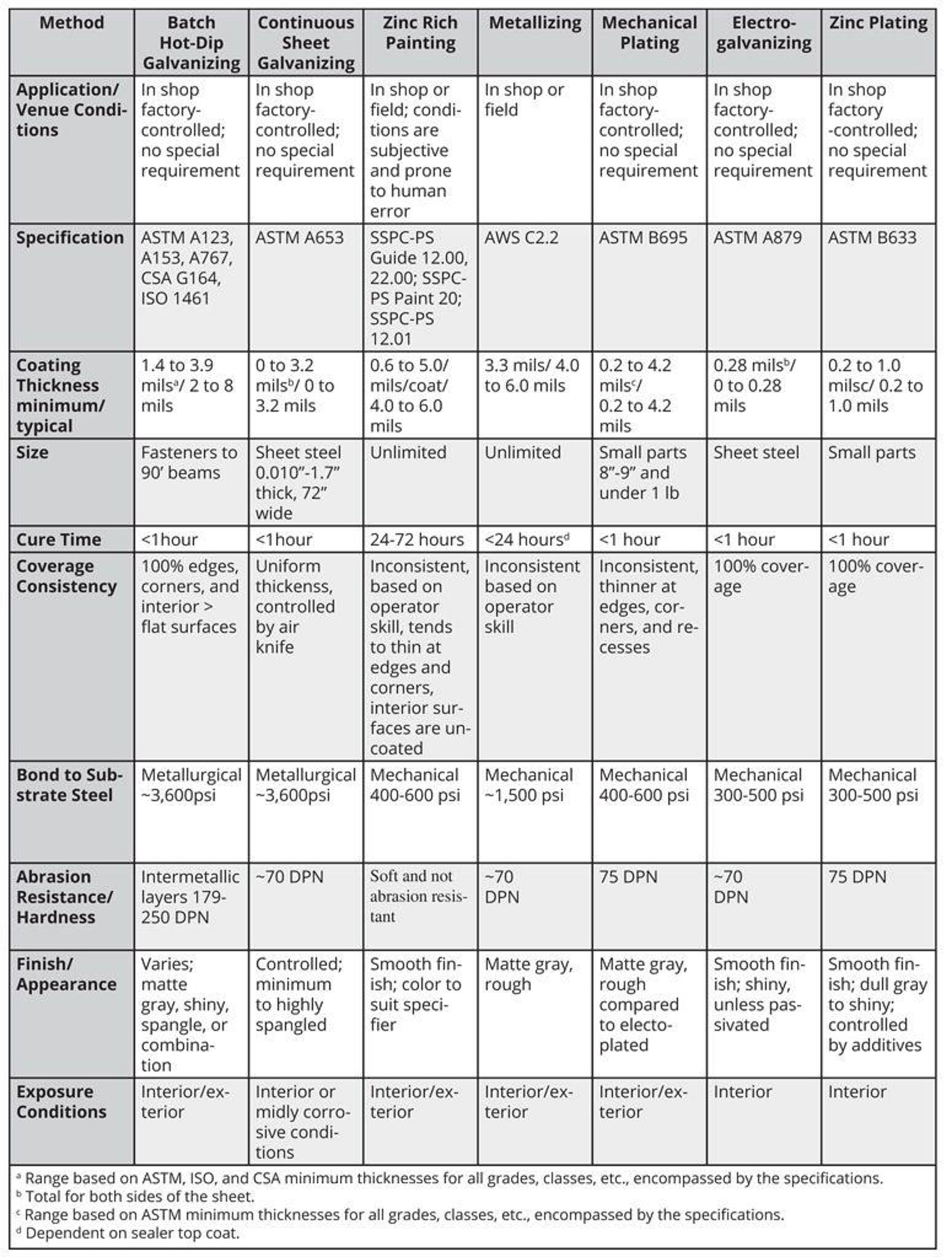
Coating Thickness vs. Coating Weight
The service life of zinc coatings is a linear function of the zinc coating thickness. However, zinc coating thickness alone can be deceiving when evaluating zinc applied by different processes. In addition to thickness, the amount of available zinc per unit volume, or density, is also important.
Various ASTM and/or other specifications require different weights or thicknesses, so it is imperative to convert all coatings to a common denominator for comparison. While coating densities for some types of zinc coatings are nearly identical, others differ considerably. The coating densities, in terms of thickness required to equal 1 oz of zinc per square foot of surface, are:
Coating | Thickness to reach 1 oz/ft2 |
---|---|
Hot-dip galvanizing (batch or continuous), electroplating, zinc plating | 1.7 mils (43 µm) |
Metallizing (zinc spraying) | 1.9 mils (48 µm) |
Mechanical plating | 2.2 mils (55 µm) |
Zinc-rich paint | 3-6 mils (75-150 µm) |
Each of these thicknesses, representing the same weight per unit area of zinc, would be expected to provide equivalent service life; i.e. 1.7 mils of hot-dip galvanized would give about the same service life as 2.2 mils of mechanical plating or 3-6 mils (depending on the paint formulation) of zinc-rich paint, assuming bond strength and edge protection are not factors.
It is also important to remember for all continuous galvanized sheet materials, including electrogalvanized, the coating weight is given for the total for both sides of the sheet. To obtain the amount of zinc per unit area of surface, the weight given must be divided in two, assuming equal distribution on both sides. For example, an ASTM A653 Class G90 sheet contains 0.90 oz/ft2 of zinc or about 0.45 oz/ft2 per side.
Economic Considerations
Initial cost will always be considered when specifying steel corrosion protection. However, in addition to the initial cost, evaluating the performance of the zinc coating in the intended environment also impacts the economics of the protective system. Hidden costs, such as accessibility of the site, production loss due to maintenance recoating, and rising wages for labor-intensive coatings, such as metal spraying and painting, must also be considered.
The choice of the most economical system is not precise, because neither the timing nor the cost of future maintenance can be predicted accurately. In addition, depreciation of capital investment, tax relief for investment, and maintenance cost and the time value of money must be considered and can change. However, to get the most realistic cost of the coating system throughout the projects life, economic models for comparing the life-cycle costs of different coatings have been developed. The American Galvanizers Association has created an online calculator to facilitate the complex process of evaluating life-cycle costs. The online calculator uses the same economic formula as the one recommended in ASTM A1068, and the data is provided by real-world performance data and published reports (NACE Paper 8279, 2008). Visit lccc.galvanizeit.org to run your own analysis.