Batch Hot-Dip Galvanizing
Batch hot-dip galvanizing, also known as general galvanizing, produces a zinc coating by completely immersing the steel product in a bath (kettle) of molten zinc. Prior to immersion in the zinc bath, the steel is chemically cleaned to remove all oils, greases, soil, mill scale, and oxides. Surface preparation is critical as zinc will not react with unclean steel.
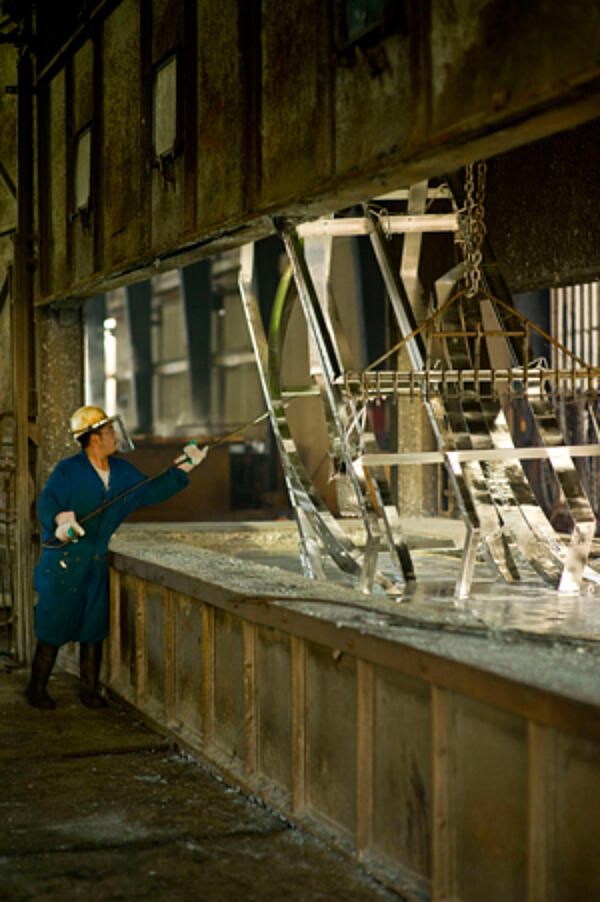
After surface preparation, the steel is immersed in the molten (830 F) zinc bath. The bath consists of more than 98% pure zinc and the remaining 2% or less consists of additives - most commonly aluminum, nickel, and bismuth. These additives help with zinc fluidity and consumption, coating appearance, and other efficiencies. While in the galvanizing kettle, the molten zinc metallurgically reacts with the iron in the steel to form the coating.
Hot-dip galvanized coatings are used on many materials in the construction sectors from electric utility to artistic sculptures. Ranging in size from small parts such as nuts, bolts, and nails to large structural shapes, galvanizing is integral to North American infrastructure. Most commonly batch hot-dip galvanizing is used in atmospherically exposed steel; however, it is also used in fresh and saltwater applications, buried in soil, embedded in concrete, and much more.
Size can be a limitation to the application of hot-dip galvanizing; however, the average length of zinc baths in North America is 40 feet and 55-60 foot kettles are common. Utilizing progressive dipping (immersing one portion of the product and then the other) significantly increases the maximum size that can be accommodated to nearly double the bath size.
Coating Characteristics
The batch hot-dip galvanized coating consists of a series of zinc-iron alloy layers with a surface layer of pure zinc. The unique intermetallic layers are tightly bonded (3,600 psi) and harder than the base steel, offering excellent abrasion resistance. The zinc-iron alloy layers, metallurgically bonded to the steel, become an integral part of the steel rather than just a surface coating. Because zinc is anodic to steel, even if the durable intermetallic layers of the hot-dip galvanized coating are damaged (up to 1/4 inch in diameter) adjacent zinc will sacrificially protect the exposed steel until all of the surrounding zinc is consumed.
Another unique characteristic of the batch hot-dip galvanized coating is its uniform, complete coverage. During the diffusion reaction in the kettle, the zinc-iron alloy layers grow perpendicular to all surfaces, ensuring edges, corners, and threads have coating equal to or greater than flat surfaces. Additionally, because hot-dip galvanizing is a total immersion process, all interior surfaces of hollow structures and difficult-to-access recess of complex pieces are coated. This complete, uniform coverage ensures critical points where corrosion commonly starts have the same protection as accessible, flat exterior surfaces.
Batch hot-dip galvanizing produces a coating thicker and/or denser than other zinc coating processes. The governing specifications for hot-dip galvanizing; ASTM A123/A123M, A153/A153M, A767, as well as CSA G164 and ISO 1461 contain minimum coating thickness requirements based on steel type and thickness.
For more information, visit the hot-dip galvanizing section of this website.