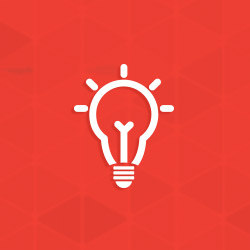
Batch Hot-Dip Galvanizing Production Process
The batch hot-dip galvanizing process, also known as general galvanizing, produces a zinc coating on iron and steel products by immersion of the material in a bath of liquid zinc. Before the coating is applied, the steel is cleaned to remove all oils, greases, soils, mill scale, and rust. The cleaning cycle usually consists of a degreasing step, followed by acid pickling to remove scale and rust, and fluxing, which inhibits oxidation of the steel before dipping in the molten zinc.
There are two different fluxing methods, dry and wet. The dry process is accomplished by pre-fluxing in a zinc ammonium chloride solution. The wet process uses a molten flux blanket on the zinc bath surface.
Hot-dip galvanized coatings are used on a multitude of materials ranging in size from small parts such as nuts, bolts, and nails to very large structural shapes. The size of available zinc baths and material handling restricts the size of steel that can be galvanized. Molten zinc baths 60 feet long and eight feet deep are common in North America. However, the maximum size that can be accommodated in the zinc bath is increased substantially, to near double bath length or depth by progressive dipping (immersing one portion of the product and then the other).
Because the material is immersed in molten zinc, the zinc flows into recesses and other areas difficult to access, coating all areas of complex shapes thoroughly for corrosion protection.
See Also:
Zinc Coatings Publication
Hot-Dip Galvanizing Process Animation
© 2025 American Galvanizers Association. The material provided herein has been developed to provide accurate and authoritative information about after-fabrication hot-dip galvanized steel. This material provides general information only and is not intended as a substitute for competent professional examination and verification as to suitability and applicability. The information provided herein is not intended as a representation or warranty on the part of the AGA. Anyone making use of this information assumes all liability arising from such use.