Repairing HDG Steel
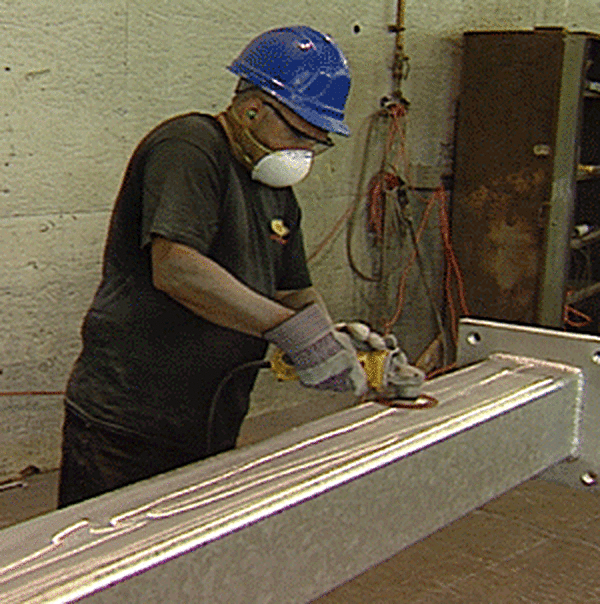
The touch-up and repair of hot-dip galvanized steel coatings is important to maintain uniform barrier and cathodic protection as well as ensure longevity. Although the hot-dip galvanized coating is very resistant to damage, small voids or defects in the coating can occur during the galvanizing process or due to improper handling of the steel after galvanizing. Touch-up and repair of galvanized steel is simple whether newly galvanized or in service for years. The practice is the same, but there are more restrictions to the allowable repairs on a new product than one that has been in service.
The AGA has produced a series of videos for our Touch-Up and Repair series. These six short videos detail the specifications and methods used to touch-up and repair hot-dip galvanized steel. The videos provide highly beneficial visual aids to those needing assistance with touch-up and repair, whether in the plant or the field. Topics include proper materials to use while performing the process, as well as specifications to follow and proper application of the repair materials.
The main restriction in the specification for repairing newly galvanized material is the size of the area which is outlined in the product galvanizing specifications:
- ASTM A123
- One inch or less in narrowest dimension
- Total Area can be no more than 1/2 of 1% of the accessible area to be coated or 36in2 per short ton per piece, whichever is less
- ASTM A153
- The bare spots shall have an area totaling not more than 1% of the surface area to be coated excluding threaded areas of the piece
- ASTM A767
- Total area in any 1ft length shall not exceed 1%
When it comes to repairing galvanized steel in the field, there is no limitation to the size that can be repaired. The zinc coating is difficult to damage, and field fabrication that requires removal of the coating should be minimized as much as possible. As noted before, the cathodic protection of the coating will provide some protection to uncoated areas, but the best practice for longevity is to touch-up any bare areas.
A listing of various manufacturers and products for the maintenance and repair of hot-dip galvanized structures is available for download.
ASTM A780 Practice for Repair of Damaged and Uncoated Areas of Hot-Dip Galvanized Coatings details how to repair a damaged hot-dip galvanized coating regardless if it is immediately after galvanizing or once it is in the field. The specification explains how to use the various repair methods as well as the required coating thickness for the repaired area. Touch-up materials are required to meet a coating thickness of at least 2.0 mils (50.8 µm) for one application, and the final coating thickness of the repair area is dictated by the material used to do the repair.
ASTM A780 contains three acceptable methods of touch-up and repair of hot-dip galvanized steel:
Zinc-Based Solders
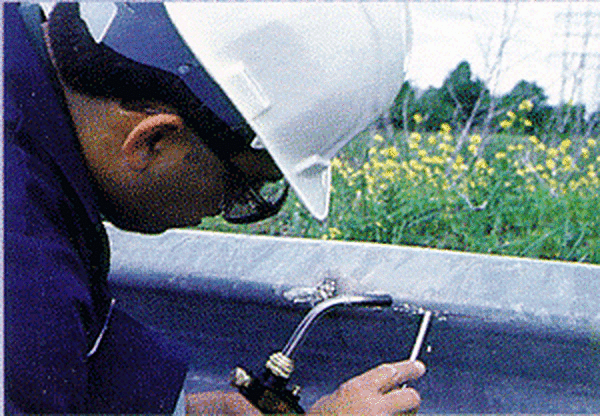
Soldering is done with zinc-based alloys in either a stick or powder form. The area being repaired needs to be preheated to approximately 600 F (315 C). The acceptable material compositions of solders used for repair are included in the ASTM A780. The repair coating thickness must meet the specification requirement for the material category of the part with a maximum thickness of 4 mils (100 µm). The thickness is measured by any of the non-destructive methods in A123/A123M. Zinc-based solder products closely match the surrounding zinc and blend in well with the existing coating appearance.
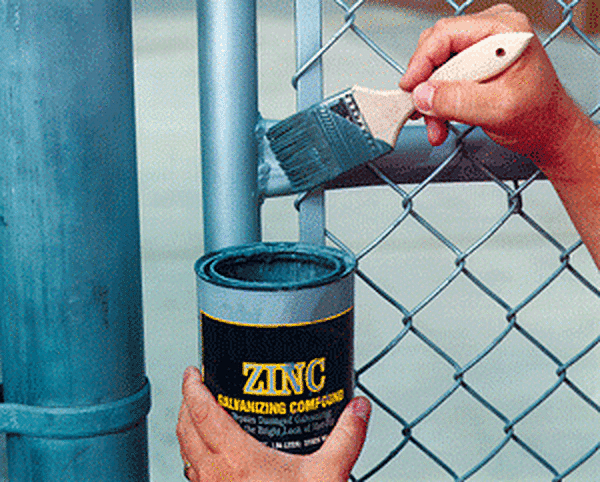
Zinc-Rich Paints
Zinc-rich paint is applied to a clean, dry steel surface by either a brush or spray. Zinc-rich paints must contain either between 65% to 69% metallic zinc by weight or greater than 92% metallic zinc by weight in dry film. Paints containing zinc dust are classified as organic or inorganic, depending on the binder they contain. Inorganic binders are particularly suitable for paints applied in touch-up applications of undamaged hot-dip galvanized areas. The coating thickness for the paint must be 50% more than the surrounding coating thickness, but not greater than 4.0 mils (100 µm), and measurements should be taken with either a magnetic, electromagnetic, or eddy current gauge to ensure compliance.
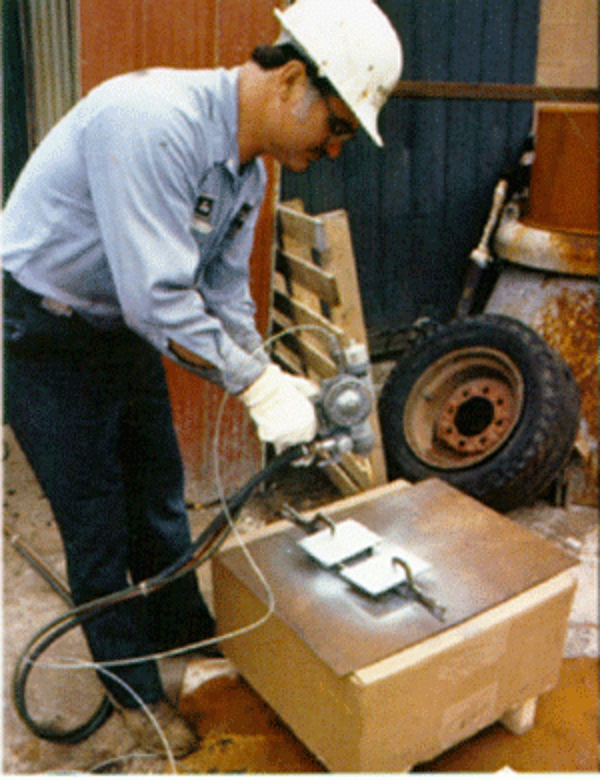
Zinc Spray (Metallizing)
Zinc spray, or metallizing, is done by melting zinc powder or zinc wire in a flame or electric arc and projecting the molten zinc droplets by air or gas onto the surface to be coated. The zinc used is nominally 99.5% pure or better. The renovated area shall have a zinc coating thickness at least as thick as that required in ASTM A 123/A 123M for the material category. For best results, thickness measurements for the metallized coating should be taken with either a magnetic or an electromagnetic gauge.