Passivation
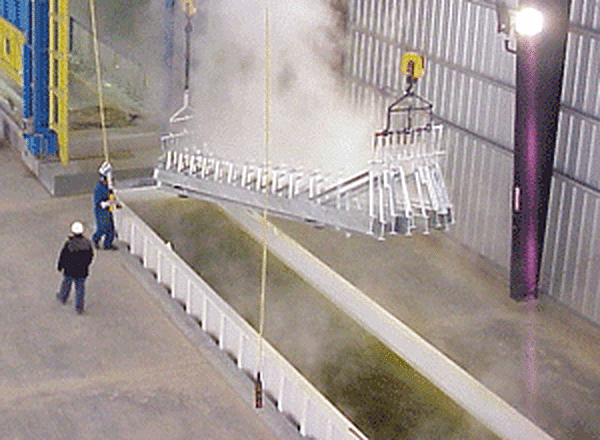
Hot-dip galvanized coatings protect steel by providing both cathodic and barrier protection. The naturally occurring formation of a tenacious, abrasion-resistant zinc carbonate patina provides yet another component to the protection afforded by galvanizing. When there are concerns with environmental and/or storage conditions to which the galvanized steel will be exposed, passivation treatments can be used to prevent the formation of wet storage stain. Generally, passivation coatings last about six weeks before being consumed. At that time, galvanized steel will begin to weather naturally.
Although galvanized steel in typical use conditions is highly tolerant of diverse atmospheric and environmental conditions, passivation-quenching can be done when environmental, storage or shipping conditions warrant. Because the galvanized zinc coating is most vulnerable to the formation of excessive zinc oxides and zinc hydroxides during its first six weeks, the thin layer of passivation agent delays their formation. Once the passivating agent is gone, galvanized steel begins to form its protective zinc patina.
Chromate passivations sometimes are used on galvanized reinforcing bar to control reactions between zinc and concrete while the concrete cures, particularly the hydrogen evolution that may affect bonding properties. Tests of the bond strength on chromate-passivated galvanized rebar show equal or slightly better bond performance when compared to black reinforcement bars.
Passivation should be avoided if the part is going to be duplex coated (painting or powder coating over the galvanized steel) as quenching can affect adhesion of the top coat system.