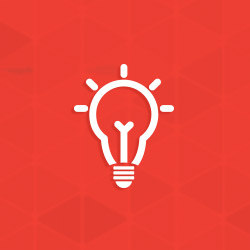
Grind Marks on Galvanized Steel
Are grind marks acceptable on my hot-dip galvanized steel?
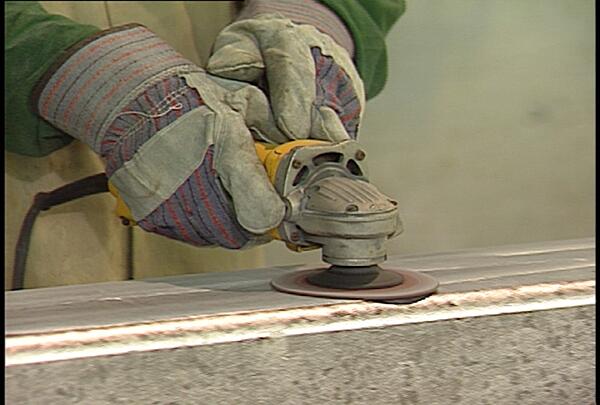
Simply put: Yes, grind marks on hot-dip galvanized steel do not affect the corrosion protection performance of the coating and are acceptable under ASTM A123. Over time, the natural weathering process of the zinc coating causes the marks to become less noticeable and more uniform with the rest of the surface. The rest of this article will focus on some of the reasons grinders may be used on a hot-dip galvanized coating and why the marks left behind are not cause for rejection.
A hot-dip galvanized coating is generally specified for its corrosion protection performance and not for its appearance. Therefore, ASTM A123 specifies only a few requirements for the finish and appearance of the coating. The specification also does not have many restrictions on the production process of hot-dip galvanized coatings; leaving the details of production in the hands of experienced galvanizers. The guidance provided by ASTM A123 leaves room for galvanizers to repair and clean the galvanized coating after it has been dipped and cooled before it is ready to ship. There are no restrictions on the methods to be used to clean up the coating, as long as the coating properties meet specifications.
Some of the required coating properties under ASTM A123 may require the galvanizer to touch-up the coating before it passes inspection. The requirements for a finish, for example, in section 6.2 of ASTM A123, say a piece may be rejectable for, …local excess coating thickness which would interfere with the use of the product or make it dangerous to handle (edge tears or spikes)… In addition to the requirements for the finish of a hot-dip galvanized coating, the appearance requirements of section 6.4 states, Lumps, projections, globules, or heavy deposits of zinc which will interfere with the intended use of the material will not be permitted. Each of these requirements may necessitate a need for a small amount of touch-up in order for the coating to be compliant with A123.
Due to the nature of the hot-dip process, the edge tears, spikes, lumps, and extra deposits of zinc are inherently going to be present on some steel directly after being dipped. When steel is drawn from the molten zinc bath, there is bound to be some zinc that cools in a run-off pattern. However, these runoffs can create areas that are not acceptable under A123 and therefore must be removed somehow. Fortunately, these inclusions of extra zinc are not detrimental to the performance of the coating and can be easily removed through the use of a rotary grinder. The process is fast and simple, but it may leave marks on the surface of the coating that could be alarming to some owners.
The marks left on the surface after grinding are purely cosmetic and do not affect the corrosion protection performance of the coating. Coating thickness measurements in the area where the grind marks are will confirm a coating meets the specifications of A123. They should be no cause for alarm, and in time will become more uniform with the rest of the coating.
© 2025 American Galvanizers Association. The material provided herein has been developed to provide accurate and authoritative information about after-fabrication hot-dip galvanized steel. This material provides general information only and is not intended as a substitute for competent professional examination and verification as to suitability and applicability. The information provided herein is not intended as a representation or warranty on the part of the AGA. Anyone making use of this information assumes all liability arising from such use.