Field Inspection
Inspection of hot-dip galvanized steel products does not end once they are accepted at the galvanizer's facility or job site. Once erected, any good corrosion protection strategy includes periodic inspection and maintenance to ensure the protective coating is performing as expected. When inspecting hot-dip galvanized steel in the field, the inspector should be aware of potential accelerated corrosion areas and aesthetic surface defects.
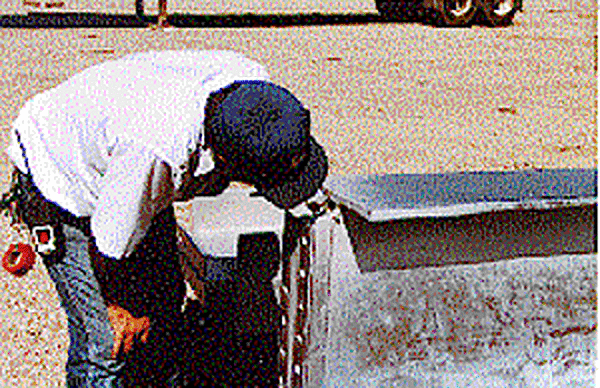
When inspecting a galvanized coating in the field, the number one concern is the number of years remaining before the coating will need to be touched-up or replaced. Fortunately, estimating the remaining time to first maintenance for hot-dip galvanized coatings in atmospheric exposures is relatively simple. For a ballpark estimation, use a magnetic thickness gauge to take a coating thickness measurement and check the thickness value against the AGA's Time to First Maintenance Chart.
In addition to taking coating thickness measurements, the galvanized coating can be visually inspected for signs of accelerated corrosion in specific areas. Thickness measurements should be taken in these areas to ensure adequate zinc coating remains or if touch-up should be performed. Corrosion-prone areas to inspect further include:

Crevices
When corrosive elements such as water penetrate crevices, the limited air flow can create differences in potential creating anodic and cathodic areas which can lead to corrosion. Some common areas include overlapped areas, mated sections between fasteners, and areas where the galvanized coating is butted up against another surface such as wood, concrete, or asphalt. When possible, crevices should be avoided during the design process.
Dissimilar Metals in Contact
When dissimilar metals are in contact, galvanic corrosion can occur. Zinc, which comprises the galvanized coating, is high on the Galvanic Series of Metals; and therefore, will preferentially corrode to almost any other metal with which it is in contact. When possible, preventing dissimilar metals from being in contact should be addressed during the design process. Electrically isolating dissimilar metals from one another stops galvanic corrosion and can be accomplished by using plastic or rubber grommets between the dissimilar metals or by painting the cathode. When the surface area of the cathode is much larger than the anode, galvanic corrosion can quickly consume the anodic material.
Areas Where Water Pools
Flat areas can collect water and other corrosive elements and can have higher corrosion rates than vertical surfaces. Visually observing galvanized steels flat areas and taking coating thickness measurements will ensure adequate corrosion protection remains. When possible, areas that collect water can be addressed by providing drain holes to prevent moisture from pooling on the surface for long periods. If drain holes do exist, inspect the drain holes of the galvanized steel for corrosion and touch-up when necessary.
Previously Touched-Up Areas
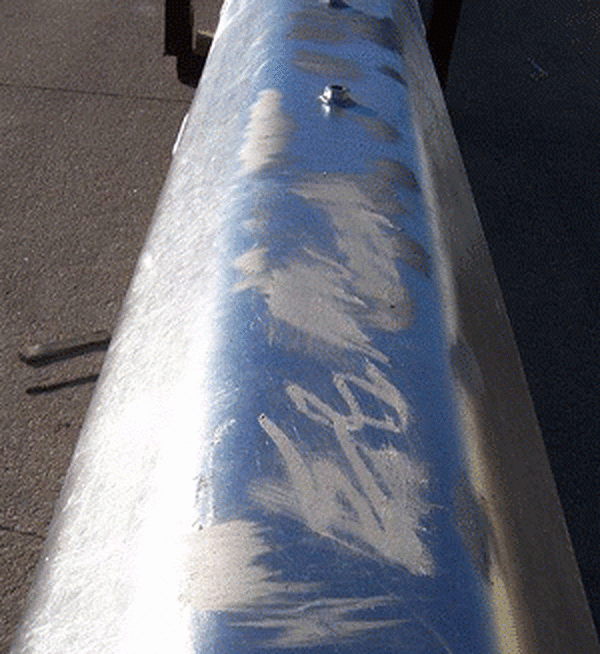
Areas of hot-dip galvanized steel previously touched-up either after the initial coating or erection often corrode more quickly than the surrounding zinc coating and should be inspected visually and tested with a magnetic thickness gauge. These areas may be touched-up when necessary using the instructions listed in the Touch-Up and Repair section of this publication to extend the service life of the part.
When inspecting galvanized steel in the field, there are a few common appearance issues you may observe. Most are surface or aesthetic conditions and not cause for concern; however, others may require attention and/or maintenance. The most common appearance issues on galvanized steel after being in service for a number of years include:
Brown Staining
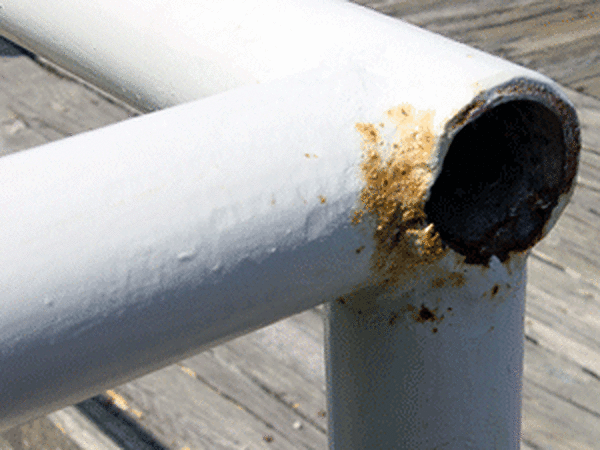
Often mistaken for corrosion, brown staining is a surface defect created when iron in the zinc-iron alloy layers oxidizes. Sometimes hot-dip galvanized coatings form without a free zinc layer, leaving intermetallic layers on the surface. Also, as galvanized steel weathers, the eta layer will be consumed and can lead to this phenomenon. Brown staining forms when free iron in the intermetallic layers reacts with moisture in the environment and oxidizes, discoloring the surrounding zinc coating. To distinguish between red rust and brown staining, simply test the area with a magnetic thickness gauge. If the gauge reading shows a coating thickness, it is brown staining and the corrosion performance of the galvanized coating is not affected. As brown staining is simply an aesthetic concern, touch-up is not necessary for the stained area, and it may be removed by brushing with a nylon bristle brush.
Wet Storage Stain
Improper storage and tight stacking of galvanized products can lead to the development of wet storage stain or zinc oxide and hydroxide build-up on the surface. If galvanized products are going to be stored before erection, it is important to properly vent the bundle to avoid the development of wet storage stain.
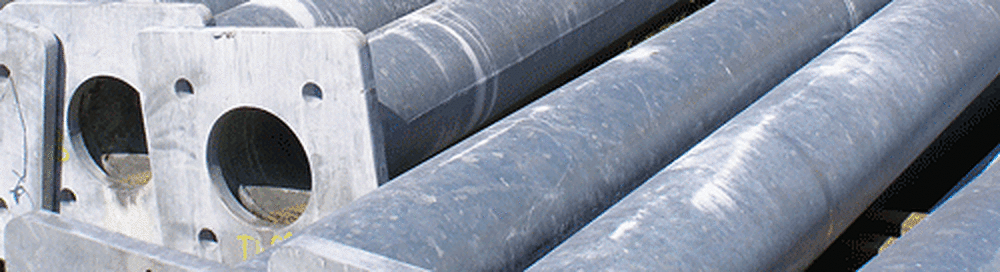
Similar to the development of wet storage stain when storing materials, galvanized products in place that have moisture on the surface without the movement of free-flowing air can develop oxides and hydroxides that look like wet storage stain. A common area for this to occur is on surfaces where snow is piled on the surface and left to melt or in areas where water pools for extended periods without drying. Wet storage stain occurs most often during the first month after galvanizing.
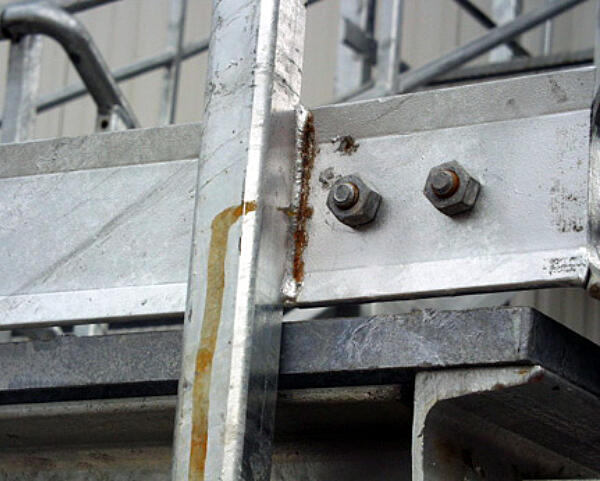
Weeping Welds
Weeping welds can be seen immediately after galvanizing, but also can occur after the steel is in service. As reviewed earlier, weeping welds are mostly a cosmetic concern; however, corrosion can be accelerated in the area where the liquids and rust bleeding are leaking. To clean and seal weeping welds, you can wash away the oxides on the outer area and apply epoxy or caulk to the area to prevent water from penetrating the crevices in the future.
Bare Spots
The galvanized coating can be compromised during delivery, handling, erection, and while in use. Some cathodic protection is offered to bare areas of the steel by the surrounding galvanized coating, but these areas can still rust if the area is too wide or corrosive elements frequently attack the steel.
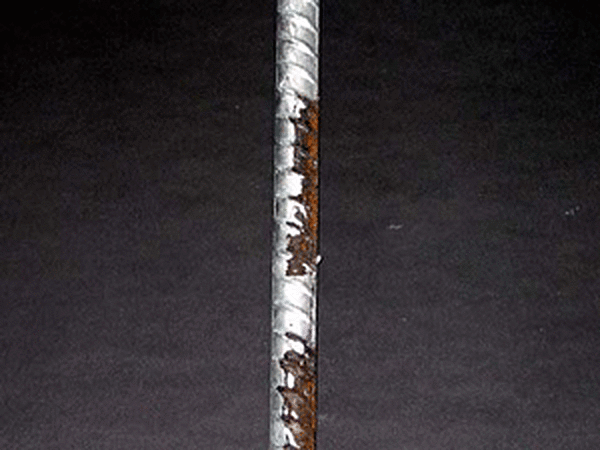
Research has shown the galvanized coating offers cathodic protection to bare areas between 1 mm - 5 mm wide depending on the electrolyte that electrically connects the galvanized coating to the bare area. Bare areas should be touched-up in accordance with the procedures outlined in this publication to ensure the longevity of the surrounding coating.