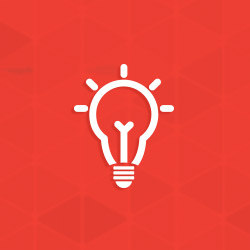
Mechanical Plating vs. Hot-Dip Galvanizing
Recently I saw some bolts described as "galvanized bolts." Are these bolts all hot-dip galvanized for corrosion protection?
Often when purchasing zinc-coated bolts, there is a misunderstanding about the difference between the different methods that can produce a zinc coating on steel. Many times a mechanically galvanized bolt will be described as a "galvanized" bolt, leading to the assumption that the bolt is hot-dip galvanized. There is a difference between the two methods; knowing the difference can be important in evaluating corrosion protection for a project.
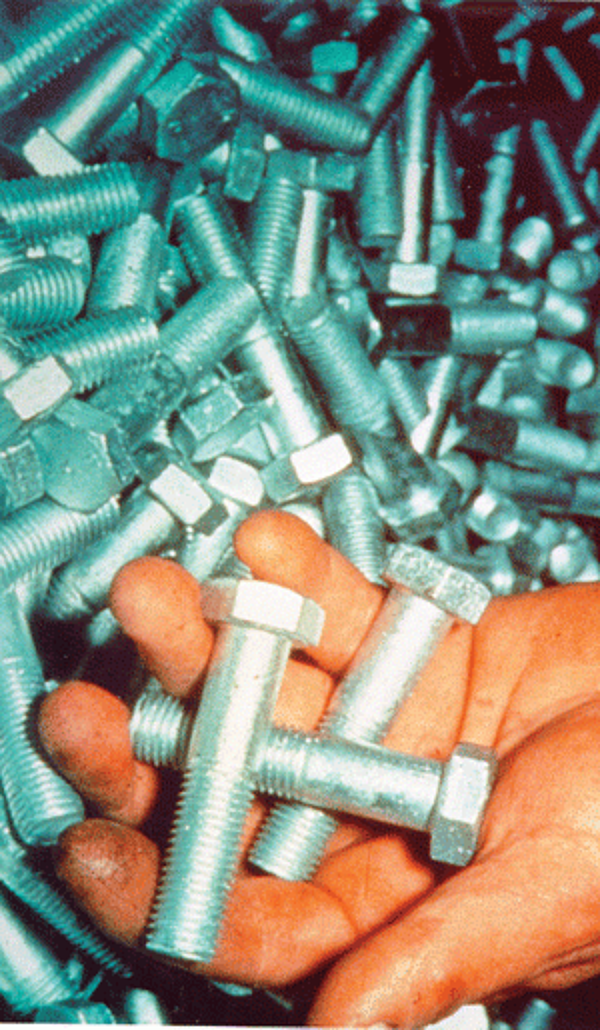
Hot-dip galvanizing, by the nature of the process, guarantees a coating that is a mixture of iron and zinc. The coating is generally uniform on all surfaces, providing excellent protection at the corners and edges. The hot-dip galvanizing process creates a metallurgical reaction between the zinc and the steel resulting in a series of zinc-iron alloy layers. The pure zinc layer and the zinc-iron alloy layers are anodic to steel, providing sacrificial protection in the event the coating is scratched or damaged. This cathodic protection plus the barrier of the zinc coating give a double protection system for corrosion prevention.
The mechanically plated coating consists of a flash coating of copper, followed by tumbling the part in a barrel with glass beads and zinc powder. Coating thickness requirements contained in ASTM Specification B695 range from 0.2 to 4.3 mils. The coating has a density of about 0.45 oz/ft2/mil compared to the hot-dip galvanized coating density of about 0.6 oz/ft2/mil. The hot-dip coating has over 30% more zinc per unit volume than the mechanical coating. The corrosion protection is directly related to the amount of zinc in the coating.
The mechanically plated coating consists of rounded particles of zinc loosely bonded together. The bond between zinc and steel and zinc to zinc is considerably weaker than the metallurgical bond found in hot-dip galvanized coatings by several orders of magnitude. Edge, corner, and thread coating thicknesses are lower because of the deposition method of the mechanical process.
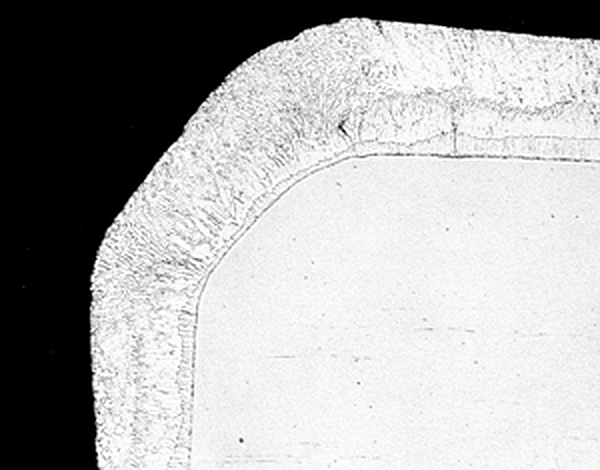
Although the mechanically plated fasteners appear to be reasonable products, there must be doubts regarding adhesion and the thinness of the coating at the sharp edges of nuts and bolts and thus the corrosion protection provided by this process. These faulty characteristics greatly affect the long-term corrosion protection of the fastener. Insist on hot-dip galvanized fasteners for reliable long-term corrosion protection.
© 2025 American Galvanizers Association. The material provided herein has been developed to provide accurate and authoritative information about after-fabrication hot-dip galvanized steel. This material provides general information only and is not intended as a substitute for competent professional examination and verification as to suitability and applicability. The information provided herein is not intended as a representation or warranty on the part of the AGA. Anyone making use of this information assumes all liability arising from such use.