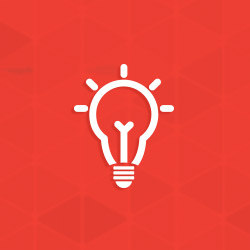
How Much Money Would the Piggy Bank Hold if the Golden Gate Bridge Had Been Hot-Dip Galvanized?
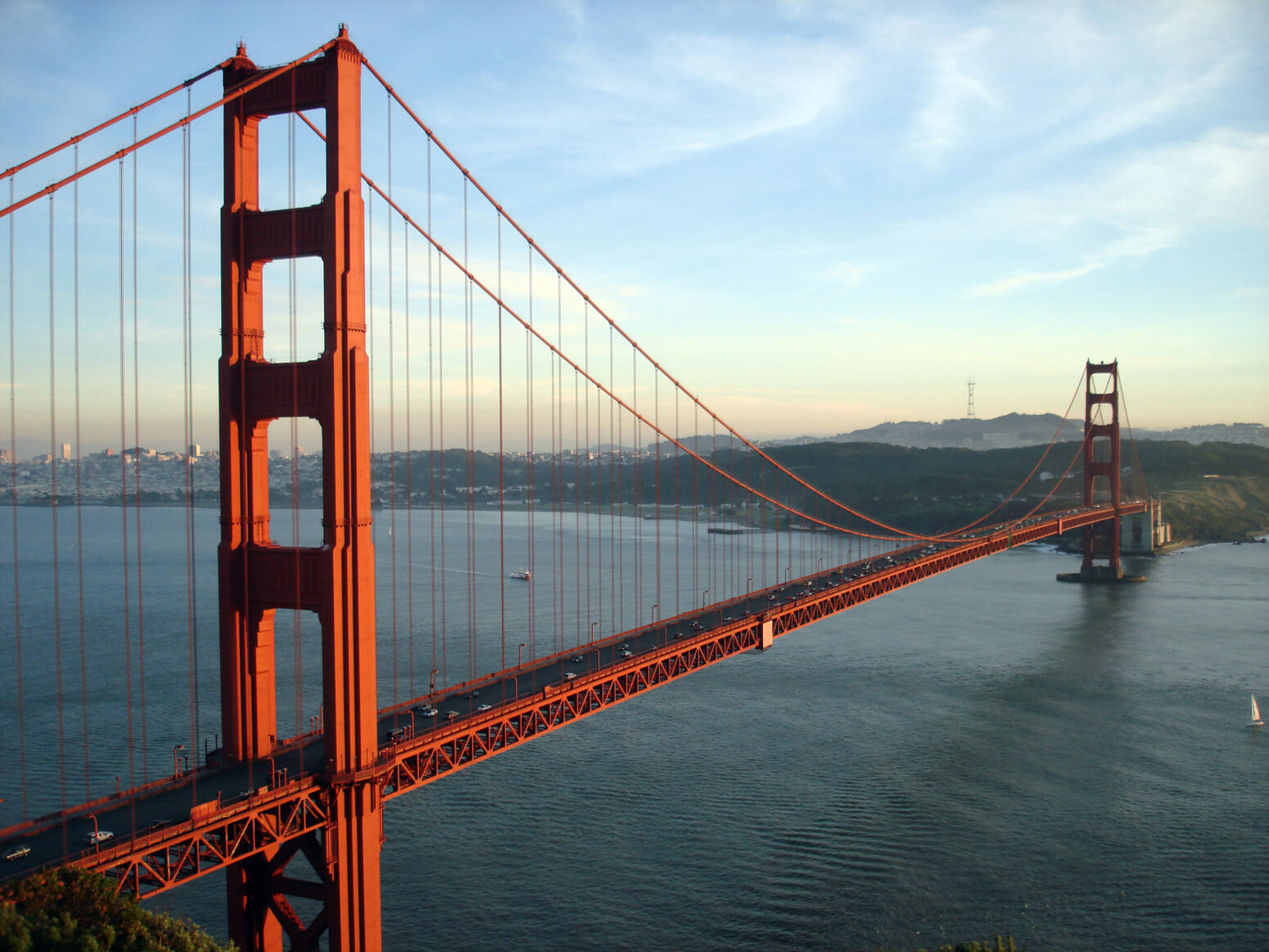
An iconic landmark known worldwide since its opening in 1937 is the 4,200 foot-long main span Golden Gate Bridge, connecting Fort Point in San Francisco to Marin County. Its name actually comes from the body of treacherous water over which it crosses, originally named Chrysopylae by Captain John C. Fremont in 1846, and now known as the Golden Gate Strait. The Golden Gate Bridge was originally painted and has been continuously painted ever since, racking up huge costs. But what if all the structural steel used to erect the bridge had been hot-dip galvanized? Would that even be practical given the scope of the project?
Most galvanizing operations today have kettles/tanks of molten zinc approximately 42 to 60 long and would not have been able to handle the very large and long structural beams used on the bridge. The galvanizing kettle at the time would have had to be about 100 long, holding 5 million pounds of molten zinc. What would the economic comparison look like? Unlike 2014, where hot-dip galvanizing is often less costly than paint systems, galvanizing in the 1930s was likely about 15% more expensive initially than the first coat of paint, but life-cycle cost, the total of all maintenance costs over the lifetime of the bridge, would surely have delivered large cost savings if the bridge were hot-dip galvanized. To answer those questions, lets first take a look at some of the specifications for this aging marvel of engineering and construction.
Specifications
The Golden Gate Bridge was the largest suspension bridge in the world prior to the construction of the Verrazano-Narrows Bridge in New York 27 years later. All 24,000 tons of the two main cables, suspension cables, and accessories were hot-dip galvanized and painted the unique orange-vermilion color called international airway orange. The original architect chose this color to make the bridge more visible in the regular fog above the water. An additional 83,000 tons of structural steel used for the suspended structure (24,000 tons), anchorages (4,400 tons), approaches (10,200 tons), and two 746 tall towers (44,000 tons) was painted with a lead-based paint from the outset, taking a full 27 years of touchup to complete. There are 1.2 million rivets used in the connections.
In 1965 the decision was made to remove the lead-based paint and apply a zinc silicate primer and a vinyl topcoat. That effort took a full 30 years to complete, and since 1995 there have been 38 full-time painters applying an acrylic topcoat and 17 iron workers replacing corroded steel on the bridge.
What If?
So, if all 83,000 tons of the structural steel had been hot-dip galvanized, what would the economic savings be? Galvanizing lasts 75 to 100 years before any maintenance is required, even in corrosive environments such as above the water in San Francisco. All of the 27 years of touchup painting, the stripping of the lead-based paints, and 30 years of painting that followed would have been unnecessary. And the cost associated with 38 painters and 17 iron workers continuously working on the bridge since 1995 could have been pocketed by the taxpayers in the state of California or directed toward many other worthwhile infrastructure projects.
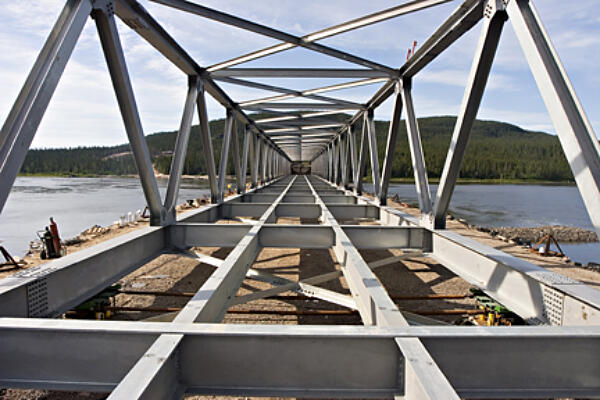
Qualifying the Analysis
Before getting too excited about the prospect of enormous savings hot-dip galvanizing may have provided, there are a few assumptions to make to estimate how big the pig would have to be to hold all that money.
First, since lead-based paints were virtually banned decades ago there is no cost basis today to use for the initial painting in the 1934 1937 timeframe and the touchup from 1937 1965. A paint system used today for a bridge might be a three-coat inorganic zinc/epoxy/polyurethane system.
Secondly, to avoid making the analysis quite complex with the introduction of the time value of money, i.e. net future value and net present value, lets assume the decades of touchup painting and top-coating are a single point in time. Third, back then, and even today there was no hot-dip galvanizing kettle large enough to accommodate the very large beams and fabrications which may have been as large as 100 long x 10 wide x 12 deep. However, with todays technology it is possible to build a very large galvanizing kettle to handle these large beams and fabrications. Let's assume one is built just for this job.
Finally, although the marine environment is fairly aggressive to zinc and the galvanized coating, no touchup would be required until 2014. The Zinc Coating Life Predictor and the American Galvanizers Associations Time To First Maintenance Chart indicate this to be a good approximation of durability.
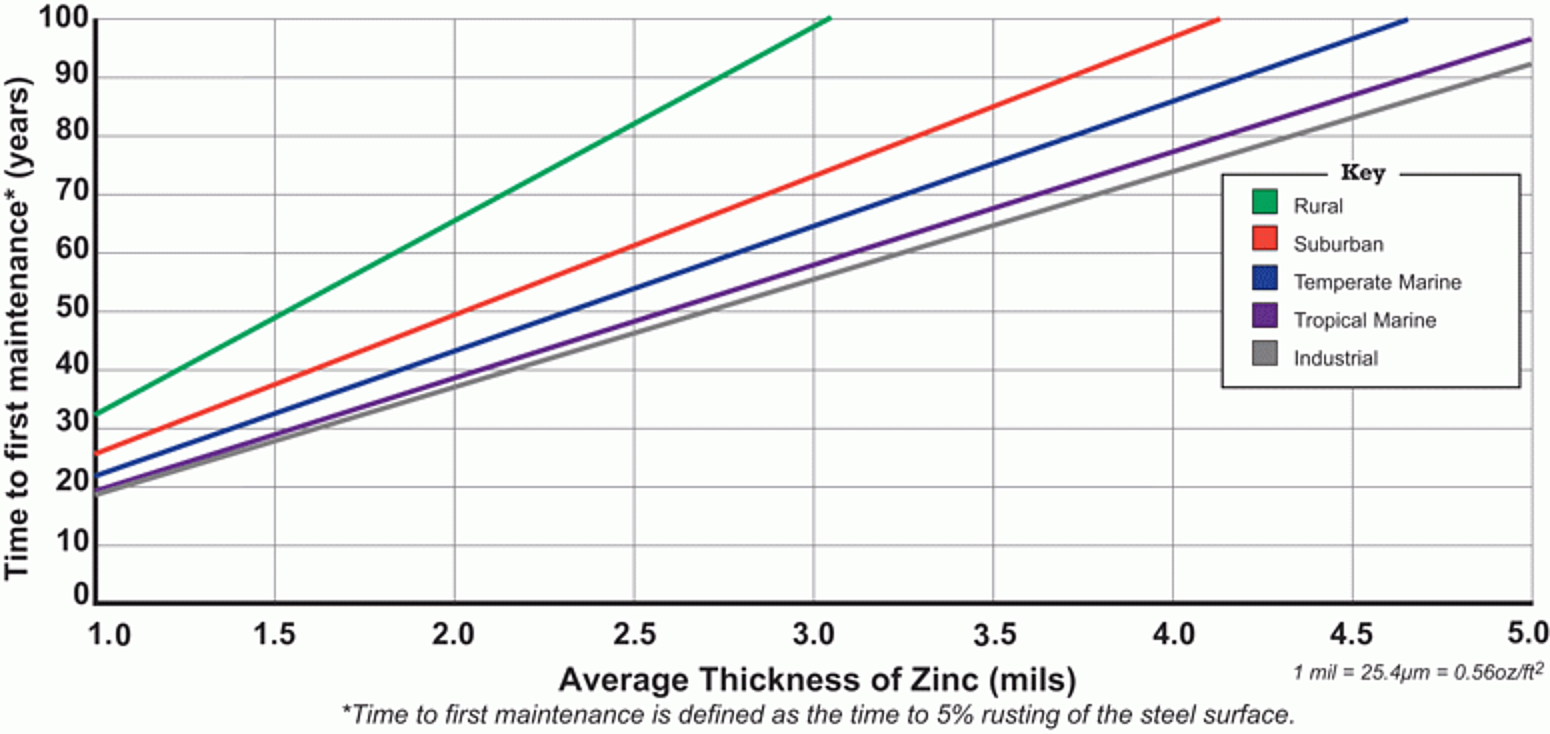
Analysis
The analysis of total estimated cost for the paint systems (collected by KTA and reported in NACE Paper 08279) as we know them to be and the cost of galvanizing to specification ASTM A123 had it been utilized is as follows: (2014 $s and no consideration for time value of money, i.e. NFV & NPV )
Paint Systems | Hot-Dip Galvanizing | |
---|---|---|
Initial Shop Appliction in 1937 (IOZ/Epoxy/Polyurethane)1,2 |
$22 million | $25 million |
Touchup 1937-1965 (Year 15 and 19)3 |
$42 million | N/A |
Galvanizing Operation4 (100' x 12' x 12') |
N/A | $20 million |
Repaint 1965-1995 | $120 million (est.) | N/A |
Maintenance Paint 1995-2014 | $120 million (est.) | N/A |
Iron Workers | $60 million (est.) | N/A |
Total | $364 million | $45 million |
1 Paint cost derived from lccc.galvanizeit.org |
Summary
The hot-dip galvanizing industry has promoted life-cycle cost analysis for many decades as a more accurate estimate of total project cost than initial cost alone. This example shows a conservative, $319 million as the potential savings had galvanizing been used on the Golden Gate Bridge. Furthermore, if the time value of money spent to paint and repaint the bridge over seven plus decades was calculated, the true savings would be closer to a billion dollars. That is a startling number for someone not aware another corrosion protection system besides paint is available.
Beyond the savings is the revelation this analysis indicates for large infrastructure projects such as the Golden Gate Bridge, it is economically practical to build a large (100 long), local galvanizing operation, even if only for one-time use. The galvanizing plant could be constructed within 18 months and located either in close proximity to the primary fabricator of the steel or adjacent to the project site. Furthermore, there is also the option to design the beams and fabrications with connections so they can fit within the common 60 kettles (either by single or progrssive dipping) currently located around the country.
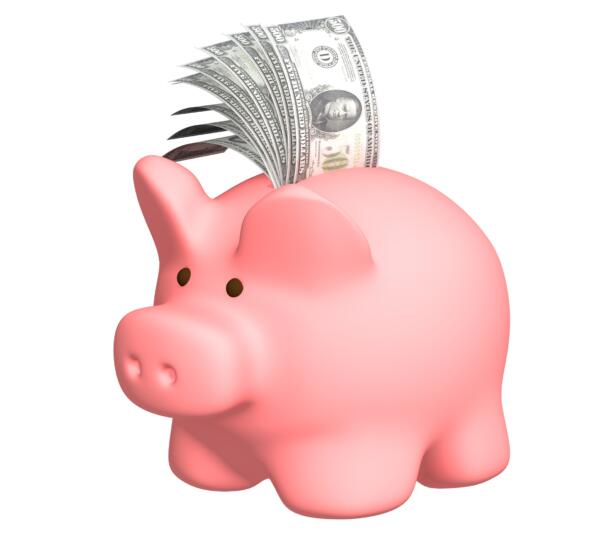
Today, hot-dip galvanizing is often less expensive initially than most two- and three-coat systems, making the payback period even shorter and the long-term savings greater. This is obviously a simplistic analysis, but the concept of building a dedicated galvanizing operation for large projects is one with merit that should be considered by public authorities, architects, and engineers during the concept and design phases. It is likely once there is federal, state, or regional commitment to galvanizing large infrastructure projects with longer, wider, and deeper structural steel/assemblies than are typically galvanized today, permanent large kettle operations would be established by the galvanizing industry. Such quasi-public private partnerships make sense and could deliver hundreds of millions of dollars in taxpayer savings and require a very large pig to hold.