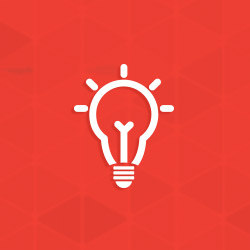
Galvanizers Cash-In with Sustainable Lighting and Heat Recovery Systems
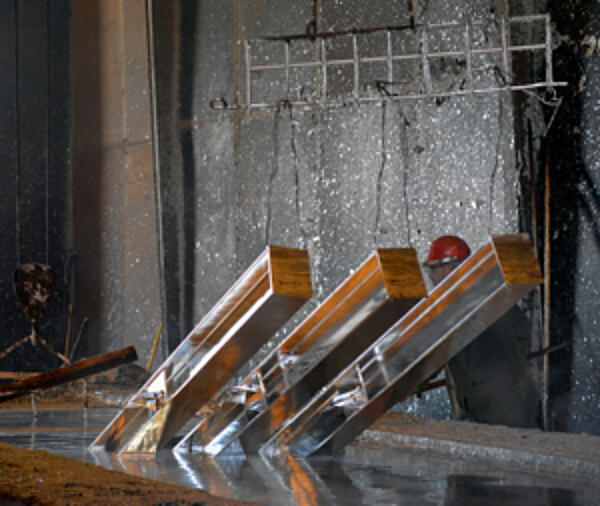
Hot-dip galvanizing (HDG) is the process of dipping fabricated steel or small parts such as bolts, nuts, washers, and nails into a kettle or vat containing molten zinc. The process is inherently simple, which provides a distinct advantage over other corrosion protection methods. While the steel is in the kettle, the iron in the steel metallurgically reacts with the molten zinc to form a tightly-bonded alloy coating that provides superior corrosion protection to steel often for 75 years or more. Specifiers understand reducing maintenance to materials over the life of a project is inherently sustainable, which is why many advocate for the use of galvanized steel products. However, there has long been a question (misperception) as to how sustainable the process of producing HDG is and whether improvements are being made in the plants.
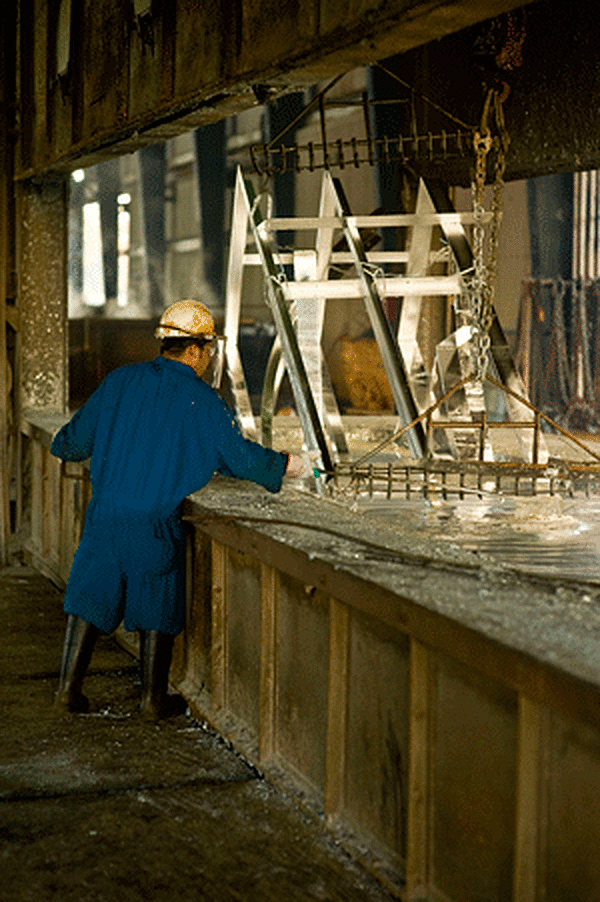
Energy use in the galvanizing process comprises approximately 20% of the overall cost of production, so galvanizers are constantly committed to driving that cost down, which in turn makes them better stewards of the environment, a measure which is meaningful to them and their customers. Readers of this article will learn how a focus by two specific galvanizers on electric consumption by in-plant lighting systems rewarded them with an 18-month payback on their investment and a long-term, annual savings of $18,000 and $26,000, respectively. Additionally, you will learn how heat capture systems have delivered major reductions in natural gas consumption across much of the industry. Fundamental to the process is the use of significant energy, almost universally clean, natural gas, to heat the zinc metal to a molten state. Because this energy use comprises about 20% of the cost to produce galvanized steel, a reduction in consumption delivers immediate economic value to galvanizing companies but just as importantly a step toward their being more sustainable.
First, lets look at excellent lighting systems which for obvious personnel safety reasons, are required in the galvanizing plant. For those currently using incandescent or halogen lamps in their fixtures there is a great opportunity to reduce electricity consumption, realize substantial operating cost savings, and contribute to a cleaner environment. Two galvanizers recently decided to engage the services of Chattanooga-based EnerG3 to evaluate the potential kilowatt hour and cost savings. EnerG3s process includes:
- Measuring the current kilowatt (kW) load by counting how many and determining what type of lighting fixtures/lamps the facility is currently using.
- The hours of plant operation when the lights are in use is then collected and averaged over a period, and this average is multiplied by the kW load to calculate the kilowatt hours (kWh) the facility is consuming. This is the benchmark from which a decision to proceed with a lighting upgrade to LEDs is based.
- This benchmark is then compared to the kWh load of the LED lighting system design proposed. The design typically utilizes motion sensors, daylight harvesting sensors, and photo cells, to further reduce the kWh load.
- The spread between the benchmark kWh and LED kWh is the planned kWh consumption reduction.
Using available energy rates from the providing power authority, the savings are calculated by multiplying the reduction in kWh by the energy rate.
Lets look at Galvanizer #1 who produces on average 2,500 tons/month of galvanized steel.
LED System Cost | $ 79,800 |
Utility Incentive | ($11,610) |
USDA Grant | ($19,950) |
EPAct Tax Deduction (cash value) | ($ 9,650) |
Net Project Cost | $ 38,590 |
Annual Savings | $ 26,150 |
Life-Cycle Savings (15-Year Service Life) | $392,000 |
Total kW Reduction | 60% |
Simple Payback | 1.5 Years |
Galvanizer #2 is considerably smaller than Galvanizer #1 but the cost and environmental savings from implementing a sustainable LED system is just as impressive and demonstrates scale is not a significant variable in the analysis to upgrade. Below are the metrics for Galvanizer #2:
LED System Cost | $ 55,358 |
Utility Incentive | ($29,779) |
Net Project Cost | $ 25,579 |
Annual Savings | $ 18,404 |
Life-Cycle Savings (15-Year Service Life) | $276,060 |
Total kW Reduction | 64.5% |
Simple Payback | 1.4 Years |
Based on the excellent payback and the kW consumption savings to the environment, both galvanizers proceeded with the LED system implementation and cashed in. Additionally, both realized substantial annual savings because there is no expense for new bulbs and ballasts, nor the associated maintenance labor hours once required by their old system. A good environmental decision with a good economic outcome.
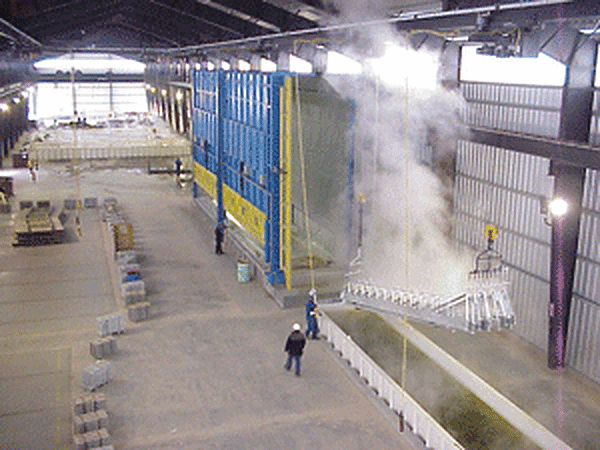
Secondly, lets look at heat capture systems within the hot-dip galvanizing process itself which represents an initial investment by the galvanizer of $40,000 to $60,000, not a small sum for a plant which may generate only about $6 million to $10 million in annual sales. The kettle or vat of molten zinc is contained on five sides, with an open top where the bare steel is lowered into the molten zinc. A natural gas-fired furnace applies heat to the four sides of the kettle to initially melt the solid zinc ingots and to keep the zinc molten at 830 F 850 F. This is a 24/7/365 function.
As you would expect, some heat is lost to the atmosphere in the immediate area of the kettle sides. A common practice in the industry is to locate an exhaust system in the furnace area to capture this escaping heat and collect it via a mechanical system where it is transferred into a heat exchanger. The captured heat, approximately 80% of the exhaust heat, is then used to heat water to steam and then passed through coils to either heat the pickling solution used to clean the bare steel prior to immersion in the molten zinc or simply to pre-heat the bare steel to minimize the heat loss in the zinc when the steel is first immersed. For those who utilize such a heat recovery system the realized savings are approximately $8,000 to $10,000 per year and the payback period is about 5 years. These types of savings and payback are smart for the galvanizer and good for our environment.
In summary, hot-dip galvanized products are readily recognized by the specifying community as being very sustainable because they generally require no maintenance for 75 years or more and use a healthy and infinitely recyclable metal zinc. The economic savings and reduced environmental impact are obvious. What isnt so obvious to architects and engineers are the strides the galvanizing industry is making to also make the process sustainable. Using LED lighting systems and heat capture systems are just two of the steps that can be taken by galvanizers to improve overall sustainability. However, there is tremendous room for improvement and just as importantly there is a high level of commitment to implement more energy saving systems within the process. Ultimately, these current and future improvements and reduction in energy consumption will favorably impact the life-cycle assessment and environmental product declarations (EPDs) for all hot-dip galvanized products, a huge step in making galvanized construction materials more accepted and sustainable.
Data and financial analysis for the lighting systems provided courtesy of EnerG3