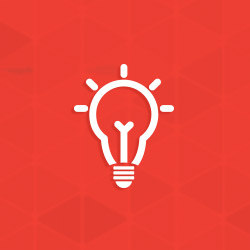
AGA Resources for Progressive Dip Calculations
How do I calculate the maximum length for progressive dipping?
To assist you with more precise progressive dipping checks and calculations, the AGA has two brand new resources available: the AGA Progressive Dip Charts and the AGA Progressive Dip Calculator.
Hot-dip galvanizing is a complete immersion process, which means parts must fit in the galvanizing bath to be fully coated. Size limitations are governed by the galvanizing kettle dimensions, but the average kettle length in North America is 40 ft (12 m) and 50-60 ft (16-18 m) kettles are common. If an item is too large for total immersion in the kettle, progressive dipping can be utilized to immerse each end of the article sequentially to coat the entire item. In other words, if at least half the steel article can be submerged in the galvanizing bath, the part can be partially galvanized at an angle, flipped and rehung, then dipped on the remaining surface to fully coat the entire part with a small overlapping area between (Figure 1). In theory, this can nearly double the size of a parts that can be galvanized when designing in modules or sub-units to accommodate the kettle dimensions cannot be achieved.

In practice, the ability to progressive dip depends on multiple variables. To simplify the calculations, the maximum progressive dipping length is most easily calculated by modeling the article as a solid box (Figure 2).
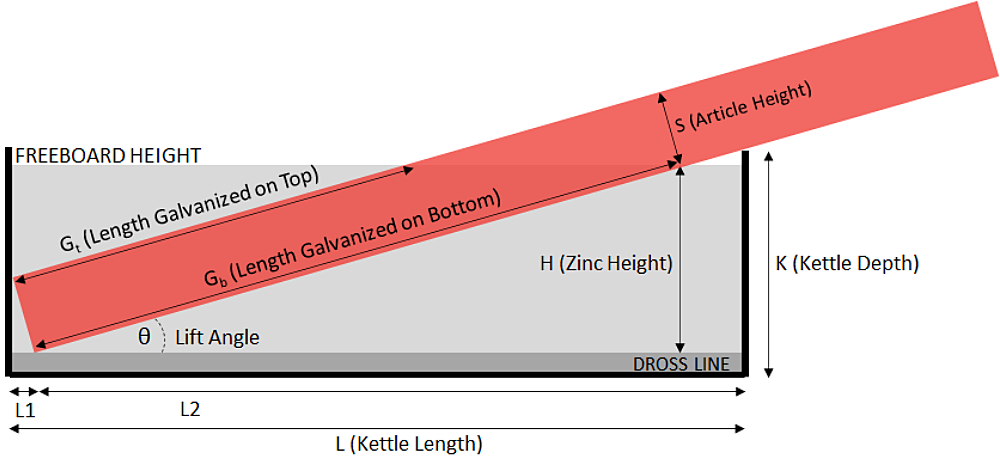
Therefore, to determine the maximum article size that can be galvanized by the progressive dip method, you will need to know or approximate:
- Part Dimensions (Length X Width X Height)
- Kettle Dimensions (Length X Width X Depth)
- Height of the dross from the kettle floor
- Freeboard height or the distance between top of the zinc and top of the kettle walls
The model is used to calculate both the maximum part size that can be progressive dipped, but can also be used to confirm whether an article of a particular size can be progressively dipped successfully or not. To assist you with these checks and calculations, the AGA has two resources available: the AGA Progressive Dip Charts and the AGA Progressive Dip Calculator.
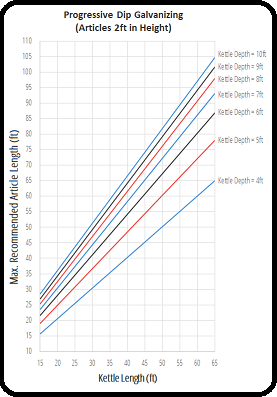
AGA Progressive Dip Charts
The AGA Progressive Dip Charts are available to estimate the maximum article length which can be galvanized if the article height and galvanizing kettle dimensions are known. These charts already assume the article width is less than the kettle width and that 1 ft of the kettle depth is unused to avoid disturbing the bottom dross area and account for any small gap between the zinc height and kettle height.
There are four charts which provide the output of maximum article length for articles of 1 ft, 2 ft, 3 ft, or 4 ft in height when considering a range of typical galvanizing kettle lengths and depths.
Note: Even if the article can be progressive dipped, the maximum height of articles above the bath, available rigging height, and maximum crane capacity varies widely by galvanizing plant and should be confirmed directly with the galvanizer ahead of time.
For examples demonstrating how to use the AGA Progressive Dip Charts, please refer to Dr. Galv "How Do I Use the AGA Progressive Dip Charts?"
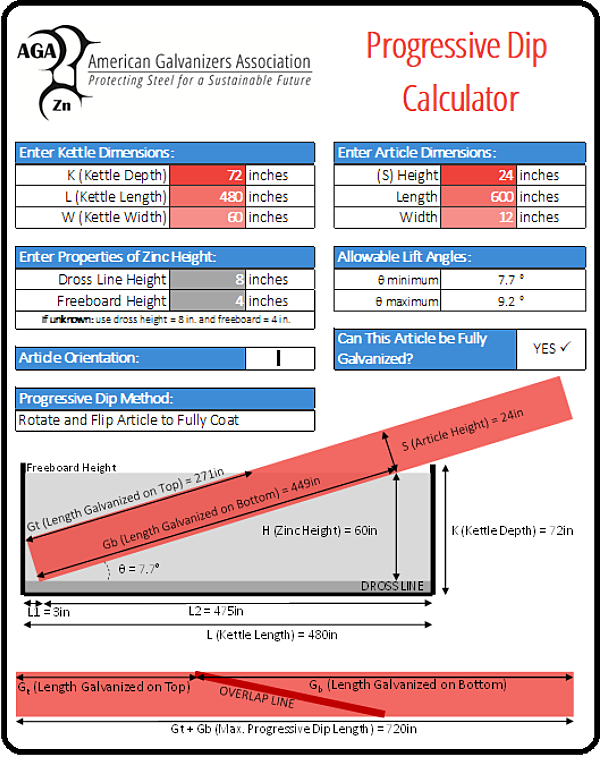
AGA Progressive Dip Calculator
The AGA Progressive Dip Calculator is available to check whether an article of specific dimensions can be hot-dip galvanized within a known galvanizing kettle size. This calculator will not only inform you whether the article can be progressive dipped successfully in the galvanizing kettle, it will also provide:
- Minimum and maximum rigging angles for successful galvanizing
- Successful article orientation, or whether rotating the article (W and H) affects galvanizing success.
- A visual 2D model of the progressive dip method labeled with the outputs from the calculator.
Note: Even if the article can be progressive dipped, the maximum height of articles above the bath, available rigging height, and maximum crane capacity varies widely by galvanizing plant and should be confirmed directly with the galvanizer ahead of time.
For examples demonstrating how to use the AGA Progressive Dip Charts, please refer to Dr. Galv "How Do I Use the AGA Progressive Dip Calculator?"
Please reach out to the AGA if you are interested in seeing the progressive dip calculator be developed into a smartphone application. An application would allow you the added benefit of visualizing the actual part within the bath using a 3D model.
Related Articles:
© 2025 American Galvanizers Association. The material provided herein has been developed to provide accurate and authoritative information about after-fabrication hot-dip galvanized steel. This material provides general information only and is not intended as a substitute for competent professional examination and verification as to suitability and applicability. The information provided herein is not intended as a representation or warranty on the part of the AGA. Anyone making use of this information assumes all liability arising from such use.