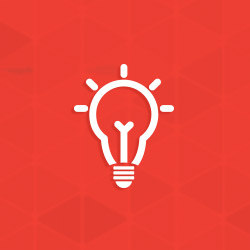
HDG Industry Specification Updates
2024 HDG Specification Updates
ASTM A123/A123M, Specification for Zinc (Hot-Dip Galvanized) Coatings on Iron and Steel Products
This specification revision includes minimum average coating thickness requirements for forgings and castings, a definition for "intended use," a new appendix clarifying common questions regarding the interpretation of Table 1, and new notes to address practical considerations when masking, re-galvanizing, or specifying elevated aesthetics. A detailed summary including background information and rationale are available from the AGA Knowledgebase: 2024 Revision of ASTM A123.
ASTM A384/A384M, Practice for Safeguarding Against Warpage and Distortion During Hot-Dip Galvanizing of Steel Assemblies
This revision includes minor revisions for clarity and introduces the term “progressive dipping”. In paragraph 3.1, the responsible party for reworking sheets susceptible to warpage/distortion was found to be unclear and additional verbiage is proposed to clarify responsibility. Additionally, Paragraph 4.5 is reworded to clarify what is being recommended regarding the hot-dip galvanizing of panel assemblies (sheet pre-welded to frame). The intention is to avoid progressive dipping of such assemblies. If needed, it is possible to galvanize the frame and sheet separately and then assemble the panel sometime after the sheet has been flattened out after galvanizing.
ASTM A767/A767M, Specification for Zinc-Coated (Galvanized) Steel Bars for Concrete Reinforcement
This revision includes minor edits in Paragraph 7 on Finish & Adherence to avoid conflating of the adherence of the initial coating with the performance of the coating during any subsequent fabrication activities by the user. This revision does not change existing requirements, but the information is re-organized to make the requirements easier to understand.
2023 HDG Specification Updates
ASTM A153/A153M, Standard Specification for Zinc Coating (Hot-Dip) on Iron and Steel Hardware
A revision to Note 6 was published in 2023 to address the acceptance of parts susceptible to residual buildup of zinc (e.g. 90 degree elbows or tees). This is relevant for projects where the number of test articles for inspection is very small compared to the lot size. The change informs a specifier that, statistically speaking, it is possible to run into a few unusable parts or outliers even if the lot passes and galvanizing best practices are followed.
NOTE 6—Since this specification is applicable to items that are centrifuged or otherwise handled to remove excess bath metal (see 1.2), irregular coating distribution is not normally encountered. Drainage problems not related to part design, which manifest themselves as local excess coating thickness that would interfere with function or as edge tears or spikes that present a safety hazard because of their sharpness, are grounds for rejection under the terms of 5.1. On part geometries with cavities and recesses, a buildup of zinc may result. Responsibility for remediation of these parts should be agreed to between the galvanizer and the customer.
ASTM B6/B6M, Standard Specification for Zinc
Regarding the purchasing of zinc slabs, Paragraph 7.1 was revised for consistency with the subsequent section 7.2 regarding the purchasing of jumbos/blocks. This does not result in any practical change to the range of slab shape/weights, but avoids the need to revise two standards (B6 and B897) should there be any weight variations in the future. See revised Paragraph 7.1:
7.1 Zinc metal may be ordered in slab, as specified in Specification B897.
AASHTO/NSBA S8.3, Hot-Dip Galvanizing
AASHTO/NSBA S8.3, Hot-Dip Galvanizing, was approved in 2022 and published in 2023. This new guide specification was jointly developed by the American Association of State Highway and Transportation Officials (AASHTO) Committee on Bridges and Structures (COBS) and the National Steel Bridge Alliance (NSBA) Task Group 8 on Coatings. It is intended for adoption by DOTs/owners for hot-dip galvanizing bridges and other highway structures after fabrication using the batch process. AGA and several of our members were involved in the development of this standard over several years. While this specification contains some elevated requirements for bridge projects, a large portion of the specification is non-mandatory commentary regarding design and fabrication best practices to address needs specific to bridge/highway fabrications.
The AASHTO/National Steel Bridge Alliance (NSBA) Collaboration publishes all standards for free download on the NSBA website.
AGA published a more detailed overview of AASHTO/NSBA S8.3 in July 2023:
AASHTO/NSBA S8.3 vs. ASTM A123
AASHTO M 111M/M 111, Standard Specification for Zinc (Hot-Dip Galvanized) Coatings on Iron and Steel Products
This standard was updated to reflect the 2017 revision of ASTM A123. Additionally, M111 now contains an additional requirement to meet the standard SSPC-SP 8, Pickling. This standard is intended for acid pickling to be performed immediately prior to painting (not hot-dip galvanizing). Further, it is unnecessary for the acid pickling process at a galvanizing plant to be held to the requirements of SSPC-SP 8. See additional information from AGA explaining why the SSPC-SP 8, Pickling requirement should be waived. M111 is available for purchase from the AASHTO store.
AASHTO M 232M/M 232, Standard Specification for Zinc Coating (Hot-Dip) on Iron and Steel Hardware
This standard was re-approved without changes and reflects the 2016a revision of ASTM A153/A153M. M232 is available for purchase from the AASHTO store.
AASHTO M 180, Standard Specification for Steel Components for Highway Guardrail
This standard has a title change and was revised extensively as a result of proposed changes from NCHRP Project 22-40 and associated Report 1020: Investigation of Material Requirements for Highway Guardrail Systems. Sheet steel components galvanized after fabrication shall continue to conform to M111, but now exclude the “one-grade-less” clause of M 111M/M 111, Section 6.1. Additionally, there are a new precautions required in M180 Section 9.1.1.4 (for sheet components) and Section 9.3.2 (for posts) during shipping and storage to minimize the occurrence of wet storage stain. Field-drilled holes no longer require repair of the hot-dip galvanized coating.
New references to specifications for the hot-dip galvanizing of fasteners are included (ASTM F2329 and ASTM F436) and only a small portion of fasteners (rectangular and square washers) may be galvanized in accordance with the requirements of M 232M/M 232. Previously, all bolts, nuts and washers could be hot-dip galvanized according to M 232M/M 232.
2022 HDG Specification Updates
ASTM A385/A385M, Standard Practice for Providing High-Quality Zinc Coatings (Hot-Dip)
ASTM A385 received a substantial number of updates to tackle topics such as steel chemistry, methods to avoid excessively thick coatings, vent hole plugs, and thermally cut edges.
Paragraph 3.2 was expanded to provide awareness to the specifier regarding accuracy and recommended use of MTRs when evaluating the chemical composition of steel for galvanizing using a cast or heat analysis.
Paragraph 3.5 was revised to list available methods to limit coating thickness when galvanizing steels of reactive steel chemistry to address industry concerns regarding thick galvanized coatings and potential for flaking during field handling.
Paragraph 3.7 was revised after several galvanizers expressed concerns regarding the 2017 inclusion of over-pickling in sulfuric as a method to remedy low coating thickness for Al-killed steels. Over-pickling is not considered best practice as it cannot be measured/confirmed and results in poor quality when mixing steel compositions in an assembly. Additionally, the phrasing incentivized the specifier to request over-pickling as opposed to utilizing proper steel selection, while also indicating blasting and over-pickling are equally suitable solutions.
Paragraph 3.7 was also expanded to discuss abrasive blast cleaning before hot-dip galvanizing as a method successfully used to achieve two different outcomes: reducing HDG coating thickness or increasing HDG coating thickness, where the difference in outcome is the result of the initial steel chemistry.
It is well known thermal cutting techniques increase hardness and change diffusion properties of steel, making it very difficult to form a coating of typical quality and aesthetics along the cut edge, particularly among flame cut edges. Paragraph 8 now includes available methods to improve the coating quality of cut edges which are often necessary to achieve a surface condition acceptable for painting, powder coating, or Architecturally Exposed Structural Steel (AESS).
Paragraph 12.5 was added to address the use of zinc and aluminum vent/drain hole plugs as this common practice had never been mentioned in ASTM standards before. Guidance was also developed to address concerns over galvanic corrosion when using aluminum plugs.
ISO 1461, Hot-dip galvanized coatings on fabricated iron and steel articles — Specifications and test methods
Overseas in Europe, our EGGA colleagues have been busy also. ISO 1461 was last updated in 2009 and the 2022 update includes the most extensive set of revisions since the first publication. While primarily used outside North America, AGA members are known to galvanize to this standard for small subsets of customers. The most significant changes for the galvanizer are related to the requirements for ultra-low silicon steels, appearance, and renovations (touch-up and repair). However, it is still the case that galvanizing to A123 will typically lead to a final quality which meets or exceeds ISO 1461.
ASTM D6386/D6386M, Standard Practice for Preparation of Zinc (Hot-Dip Galvanized) Coated Iron and Steel Product and Hardware Surfaces for Painting
A 2022 revision of ASTM D6386, is now available for purchase through ASTM with changes that open up the recommendations for blast media used to prepare HDG surfaces for painting.
The beginning of Paragraph 5.4.1 now states:
5.4.1 Sweep Blasting—Abrasive sweep or brush blasting in accordance with procedures described in SSPC Surface Preparation No. 16, which uses a rapid nozzle movement will roughen the galvanized surface profile. The abrasive material must be chosen with care to provide a stripping action without removing excess zinc layers, removal of up to 25 microns (1 mil) is acceptable. One of the materials that has been used successfully is aluminum/magnesium silicate. Particle size should be in the range of 200 to 500 μm (8 to 20 mils). Other materials that can be used are soft mineral sands with a MOH hardness of five or less, organic media, such as corn cobs or walnut shells, corundum, limestone or cast zinc shot. The use of abrasive media with Mohs hardness 5 or greater or a bulk density over 200 lbs/ft is capable of producing roughened galvanized surfaces with increased peak heights, but additional mitigations may necessary by the blaster to significantly reduce the risk of damage. Depending on the value of hardness for the abrasive medium, blasting pressure may need to be determined for the appropriate nozzle to work-piece distance, geometry of the component, and blasting medium. […]
2020 HDG Specification Updates
ASTM A780/A780M, Practice for Repair of Damaged and Uncoated Areas of Hot-Dip Galvanized Coatings
A new revision of A780 was published in September 2020 to address the surface preparation of bare spots for metallizing repairs where it is impractical to perform abrasive blast cleaning.
According to ASTM A780 and the industry standard on metallizing (SSPC-CS 23.00/AWS C223M/NACE No. 12 Specification for the Application of Thermal Spray Coatings (Metallizing) of Aluminum, Zinc, and Their Alloys and Composites for the Corrosion Protection of Steel), abrasive blast cleaning is the required surface preparation method for the application of zinc metallizing. SSPC-CS 23.00 further clarifies the abrasive blasting standard SSPC-SP 5/NACE No. 1 White Metal, is the required surface cleanliness standard for parts to be placed in immersion service while SSPC-SP 10/NACE No. 2 Near White Metal, is acceptable for all other applications.
Galvanizers asked to perform metallizing repairs at their plant occasionally experience times when a bare spot in the galvanized coating is accessible for repair, but is difficult or impractical to blast clean to the required standard. Where abrasive blast cleaning cannot be reasonably performed, industry research indicates metallizing may also be applied to power tool cleaned surfaces (SSPC-SP 11 Power Tool Cleaning to Bare Metal), but with a potential for reduced adhesion to the steel surface.
The potential for reduced adhesion is related to the difference in surface roughness properties (particularly peak height) achieved using the different cleaning methods. SSPC-CS 23.00 requires the angular anchor profile achieved from blast cleaning to be within 2.5-5.0 mils. Meanwhile, SSPC-SP 11 requires only a minimum surface profile of 1.0 mil with no mention of angularity. A peak height between 1.0-2.5 mils is attributed to lower adhesion values for metallized coatings subject to pull-off adhesion testing, but is acceptable for the purpose of repairing small bare spots in the hot-dip galvanized coating.
To bring ASTM A780 in line with the most recent revision of SSPC-CS 23.00 and to accommodate the use of mechanical cleaning for preparation of metallizing repairs where appropriate, paragraph A3.3 of ASTM A780 in the 2020 revision has been updated with the following language:
A3.3 Where anticipated field service conditions include immersion, blast clean the surface in accordance with SSPC-SP5/NACE No. 1 white metal. For less critical field exposure conditions, clean the surface to bare metal in accordance with SSPC-SP10/NACE No. 2 near white metal, as a minimum. Where abrasive blast cleaning cannot be reasonably performed, it is permissible to mechanically clean the surface in accordance with SSPC-SP 11, Power Tool Cleaning to Bare Metal to achieve a surface condition suitable for metalizing repair with the potential for reduced adhesion.
2017 HDG Specification Updates
ASTM A123/A123M, Specification for Zinc (Hot-Dip Galvanized) Coatings on Iron and Steel Products
Single Fabrication with Multiple Material Categories
ASTM has balloted a few changes to ASTM A123 to add some clarity to the repair requirements, to specifically address the acceptance of skimmings in final inspection, and to reference the specification for continuous galvanized rebar in the scope section. It has always been difficult to describe the area on the galvanized parts that can be repaired through ASTM A780. The proposed change includes new language to further identify the maximum size of an area that can be repaired, as well as a drawing of two areas to be repaired to show in pictorial form the acceptable and rejectable repair areas. The change also includes language to address repairs to galvanized parts in the field where there is no minimum size for areas to be repaired. This change has been approved through the ASTM balloting and a new version of A123 will be published in the next couple of months. The AGA Blue Book of Selected Specifications will not be updated this year but an insert with the changes will be provided in all copies purchased until new AGA books are ordered from ASTM. This is likely about two years away based on current inventory.
The second proposed change to A123 addresses the acceptance or rejection of areas of galvanized skimmings on the surface of the coating. Since the galvanized coating is complete under the skimmings, the presence of skimmings on top of the coating is not cause for rejection. The change goes on to say that for appearance reasons the skimmings can be brushed off the surface or washed off. Some skimmings may need to be ground off the surface making sure to avoid taking off too much zinc so the coating thickness no longer meets the minimum requirement. This change had one negative vote and the ASTM editor reviewed the editorial change and agreed with the change being classified as editorial so the ballot is now passed and will be included in the next revision of A123.
The third proposed change to A123 is to reference in the scope of the specification the newly accepted specification on continuous galvanized rebar, A1094. The reference directs the reader to go to A1094 for requirements specific to reinforcing steel that is galvanized by the continuous process. This change has been approved through the ASTM balloting and a new version of A123 will be published in the next couple of months.
ASTM A385/A385M, Standard Practice for Providing High-Quality Zinc Coatings (Hot-Dip)
Another specification under consideration for language changes is ASTM A385. This is the specification that describes the chemistry of the steel affecting the coating thickness and appearance. This is a tricky subject since the combination of silicon and phosphorus can introduce thick and dull coatings even when both elements are in supposed safe regions. The chemistry of the steel is measured through a sampling of the steel heat reported on a Material Test Report (MTR), and this can also provide questionable evidence for silicon and phosphorus content that can be directly linked to the coating thickness and appearance. The specification change attempts to give more information on the use of MTR values for silicon and phosphorus in anticipating the coating thickness and appearance. Specifiers should not set limits on steel chemistry since even silicon values in the middle of the Sandelin region or beyond silicon content of 0.25% can produce acceptable corrosion protection. This change has been approved through the ASTM balloting and a new version of A385 will be published in the next couple of months.
2015 & 2016 HDG Specification Updates
A123/A123M, Specification for Zinc (Hot-Dip Galvanized) Coatings on Iron and Steel Products
The latest revision to A123 reflects the need within the industry to define the responsibility for preparation of the hot-dip galvanized surface for painting or powder coating. Sections 6.2 and 6.4 were revised to clarify that confirmation should be reached between the galvanizer and the painter as to the responsibility for preparation of the hot-dip galvanized surface for painting or powder coating. Additionally, it is noted painting and powder coating of hot-dip galvanized items (including cleaning, profiling, and outgassing) shall be in accordance with D6386 and D7803, respectively, and shall be the responsibility of the applicator.
Table 1 was also revised to provide consistent formatting and to clarify the steel thickness ranges for each material category by updating the boundary symbols. The table below reflects the changes as they appear in the revised specification.
A153/A153M, Standard Specification for Zinc Coating (Hot-Dip) on Iron and Steel Hardware
The latest revision of A153 includes a number of minor clarifications to the wording of the specification.
A385/A385M, Standard Practice for Providing High-Quality Zinc Coatings (Hot-Dip)
A comment was added to the latest revision of A385 to warn specifiers that hot-dip galvanizing of aluminum-killed steels may result in a thin coating unable to meet the minimum thickness requirements specified within ASTM A123/A123M.
Table 1: Minimum Average Coating Thickness Grade by Material Category (2015) |
||||||
All Specimens Tested, Steel Thickness Range (Measured) in. [mm] |
||||||
Material Category |
<1/16 |
>1/16 to <1/8 |
>1/8 to 3/16 [>3.2 to < 4.8] |
>3/16 to <1/4 |
>1/4 to <5/8 |
>5/8 |
Structural Shapes |
45 |
65 |
75 |
75 |
100 |
100 |
Strip and Bar |
45 |
65 |
75 |
75 |
75 |
100 |
Plate |
45 |
65 |
75 |
75 |
75 |
100 |
Pipe & Tubing |
45 |
45 |
75 |
75 |
75 |
75 |
Wire |
35 |
50 |
60 |
65 |
80 |
80 |
Reinforcing Bar |
-- |
-- |
-- |
-- |
100 |
100 |
2013 HDG Specification Updates
ASTM A123/A123M, Specification for Zinc (Hot-Dip Galvanized) Coatings on Iron and Steel Products
The new changes to A123 are part of the continuing evolution of the specification to accurately depict the outcome of industry practices to produce quality galvanized products and to tweak the language to make it more understandable and objective.
As it appears in the revised specification, the table below reflects new coating grades for plate steel, which is now a separate material category from structural shapes, new coating thicknesses for strip and bar, and a new column for steel thickness of >5/8 (16 mm) for all material categories.
Table 1: Minimum Average Coating Thickness Grade by Material Category (2013) |
||||||
All Specimens Tested, Steel Thickness Range (Measured) in. [mm] |
||||||
Material Category |
<1/16 |
>1/16 to <1/8 |
>1/8 to 3/16 [>3.2 to < 4.8] |
>3/16 to <1/4 |
>1/4 to <5/8 |
>5/8 |
Structural Shapes |
45 |
65 |
75 |
75 |
100 |
100 |
Strip and Bar |
45 |
65 |
75 |
75 |
75 |
100 |
Plate |
45 |
65 |
75 |
75 |
75 |
100 |
Pipe & Tubing |
45 |
45 |
75 |
75 |
75 |
75 |
Wire |
35 |
50 |
60 |
65 |
80 |
80 |
Reinforcing Bar |
-- |
-- |
-- |
-- |
100 |
100 |
The highlight of the changes is plate and strip and bar < 5/8 thick now have a minimum coating grade of 75 which will ease the burden many galvanizers have to meet the specification. This is especially true for those galvanizers processing steel that is aluminum killed, which has very low silicon content and on the other end of the reactive steel spectrum.
If you haven't looked at Table 1 for a while you may also notice a change made in 2012. That change added a reinforcing bar as a material category and was done to address the deficiency of ASTM A767 which did not provide a coating thickness requirement for reinforcing steel used in a weldment with, for example, plate embedments.
The other changes to A123 are simple text changes but significant in that they modify paragraph 7.3 to replace the words test specimens with test articles so the paragraph is in agreement with what is represented in Figure 1 of the specification.
Note: AGA cannot distribute copies of ASTM standards to members or their customers for information or use. Most products produced by a standards organization such as ASTM, ISO, etc. are copyrighted and protected by U.S. and International law. When you download an individual standard or a standards volume, typically there are restrictions on how you can use, share, and distribute the file and its contents. Learn more from AGA about revisions & proper use of galvanizing standards.
© 2025 American Galvanizers Association. The material provided herein has been developed to provide accurate and authoritative information about after-fabrication hot-dip galvanized steel. This material provides general information only and is not intended as a substitute for competent professional examination and verification as to suitability and applicability. The information provided herein is not intended as a representation or warranty on the part of the AGA. Anyone making use of this information assumes all liability arising from such use.