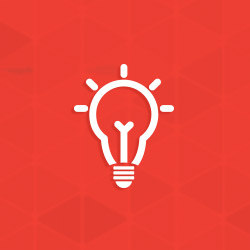
AASHTO/NSBA S8.3 vs. ASTM A123
One of my customers has asked me to galvanize his product according to AASHTO/NSBA S8.3. Is this specification different from ASTM A123? And, if so, what are the differences?
AASHTO/NSBA S8.3 Hot-Dip Galvanizing is a guide specification jointly developed by the American Association of State Highway and Transportation Officials (AASHTO) Committee on Bridges and Structures (COBS) and the National Steel Bridge Alliance (NSBA) Task Group 8 on Coatings. It is intended for adoption by DOTs/owners for hot-dip galvanizing bridges and other highway structures after fabrication using the batch process. AASHTO/NSBA S8.3 contains some additional requirements and commentary which address needs specific to bridge/highway fabrications.
ASTM A123, Standard Specification of Zinc (Hot-Dip Galvanized) Coatings on Iron and Steel Products, is the primary standard in North America for products fabricated and then hot-dip galvanized using the batch process.
AASHTO/NSBA S8.3 contains guide specification language and commentary pertaining to the owner, general contractor, fabricator, galvanizer, and inspector. Therefore, not all requirements and commentary within AASHTO/NSBA S8.3 are applicable to the galvanizer. There are many instances where hot-dip galvanizing in accordance with ASTM A123 and ensuring design and fabrication are in accordance with ASTM A385, A384, and A143 will result in a final product that satisfies the galvanizing requirements of AASHTO/NSBA S8.3. In other instances, the galvanizer, fabricator, general contractor, or inspector may be required or asked to satisfy additional requirements.
The purpose of this article is to give a basic overview of the similarities and differences between AASHTO/NSBA S8.3 and ASTM A123 as they relate to design/fabrication best practices, coating thickness, appearance, repairs, adhesion, and inspection. It is not intended to be used as an exhaustive guide on the differences in terms of inspection requirements or contractual obligations when substituting one specification for the other.
Scope
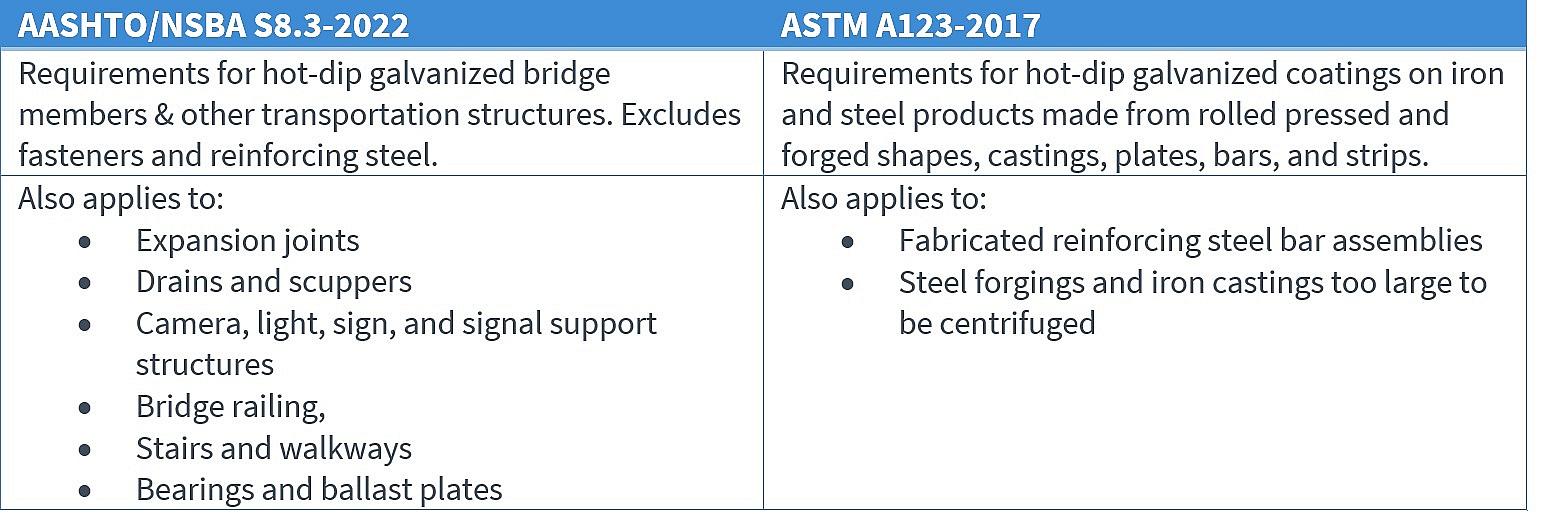
Ordering Information
AASHTO/NSBA S8.3 is similar to A123 in terms of ordering information, and places particular emphasis on communication of project-specific requirements.
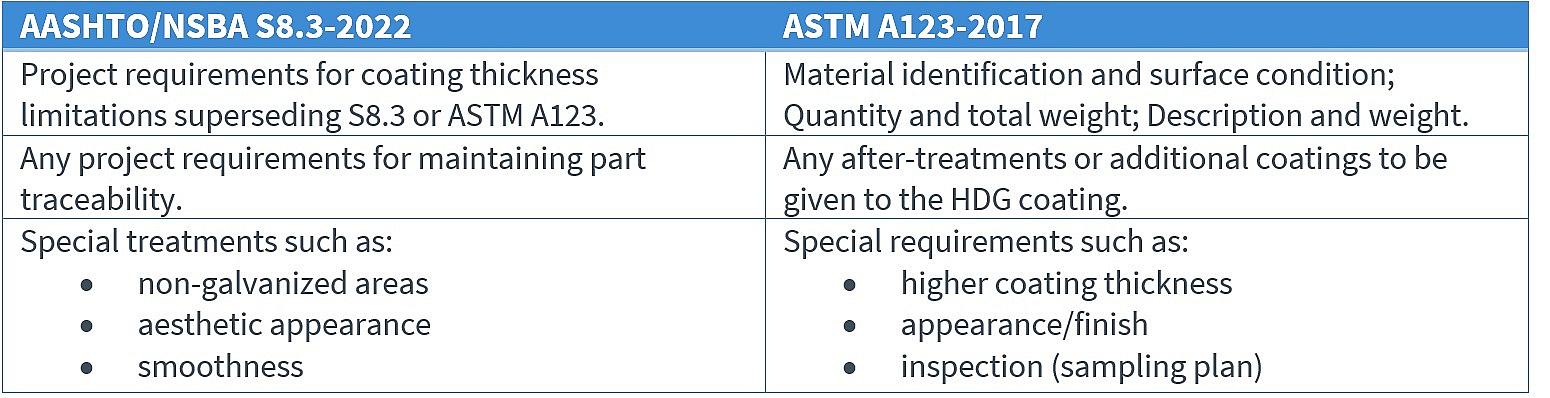
Steel Material Considerations
AASHTO/NSBA S8.3 contains additional requirements on the designer and fabricator for steels to be galvanized which are not mentioned in ASTM A123:
- Do not galvanize steels heat-treated in the temperature range of the galvanizing kettle.
- Avoid galvanizing ASTM A709 HPS 70W and 100W.
- When galvanizing structures composed of weathering steel, preblasting is required.
The AASHTO/NSBA S8.3 specification does not contain requirements related to steel reactivity. However, it recommends practices for managing reactivity of steel be considered. A list of these practices, including practices specific to common bridge steels and bridge fabrications, are provided in the commentary which includes a reference to ASTM A385.
ASTM A123 does not contain requirements related to steel reactivity, but notes there are elements in steel compositions which can influence coating weight and appearance. For guidance on design and fabrication, ASTM A123 states ASTM A385 shall be complied with. ASTM A385 discusses steel compositions and the use of blast cleaning before galvanizing limit coating thickness on reactive steel chemistries, but heat-treated steels and weathering steels are not discussed in ASTM A123 or ASTM A385.
Neither specification requires the purchaser provide Material Test Reports (MTRs) to the galvanizer, but AASHTO/NSBA S8.3 and ASTM A385 both discuss the use of MTRs.
Product Identification
Both AASHTO/NSBA S8.3 and ASTM A385 contain or reference recommended details for satisfactory identifications, but AASHTO/NSBA S8.3 differs in that it prohibits the use of weld marking unless the contract allows.
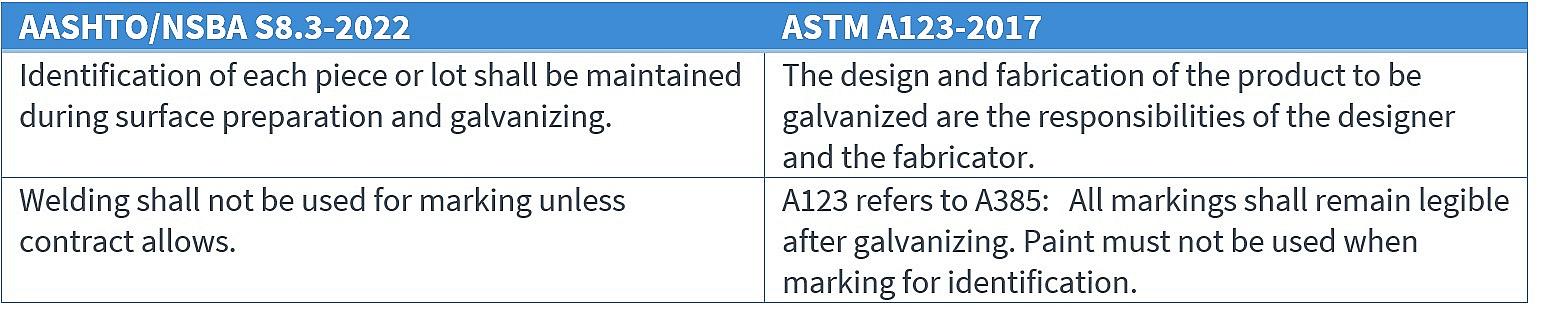
Shop Drawings & Handling
AASHTO/NSBA S8.3 contains a section on “Shop Drawings and Handling” which requires shop drawings include provisions for sufficient vent and drain holes in accordance with ASTM A385. Should the vent and drain holes be inadequate, the fabricator shall contact the owner to coordinate a resolution. AGA resources are referenced in the commentary regarding size and placement of vent and drain holes. Limits on faying surfaces for slip-critical connections are also required to be clearly delineated. To accommodate lifting and handling during galvanizing, any additional holes require approval by the engineer and any temporary welded attachments must follow the requirements of AASHTO/AWS D1.5M/D1.5 Bridge Welding Code.
ASTM A385 similarly requires fabricated assemblies be designed with sufficient vent and drain holes, but ASTM A123 nor ASTM A385 contain requirements for shop drawings or the resolution of inadequate holes. A385 only states it is beneficial to supply the galvanizer with shop drawings before fabrication to determine if additional vent/drain holes, larger holes, or optimized hole designs can be specified relative to the handling orientation. ASTM A123 nor ASTM A385 contain requirements for additional holes or weld attachments used to accommodate lifting and handling during galvanizing.
HDG Coating Properties & Product Details
AASHTO/NSBA S8.3 requires the HDG coating meet the thickness and surface criteria of ASTM A123 with additional requirements regarding inspection and surface finish.
Coating Thickness
During the development of this standard, a concern was raised about the potential for near-zero individual measurements (gage readings) when inspecting to A123. To address this concern, additional requirements were placed on individual measurements (gage readings) and a procedure was developed for investigating and renovating low-thickness areas. This procedure is described in S8.3 Section 6.2.1 and references the dry film thickness (DFT) inspection standard SSPC-PA 2 from AMPP.
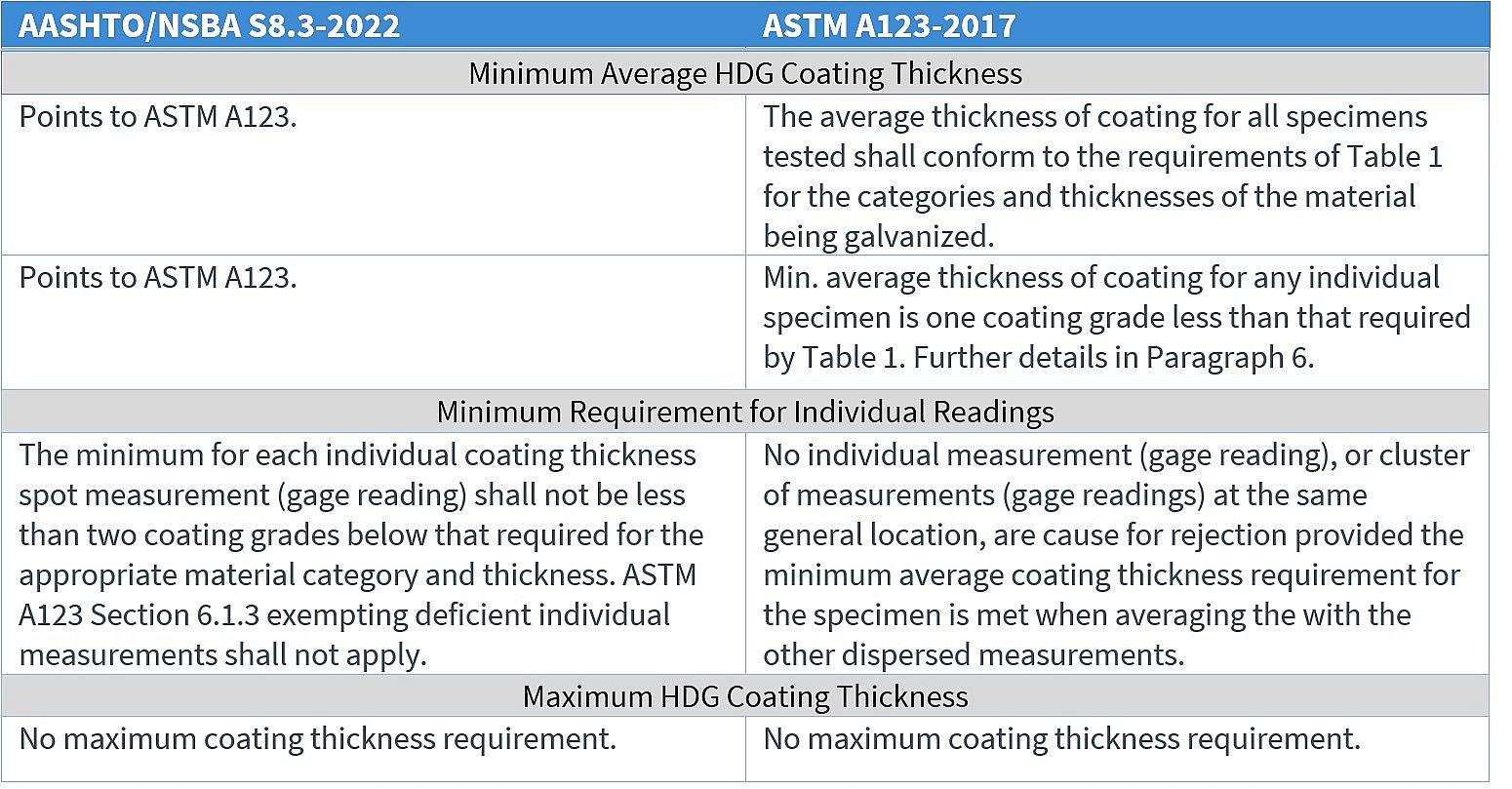
Coating Thickness Inspection of Plate Girders and Rolled Beams
For only I-shaped primary members, AASHTO/NSBA S8.3 contains a sampling plan which differs from ASTM A123. The most obvious difference is the use of four specimens for members longer than 65 ft [20 m] rather than three per ASTM A123. It is also required to give thermally-cut edges a close visual inspection for flaking. The detailed procedure can be found in AASHTO/NSBA S8.3 Section 6.2.3.
Finish
At a minimum, AASHTO/NSBA S8.3 requires exposed galvanized surfaces to meet the requirements of ASTM A123.
When describing AASHTO/NSBA S8.3 defines a term “prominences” which is not found in ASTM A123. Prominences are localized elevated points on a galvanized surface that can be excessive deposits of zinc, or dross or other debris covered by zinc.
There are elevated aesthetic requirements for pedestrian contact areas (subject to direct human contact or close observation) which may require the galvanizer to coordinate vent and drain hole optimization, exercise additional care in handling, perform surface smoothing of prominences, cosmetic touch-ups, or more.
Slip-critical connections are common in bridge fabrications and require firm contact between the plies during high-strength fastener installation and tightening. For this reason, AASHTO/NSBA S8.3 contains requirements for the finish on faying surfaces. ASTM A123 nor ASTM A385 discuss faying surfaces, however, ASTM A123’s “intended use” clause is typically employed to address the presence of prominences or high spots in the coating in the coating that may affect the functional features or fit-up of faying surfaces. With either specification, specifiers should exercise caution when placing sole responsibility for meeting requirements for faying surfaces on the galvanizer. In reality, additional smoothing by the fabricator or erector is sometimes required to further reduce high spots or achieve firm contact.
Adhesion & Embrittlement
In some cases, AASHTO/NSBA S8.3 requires inspection for edge flaking and adhesion testing. During the development of this standard, it was discussed some common bridge fabrications and other transportation structures weld together thick and thin material. This can result in heavier coatings on the thinner material because bridge steels tend to be reactive with respect to hot-dip galvanizing (ASTM A709 allows silicon content up to 0.40% maximum). Examples include thick flanges with thinner web/stiffeners and thick base plates for thinner poles with stiffeners. A coating of 20 mils is not inherently defective but is sometimes associated with the need for additional care during shipping and handling to prevent flaking. Should flaking occur, it is possible to repair at the jobsite and should not continue after installation.
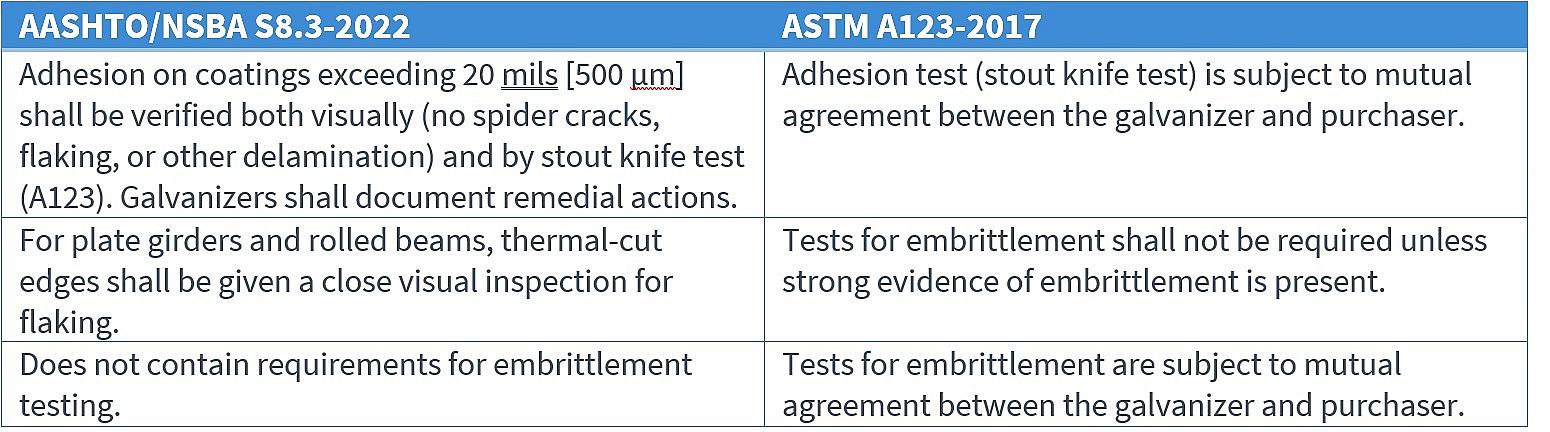
Fabrication, Surface Preparation Before Galvanizing, and Distortion
AASHTO/NSBA S8.3 contains additional requirements and commentary for the fabricator regarding field-applied shear studs, thermally cut edges, copes, sheared edges, progressive dipping, blasting before galvanizing, surface preparation before galvanizing, temporary bracing to minimize distortion, and acceptance criteria for distortion. ASTM A123 does not address these topics, but does reference ASTM A385 for design and fabrication best practices and ASTM A384 for practices to safeguard against distortion.
For the galvanizer, AASHTO/NSBA S8.3 assigns additional responsibility to inspect copes in connection plate and girder webs for cracks after galvanizing.
When assigning responsibility for abrasive blasting of built-up plate girders and rolled beams prior to galvanizing, the specifier should be mindful that not all galvanizing facilities have blasting capabilities. It is recommended this responsibility be subject to mutual agreement between fabricator and galvanizer.
Handling & Storage
Handling and storage are topics outside the scope of ASTM A123. On the other hand, AASHTO/NSBA S8.3 places requirements for handling and storage of galvanized products on the galvanizer, fabricator, and erector. Galvanized products must be stored off the ground and not in standing water. Additionally, any handling must avoid damaging the galvanized coating including raising burrs at lift points.
Duplex Systems
In practice, the requirements of AASHTO/NSBA S8.3 align with ASTM A123. Both reference industry best practices such as preparation of hot-dip galvanized surfaces in accordance with ASTM D6386 for painting and ASTM D7803 for powder coating.
The commentary of AASHTO/NSBA S8.3 recommends the galvanizer be responsible for surface smoothing while further surface preparation be the responsibility of the painter. To avoid a misalignment of expectations, it can be helpful for the galvanizer to be involved in the development and agreement of acceptance criteria for galvanized surfaces after surface smoothing.
With either specification, all parties should also be made aware of AGA’s publications Preparing HDG Steel for Paint and Preparing HDG Steel For Powder Coating.
Quality Management System (QMS)
AASHTO/NSBA S8.3 requires a quality management system. Detailed requirements and a list of items the QMS shall address are provided in Section 11.2. Alternatively, ASTM A123 was developed as a “performance-based” standard where there are requirements regarding final product quality rather than adherence to a specific procedure.

© 2025 American Galvanizers Association. The material provided herein has been developed to provide accurate and authoritative information about after-fabrication hot-dip galvanized steel. This material provides general information only and is not intended as a substitute for competent professional examination and verification as to suitability and applicability. The information provided herein is not intended as a representation or warranty on the part of the AGA. Anyone making use of this information assumes all liability arising from such use.