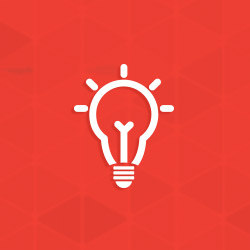
2024 Revision of ASTM A123
What's new in the 2024 Revision of A123?
In summary, this specification revision includes minimum average coating thickness requirements for forgings and castings, a definition for "intended use," a new appendix clarifying common questions regarding the interpretation of Table 1, and new notes to address practical considerations when masking, re-galvanizing, or specifying elevated aesthetics.
For more information on keeping your galvanizing standards up to date, see our Knowledgebase article on Revisions & Proper Use of Galvanizing Standards (Specifications).
Minimum Avg. Coating Thickness for Forgings and Castings
Forgings and castings which cannot be hot-dip galvanized to A153/A153M standard have long been a part of the A123 scope, but the minimum average coating thickness requirements are not provided. The revision to Table 1 includes a new material category to clarify min. avg. coating thickness requirements which are practically achievable for the thickness ranges understood to be hot-dip galvanized to this standard.
Table 1: Minimum Average Coating Thickness Grade by Material Category | ||||||
---|---|---|---|---|---|---|
All Specimens Tested, Steel Thickness Range (Measured) in. [mm] | ||||||
Material Category | <1/16 [<1.6] | >1/16 to <1/8 [>1.6 to <3.2] | >1/8 to 3/16 [>3.2 to < 4.8] | >3/16 to <1/4 [>4.8 to <6.4] | >1/4 to <5/8 [>6.4 to <16.0] | >5/8 [>16.0] |
Structural Shapes | 45 | 65 | 75 | 75 | 100 | 100 |
Strip and Bar | 45 | 65 | 75 | 75 | 75 | 100 |
Plate | 45 | 65 | 75 | 75 | 75 | 100 |
Pipe & Tubing | 45 | 45 | 75 | 75 | 75 | 75 |
Wire | 35 | 50 | 60 | 65 | 80 | 80 |
Reinforcing Bar | -- | -- | -- | -- | 100 | 100 |
Forgings and Castings | -- | -- | -- | 100 | 100 | 100 |
Table 1 and "One Coating Grade Below"
ASTM A123 states the minimum average coating thickness grade for any specimen shall be one coating grade below that required for the appropriate material category and thickness in Table 1.
One of the most common support requests received by subcommittee A05.13 is from specifiers and inspectors requesting clarity on the term “one coating grade below” as it is not clearly defined whether the specifier should consult Table 1 or Table 2 to determine the value. Specifiers attempting to reference Table 1 will find instances where “one coating grade below” incorrectly results in the same value as the required average coating thickness for all specimens tested.
Example: Incorrect interpretation of “one coating grade below” for ¾-inch [measured] plate and 3/16-inch [measured] plate
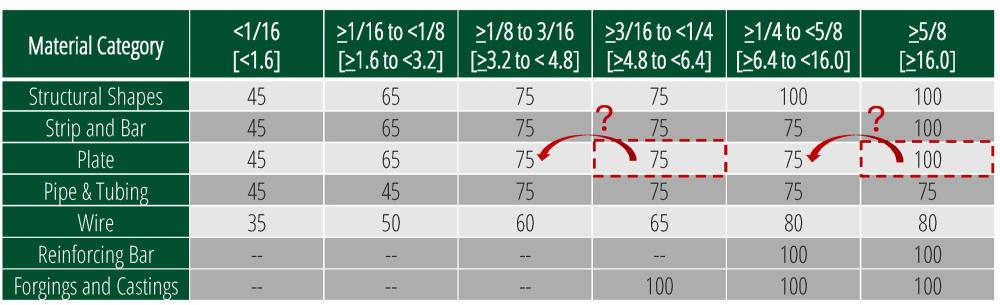
To avoid such confusion in the future, additional verbiage is provided in 4 paragraphs (3.2.11, 6.1, 6.1.1, and 6.1.2) to clarify the value for “one coating grade below “is obtained by consulting the order of thickness grade values listed in Table 2.
Example: One coating grade below grade 100 is grade 85 according to ASTM A123 Table 2.
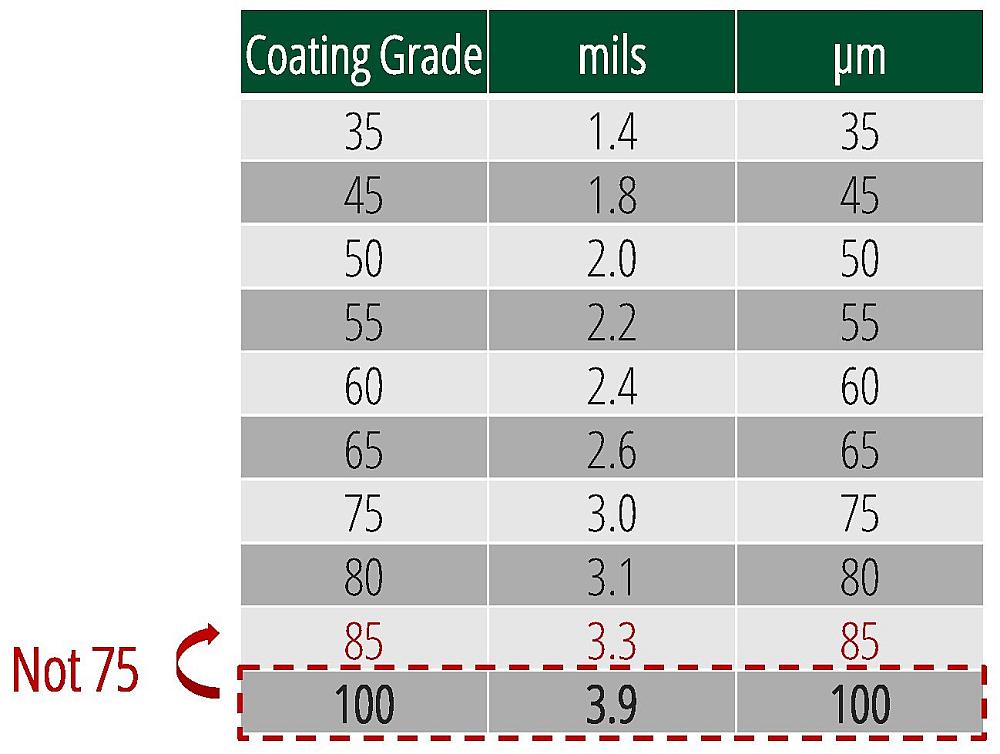
New Appendix: Table 1 & Material Categories
Occasionally, steel products may visually resemble products fabricated from a different type of material or process of manufacture. Examples include utility poles fabricated from plate or beams and angles fabricated from plate. A new appendix provides additional clarity regarding the assignment of material category for such products. Where products are assigned the incorrect material category, the coating thickness grade may sometimes be incorrectly identified.
A123 Appendix X1.1: Examples of material category classifications for common fabrications
- Bar grating belongs to the category “strip and bar”.
- Handrail belongs to the category “pipe and tubing,” etc.
- Poles made from bent plate are not “structural shapes” but belong to the category “plate”.
- Rolled beams belong to the category “structural shapes” while beams fabricated from plate (e.g., plate girders) belong to the category “plate”.
- Rolled angles belong to the category “structural shapes” while angles fabricated from welded plate belong to the category “plate”.
Here is one example where correct identification of the material category results in a lower coating thickness grade when compared to the practice of a visual assignment: A rolled beam with measured steel thickness of ½-inch should be assigned the material category “structural shapes” (Grade 100). A beam made from plate (e.g., plate girder) with measured steel thickness of ½-inch should be assigned the material category “plate” (Grade 75) and not the material category “structural shapes” (Grade 100).
Alternatively, here is a different example where correct identification of the material category results in a higher coating thickness grade when compared to the practice of a visual assignment: Poles (round or bent) fabricated using plate with measured steel thickness of 5/8-inch should be assigned the material category “plate” (Grade 100) and not the material category “Pipe and Tubing” (Grade 75).
New Appendix: Table 1 & Measured Steel Thickness
To determine the minimum average coating thickness requirement in Table 1, measured steel thickness is utilized instead of the nominal steel thickness due to known differences between them which are significant for the hot-dip galvanizing process. However, previous revisions of A123 did not address correct identification of coating thickness grade for products with multiple thicknesses which can be measured (tapered designs, or hot-rolled beams and channels where webs are thinner than flanges). Additionally, in some cases the measured thickness is not always practically available. A new appendix provides additional clarity regarding minimum average coating thickness requirements, requirements when measured thickness is not practically available, and instances when the use of nominal thickness/project drawings may be practical.
A123 Appendix X1.2: Steel Thickness
- Steel thickness is determined using measured steel thickness as stated in Table 1. The use of nominal steel thickness for pipe, tube and plate can sometimes result in incorrect identification of the average coating thickness requirement in 6.1 due to relatively significant differences between the measured and nominal steel thickness.
- If the measured thickness before galvanizing is unavailable or otherwise impractical, one alternative method is to measure the part thickness after galvanizing to closely approximate the steel thickness. For specimens inaccessible for steel thickness measurement, an alternative method is to refer to the nominal steel thickness or dimensions from project drawings to approximate the steel thickness.
- For tapered designs, it is intended the steel thickness measurement is obtained from the location of the thinnest steel section.
- For structural shapes containing variations in steel thickness among flanges, webs, or legs, it is intended the steel thickness measurement is obtained from the location of the thinnest steel section.
- For expanded metal, steel thickness is determined using the measured sheet thickness value.
Intended Use, Duplex Systems and AESS
Interference with intended use is not permitted, but the term “intended use” was not previously defined in A123. The “intended use” clause was originally introduced to require the hot-dip galvanized coating avoid interfering with the objective or function of a product (functional features, required fit-up to other parts, or ability to be painted or powder coated). Surface conditions which are primarily aesthetic in nature do not affect the intended use of the product but may result in confusion over calls for rejection if the product did not “turn out as intended.”
A definition of “intended use” is now provided to clarify “intended use” is different from “intended appearance”:
3.2.5 intended use, n– the objective or function a product is designed to be used for which is not primarily aesthetic in nature. This includes functional features of the product, required fit-up to other parts, or ability to be painted or powder coated.
Additionally, new verbiage related to the intended use clause addresses concerns over the removal of surface conditions which would prevent surfaces from mating properly (e.g. faying surfaces for slip-critical connections):
6.2 Finish– […] Except for local excess coating thickness which would interfere with the use of the product, prevent surfaces from mating properly, or make it dangerous to handle (edge tears or spikes), rejection for nonuniform coating shall be made only for plainly visible excess coating not related to design factors such as holes, joints, or special drainage problems (see Note 6). Since surface smoothness is a relative term, minor roughness that does not interfere with the intended use of the product such as particulates of dross (Fe/Zn solid particles) in the coating that appear like pimples, or roughness that is related to the as-received (un-galvanized) surface condition, steel chemistry, or steel reactivity to zinc shall not be grounds for rejection (see Note 7). […]
There is also a need to clarify how the purchaser can request additional finish/appearance requirements for AESS (Architecturally Exposed Structural Steel), duplex systems (paint or powder coating over hot-dip galvanizing) or other projects requiring elevated aesthetics. A123 now addresses purchaser requests for elevated aesthetic requirements:
6.4.1 Subject to mutual agreement between the galvanizer and the purchaser, the purchaser may establish final appearance criteria for Architecturally Exposed Structural Steel (AESS) or any other project-specific aesthetic requirements beyond the requirements of 6.4. These requirements should be clearly defined using project specifications and communicated to the galvanizer in the purchase order.
Re-galvanizing Parts with Deficiencies Related to Design or Fabrication
The practice of stripping and recoating (re-galvanizing) according to Paragraph 6.2.4 is not known to remedy uncoated areas resulting from deficiencies related to design, detailing, or fabrication which hinder the flow of pretreatment chemicals and/or molten zinc. A new note alerts the specifier of a potential consequence on the coating properties when practices A143/A143M, A384/A384M, and A385 are not complied with in both design and fabrication (see Paragraph 5.2).
Note 9—The practice of stripping and recoating (6.2.4) is unlikely to remedy uncoated areas resulting from deficiencies related to design, detailing, or fabrication as addressed in 5.2.
Variation in Coating Thickness due to Differences in Initial Surface Condition
Under Paragraph 8.2.1, a new note explains the reason for a common inspection concern where variation in coating thickness measurements (both higher or lower) are observed for parts with different initial surface conditions prior to hot-dip galvanizing. Such variations should be considered during inspection to accurately represent the average coating thickness of specimens.
NOTE 13– Specimens containing a mixture of initial surface conditions before galvanizing such as roughness, pitting, cast surfaces, or newly machined surfaces are likely to result in areas of varying coating thickness after galvanizing despite identical steel chemistry. Consider these expected variations when obtaining dispersed measurements to accurately represent the specimen. For example, castings machined to remove extraneous material before galvanizing are likely to experience thinner coatings in the machined area.
Fabrications Containing Multiple Steel Compositions
In the marketplace, it is common for the galvanizer to receive requests from the purchaser to limit coating thickness on reactive steels by reducing immersion times in the galvanizing kettle. As immersion time is only one of many variables that influence the final coating thickness, this practice is not known to guarantee the desired result. Additionally, the potential effectiveness of this strategy is further reduced when fabrications contain a mixture of reactive and non-reactive steels, or if the geometry, vent/drain holes, and orientation of the part do not allow for effective immersion and withdrawal from the galvanizing kettle.
A new note alerts the specifier of the possibility for insufficient coating thickness on non-reactive steel compositions when galvanizing fabrications containing a mixture of steel compositions within the same material category and thickness range. A reference to ASTM A385 is provided where additional background information is available.
NOTE 14–Fabrications containing a mixture of steel compositions within the same material category and thickness range can present a challenge in developing a galvanized coating that meets the thickness requirements of 6.1 for steels of a non-reactive composition when attempting to avoid excessively thick coatings on steels with a reactive steel composition. In these cases, the galvanizer and the purchaser should agree on a plan of action. Practice A385/385M provides guidance on steel selection and discusses the effects of various elements in steel compositions (for example, silicon), that influence coating thickness.
Masking
Masking is a common practice used to treat a portion of the steel surface so the area remains ungalvanized. It is now defined in A123 so common questions about the impact on inspection can be addressed:
3.2.6 masking, n– the practice of treating a portion of the steel surface with a material not removable by chemical cleaning during the galvanizing process to achieve purposely ungalvanized areas.
Regarding inspection, additional language clarifies the calculation of max area subject to renovation. Masked areas cannot be considered “accessible surface area to be hot-dip galvanized” and therefore should be excluded from the surface area calculation:
6.2 Finish– […] Surface conditions resulting from the practice of masking shall not be grounds for rejection and are not subject to the requirements of Section 6. The use of masking materials and responsibilities for masking material application and removal shall be subject to mutual agreement between the galvanizer and the purchaser.
NOTE 6—Areas with masking applied before galvanizing are not considered accessible surface areas to be hot-dip galvanized.
Practical impacts are demonstrated with the following example: on a beam with masking on top of one flange, previously that masked area would be counted when determining maximum area allowable for renovation using the formulas in 6.2.2 (e.g. total bare area should not exceed 0.5% of accessible area). Alternatively, for parts where the other calculation is the limiting factor (e.g. total bare area should also not exceed 36 in2 per short ton), less bare area will be allowed for repair at the HDG facility and this becomes more significant for the galvanizer to consider on parts containing large areas of masking.
Related Articles:
© 2025 American Galvanizers Association. The material provided herein has been developed to provide accurate and authoritative information about after-fabrication hot-dip galvanized steel. This material provides general information only and is not intended as a substitute for competent professional examination and verification as to suitability and applicability. The information provided herein is not intended as a representation or warranty on the part of the AGA. Anyone making use of this information assumes all liability arising from such use.