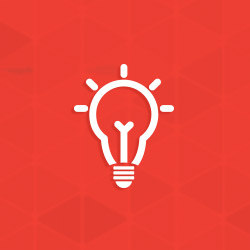
Thick Coatings and Added Cost
Am I (customer) being charged for thick coatings? Why do I keep getting thick coatings from the galvanizer– are they trying to inflate the total selling price by putting more zinc on the steel?
This is a question the AGA receives from time to time over concerns related the thickness of the hot-dip galvanized coating. Although sometimes a thick coating can be desired to achieve greater longevity of the hot-dip galvanized coating, other times an excessive coating thickness potentially results in issues related to fit-up between parts, appearance concerns, or flaking of the coating.
However, it is not true that galvanizers provide thick coatings in an attempt to charge more for their services on a per-pound basis. Zinc is the largest material cost factor in the hot-dip galvanizing process, and thick coatings result in lower profit margins. If we look at the cost of zinc used in the hot-dip galvanizing process, it is possible to see the impact zinc prices and thick coatings have on the galvanizer’s bottom line.
Prices of zinc over the last year (USD):
- 52-week low: $1.04/lb
- 52-week high: $1.64/lb
- Current: $1.19/lb
Galvanizers charge for their services by weighing the part after it has been galvanized, and this results in pricing anywhere from $0.20 to $0.50 (USD) per pound of finished weight. This pricing information is general to the industry in North America and based on survey data obtained from AGA galvanizing members. Though an increase in coating thickness adds extra weight (and therefore cost) to the final product, the zinc prices referenced above mean the galvanizer actually loses $0.69 to $0.99 for each additional pound of zinc on a part which is beyond the minimum needed to meet the specification requirements. This explains why it is not in the galvanizer’s best interest (financial or otherwise) to provide excessively thick coatings. Instead, the galvanizer’s profit margins increase when the minimum average coating thickness is met while overall zinc consumption is minimized.
Then why does the galvanizer occasionally provide thick coatings when it is not desired by either the galvanizer or the customer? The primary challenge occurs when the customer provides the following types of steels or steel assemblies that make limiting the coating thickness very difficult. The list below contains links to additional Dr. Galv articles explaining why these conditions may result in thick coatings:
- The use of reactive steels containing silicon and phosphorus content beyond recommended levels (including weathering steel)
- The combination of thick and thin materials in the same assembly
- The combination of steels with different steel chemistries and/or initial surface conditions
- Assemblies with poor venting and drainage designs
- Thick steels (1 inch thickness or greater)
When specifying these steels or assembly types, there are some methods the galvanizer can employ to try and limit the coating thickness. It is important to note not all of these methods may be applicable to a project, and a thinner coating is never guaranteed:
- Reduce immersion time
- Request the customer blast clean the parts before hot-dip galvanizing
- Move/agitate the part as much as possible while immersed in the bath
- Increase immersion rate and decrease withdrawal rate from the zinc bath (effectiveness limited by poor venting/drainage design)
- Add elements to the zinc bath known to reduce the surface tension of the zinc and/or reduce reactivity for Sandelin Steels with 0.04 – 0.15 % Si content (impractical to change existing bath chemistry for one customer)
- Lower the bath temperature (often impractical)
In order for these methods to be used successfully, steel chemistry and/or assembly make-up should be provided to the galvanizer ahead of time in order to evaluate the steel chemistry, review the overall design, and then determine which measures are appropriate to limit the coating thickness.
To avoid future concerns about thick coatings and pricing in the future, direct communication with the galvanizer is critical to ensure a successful combination of design, fabrication, and galvanizing practices are employed. These practices help ensure your expectations are met regarding cost, fit-up, appearance, and overall quality.
© 2025 American Galvanizers Association. The material provided herein has been developed to provide accurate and authoritative information about after-fabrication hot-dip galvanized steel. This material provides general information only and is not intended as a substitute for competent professional examination and verification as to suitability and applicability. The information provided herein is not intended as a representation or warranty on the part of the AGA. Anyone making use of this information assumes all liability arising from such use.