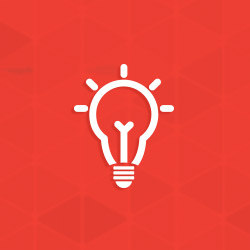
HDG for Waterparks, Pools, and Aquatic Facilities
Is HDG Suitable for Pool and Waterpark Projects?
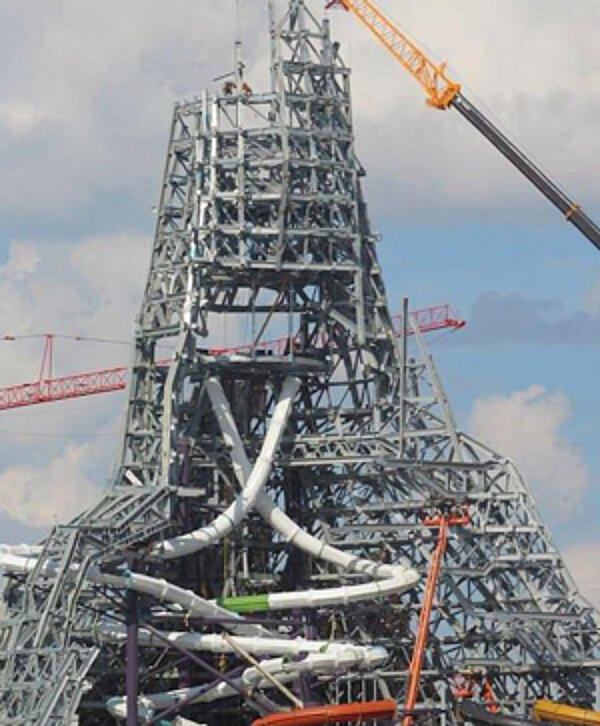
Waterparks, pools and aquatic facilities are constantly assaulted by the corrosive effects of water and treatment chemicals. Since these structures are often enjoyed by hundreds, thousands or millions of people per year, employing an appropriate method of corrosion protection is a critical step in protecting visitors from deterioration while maintaining aesthetic appeal. Although the presence of chlorinated water can present an aggressive environment for hot-dip galvanizing (HDG), there are ways to successfully specify HDG for the protection of many structural and ornamental components.
The suitability of hot-dip galvanizing should always be evaluated on a project-by-project basis for waterparks and aquatic facilities. However, when appropriately specified, hot-dip galvanizing and/or a duplex system (painting or powder coating over HDG) can offer an affordable method of corrosion protection that delivers safety and protects the stability of these facilities while maintaining their exciting visual appearance for years to come.
Hot-dip galvanized waterparks
Hot-dip galvanizing has been used successfully in the waterpark industry for many unique and high visibility projects over the years. For these projects, it is possible to hot-dip galvanize decorative components as well as support structures, canopies, stairways, and handrails. These hot-dip galvanized support structures and stairwells allow the visitors in the park to rest easy as they can visually confirm the safety and stability of the park rides. Where other corrosion protection methods have left water park attractions in need of repair within only a year, hot-dip galvanizing and duplex systems can demonstrate maintenance-free protection for many seasons.
In fact, new waterpark projects continue to be specified as a result of hot-dip galvanizings demonstrated longevity in this type of application. In 2017, the Universal Studios design team specified hot-dip galvanizing for the enclosure and total support structure of Krakatau Volcano, the centerpiece for the highly anticipated Volcano Bay attraction (Figure 1). This decision was largely based on positive experiences with galvanizings maintenance-free service on previous waterpark projects throughout the park. By selecting hot-dip galvanizing, Universal Studios will ensure Krakatau Volcano will be enjoyed by Floridians and the millions of tourists who visit Orlando's theme park annually.
Although hot-dip galvanizing can demonstrate suitable longevity for many waterpark projects, it is important to note direct exposure to pool water is still an aggressive environment for HDG. Regular splashing from chlorinated water could potentially result in the additional buildup of white corrosion products (zinc chlorides) on the hot-dip galvanized surface. However, regular rinsing and drying in combination with seasonal use will result in only a moderate effect on the corrosion rate. For other projects where significant longevity or additional protection from chlorine exposure is required, it can be practical to specify a duplex system. A duplex system can provide maintenance-free corrosion protection for 1.5+ times the sum of the paint life and galvanizing life for waterpark projects. However, practically it is expected maintenance will be performed at periods of 10 years or less to maintain the paint coating for aesthetic reasons. If routine maintenance is performed on the paint or powder coating system, the overall coating system will last indefinitely because the galvanizing will never become exposed to the environment.
While duplex systems can provide an additional layer of protection in the pool water environment, they also allow for the colorful and exciting appearance expected from a waterpark. Depending on the look the owner is trying to achieve, steel components can be themed based on the subject matter of the park or ride. For example, many of the rides at Six Flags Hurricane Harbor in Los Angeles, CA (2006) include duplexed vertical components which were hand painted over the powder coating to look like the trunk of decorative palm trees (Figure 2).
Additional examples of successful waterpark projects are available within the AGA Project Gallery:
- Tommy Garrott Aquatics Facility
- Knotts Berry Farm Water Park
- King George Water Park
- Calipso Water Park
- Hawaiian Falls Roanoke
- ZOOMbabwe Slide
- H2OBX Outer Banks Waterpark
Pool Water Immersion
The use of hot-dip galvanized steel immersed within pool water (e.g. partially or fully immersed handrail or walls) is not a typical application for the hot-dip galvanized coating. Given the high levels of chlorine in the water, a very high rate of corrosion might be expected for hot-dip galvanized steel inside the pool water. The expected lifetime or corrosion rate for hot-dip galvanized products in pool water cannot ever be exactly predicted, as the chlorine level, temperature and water hardness of the pool will fluctuate over time. However, the coating can be expected to perform anywhere from a few months to a few years.
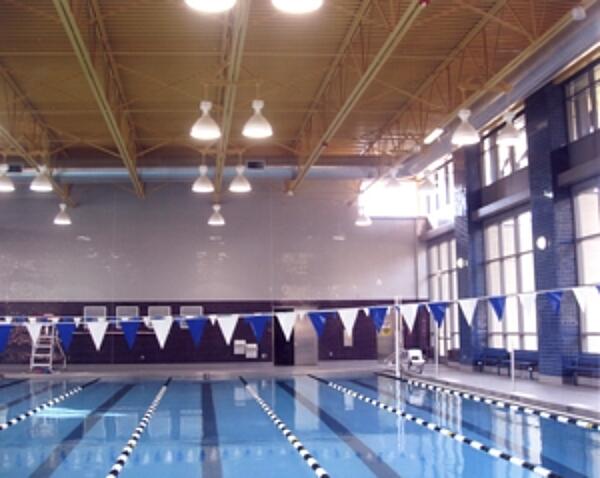
Indoor Pools and Aquatic Buildings
According to International Organization for Standardization guidelines for categorizing atmospheric environments, indoor pools and aquatic buildings are categorized as a C4 environment, similar to coastal areas with moderate salinity or industrial environments. Despite the highly corrosive atmosphere, hot-dip galvanized structural steel has demonstrated good performance when used indoors above both chlorine and saltwater pools. Though often a humid environment, hot-dip galvanizing can provide suitable protection to columns, roofing beams, joists and miscellaneous steel around the pool area since direct exposure to chlorine is minimized. Where structural steel components within an aquatic building are hidden (e.g. behind a suspended ceiling), hot-dip galvanizing alone is often suitable for long term corrosion protection. However, a duplex system is recommended for increased longevity of any visible steel components.
North Arundel Aquatic Center in Glen Burnie, MD (Figure 3) is an example where hot-dip galvanized steel has certainly demonstrated longevity positioned above pool water in an indoor facility. In 2006, the roof structure and various columns were duplexed specifically to protect the building from corrosion while complimenting the primary colors of the indoor playground, staircases and slides. As a result, the aquatic center has been a great source of leisurely entertainment over the years for the local community.
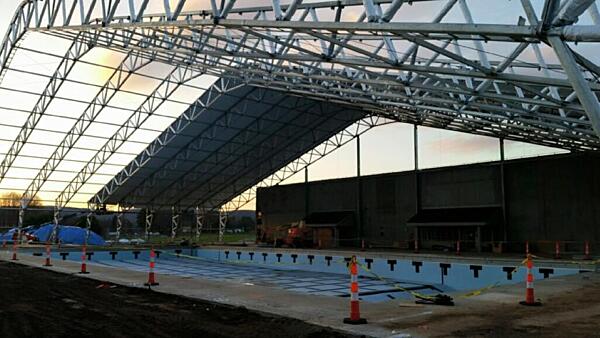
Outdoor pool environment
Hot-dip galvanizing can provide additional benefits for outdoor pool environments. Hot-dip galvanized pool structures are not damaged by UV, have superior abrasion resistance, and can provide maintenance-free protection of structural components. The tension membrane roof skeleton of the Cheshire, CT community pool is one such structure demonstrating protection from the elements. The roof, made of galvanized steel and tensile fabrics, provides shade and protection from corrosion while maintaining the outdoor pools open, airy feel (Figure 4). Positioned above the water, the hot-dip galvanized components are still capable of providing effective corrosion protection since direct contact with chlorine is minimized.
As demonstrated by the specification of HDG for the Northside Swim Center in San Antonio, TX, the coating is also suitable for nearby stairways, handrail, and stadium components around the outdoor pool area (Figure 5). For this swim center, hot-dip galvanizing will provide the durability and longevity required to host spectators year after year at the impressive 50 meter Olympic-size swimming pool and 25 meter diving pool.
AGA Galvanizing Note
For more information on specifying hot-dip galvanizing for various water environments, see AGA Galvanizing Note, HDG Performance in Water Environments. This guideline provides instruction on how to evaluate HDG performance in various water types (seawater, freshwater, brackish water, etc.) as well as how to evaluate performance in specific water-related applications such as above water, splash zones, coastlines, flood zones, and pools/waterparks.
© 2025 American Galvanizers Association. The material provided herein has been developed to provide accurate and authoritative information about after-fabrication hot-dip galvanized steel. This material provides general information only and is not intended as a substitute for competent professional examination and verification as to suitability and applicability. The information provided herein is not intended as a representation or warranty on the part of the AGA. Anyone making use of this information assumes all liability arising from such use.