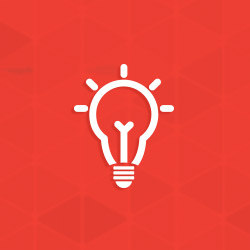
The Performance of Hot-Dip Galvanized Steel in Water Environments
Introduction
The varieties of water throughout the world differ to the extent that predicting the corrosion rate in water environments is one of the more difficult aspects for hot-dip galvanizing applications. Many parameters affect the performance of zinc in water, but despite the difficulty of predicting corrosion rates, hot-dip galvanizing can provide good corrosion protection for a variety of water applications.
The first step in deciding whether hot-dip galvanized steel is suitable for a particular application is to evaluate the properties of the water and determine what type of water will be in contact with the galvanized steel. This Galvanizing Guideline describes a few trends regarding water properties that have a general influence on the corrosion rate of zinc, and then describes the impact of specific water types and applications for additional consideration. Though specific corrosion rates cannot be easily determined for many water applications, each description provides general guidance to determine whether hot-dip galvanizing may be suitable for long term corrosion protection. In addition to this guidance, real world corrosion data is included in the Appendix to cover a wide variety of water types, locations, and water properties.
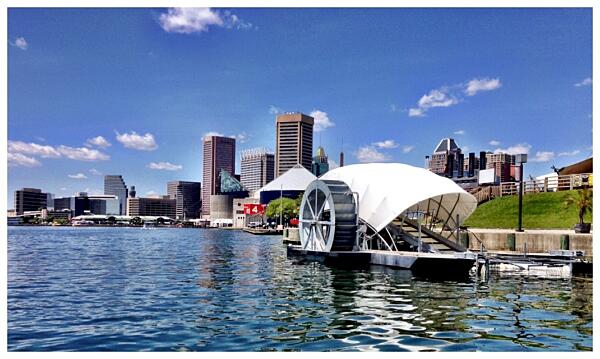
Effect of Water Properties on Corrosion
pH
Zinc corrosion rate in water is lowest in the pH range from 5.5-12. The corrosion rate increases substantially when pH is less than 4 or greater than 12.
Dissolved Gasses & Aeration
The presence of dissolved gases (e.g. oxygen, carbon dioxide) can increase the corrosion rate when distributed nonuniformly as localized attack (pitting) occurs in surface areas that experience lower oxygen content. Corrosion rates of galvanized steel increase significantly with the presence of aeration.
Hardness
In moderately hard waters (60-120 ppm calcium carbonate equivalent) and hard waters (120-180 ppm) containing significant carbonate and bi-carbonate levels, zinc combines with magnesium and calcium ions to form protective scales (zinc carbonate) and provide an insoluble barrier with increased protection against oxygen and chlorides. In general, soft water (< 17 ppm) is much more corrosive to galvanized steel because these protective scales do not form as easily. Soft waters also tend to have greater amounts of dissolved oxygen.
Tidal Zones and Water Agitation
One of the most corrosive areas for galvanized steel is on wash zones and tide lines. Agitation accelerates the corrosion rate of the zinc. Often the washing motion removes the buildup of passive and protective scales from forming on the zinc surface, and instead fresh zinc is constantly re-exposed. This leads to rapid erosion of zinc coating and increased corrosion rates.
Temperature
Generally, the warmer the water, the higher the attack on zinc. In addition, in warm water it is more difficult to develop passive and protective scales on the zinc surface which help to slow corrosion rates.
Flow Rate
Higher flow rates tend to increase the corrosion of zinc because it often means increased abrasion and removal of protective scales which may be attempting to form on the galvanized surface.
Chlorides
Chloride is the most aggressive ion to zinc, especially if present in amounts exceeding 50ppm. This effect is greater in soft waters with low carbonate levels and/or waters where protective scales are unable to form and provide a passive barrier to slow the corrosion rate. A chloride content of 80ppm in soft water causes quite severe corrosion while little-to-no corrosion may occur in hard water with a chloride content of 700ppm.
Hot-dip Galvanizing Resistance to Aqueous Corrosion
Pure Water
Pure water, also known as de-ionized or distilled water, is usually very corrosive to zinc due to the presence of dissolved oxygen and carbon dioxide. Corrosion rates increase with aeration of pure water and can typically range from 0.6-5.9 mils (15-150 µm) per year. The degree of distillation has minimal impact on corrosion rate. Between 120-150°F (5-65°C), corrosion rates can increase with temperature due to the type of corrosion products formed in this specific temperature range.
Natural Freshwater
Freshwater refers to hot and cold domestic, industrial, river, lake and canal waters or any water except sea water. It can be especially difficult to predict the performance of zinc in freshwater because relatively small differences in the properties can produce substantial changes in corrosion rate. Performance is largely influenced by dissolved gases, mineral constituents, organic matter, and microbial life. In some waters with microbial life, aggressive localized attack can occur due to microbial induced corrosion (MIC). However, other factors such as pH, temperature, and motion affect the composition of corrosion products formed on the exposed zinc surface (and thereby the corrosion rate).
In freshwater immersion, alternating wet and dry cycles do not exist since the coating is always wet. This means the zinc patina does not form underwater like it does in atmospheric exposure. Normally this would be cause for concern, but a natural scale of insoluble salts tends to form on the galvanized surface in freshwater of moderate/high water hardness and the ions from these salts combine with zinc to form a protective barrier of calcium carbonate and basic zinc carbonate. Because this protective barrier slows the corrosion rate, immersion in hard water is generally much less corrosive than soft water for freshwater applications. Corrosion rates tend to be higher at the beginning of exposure and decrease with time as the protective scale develops.
For partial immersion in freshwater, agitation from tidal activity accelerates the corrosion rate. The “washing” motion removes the passive scales forming on the galvanized surface, and exposes fresh zinc to redevelop more scales/patina. This leads to rapid erosion of the coating and increased corrosion rates.
Seawater
The biggest determinants to galvanized steel’s performance in seawater are temperature and ion interaction. Seawater temperature varies widely from 28 F (-2 C) at the poles to 95 F (35 C) near the equator. Generally, the corrosion rate of hot-dip galvanizing in tropical seawater is much more corrosive than temperate seawater. The warmer the water, the higher the attack on zinc because reactions between oxygen and zinc happen faster at higher temperatures. Meanwhile, temperate seawaters experience a freeze cycle. In moderate and temperate temperature ranges, zinc forms salts with magnesium and calcium that are not water soluble. These passive compounds form on the surface preventing zinc from reacting with oxygen and chlorides to slow the corrosion rate. Tropical waters tend to remain at or above 70 F (21 C), making it difficult to develop these compounds.
Given the high level of chlorides in sea water, a very high rate of zinc corrosion can be expected. However, the presence of magnesium and calcium ions can have a strong inhibiting effect, especially for temperate waters. Typical corrosion rates are 25 µm (1 mil) per year in tropical seawater and 13 µm (0.5 mil) per year in temperate seas. Corrosion rates can greatly increase for environments involving partial immersion or heavy and direct sea spray.
Seawater splash/tidal zones are the most aggressive environment for hot-dip galvanized steel. The zinc coating reacts with chloride ions in the water, and zinc corrosion products are formed. When these corrosion products dry and are later washed away when the steel is wetted again, more zinc corrosion products form. This process repeats itself until the galvanized coating is consumed. A time to first maintenance of 2-3 years is not uncommon for such applications. Meanwhile, a time to first maintenance of 5+ years or more may be typical for full immersion, depending on the composition and temperature of the seawater.
Brackish Water
The performance of hot-dip galvanizing immersed in brackish waters is difficult to predict as the salt content is often variable over time. Depending on the composition and temperature of the brackish water, a coating lifetime of 2-3 years for partial immersion/splash zones or greater than 5 years for full immersion may be typical. In some applications, hot-dip galvanized steel has experienced no rust after 11 years in brackish water.
Structures Above Water (or Prone to Flooding)
When galvanized steel will not be constantly exposed to water, but resting above it, lower corrosion rates are experienced. More often, corrosion rates are more closely related to atmospheric corrosion rates. Occasional flooding is not likely to significantly impact the performance of the coating unless the water lies stagnant over the galvanized steel for an extended period of time. Rinsing or power washing the structure with fresh water after a flooding event can limit the exposure of the surface to the corrosive salts left from the water.
Potable Water
Galvanized steel is a suitable application for potable water as most potable waters have a pH range from 5-8.5. However, corrosion rates vary depending on the level of impurities. When specifying the use of hot-dip galvanizing for potable water, specifiers should be aware of the U.S. Clean Water Act and the included Drinking Water Standard. This standard requires any material or coating in contact with drinking water to be tested according to NSF Standard 61: Drinking Water Systems Components: Health Effects. As a result, only galvanizers audited and approved by the NSF have the authority to galvanize products for use with potable water. Contact NSF directly to request certification and NSF will arrange an evaluation of the galvanizer if they are not already certified for a specific product and/or end use.
Wastewater & Water Treatment Facilities
Although there have been several cases where hot-dip galvanizing has performed suitably for wastewater clarifiers and wastewater treatment facilities where the coating is in direct contact with the water, this environment is potentially very corrosive. Determining pH, hardness, total dissolved solids, and temperature can assist in determining a general corrosion rate for components in direct contact with the water. However, the nature of wastewater means the water composition is ever changing. This makes predicting the performance of hot-dip galvanizing challenging (if at all possible). It has been experienced that the same design with similar feed waters can have variable performance. Some galvanized coatings perform greater than 10 years while others have failed within only a couple of years. Despite these challenges, hot-dip galvanizing is very suitable to protect ancillary components which are not submerged or in constant contact with the wastewater or treated water.
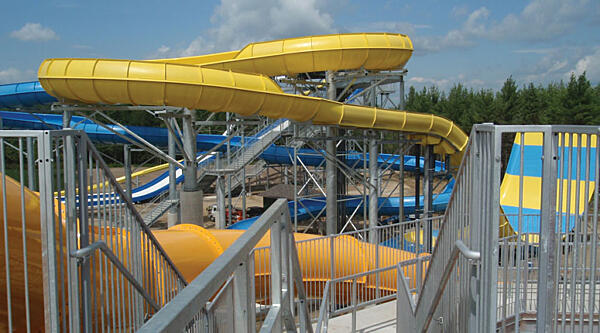
Pools, Waterparks, and Aquatic Facilities
For many chlorinated water projects, hot-dip galvanizing has demonstrated good performance for decorative components as well as support structures, canopies, stairways, and handrails. Though regular splashing from chlorinated water results in the additional buildup of corrosion products (zinc chlorides), regular rinsing and drying in combination with seasonal use results in only a moderate effect on corrosion rate. Where additional protection from chlorine exposure is required, it can be practical to specify a duplex system.
The use of hot-dip galvanized steel immersed in pool water is not a typical application. Given the fluctuating water properties and high levels of chlorine, a high or variable corrosion rate can be expected. The coating may perform anywhere from a few months to a few years. Meanwhile, hot-dip galvanized steel has demonstrated good performance when used indoors above chlorine and saltwater pools. Though often a humid environment, suitable protection is given to columns, roofing beams, joists and other steel around the pool where direct chlorine exposure is minimized. For additional corrosion protection, or where aesthetics are a consideration, a duplex system can be specified.
Hot Water Heaters & Polarity Reversal
Accelerated corrosion from polarity reversal was first discovered when hot water heaters for residential/commercial applications experienced premature failure when hot-dip galvanized. However, the polarity reversal effect must have specific conditions before it happens. The hot-dip galvanized part must be in contact with a water solution, the water solution must contain dissolved oxygen, the water solution must also contain some bicarbonate or nitrate ions, and the temperature of the solution must be in the range between 140-180 F (60-82 C). Only if these conditions are present can the zinc coating experience the polarity reversal.
Duplex System: Extending Time to First Maintenance in Water Environments
The specification of a Duplex System (paint or powder coating over hot-dip galvanizing) is a good option to significantly extend coating life in water environments. Even for highly corrosive locations such as offshore platforms, duplex coatings have been known to protect against rust for 10-20 years where hot-dip galvanizing or paint alone may have only lasted a few years.
Assuming a duplex system is utilized, the coating life can be extended approximately 1.5-2.3*(HDG life + Paint life) due to a property known as the synergistic effect. The 1.5-2.3 range for the duplex-multiplier is dependent on environment. For example, 1.5 is the minimum limit meant for the most corrosive environments with high pollution, salt, or humidity, while 2.3 is appropriate for mild or rural environments. To further assist you, the AGA has established a guide for estimating time to first maintenance of duplex systems to provide more information on the synergistic effect and other beneficial properties of a duplex coating.
Appendix
Corrosion Data for Zinc in Water Environments
References
- Porter, F. C.; Corrosion Resistance of Zinc and Zinc Alloys. Dekker, New York, 523pp. 1994.
- Zhang, Xiaoge Gregory; Corrosion and Electrochemistry of Zinc, Plenum Press, New York . 1996.
- Defrancq, J. N.; Zinc and zinc-lead alloys in domestic water, Br. Corros. J. 17, 125-130, 1982.
- Slunder, C. J., and Boyd, W. K.; Zinc: Its Corrosion Resistance, 2nd ed., International Lead Zinc Research Organization, Inc., New York, 1986.
- E. A. Anderson, C. E. Reinhard and W. D. Hammel; The Corrosion of Zinc in Various Waters, American Water Works Association Vol. 26, No. 1 (JANUARY, 1934), pp. 49-60.
- Gosar, Leon and Drev, Darko; Contact with Chlorinated Water: Selection of the Appropriate Steel, Materials and technology 45 (2011) 6, 639–644
- Craig, A B. and Anderson, D.; Handbook of Corrosion Data, 2nd Edition, ASM International, 1995.
- Siska Prifiharni, Lutviasari Nuraini, Gadang Priyotomo, Sundjono, Hadi Gunawan, and Ibrahim Purawiardi; Corrosion performance of steel and galvanized steel in Karangsong and Limbangan sea water environment, AIP Conference Proceedings 2018 1964:1.
© 2025 American Galvanizers Association. The material provided herein has been developed to provide accurate and authoritative information about after-fabrication hot-dip galvanized steel. This material provides general information only and is not intended as a substitute for competent professional examination and verification as to suitability and applicability. The information provided herein is not intended as a representation or warranty on the part of the AGA. Anyone making use of this information assumes all liability arising from such use.