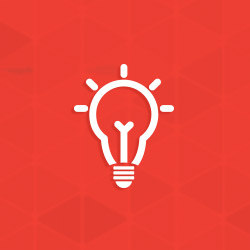
Maximizing HDG Aesthetics for AESS Projects
How can I maximize hot-dip galvanizing (HDG) quality for AESS projects?
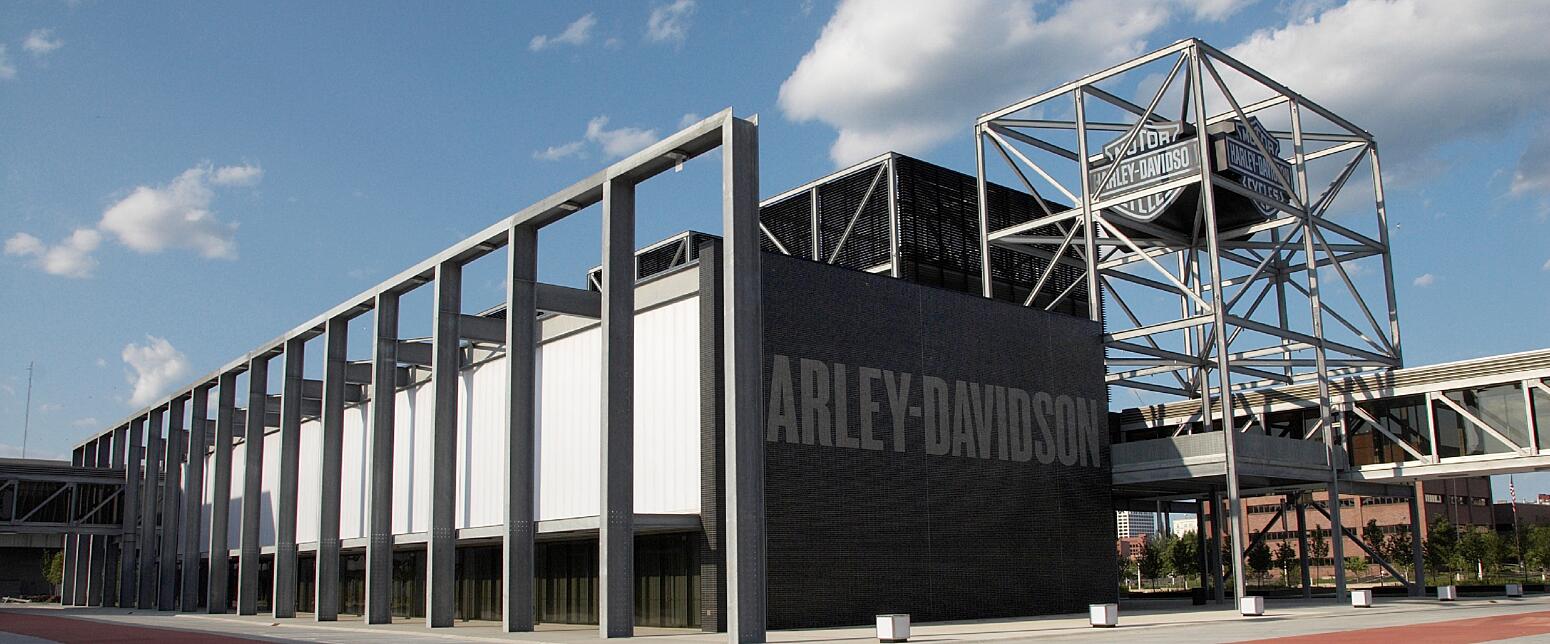
More and more, specifiers are looking to hot-dip galvanize Architecturally Exposed Structural Steel (AESS) to create artful, durable, and sustainable structures for generations to enjoy.
However, there is a common misconception it is not possible to obtain batch hot-dip galvanized (HDG) steel of the quality and aesthetics required for projects involving AESS.
This is because unlike painted or powder coated steel, stainless steel, concrete, or metal plating, the initial appearance of hot-dip galvanized steel is hard to predict for a variety of reasons such as steel chemistry, cooling rate, and stress induced during steel processing. Furthermore, many surface conditions normally acceptable under the primary galvanizing specification ASTM A123 (i.e. runs, skimmings, roughness, excess zinc) may not be acceptable for showcase or feature elements without additional detailing by the galvanizer and/or fabricator. As a result, hot-dip galvanized AESS jobs can sometimes present a challenge for many specifiers looking to achieve a consistent, smooth and uniform galvanized finish within budget.
Despite these challenges, it is certainly possible to achieve high quality coatings when the necessary aesthetic requirements are clearly and directly communicated to all parties prior to fabrication. The following guidelines explain how to apply a new categorical approach to AESS to facilitate communication and minimize the cost premium for achieving galvanized AESS as well as best practices to be performed by the specifier, designer, fabricator and galvanizer to maximize appearance.
AESS: The New Categorical Approach
To assist you in communicating the additional aesthetic requirements for AESS (including requirements above and beyond ASTM A123), the American Institute of Steel Construction (AISC) and Canadian Institute of Steel Construction (CISC) have updated their guidelines for specifying AESS in 2017 and 2011, respectively. These guidelines provide a categorical approach to specifying AESS which can be used to clarify the requirements and establish responsibilities between the architect, general contractor, fabricator, and galvanizer. Both AISC and CISC developed definitions to establish different AESS categories for the steel based on the viewing distance, type/function of the structure, and cost increase to achieve sequentially higher AESS categories:
- AESS 1: Basic elements
- AESS 2: Feature elements viewed at a distance greater than 20 ft (6 m)
- AESS 3: Feature elements viewed at a distance less than 20 ft (6 m)
- AESS 4: Showcase elements with special surface and edge treatment beyond fabrication
- AESS C: Custom elements with characteristics described in the contract documents
A summary of requirements for each AESS category can be found in Table 1. For a detailed description of these AESS categories, refer to each respective guide among the following resources:
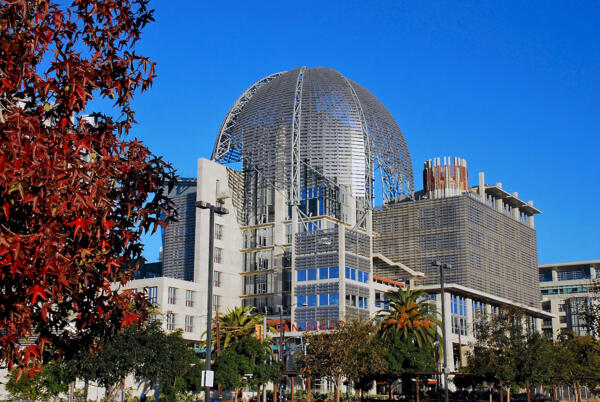
The key takeaway from this categorical approach is AESS categories do not need to be equally applied across a project: AESS 1 or 2 are more suitable for visible framings high up that will not be closely seen by the public/intended user (or will be covered in heavy coatings or fireproofing), while artwork, columns, or showcase elements to be touched and viewed up close may require AESS 3 or 4. This categorical approach allows you to optimize the quality and inspection requirements for various galvanized members of the project, so you can avoid unnecessary and expensive detailing/smoothing where it is not needed. Additionally, this approach can prevent the project from becoming cost prohibitive if the same highest standard was applied in all areas of the project.
Table 1 below outlines the characteristics required of each AESS category with an X and anticipated cost premiums (% overall) for each additional characteristic listed beyond the category requirements. For example, if AESS 2 is specified with the addition of all welds to be contoured and blended, the guidelines inform the specifier they could likely encounter an additional 25-40% cost premium beyond the overall 25-30% premium for AESS 2.
Table 1: AESS Category and Cost Matrix | ||||
---|---|---|---|---|
Category Characteristics | AESS 4 Showcase Elements | AESS 3 Feature Elements <20 ft | AESS 2 Feature Elements >20 ft | AESS 1 Basic Elements |
General Cost Premium | 100-150% | 40-75% | 25-30% | 10-20% |
Steel Surface prep SSPC-SP 6 | X | X | X | X |
Sharp edges ground smooth | X | X | X | X |
Continuous weld appearance | X | X | X | X |
Standard structural bolts | X | X | X | X |
Weld spatters removed | X | X | X | X |
Visual samples | X | X | Optional | +5-25% |
One-half standard fabrication tolerances | X | X | X | +5-15% |
Fabrication marks not apparent | X | X | X | +5-15% |
Welds uniform and smooth | X | X | X | +5-15% |
Mill marks removed | X | X | +5-15% | +5-15% |
Butt and plug welds ground smooth and filled | X | X | +5-10% | +5-10% |
HSS weld seam oriented for reduced visibility | X | X | +1-5% | +1-5% |
Cross-sectional abutting surface aligned | X | X | +5-15% | +5-15% |
Joint gap tolerances minimized | X | X | +5-10% | +5-10% |
All welded connections | Optional | Optional | +15-30% | +15-30% |
HSS seam not apparent | X | +5-20% | +5-20% | +5-20% |
Welds contoured and blended | X | +25-40% | +25-40% | +25-40% |
Surfaces filled and sanded | X | +30-50% | +30-50% | +30-50% |
Weld show-through minimized | X | +5-20% | +5-20% | +5-20% |
Special care in fabrication and erection | X | X | X | X |
Finish: Galvanizing | +20-40% | +20-40% | +20-40% | +20-40% |
The Challenge with Using Galvanized Samples to Demonstrate Aesthetic Quality
You will notice there is a requirement for visual samples to demonstrate the capability of meeting AESS 3 or 4 requirements. Such samples can be useful to determine whether the galvanizer and fabricator are capable of providing a galvanized part with suitable corrosion protection, smoothness, installation tolerances and overall quality. However, it is impractical to expect an aesthetic finish which exactly matches the sample for all the pieces galvanized in a project.
The initial appearance of hot-dip galvanized steel is hard to predict for a variety of reasons, including steel chemistry, cooling rate, and stress induced during steel processing. In fact, it can be common to galvanize identical pieces at the same time which result in different finishes or overall appearance. Regardless of the initial appearance, all galvanized steel parts will take on a uniform matte gray appearance upon exposure to the environment, typically within six months to two years. As the coating is exposed to natural wet/dry cycles after installation it develops a zinc patina with a uniform soft gray appearance, evening out any differences that may have existed originally. When requesting a visual sample, it is important to consider this natural weathering of the coating so that realistic aesthetic criteria are established for the project.
Using the Categorical Approach to Assign Responsibilities Beyond ASTM A123
Although most additional requirements for the AESS categorical approach are related to fabrication, it is important to familiarize yourself with the ASTM A123 hot-dip galvanizing finish and appearance requirements in order to successfully assign responsibility for additional detailing work required to meet the aesthetic characteristics for each AESS category. This is because many surface conditions are typically acceptable under ASTM A123 (roughness, runs, dross, etc.) since they do not affect corrosion protection, but these same conditions may or may not be acceptable for the project in terms of aesthetics.
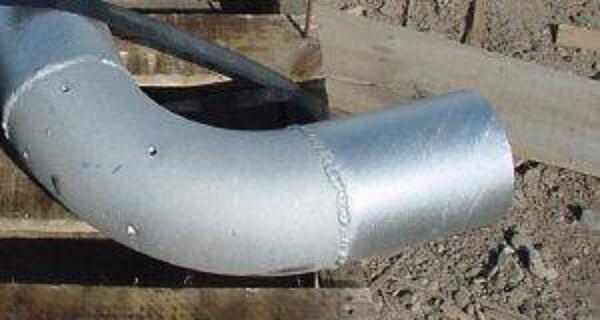
For example, if welds are required to be contoured and blended the fabricator can perform this before HDG, but depending on the chemistry of the weld material a thicker and/or darker HDG coating may be present over weld area after galvanizing. Therefore, additional smoothing after hot-dip galvanizing is often needed to ensure weld contouring and blending in addition to optional use of recommended welding materials or weld material with a chemical composition closer to the base steel.
Another example would be to address the presence of any thermally cut edges. Although the fabricator may perform grinding of sharp edges in cut areas as outlined per AESSS category requirements, this is not often enough to prevent known quality issues related to thin and/or flaking coatings present on thermally cut edges after HDG.
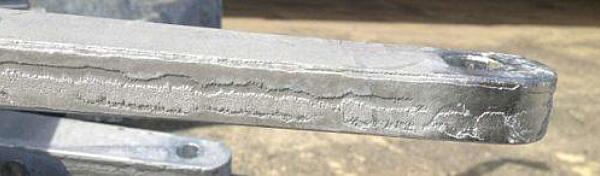
To achieve a high quality finish along thermally cut edges and avoid field repair of the coating, you will need to designate responsibility for ensuring all affected surfaces are ground up to 1/16 inch even though this is not explicitly stated within the AESS category requirement.
If the responsibility for certain detailing steps is left unassigned, the galvanizer and fabricator/general contractor are unlikely to include the significant additional cost for this detailing in their bids, leaving both parties unwilling to take on the additional work. Where there is any discrepancy between A123 requirements and the specified AESS category, explicitly state these requirements during the bid phase and before contract award.
An additional pre-job meeting where the galvanizer, fabricator and general contractor are in attendance is also ideal for clarifying additional responsibilities and pricing related to detailing unaccounted for in the bid phase. The above reasons are why an additional 20-40% markup for galvanizing is listed in Table 1 to potentially bring the hot-dip galvanized coating to the aesthetic requirements of each AESS category.
To learn more about A123 quality and aesthetic requirements, AGA has the following free resources related to the inspection of hot-dip galvanized steel:
- Inspection of Hot-Dip Galvanized Steel Products Publication (also available in Spanish and Canadian French)
- Hot-dip Galvanized Coating Appearance Publication
- Inspection App (available for free in the Apple and Google Play stores)
- AGA Online Inspection Course & Certificate of Completion
- Touch-up and Repair Video Series on YouTube
Maximizing Aesthetics Through Design and Specification
Although the AISC and CISC guidelines attempt to facilitate better communication about requirements in order to maximize aesthetic quality, the overall design of the parts before fabrication is a primary factor driving the final appearance of the galvanized finish. To maximize appearance before fabrication, a good start would be to incorporate any applicable design details listed within ASTM A385, Standard Practice for Providing High-Quality Zinc Coatings (Hot-Dip). However, all parties must keep in mind the recommendations contained within ASTM A385 do not necessarily provide enough recommendations to maximize the aesthetics for AESS, and you may need to implement additional design optimizations to minimize the amount of surface smoothing and filing after galvanizing.
For example, working in direct communication with the galvanizer to optimize placement, quantity, and size of venting/drainage holes in relation to the handling orientation will go a long way to improving the aesthetic appearance. To take it a step further, you may also want to discuss temporary/designated lift points to minimize the appearance of chain and wire marks. Material selection also has a major influence on the HDG coating appearance. Combining steels of different material thickness, steel chemistries or initial surface conditions will result in a mixed appearance after hot-dip galvanizing.

Where unavoidable, materials can be sent to the galvanizer separately in an attempt to match appearance before bolting/welding after galvanizing or abrasive blasting before HDG can be specified to maximize the potential for a uniform appearance.
Designers should also consider the practical limitations of the galvanizing plant it may be difficult to meet AESS quality for large parts that come too close to the height of the bottom dross layer when dipped, or for oversized parts that must be progressively dipped. Where possible, discuss such concerns with the galvanizer directly since kettle dimensions vary.
To assist the designer and specifier, there are many resources and additional specifications available to help avoid common design issues which affect HDG aesthetics:
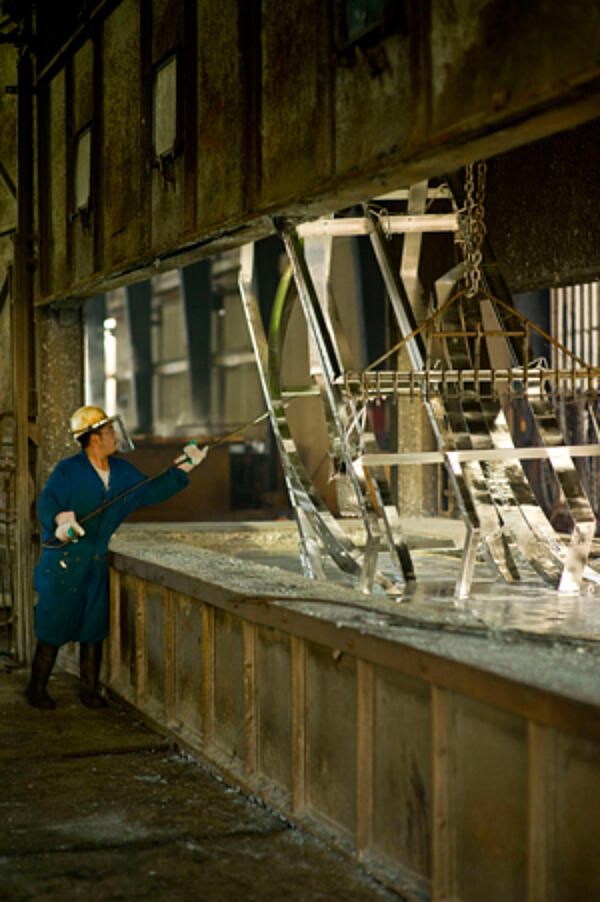
Maximizing Aesthetics Through Process Controls
In addition to optimizing the design for hot-dip galvanizing, there are process controls the galvanizer can implement for AESS projects to minimize the amount of surface smoothing after galvanizing. Specifically, it may be possible for the galvanizer to hang parts at the highest possible angle, keep suspension of the parts above the height of the bottom dross layer, immerse the parts as quickly as possible, minimize dip time and withdraw parts slowly from the bath.
In addition, some galvanizers include elemental additions to the galvanizing bath to improve aesthetics, zinc fluidity and drainage. These process controls are not necessarily applicable or suitable for every project. For example, the aesthetic quality for steels with a chemical composition outside the recommendations for galvanizing may be negligibly affected by many of these process controls. Regardless, the ability and/or willingness of the galvanizer to perform specific optimizations should be discussed during the project bid phase.
Maximizing Aesthetics when Painting or Powder Coating HDG
When preparing hot-dip galvanized products for painting or powder coating, surface preparation is critical to the appearance and overall performance. When the galvanizer and the paint or powder coating applicator are comprised of two different parties, critical surface preparation steps can sometimes be left out due to poor communication, resulting in adhesion issues and poor aesthetics. It is the responsibility of the owner or contractor to clearly inform all parties when hot-dip galvanized parts will be painted/powder coated and to clarify when agreement between all parties is required regarding responsibilities for surface smoothing.
Although sanding is commonly performed to smooth high spots in the coating, it may also be desired to fill low spots or depressions to even out divots in the steel or indentations from vent/drain hole plugs pushed in too far. To achieve a smooth, paintable surface in these areas which meets AESS 3 or 4 requirements, you may need to specify a filler material (putty or similar) the galvanizer/painter can use. Always confirm with the paint manufacturer whether the specified filler material is compatible with the primer coat.
In addition to these recommendations, the AGA has developed the following resources and instructional videos for successfully preparing the hot-dip galvanized surface:
Touch-up & Repair Materials
Should the hot-dip galvanized coating need to be repaired at the galvanizing facility, selection of repair material (zinc metallizing, zinc solder, or zinc-rich paint) can be considered for maximum aesthetics. In terms of appearance, zinc-based solders and zinc-spray metallizing more closely match the appearance of hot-dip galvanized steel, but there are limitations to applying both materials which must be considered in addition to cost. Zinc-rich paints can economically provide suitable aesthetics if a matte gray or weathered color repair paint is utilized. Although the appearance may at first be a mixture of gray paint and shiny hot-dip galvanizing, all hot-dip galvanized coatings will weather to a matte gray and more closely match the repair paint color over time. The use of a shiny or silver repair paint will result in permanent mixed appearance once the base galvanizing weathers.
Preventing Wet Storage Stain
After acceptance of the material, hot-dip galvanized articles should be stored in a way to minimize the occurrence of wet storage stain.
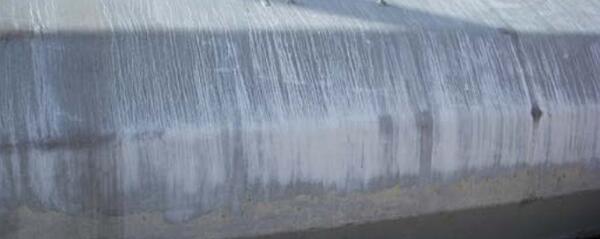
The presence of light or medium wet storage stain does not negatively affect the level of corrosion protection and does not require remediation, but for aesthetic purposes it can be removed using commercially available chemicals and a stiff nylon bristle brush. Despite the presence of light or medium wet storage stain, the parts will weather to a uniform appearance over time typically six months to two years depending on the environment.
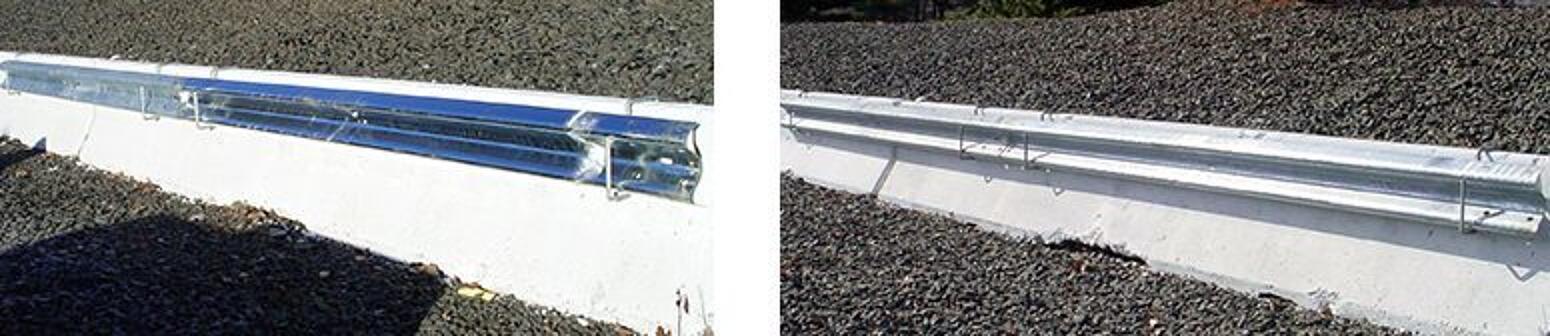
Refer to the AGA publication Wet Storage Stain (also available in Spanish and Canadian French) for preventive measures and cleaning instructions.
Conclusion
With more specifiers requesting hot-dip galvanized AESS, it is important to account for the unique properties of the hot-dip galvanized coating and stress the importance of direct communication between all parties regarding aesthetic requirements. With the help of a new categorical approach to AESS and an understanding of ASTM A123 finish requirements, it is possible to bridge this communication gap so elevated aesthetics for galvanized AESS projects are achieved without headaches.
If you have any questions on AESS and hot-dip galvanizing, please contact the AGA Technical Department.
© 2024 American Galvanizers Association. The material provided herein has been developed to provide accurate and authoritative information about after-fabrication hot-dip galvanized steel. This material provides general information only and is not intended as a substitute for competent professional examination and verification as to suitability and applicability. The information provided herein is not intended as a representation or warranty on the part of the AGA. Anyone making use of this information assumes all liability arising from such use.