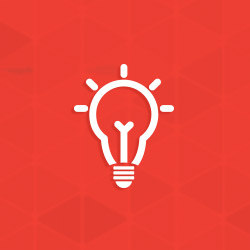
Welding Electrodes Before Galvanizing
What welding electrodes are recommended for fixtures, kettle repair, or fabrications?
Selecting the proper welding material is critical for long-lasting kettle repairs, fabricating equipment used to support hot-dip galvanizing operations (overhead fixtures, racks, and baskets), as well as before galvanizing to reduce coating thickness over the welds. Molten zinc is very aggressive to steel and weld materials, so selecting the wrong material can cause the weld to erode in a matter of weeks and lead to excessive and costly repairs. To prevent rapid attack or corrosion of the weld material, it is necessary to use welding rods that will not be quickly consumed by the zinc, but instead corrode at a similar rate to the base metal.
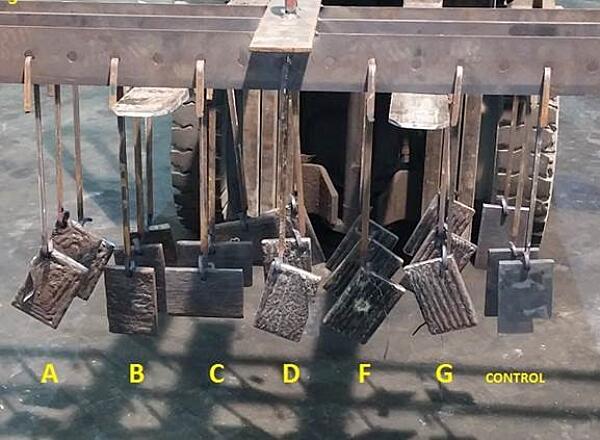
Twenty five years ago, the AGA evaluated the corrosion resistance of various weld materials to molten zinc and established a list of six materials recommended for kettle repair and the fabrication of fixtures or racks. Unfortunately, some of the weld materials that were tested previously are no longer being produced today. To update the existing list, a new set of welding electrodes was tested in 2017 upon consultation with Lincoln Electric (Figure 1). The scope was expanded beyond stick welding (SMAW) rods and flux-cored arc welding (FCAW) wires, and now includes a submerged arc welding (SAW) electrode for faster weld deposition. These materials were immersed in a galvanizing kettle of molten zinc and some were removed at 1 month, 3 month, and 6 month test periods. The updated list of recommended welding materials in Table 1 includes the new welding materials from the updated study which showed similar weight loss to the unwelded control sample or base metal. Generally, it was determined that weld materials with a silicon content less than 0.25% tend to work well in contact with the molten zinc.
TABLE 1: RECOMMENDED WELDING MATERIALS FOR KETTLE REPAIRS, FIXTURES, RACKS AND BASKETS (UPDATED 2017)
Welding Process | Lincoln Electric Welding Electrode | AWS Designation | Silicon (Weight %) |
---|---|---|---|
SMAW | Jetweld 2 Fleetwood 35 LS | E6027 E6011 | 0.22-0.26% 0.10-0.18% |
SAW | L60-860 | F6A2-EL12 | 0.24% |
FCAW | *NR-203 NiC+ NR 203 MP NR 233 NR 311 | E71T8-K2 E71T-8J E71T-8 E70T-7 | 0.06% 0.22-0.26% 0.19-0.20% 0.12-013% |
* Welding wire lost prior to fabrication during the study; it is recommended to use a test plate before use. |
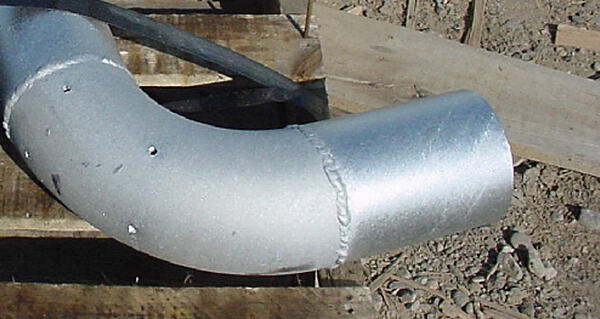
Table 1 can also be used to specify welding materials that are suitable for use during fabrication where welding is performed before hot-dip galvanizing. When the selected welding rod material is more reactive than the surrounding steel, a different appearance over the weld can be expected which is often duller in appearance, rougher, and thicker (Figure 2). However, the latest results of the Welding Rod Study indicate that the Silicon content (% Si) of the weld material does not necessarily follow the pattern of galvanizing reactivity as shown by the Sandelin Curve. Although the Sandelin curve is a useful chart for determining the reactivity of steel to be hot-dip galvanized, it may not be a useful metric when trying to match weld material reactivity to base metal reactivity to achieve similar coating thickness and appearance. Where unsure, the welding materials listed in Table 1 can be used to reduce coating thickness over the welds, resulting in a more uniform appearance overall.
For more details and an explanation of the test method and results, refer to the Galvanizing Note entitled Welding Electrodes Resistant to Molten Zinc Attack.
See Also:
- The AGA's various publications on Welding
- Welding Before HDG
© 2025 American Galvanizers Association. The material provided herein has been developed to provide accurate and authoritative information about after-fabrication hot-dip galvanized steel. This material provides general information only and is not intended as a substitute for competent professional examination and verification as to suitability and applicability. The information provided herein is not intended as a representation or warranty on the part of the AGA. Anyone making use of this information assumes all liability arising from such use.