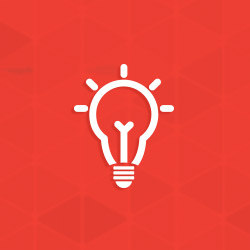
Variation and Average Coating Thickness
Does variation in coating thickness indicate poor quality?
During the inspection of test lots to determine conformance to a minimum specification, some established sampling procedures and quality plans require a statistical evaluation of properties (such as average coating thickness) to ensure the minimum requirements are met with low variation. Variation is measured by sample standard deviation, sample range, or known standard deviation.
However, such procedures are only valid when inspecting properties that follow a nearly normal distribution where the data tends to be centered around one value. In practice, hot-dip galvanized coatings are well known to present irregularities and variations, and may instead follow a skewed distribution (Figure 1).
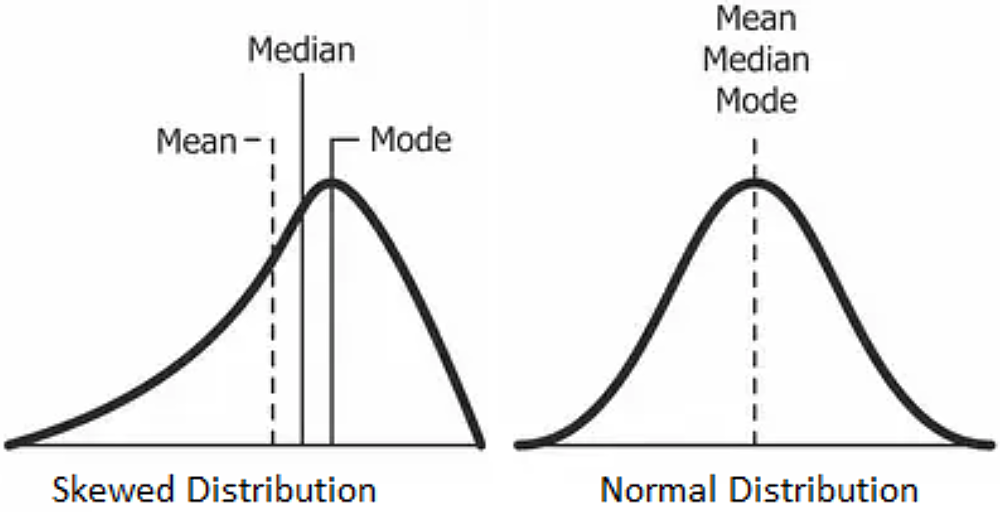
Though these types of sampling plans are not applicable for evaluating batch hot-dip galvanized coating thickness, customers concerned with tight tolerances or smooth/uniform coatings may occasionally request them. However, concerns can arise when the galvanizer and customer are not aware of the increased risk of error that can occur when using such procedures.
Here is an example to demonstrate the concern:
To evaluate coating thickness for parts galvanized to CSA G164, a procedure from CSA C83 Annex B is used. This procedure (called a “range plan”) requires statistical evaluation of the inspection test lot to establish conformance to a required minimum average coating thickness (in this example, 75μm or 3 mils). Upon inspecting the articles in the test lot, we find:
Minimum average coating thickness
Test article 1 | 91 μm |
Test article 2 | 100 μm |
Test article 3 | 86 μm |
Test article 4 | 88 μm |
Test article 5 | 89 μm |
Average | 91 μm |
For many galvanizers, the values encountered in this inspection are quite common and would normally be acceptable under ASTM 123. However, this lot would be rejectable under the range plan due to a mathematical formula used to compare the variance against an acceptance criteria constant. This formula considers the range of the values (max – min) as well as the difference between the lot average (91 μm) and the minimum requirement (75 μm).
When the value for the acceptance criteria constant is too restrictive regarding variation, the sampling plan may not allow for reasonable evaluation of coating thickness for:
- articles of reactive steel chemistry which significantly exceed minimum coating thickness requirements but are otherwise acceptable
- steels of varied surface chemistry due to steel processing or fabrication techniques but are otherwise acceptable
Therefore, galvanizers should be very careful when accepting the use of a range plan unless the purchaser and galvanizer can agree on a plan of action when failing lots are otherwise acceptable in terms of general requirements, minimum average coating thickness, adherence, and finish. Otherwise, refer the customer to the instructions for evaluating minimum average coating thickness provided directly with ASTM A123. For assistance in determining whether products conform to ASTM A123 minimum coating thickness requirements, the AGA has developed the following resources to assist you:
© 2025 American Galvanizers Association. The material provided herein has been developed to provide accurate and authoritative information about after-fabrication hot-dip galvanized steel. This material provides general information only and is not intended as a substitute for competent professional examination and verification as to suitability and applicability. The information provided herein is not intended as a representation or warranty on the part of the AGA. Anyone making use of this information assumes all liability arising from such use.